Tungsten Carbide Surfacing Process Can Reduce the Cost of Mold Production
- Details
- Category: Tungsten Information
- Published on Thursday, 26 October 2017 22:03
Mold is the basis of modern industry, with the development of the global economy, the accuracy of the mold, performance and cost of higher requirements are put forward.
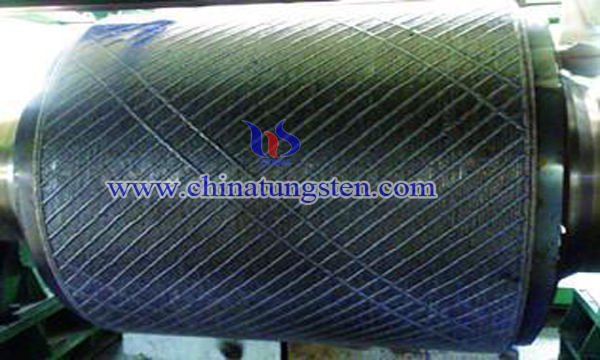
Ordinary steel hardfacing can be used as cheap base material, and surface treatment, can greatly reduce the cost of mold, which is expected to achieve by ordinary steel welding + surface strengthening instead of die steel, opens up a new way for the selection of die materials.
Tungsten carbide surfacing technology is widely used in hardfacing technology. Using tungsten carbide rod oxy acetylene surfacing method can prepare composite hardfacing layer on the surface of the mould, the surfacing layer is a metal based tungsten carbide ceramic composite material, the composite material consists of ordinary carbon steel metal matrix and ceramic particle distribution of carbides in the matrix composition has excellent abrasion resistance in order to ensure the service life of the die, the die cavity surface with high hardness, wear resistance, corrosion resistance, fatigue resistance and oxidation resistance.
Casting tungsten carbide rod with surfacing material, model YZ3 mould material is 45 steel. Oxygen acetylene flame surfacing layer by tungsten carbide ceramic particles and carbon steel not melt, tungsten carbide particles embedded in the substrate, forming a metal based tungsten carbide ceramic composites due to the oxygen acetylene flame welding heat source in low temperature, low energy density, only a small amount of matrix material melts. Through skilled welding workers, tungsten carbide ceramic particles play an important role in the surfacing layer, which is the main wear-resistant phase, and the metal matrix plays a role in fixing and supporting tungsten carbide particles. Because the melting point of tungsten carbide is very high, it may not melt basically, but exists in the weld. It is inlaid and even brazed on the matrix, forming the hardfacing layer of cemented carbide composite material.
Tungsten carbide wear resistance depends on its own high hardness, high wear resistance. In order to give full play to the wear resistance of tungsten carbide, the melting of tungsten carbide particles should be avoided and the original shape should be kept in the process of surfacing.
The production practice shows that the mold mold large size, relatively simple structure, the ordinary steel + tungsten carbide welding method for surface strengthening, the rational use of materials, saving the precious metal, improve the service life of the die, it is significant to reduce the cost of mould manufacturing.
- Tungsten Carbide Manufacturer & Supplier, Chinatungsten Online: tungsten-carbide.com.cn
- Tungsten News & Prices of China Tungsten Industry Association: www.ctia.com.cn
- Molybdenum News & Price: news.molybdenum.com.cn
- Tel.: 86 592 5129696; Fax: 86 592 5129797; Email: sales@chinatungsten.com