三氧化钨和钨酸钡的电输运Ⅰ
- 详细资料
- 分类:钨业知识
- 发布于 2015年12月30日 星期三 15:55
在金刚石对顶砧装置中,通过直流电阻率和交流阻抗谱的测量方法,在36GPa的压力范围内,探究电阻率、晶粒电阻、晶界电阻和弛豫频率等物理量在高压下的变化规律。以高压下微晶WO3的电输运性质为实验,结果发现,样品电阻率的不连续变化出现在1.8,21.2和30.4GPa的压力处,反映了WO3的压致结构相变。卸压之后电阻率并没有恢复到原来的数值,说明WO3的结构相变是不可逆的。
实验光刻过程中带有倒角的金刚石
另外,晶粒电阻和传导激活能在3和10GPa的异常变化与先前拉曼研究中的等结构相变有关。高压下的电阻率随温度变化的规律表明,WO3从常压到25.3GPa依然保持半导体的性质。通过同步辐射X射线衍射实验在约24和31GPa出现的新峰,证实了结构相变的发生,说明了电学测量结果和相关分析的正确性。
通过对纳米WO3的高压原位电阻率的测量发现,样品电阻率在4.3和10.5GPa出现了不连续的变化,反映了纳米WO3的电子结构相变,晶粒的尺度效应导致了相变的迟滞;电阻率的斜率在24.8和31.6GPa处的变化反映了纳米WO3的结构相变;电阻率从36GPa卸压到常压并没有恢复到初始状态的值,说明纳米WO3的结构相变也是不可逆相变;变温电阻率的研究结果发现,纳米WO3从常压到36GPa一直保持半导体的传输特性,这与体材料WO3也是相似的。对其变频交流阻抗谱的研究发现:在压力作用下出现了晶界效应;晶粒电阻在4.6和10.3GPa处的不连续性也为电子相变提供了依据;压致弛豫频率的变化表明在10.3GPa处的电子相变中的弛豫过程时间较短;晶界弛豫频率的痕迹也说明晶界效应并非完全消失,这与Nyquist阻抗谱图的结论相一致。
氧化钨供应商:中钨在线科技有限公司 | 产品详情: http://www.tungsten-oxide.com |
电话:0592-5129696 传真:5129797 | 电子邮件:sales@chinatungsten.com |
钨钼文库:http://i.chinatungsten.com | 钨钼图片: http://image.chinatungsten.com |
钨新闻3G版:http://3g.chinatungsten.com | 钼业新闻: http://news.molybdenum.com.cn |


碲化钨
- 详细资料
- 分类:钨业知识
- 发布于 2015年12月30日 星期三 15:30
中文名称:碲化钨(IV)
英文名称:bis(tellanylidene)tungsten
英文别名:Tungsten ditelluride;
EINECS 235-086-0; Tungsten telluride; ditelluroxotungsten;
CAS号:12067-76-4
分子式:H2Te2W 分子量:441.05600
精确质量:445.77900
二碲化钨( WTe2) 是具有层状结构的过渡族金属硫族化合物,在其正交晶胞中钨链沿着碲层的 a 轴方向呈一维分布,是一种非磁性的半金属材料。WTe2以其良好的热电性能早已为人们所认知,普林斯顿大学教授 Cava 研究组在 2014 年意外地发现 WTe2在常压下具有不饱和的大磁阻( LMR) 特性( Nature,514 ( 2014)205) ,即在磁场下这种材料表现出异常大的正电阻效应,而且在非常高的磁场下也不饱和。这种特性不仅为其在电子器件方面的应用提供了潜在的可能,同时也为大磁阻材料的研究开辟了新的方向。在半金属中,非常高的磁阻是由于空穴-电子间的“共振”所产生的,而 WTe2是第一种人们发现的具有这种完美共振的材料。
钨产品供应商:中钨在线科技有限公司 | 产品详情: http://cn.chinatungsten.com |
电话:0592-5129696 传真:5129797 | 电子邮件:sales@chinatungsten.com |
钨钼文库:http://i.chinatungsten.com | 钨钼图片: http://image.chinatungsten.com |
钨新闻3G版:http://3g.chinatungsten.com | 钼业新闻: http://news.molybdenum.com.cn |


钨酸铈
- 详细资料
- 分类:钨业知识
- 发布于 2015年12月30日 星期三 15:25
中文名称:钨酸铈氧化钨铈
中文别名:氧化钨铈
英文名称:Cerium Tungstate
英文别名:Ceriumtungstateoffwhitepowder; Cerium tungsten oxide (REO); dicerium tritungsten dodecaoxide; Cerium tungsten oxide; CERIUM TUNGSTEN OXIDE;
CAS号:13454-74-5
分子式:Ce2O12W3
分子量:1023.74000
精确质量:1023.60000
物性数据
1.性状:黄色四方晶系
2.密度(g/mL,25/4℃):6.77
3.溶解性:不能溶解的
毒理学数据
1、急性毒性:主要的刺激性影响:
在皮肤上面:刺激皮肤和粘膜;
在眼睛上面:刺激的影响;没有已知的敏化影响。
2、致敏作用:通过吸入可能造成敏化作用,通过皮肤接触可能造成敏化作用。
生态学数据
通常对水是不危害的,若无政府许可,勿将材料排入周围环境。
性质与稳定性
常温常压下稳定
避免的物料 酸 碱。黄色四方晶系,相对密度6.77,熔点1089℃,在30K以下具有铁磁性。
贮存方法
常温密闭,阴凉通风干燥
合成方法
将Ce2O3、CeO2与WO3混合加热制取钨酸亚铈。
钨产品供应商:中钨在线科技有限公司 | 产品详情: http://cn.chinatungsten.com |
电话:0592-5129696 传真:5129797 | 电子邮件:sales@chinatungsten.com |
钨钼文库:http://i.chinatungsten.com | 钨钼图片: http://image.chinatungsten.com |
钨新闻3G版:http://3g.chinatungsten.com | 钼业新闻: http://news.molybdenum.com.cn |


钨矿物种类
- 详细资料
- 分类:钨业知识
- 发布于 2015年12月30日 星期三 15:18
在成矿过程中钨绝大多数形成氧化物,即钨酸盐类,很少形成硫化物,没有自然钨。目前在地壳中仅发现有20余种钨矿物和含钨矿物。
黑钨矿族:钨锰矿,钨铁矿,钨锰铁矿;
白钨矿族:白钨矿,钼白钨矿,铜白钨矿;
钨华类矿物:钨华,水钨华,高铁钨华,钇钨华,铜钨华,水钨铝矿;
不常见的钨矿物:钨铅矿、斜钨铅矿、钨锌矿、钼钨铅矿、钨铋矿、锑钨烧绿石、钛钇钍矿(含钨)、硫钨矿等。
黑钨矿
因含有不同比例的铁钨酸盐和锰钨酸盐,所以又被称作钨锰铁矿,约占全球钨矿资源总量的30%。如果含铁量高就叫钨铁矿,含锰量高就叫钨锰矿。黑钨矿的颜色随着铁、锰含量的变化而变化,常见的颜色有暗灰色、淡红褐、淡褐黑、发褐及铁褐等。黑钨矿具有金属或半金属光泽,性脆,具有弱磁性。黑钨矿主产于高温热液石英脉中,我国江西南部、湖南东部、广东北部均为世界著名的黑钨矿产区,此外,俄罗斯西伯利亚、缅甸、泰国、澳大利亚、玻利维亚等也是黑钨矿的主产地。黑钨矿主要用来炼钨和制造钨酸盐。
白钨矿
白钨矿是一种外形为粒状或块状的透明到半透明的矿物,颜色随着钼含量的变化而变化,常见的颜色有白色、灰色、浅黄、浅紫、浅褐色、淡红色、绿色等,具有油脂光泽或玻璃光泽,约占全球钨矿资源总量的70%。白钨矿具有发光性,在紫外光照射下发浅蓝色至黄色荧光。
白钨矿主产于接触交代矿床、高温热液脉和云英岩中。我国湖南瑶岗仙是世界著名的白钨矿产地,此外,我国江西大庚、湖南大顺窿、云南文山等地以及朝鲜南部的山塘、德国萨克森、英国康沃尔、澳大利亚新南威尔士、玻利维亚北部和美国内华达等也是白钨矿的主产地。白钨矿主要用来生产钨铁,也可制作永久性磁石。
钨产品供应商:中钨在线科技有限公司 | 产品详情: http://cn.chinatungsten.com |
电话:0592-5129696 传真:5129797 | 电子邮件:sales@chinatungsten.com |
钨钼文库:http://i.chinatungsten.com | 钨钼图片: http://image.chinatungsten.com |
钨新闻3G版:http://3g.chinatungsten.com | 钼业新闻: http://news.molybdenum.com.cn |


钨合金F1赛车配重Ⅳ
- 详细资料
- 分类:钨业知识
- 发布于 2015年12月30日 星期三 11:35
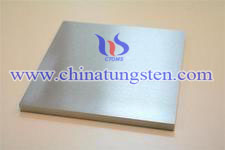
高比重合金供应商:中钨在线科技有限公司 | 产品详情: http://www.tungsten-alloy.com |
电话:0592-5129696 传真:5129797 | 电子邮件:sales@chinatungsten.com |
钨钼文库:http://i.chinatungsten.com | 钨钼图片: http://image.chinatungsten.com |
钨新闻3G版:http://3g.chinatungsten.com | 钼业新闻: http://news.molybdenum.com.cn |


钨合金F1赛车配重Ⅲ
- 详细资料
- 分类:钨业知识
- 发布于 2015年12月30日 星期三 11:32
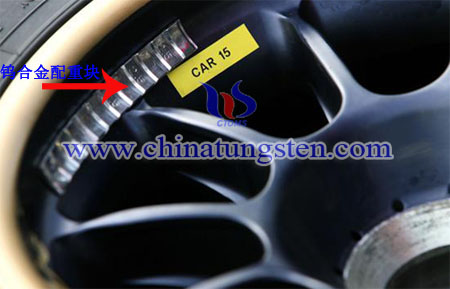
高比重合金供应商:中钨在线科技有限公司 | 产品详情: http://www.tungsten-alloy.com |
电话:0592-5129696 传真:5129797 | 电子邮件:sales@chinatungsten.com |
钨钼文库:http://i.chinatungsten.com | 钨钼图片: http://image.chinatungsten.com |
钨新闻3G版:http://3g.chinatungsten.com | 钼业新闻: http://news.molybdenum.com.cn |


钨合金F1赛车配重Ⅱ
- 详细资料
- 分类:钨业知识
- 发布于 2015年12月30日 星期三 11:29
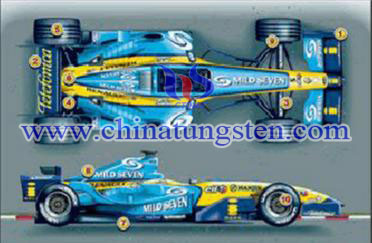
高比重合金供应商:中钨在线科技有限公司 | 产品详情: http://www.tungsten-alloy.com |
电话:0592-5129696 传真:5129797 | 电子邮件:sales@chinatungsten.com |
钨钼文库:http://i.chinatungsten.com | 钨钼图片: http://image.chinatungsten.com |
钨新闻3G版:http://3g.chinatungsten.com | 钼业新闻: http://news.molybdenum.com.cn |


钨合金F1赛车配重Ⅰ
- 详细资料
- 分类:钨业知识
- 发布于 2015年12月30日 星期三 11:26
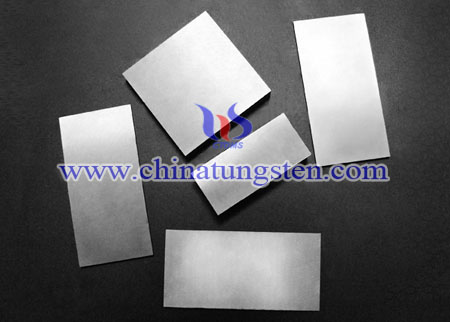
高比重合金供应商:中钨在线科技有限公司 | 产品详情: http://www.tungsten-alloy.com |
电话:0592-5129696 传真:5129797 | 电子邮件:sales@chinatungsten.com |
钨钼文库:http://i.chinatungsten.com | 钨钼图片: http://image.chinatungsten.com |
钨新闻3G版:http://3g.chinatungsten.com | 钼业新闻: http://news.molybdenum.com.cn |


游离氨和补加酸对制取仲钨酸铵的影响
- 详细资料
- 分类:钨业知识
- 发布于 2015年12月30日 星期三 09:27
钨产品供应商:中钨在线科技有限公司 | 产品详情: http://cn.chinatungsten.com |
电话:0592-5129696 传真:5129797 | 电子邮件:sales@chinatungsten.com |
钨钼文库:http://i.chinatungsten.com | 钨钼图片: http://image.chinatungsten.com |
钨新闻3G版:http://3g.chinatungsten.com | 钼业新闻: http://news.molybdenum.com.cn |


仲钨酸铵结晶强化--超声波法
- 详细资料
- 分类:钨业知识
- 发布于 2015年12月30日 星期三 08:25
仲钨酸铵供应商:中钨在线科技有限公司 | 产品详情: ammonium-paratungstate.com |
电话:0592-5129696 传真:5129797 | 电子邮件:sales@chinatungsten.com |
钨钼文库:http://i.chinatungsten.com | 钨钼图片: http://image.chinatungsten.com |
钨新闻3G版:http://3g.chinatungsten.com | 钼业新闻: http://news.molybdenum.com.cn |

