Introduction to WHA
- Details
- Category: Tungsten Information
- Published on Friday, 07 June 2013 11:12
- Hits: 2399
Tungsten heavy alloy (WHA) are ideally suited to a wide range of density applications, offering a density approaching that of pure tungsten but without the very costly processing and inherent size and shape limitations of the former. WHAs are produced by a powder metallurgy (P/M) technique known as liquid phase sintering (LPS), in which completely dense, fully alloyed parts are formed from pressed metal powders at a temperature less than half the melting point of pure tungsten. While sintered steel and copper alloy parts commonly contain significant residual porosity that may require polymeric infiltrants to seal, sintered WHAs have a nonporous surface.
WHA parts are manufactured from very fine, high purity metal powders – typically tungsten, nickel, and iron. The blended metal powder is compacted under high pressure (up to 30 ksi) to form a specific shape that is very close to the geometry of the final part. By utilizing this near net shape forming approach, economy is realized by the elimination of excess material and the time and energy necessary to remove unwanted stock from mill shapes. Pressed parts are then subjected to high temperature sintering in hydrogen. As the parts are slowly heated, the hydrogen reduces metal oxides present and provides a clean, active surface on each of the very small metal particles. As temperature increases further, chemical diffusion takes place between particles. Neck growth occurs between particles, and surface energy drives pore elimination and part densification. The pressed part shrinks uniformly, with about 20% linear shrinkage (equating to approximately 50% volumetric shrinkage) being typical. Once the temperature is sufficiently high to form the liquid phase, any remaining densification occurs very quickly as the alloy assumes a "spheroidized" microstructure by a mechanism know as Ostwald Ripening. The sintered structure of a common commercial WHA is two-phase, consisting of a linked network of tungsten spheroids contained in the ductile matrix phase.
Tungsten Manufacturer & Supplier: Chinatungsten Online - http://www.chinatungsten.com
Tel.: 86 592 5129696; Fax: 86 592 5129797
Email: sales@chinatungsten.com
Tungsten Picture Center: http://picture.chinatungsten.com
Tungsten Video Center: http://v.chinatungsten.com
Tungsten News & Tungsten Prices, 3G Version: http://3g.chinatungsten.com
Introduction to Tungsten
- Details
- Category: Tungsten Information
- Published on Friday, 07 June 2013 11:06
- Hits: 2214
The name "tungsten" is derived from the Swedish term meaning "heavy stone". Tungsten has been assigned the chemical symbol W after its German name wolfram. While sometimes regarded as a scarce or exotic metal, its abundance in nature is actually about the same as that of copper. The largest known tungsten reserves are in mainland China, though plentiful reserves also exist in North America.
Tungsten has the highest melting point (3410°C or 6170°F) of all metals. The extremely high melting point of pure tungsten makes all the common manufacturing techniques used for metals such as iron impractical. Specialized methods make possible the processing of pure tungsten into rod, sheet, and wire for a wide variety of high temperature applications including incandescent lamp wire, TIG welding electrodes, and high temperature heat shielding.
Another important industrial property of tungsten is its high density of 19.3 g/cc (0.70 lbs/in3). In addition to high gravimetric density, its high radiographic density makes it an ideal material for shielding or collimating energetic x- and g-radiation. For such applications, tungsten is commonly alloyed in order to circumvent the extremely high processing temperatures that would otherwise be required to melt and cast the pure metal.
Tungsten Manufacturer & Supplier: Chinatungsten Online - http://www.chinatungsten.com
Tel.: 86 592 5129696; Fax: 86 592 5129797
Email: sales@chinatungsten.com
Tungsten Picture Center: http://picture.chinatungsten.com
Tungsten Video Center: http://v.chinatungsten.com
Tungsten News & Tungsten Prices, 3G Version: http://3g.chinatungsten.com
Applications of 3D Printing Technique in Aviation Industry (II)
- Details
- Category: Tungsten Information
- Published on Friday, 07 June 2013 09:00
- Hits: 2430
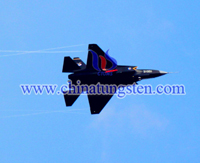
On May 29th 2013, there was an article in South China Morning Post of Hong Kong named as 3D Printer Promotes the Development of Chinese aircraft. For aircraft enthusiasts, it is not a dream that use computer and 3D printer to manufacture a small plastic aircraft. How about manufacturing a real aircraft?
The Chinese scientists and aeronautical engineer consider that can be realized. They have began to use 3D printer to manufacturer refractory metal aircraft parts without molding, forging, assembling or other traditional manufacturing processes.
3D printing, also called as laser rapid prototyping is a newly developing manufacturing technique. 3D printers can transform blueprint on computer into material object directly by overlying materials layer by layer until finished products.
Refractory metal aircraft parts, being manufactured by 3D printing technique have been widely used for C-919 the first Chinese civil aircraft, J-15 the first carrier fight, J-16 multipurpose fighter-bomber, J-20 the first Chinese stealth fighter and J-31 the fifth generation fighter.
Traditional aviation industry not only spends too much time, and it also wastes a lot of materials. In generally, only 10 percent of raw materials are utilized. The rest are lost during the processes of molding, forging, cutting and burnishing. F-22 fighter which developed by Lockheed Martin in the U.S. needs 2796kg titanium alloy. In fact, only 144kg is utilized.
Sidney Wong, the associate dean of Enterprise Development Department in Hong Kong Polytechnic University showed that 3D printing technique could accelerate the development of Chinese new generation aircraft. He said, “3D printing technique can save time and materials. Researchers can print refractory metal aircraft parts directly in a short time. The cost of prototype is low without molding or any other complicated traditional processes and scientists can manufacture constantly more repetitions for test.”
Professor Wang Huaming, the expert of aerial material in Beijing University of Aeronautics & Astronautics considered that Chinese 3D printing technique had exceeded the U.S. because the U.S. could only manufacture small products by using the technique. However, Luo Jun, the CEO of Asian Manufacturing Association in Beijing considered that the Chinese printing technique still fell behind the West.
Tungsten Manufacturer & Supplier: Chinatungsten Online - http://www.chinatungsten.com
Tel.: 86 592 5129696; Fax: 86 592 5129797
Email: sales@chinatungsten.com
Tungsten Picture Center: http://picture.chinatungsten.com
Tungsten Video Center: http://v.chinatungsten.com
Tungsten News & Tungsten Prices, 3G Version: http://3g.chinatungsten.com
Industry Specifications for Tungsten Alloys
- Details
- Category: Tungsten Information
- Published on Friday, 07 June 2013 10:58
- Hits: 2569
MIL-T-21014D |
SAE AMS-T-21014 |
ASTM B777-07 |
In August of 1986 the last revision of the “Proposed Military Specification” for Tungsten Base Metal, High Density (MIL-T-21014D) was issued. In use for many years this specification defined the requirements for four classes of machinable, high density tungsten base metal produced by consolidating metal powder mixtures comprised primarily of tungsten. The alloy classes differed in tungsten content and density. The specification defined four slightly magnetic tungsten alloys (containing Ni-Fe binders) and three nonmagnetic tungsten alloys (containing Ni-Cu binders) in terms of their composition, mechanical properties, and machinability. ASTM approved a standard containing essentially the same content in 1987. The most recent revision of the ASTM standard (ASTM B777-07) was published in November of 2007 and is the active standard for tungsten alloys at this time. A third standard was introduced in August of 1998 by the Society of Automotive Engineers (SAE Technical Standard AMS-T-21014). All three of these standards contained the same set of mechanical properties for the various alloy classes. These properties are summarized in the table below.
Tungsten Alloy Shielding Tube & EFP Test
- Details
- Category: Tungsten Information
- Published on Thursday, 06 June 2013 18:28
- Hits: 2441
There are various kinds of test for penetration of EFP (explosively formed penetrators). The first method is utilizing impulse X radiography to know the speed and attitude of EFP before or after penetrating, residues of EFP after penetrating and the fragments after penetrating target. Because strong flashing light and smoke accompany with the process of penetrating. For that, the only method to know the influence of EFP on target and the situation after penetrating target is adopting X-ray radiography. So impulse X-ray radiography has significance for research on penetrating mechanism of EFP. However X-ray may do harm to health during test. So the protection to researchers is necessary. Tungsten alloy shielding tube is made of tungsten alloy for protecting researchers from damaging of X-ray. Tungsten alloy shielding tube has good performance of radiation to radioactive substance for the high density of tungsten alloy. Otherwise, compared with lead, tungsten alloy is more environmentally friendly,and tungsten alloy is non-toxic and non-radioactive.