China Conquered Problems with Tungsten in 3D Printing - 2
- Details
- Category: Tungsten's News
- Published on Wednesday, 27 February 2019 14:51
For thermal control system of spacecraft, the radiator is the main device, but also a determinant of the life of the chip. In order to achieve better heat dissipation effect, the radiator is generally porous, and is covered on the chip to increase the contact area of chip and air to reduce the temperature of the chip.
Usually, radiators are made of metals with good thermal conductivity, such as copper. However, although copper, as a traditional metal dissipates heat well, but its shortcomings cannot be ignored. The heat exchange of aerial and astronautic chips is very large, which will lead to serious deformation of copper radiator, effecting the heat dissipation effect, and ultimately will affect the service life of the chip.
Therefore, the current solution is to make a porous tungsten skeleton out of metallic tungsten first, and then infiltrate copper into the porous tungsten skeleton to obtain a tungsten copper composite that combines the characteristics of tungsten and copper. That is to say, tungsten copper radiator can take advantage of the perspire refrigeration effect of copper’s volatilization under high temperature, reducing the surface temperature of tungsten copper, and ensure the use under high temperature and extreme conditions. It prevents the deformation of copper material when heat exchange of chip is large.

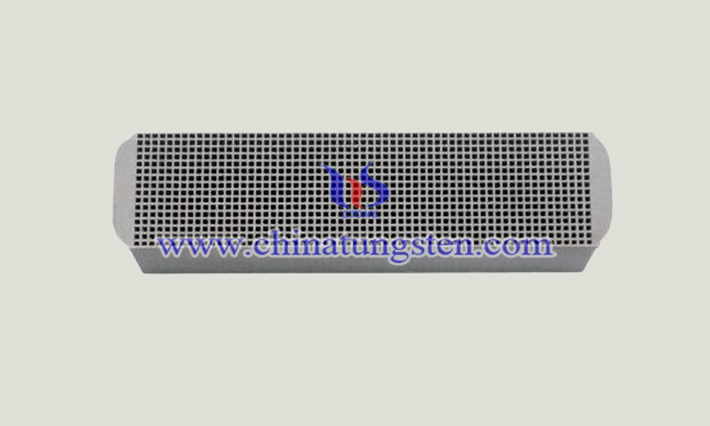
However, the production of porous tungsten skeleton is difficult, because tungsten is not only a strategic metal, but also a refractory metal. It has excellent properties such as wear resistance, high hardness, high strength, corrosion resistance and good toughness. The traditional process for tungsten is consists of powder metallurgy and machining. The complex process leads to long processing time, and it is hard to make the porous mold. All of these lead to high cost. In addition, tungsten is brittle (easy to drop and make the processing surface defects) and with high hardness (will aggravate mold and tool wear) at room temperature, increasing difficulty for post-machining. In a word, the traditional production process has been increasingly unable to meet the current desire for production and processing. Therefore, cutting-edge manufacturing technology such as 3D printing has attracted wide attention in recent years. It combines design and production.
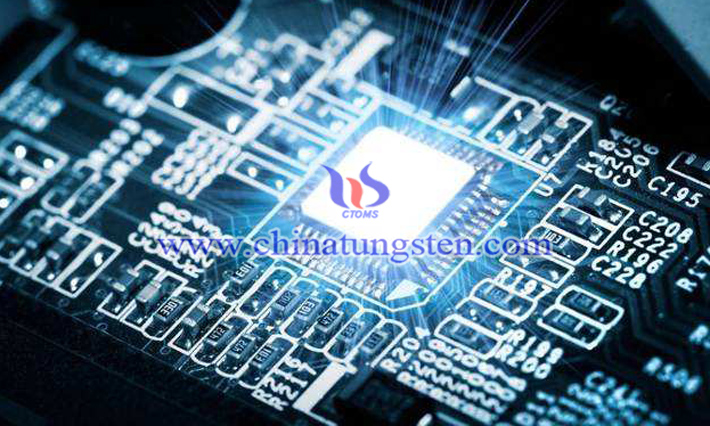
Picture of aerospace chip
As China conquered the difficulty and “printed” tungsten copper alloy radiator, it shortened the gap with advanced countries in the field of 3D printing. 3D printing technology enables a more flexible design of the channel structure of the radiator and shortens the production period. Even if it is a porous variable diameter structure, it can also be molded at once and doesn’t need to post-machining.
There is no end in space exploration. Chinese scientists and space workers will surely contribute their wisdom to the development of astronautic industry and contribute more strength to the peaceful use of space. China's scientific research team will also scale the peak of 3D printing technology, shorten the research and development cycle of aerospace equipment, improve material utilization, reduce manufacturing costs, optimize parts structure, and reduce material weight.
- Tungsten Manufacturer & Supplier, Chinatungsten Online: www.chinatungsten.com
- Tungsten News & Prices of China Tungsten Industry Association: www.ctia.com.cn
- Molybdenum News & Price: news.molybdenum.com.cn
- Tel.: 86 592 5129696; Fax: 86 592 5129797; Email: sales@chinatungsten.com