Tungsten Carbide Cutting Tool Crack Analysis
- Details
- Category: Tungsten Information
- Published on Friday, 07 November 2014 16:47
- Written by xjq
- Hits: 471
The higher intensity the tungsten carbide cutting tool has, the lower the risk that it will produce cracks. However, in the actual production process, even the carbide material with highest intensity and abrasion resistance will produce cracks. So, what are the reasons for this?
Tungsten carbide cutting tool cracks are formed because the welding stress exceeds the intensity limit of tungsten carbide cutting tools. If the tungsten carbide cutting tool bends, then there will be tensile stress along the direction of carbide blade thickness. When the cutting tool is welded, it is not conducted on the same plane, but on several planes. In addition, when tungsten carbide suffers rapid heating or cooling, the blade surface temperature will be pretty unevenly and thus obvious instantaneous stress can happen, which will easily results in tungsten carbide cutting tool cracks. Therefore, the heating or cooling of the cutting tools should be conducted slowly.
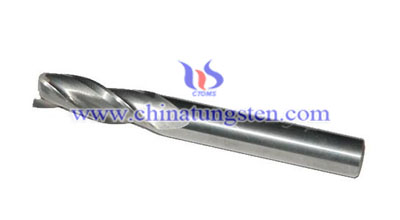
Tungsten Manufacturer & Supplier: Chinatungsten Online - http://www.chinatungsten.com
Tel.: 86 592 5129696; Fax: 86 592 5129797
Email: sales@chinatungsten.com
Tungsten & Molybdenum Information Bank: http://i.chinatungsten.com
Tungsten News & Tungsten Prices, 3G Version: http://3g.chinatungsten.com
Molybdenum News & Molybdenum Price: http://news.molybdenum.com.cn
Tel.: 86 592 5129696; Fax: 86 592 5129797
Email: sales@chinatungsten.com
Tungsten & Molybdenum Information Bank: http://i.chinatungsten.com
Tungsten News & Tungsten Prices, 3G Version: http://3g.chinatungsten.com
Molybdenum News & Molybdenum Price: http://news.molybdenum.com.cn