China’s Zhangyuan Tungsten Raised Long-term Contract Prices for the Second Half of August 2023
- Details
- Category: Tungsten's News
- Published on Wednesday, 23 August 2023 14:53
- Written by Shuxia
- Hits: 500
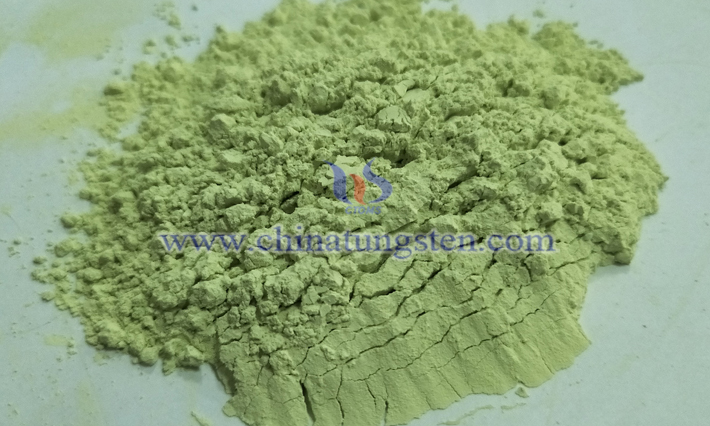
Analysis of latest tungsten market from Chinatungsten Online
At the beginning of the week, China tungsten price held steady, with the market trading atmosphere remaining cautious and primarily driven by on-demand transactions.
China Tungsten Price Was in the Upward Trend in the Middle of August 18, 2023
- Details
- Category: Tungsten's News
- Published on Wednesday, 23 August 2023 14:50
- Written by Shuxia
- Hits: 485
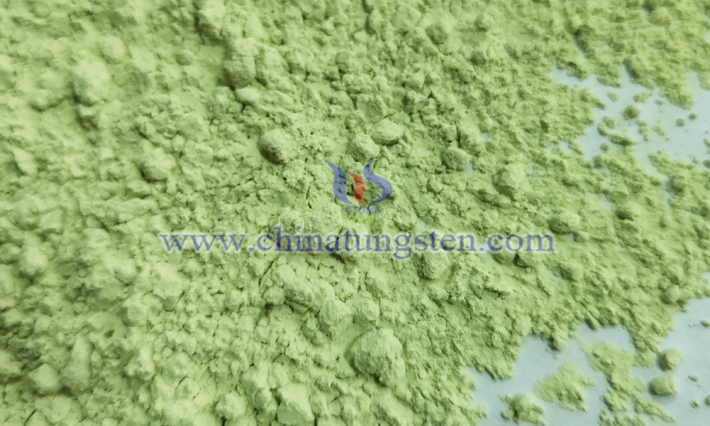
Analysis of latest tungsten market from Chinatungsten Online
China tungsten price was in the upward trend in the week ended on Friday, August 18, 2023 despite limited progress in market demand.
Read more: China Tungsten Price Was in the Upward Trend in the Middle of August 18, 2023
Molybdenum Oxide Price - August 21, 2023
- Details
- Category: Tungsten's News
- Published on Wednesday, 23 August 2023 14:42
- Written by Shuxia
- Hits: 1796

Molybdenum Market on August 21, 2023
At the beginning of the week, China’s domestic molybdenum market is generally experiencing pressure at high levels. The impact of low enthusiasm from downstream users for inquiries and purchases, combined with the continuous decline in international molybdenum prices, has led to a decrease in the stable pricing confidence of many suppliers.
China Rare Earth Prices - August 21, 2023
- Details
- Category: Tungsten's News
- Published on Wednesday, 23 August 2023 14:47
- Written by Shuxia
- Hits: 533
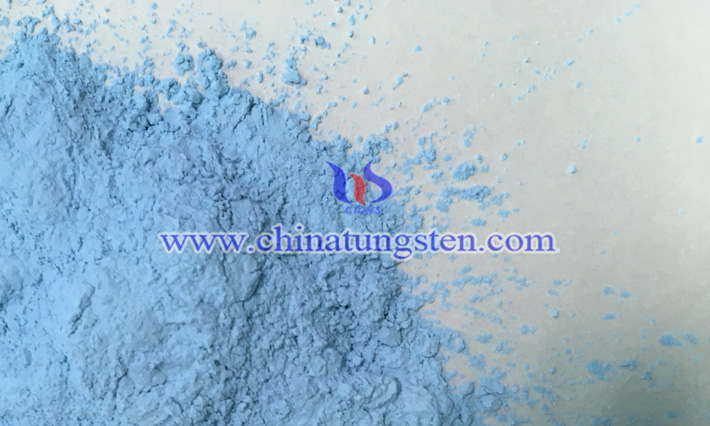
At the beginning of the week, China rare earth prices have seen a slight upward shift in overall focus. This is mainly attributed to restricted production from certain rare earth manufacturers, positive developments in emerging industries, and relatively low raw material inventories for magnet material companies.
China’s Tungsten Carbide Powder Prices Keep Firm Driven by Cost Factors
- Details
- Category: Tungsten's News
- Published on Monday, 21 August 2023 18:04
- Written by Shuxia
- Hits: 514
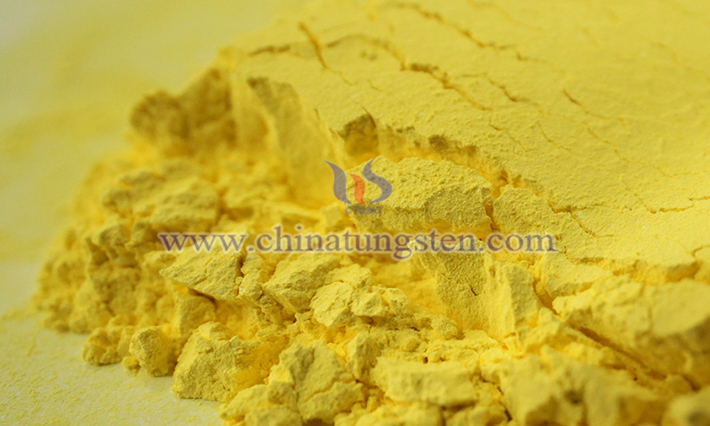
Analysis of latest tungsten market from Chinatungsten Online
The recent Chinese tungsten price has remained stable, as major tungsten enterprises' upward adjustments in long-term contract prices have boosted market confidence, resulting in robust offers from traders.
Read more: China’s Tungsten Carbide Powder Prices Keep Firm Driven by Cost Factors