硬质合金压坯滑移型拐角裂纹
- 詳細
- カテゴリ: 钨业知识
- 2017年5月18日(木曜)16:32に公開
- 作者: ruibin
- 参照数: 1961
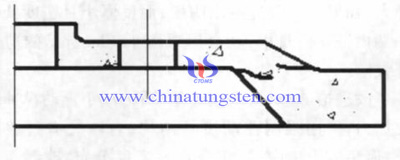
硬质合金供应商:中钨在线科技有限公司 | 产品详情: http://www.tungsten-carbide.com.cn |
电话:0592-5129696 传真:5129797 | 电子邮件:sales@chinatungsten.com |
钨钼文库:http://i.chinatungsten.com | 钨钼图片: http://image.chinatungsten.com |
钨新闻3G版:http://3g.chinatungsten.com | 钼业新闻: http://news.molybdenum.com.cn |


钨合金镀金板印刷技术
- 詳細
- カテゴリ: 钨业知识
- 2017年5月18日(木曜)08:56に公開
- 作者: meijin
- 参照数: 1658
随着电子技术的迅速发展,电子元器件会变得越来越小,焊球阵列封装(BGA)的球径和集成电路(IC)的间隙也越来越小,镀金板交会是表面贴装技术(SMT)的发展趋势之一。钨合金镀金板的应用包括:手机、液晶电视控制析/智能式家电、计算机及周边产品和医疗器材等。
SMT是表面组装技术(Surface Mounted Technology的缩写),是目前电子组装行业里最流行的一种技术和工艺。电子电路表面组装技术(Surface Mount Technology,SMT),称为表面贴装或表面安装技术。它是一种将无引脚或短引线表面组装元器件(简称SMC/SMD,中文称片状元器件)安装在印制电路板(Printed Circuit Board,PCB)的表面或其它基板的表面上,通过再流焊或浸焊等方法加以焊接组装的电路装连技术。
与喷锡板比较,钨合金镀金板具有以下特点:表面平整,不易氧化,储存时间长。钨合金镀金板印刷技术对印刷的要求非常严格:
脱离速度:7mm/s~8mm/s
印刷压力:5kg
刮刀角度:45o
印刷速度:60mm/s
最多印刷3~4次要清洗钢网
通过率:96.8%
钨合金镀金板工艺,包括以下步骤:a.在电路板上一次性做出包括镀金区域和外层镀金导线在内的所有板内图形,同时制作外层引线和导电辅助边;所述镀金区域与所述外层镀金导线相连接,所述外层镀金导线与所述外层引线相连接,所述外层引线与所述导电辅助边相连接;b.利用外层引线和导电辅助边作为导电,对电路板上的镀金区域和外层镀金导线进行镀金;c.采用激光定点熔线工艺去除掉外层引线,所述的激光熔线工艺是:通过激光高温侧面切断铜线和镀金区域的连接,其激光熔线的温度为1100摄氏度、时间为1min。钨合金镀金板工艺能够克服现有技术镀金渗镀、蚀刻不净、镀金质量差、镀金区域塌陷和工艺局限性的缺陷。
钨合金镀金板从传统镀金板三个方面调整:刮刀压力控制、零间隙印刷和钢网清洗系统、解决镀金板的印刷问题。取得了良好的效果,以其优良的耐磨性和焊接性能适应于表面组装技术(SMT)工艺中。
高比重合金供应商:中钨在线科技有限公司 | 产品详情: http://www.tungsten-alloy.com |
电话:0592-5129696 传真:5129797 | 电子邮件:sales@chinatungsten.com |
钨钼文库:http://i.chinatungsten.com | 钨钼图片: http://image.chinatungsten.com |
钨新闻3G版:http://3g.chinatungsten.com | 钼业新闻: http://news.molybdenum.com.cn |


粉末对硬质合金表面裂纹的影响
- 詳細
- カテゴリ: 钨业知识
- 2017年5月17日(水曜)16:02に公開
- 作者: ruibin
- 参照数: 1885
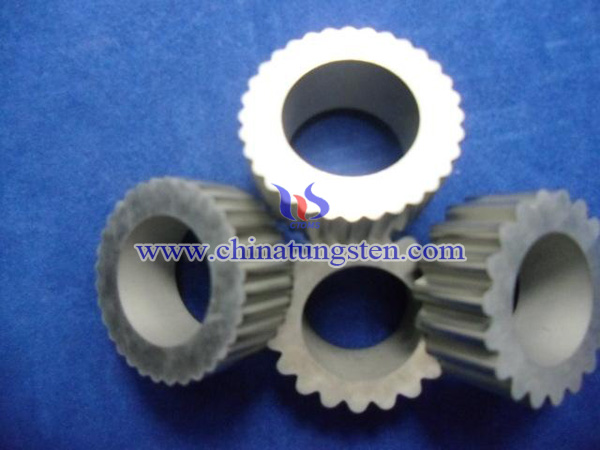
硬质合金供应商:中钨在线科技有限公司 | 产品详情: http://www.tungsten-carbide.com.cn |
电话:0592-5129696 传真:5129797 | 电子邮件:sales@chinatungsten.com |
钨钼文库:http://i.chinatungsten.com | 钨钼图片: http://image.chinatungsten.com |
钨新闻3G版:http://3g.chinatungsten.com | 钼业新闻: http://news.molybdenum.com.cn |


硬质合金压坯皱纹
- 詳細
- カテゴリ: 钨业知识
- 2017年5月17日(水曜)16:04に公開
- 作者: ruibin
- 参照数: 1931
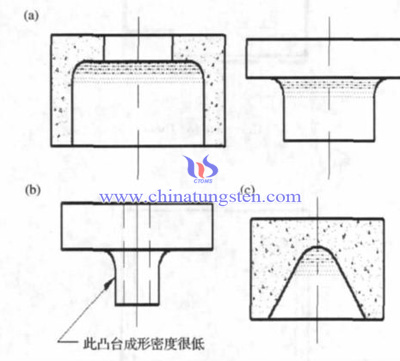
硬质合金供应商:中钨在线科技有限公司 | 产品详情: http://www.tungsten-carbide.com.cn |
电话:0592-5129696 传真:5129797 | 电子邮件:sales@chinatungsten.com |
钨钼文库:http://i.chinatungsten.com | 钨钼图片: http://image.chinatungsten.com |
钨新闻3G版:http://3g.chinatungsten.com | 钼业新闻: http://news.molybdenum.com.cn |


硬质合金压制表面裂纹
- 詳細
- カテゴリ: 钨业知识
- 2017年5月17日(水曜)16:00に公開
- 作者: ruibin
- 参照数: 2174
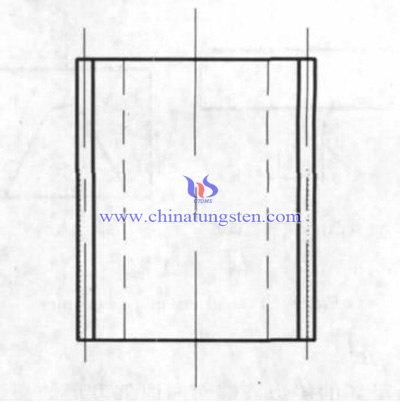
硬质合金供应商:中钨在线科技有限公司 | 产品详情: http://www.tungsten-carbide.com.cn |
电话:0592-5129696 传真:5129797 | 电子邮件:sales@chinatungsten.com |
钨钼文库:http://i.chinatungsten.com | 钨钼图片: http://image.chinatungsten.com |
钨新闻3G版:http://3g.chinatungsten.com | 钼业新闻: http://news.molybdenum.com.cn |

