钨合金防辐射包装
- 詳細
- カテゴリ: 钨业知识
- 2017年5月19日(金曜)09:00に公開
- 作者: meijin
- 参照数: 1828
防辐射包装是防止外界各种射线透过包装容器,从而破坏内装物质量的包装。如将感光胶卷盛装在能够防止光线照射的容器中。
辐射种类一般分为四种:1.电磁辐射;2.核辐射;3.光源辐射;4.微波辐射
固体电子器件对核辐射效应极其敏感,核辐射将使半导体中的原子电离或移位,影响该器件的工作特性。对光敏感的感光材料制品如照相胶卷、电影胶片、X光胶片、印相纸和其他光敏产品,在受到强光源辐射后将会损坏和失去使用价值。而微波辐射在导航、跟踪、通信、食物烘烤、医疗等领域得到广泛的应用,微波发生器和雷达会对周围附近和较远的物品产生不同程度的影响。电子设备的屏蔽可以防止外来电磁波的干扰,以确保设备正常工作;又可以阻止本电子设备工作时发射的电磁波去十扰别的电子设备工作和影响操作人员的健康。所以有必要对一些物品实施防辐射包装。
防辐射包装的关键是选择合适的包装材料,电磁敏感产品在生产、储存、运输、销售的过程中都要进行保护,这就需要防辐射电磁屏蔽包装,常用的防高能辐射的钨合金材料,能够防电磁辐射、光辐射、X射线辐射、防γ射线辐射、防中子辐射等;也有采用轻而小的钨合金纤维材料及添加稀土合金的复合材料来制作屏蔽包装。钨合金屏蔽件材料的辐射屏蔽性与材料的密度密切相关。更高的密度意味着更好的射线吸收能力和射线屏蔽能力,由于钨合金的密度比其他材料高,以钨合金为屏蔽材料的防辐射包装对各种辐射有着更好的屏蔽性,并且可减小防辐射包装的体积。对电子产品而言,单纯采用高性能屏蔽包装材料不一定能完全可靠有效地消除电磁辐射对产品性能的影响,还需要在电子产品的电路结构设计时综合考虑到电磁保护和屏蔽问题,因为传统的外包装屏蔽材料不能完全阻隔电磁波,所以现在人们普遍运用到防电磁辐射包装方法,即除了常用的防辐射包装材料除金属屏蔽材料外,还有导电性复合塑料屏蔽材料。将特制的钨合金细纤维的粒料加入到热塑性塑料中进行注塑,可以形成各种屏蔽性包装材料和容器,如模压导电复合塑料、填料导电复合薄膜、表面导电处理材料等。
高比重合金供应商:中钨在线科技有限公司 | 产品详情: http://www.tungsten-alloy.com |
电话:0592-5129696 传真:5129797 | 电子邮件:sales@chinatungsten.com |
钨钼文库:http://i.chinatungsten.com | 钨钼图片: http://image.chinatungsten.com |
钨新闻3G版:http://3g.chinatungsten.com | 钼业新闻: http://news.molybdenum.com.cn |


硬质合金挤压成形与注射成形的工艺异同
- 詳細
- カテゴリ: 钨业知识
- 2017年5月18日(木曜)16:53に公開
- 作者: ruibin
- 参照数: 2061
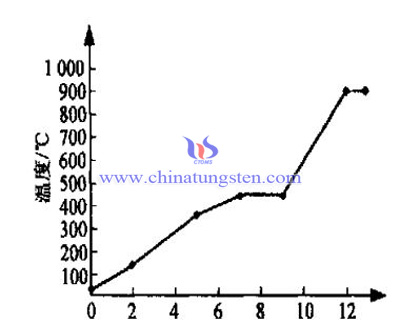
硬质合金供应商:中钨在线科技有限公司 | 产品详情: http://www.tungsten-carbide.com.cn |
电话:0592-5129696 传真:5129797 | 电子邮件:sales@chinatungsten.com |
钨钼文库:http://i.chinatungsten.com | 钨钼图片: http://image.chinatungsten.com |
钨新闻3G版:http://3g.chinatungsten.com | 钼业新闻: http://news.molybdenum.com.cn |


硬质合金压坯形位公差超差
- 詳細
- カテゴリ: 钨业知识
- 2017年5月18日(木曜)16:50に公開
- 作者: ruibin
- 参照数: 1843
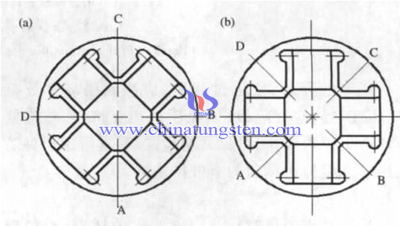
硬质合金供应商:中钨在线科技有限公司 | 产品详情: http://www.tungsten-carbide.com.cn |
电话:0592-5129696 传真:5129797 | 电子邮件:sales@chinatungsten.com |
钨钼文库:http://i.chinatungsten.com | 钨钼图片: http://image.chinatungsten.com |
钨新闻3G版:http://3g.chinatungsten.com | 钼业新闻: http://news.molybdenum.com.cn |


硬质合金挤压成形剂体系
- 詳細
- カテゴリ: 钨业知识
- 2017年5月18日(木曜)16:51に公開
- 作者: ruibin
- 参照数: 1937
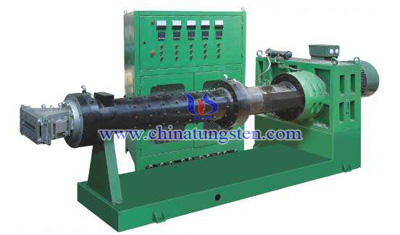
硬质合金供应商:中钨在线科技有限公司 | 产品详情: http://www.tungsten-carbide.com.cn |
电话:0592-5129696 传真:5129797 | 电子邮件:sales@chinatungsten.com |
钨钼文库:http://i.chinatungsten.com | 钨钼图片: http://image.chinatungsten.com |
钨新闻3G版:http://3g.chinatungsten.com | 钼业新闻: http://news.molybdenum.com.cn |


硬质合金压坯尺寸超差
- 詳細
- カテゴリ: 钨业知识
- 2017年5月18日(木曜)16:47に公開
- 作者: ruibin
- 参照数: 2006
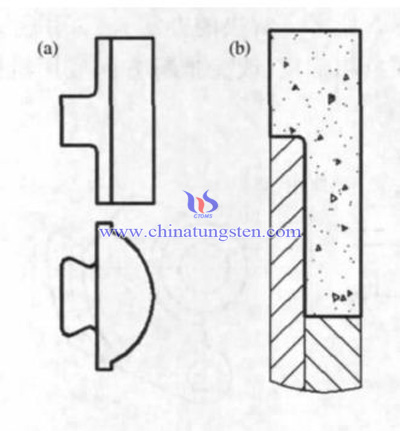
硬质合金供应商:中钨在线科技有限公司 | 产品详情: http://www.tungsten-carbide.com.cn |
电话:0592-5129696 传真:5129797 | 电子邮件:sales@chinatungsten.com |
钨钼文库:http://i.chinatungsten.com | 钨钼图片: http://image.chinatungsten.com |
钨新闻3G版:http://3g.chinatungsten.com | 钼业新闻: http://news.molybdenum.com.cn |

