Superiority of Tungsten Carbide Dies
- Details
- Category: Tungsten Information
- Published on Thursday, 12 July 2018 16:58
In the production of standard fasteners, the use of tungsten carbide dies has a series of advantages.
1, The life of the mould is greatly improved.
For example, a para factory produces M 8 bolts. In the past, every class averagely needs 4 cavity blocks. But now a tungsten carbide mold can be applied to three classes for half a month, up to one month. The die life is increased by more than 100 times. In the past, the production of M10 and M12 bolts has been used on the average of 6 dies per class. Now a three production of cemented carbide dies can be used for one week and the life expectancy is nearly one hundred times.
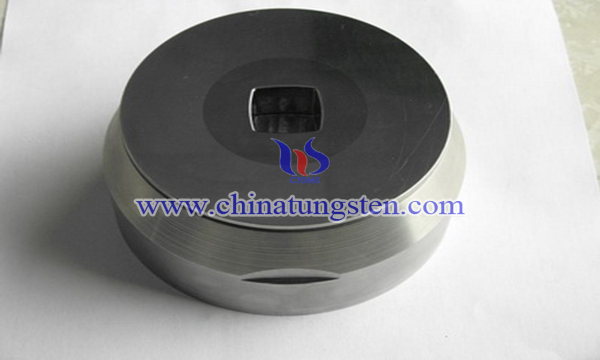
2, A lot of die steel materials are saved. Taking a para factory production as an example, a Z12-8 double-click cold heading machine needs 300 female dies in the past month. After the use of tungsten carbide dies, only 2~3 is required. 300 kilograms of tool steel materials can be saved in the whole month. A Z12-12 double-click cold heading machine used to need 400 dies per month, and only 5~6 after using tungsten carbide dies. It saves one ton of tool steel throughout the month.
If the tungsten carbide dies are popularized on dozens of equipment in the whole plant, a large number of expensive tool steels will be saved every year for the country. At the same time, the workload of mould manufacturing will be reduced greatly, and a large number of cutting tools and precision equipment will be saved.
3, The quality of products is improved. The use of tungsten carbide mold can better ensure the size accuracy of the screw, thereby improving the thread accuracy. Because of the high hardness of the die, the quality of the product can be guaranteed when the material is slightly poor.
4, It can improve the productivity of the cold heading machine. Given the long service life of the tungsten carbide die, the time of replacement and adjustment of the die is greatly reduced. And the opening rate of the machine is improved, so the production of the cold heading machine has increased significantly. At the same time, as the number of moulds is reduced, the labor intensity of workers is greatly reduced.
5, The use of tungsten carbide die is one of the important conditions for developing advanced cold heading technology and cold heading equipment. For example, the six corners of the bolts have no scrap forming cold heading process, so it is difficult to achieve ideal results without using tungsten carbide dies. Multi station cold heading and cold extrusion automata are difficult to develop their high productivity without tungsten carbide dies.
The above examples show that vigorously developing of tungsten carbide dies is a directional technological innovation in the production of standard fasteners.
- Tungsten Carbide Manufacturer & Supplier, Chinatungsten Online: tungsten-carbide.com.cn
- Tungsten News & Prices of China Tungsten Industry Association: www.ctia.com.cn
- Molybdenum News & Price: news.molybdenum.com.cn
- Tel.: 86 592 5129696; Fax: 86 592 5129797; Email: sales@chinatungsten.com