Typical Tungsten Carbide Cutting Technology
- Details
- Category: Tungsten Information
- Published on Thursday, 23 November 2017 20:49
For the cutting technology of tungsten carbide, the control of cutting condition is very important. The choice of different green parts, processing technology of sintered parts and the cutting tool determines the different optimal cutting parameters. For the processing of green parts, the high cutting speed can be adopted because the cutting speed has little effect on the surface finish and the edge breakage width.
In addition, compared with the processing of sintered parts, the higher feed rate can be adopted. When the cutting blank is more, the low feed rate will make the tool edge wear prematurely, and the higher wear rate can reduce the total wear of the tool.
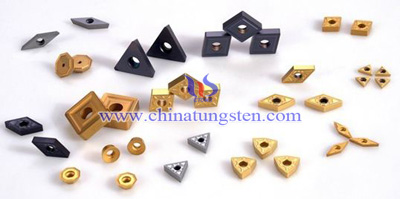
In cemented carbide cutting technology, the choice of appropriate tool materials and processing parameters is important to improve the processing efficiency of blanks and reduce the reject rate. The cutting edge of cutting plasticizing alloy blank is both sharp and wear resistant. Selecting the YN05 and YT726 alloy with hardness above HRA93 and supplementing by proper tool structure can ensure the dimensional accuracy of blank machining.
The geometric parameters of commonly used cutters are respectively: drill vertex angle 2φ=60~70°, relief angleα=10~14°, turning tool, anterior angleγ=25~20°,relief angleα=20~25°, main and auxiliary deflection angleψ=ψ1=60~75°,r=0.2~0.3mm, hobbing anterior angleγ=5~10°,relief angleα=20~25°. When grinding, the soft grinding wheel with alumina grain size of 300~400 can be used.
- Tungsten Carbide Manufacturer & Supplier, Chinatungsten Online: tungsten-carbide.com.cn
- Tungsten News & Prices of China Tungsten Industry Association: www.ctia.com.cn
- Molybdenum News & Price: news.molybdenum.com.cn
- Tel.: 86 592 5129696; Fax: 86 592 5129797; Email: sales@chinatungsten.com