放射治疗室屏蔽墙
- 詳細
- カテゴリ: 钨业知识
- 2017年5月11日(木曜)19:27に公開
放射性治疗是现代先进的治疗手段,可医治很多病症,在肿瘤治疗中的作用和地位日益突出,已成为治疗恶性肿瘤的主要手段之一。利用放射线治疗肿瘤的一种局部治疗方法。放射线包括放射性同位素产生的α、β、γ射线和各类x射线治疗机或加速器产生的x射线、电子线、质子束及其他粒子束等。但是用放射性治疗手段会产生放射性皮炎、放射性食管炎以及食欲下降、恶心、呕吐、腹痛、腹泻或便秘等诸多毒副反应。因此在使用放射性物质时要用医疗防辐射屏蔽设施加强自身保护。
在治疗过程中,使用医用钨合金屏蔽墙能够屏蔽对该控制区和非控制区的辐射影响,提高放射工作人员健康,降低对职业性外照射剂量水平。由于钨合金对X射线和γ射线具有良好的屏蔽性,是放射治疗室屏蔽墙材料的首选。屏蔽防护的原理是:射线包括穿透物质时强度会减弱,一定厚度的屏蔽物质能减弱射线的强度,在辐身源与人体之间设置足够厚的屏蔽物,便可降低辐射水平,使人们在工作所受到的剂量降低最高允许剂量以下,确保人身安全,达到防护目的,屏蔽防护的要点是在射线源与人体之间放置一种能有效吸收射线的屏蔽材料。在CT扫描显像期间,机房和控制室之间都有设置钨合金屏蔽墙来阻挡辐射。和传统的屏蔽材料,体积更小的钨合金屏蔽墙,密度却更高,钨合金屏蔽墙的体积只有铅的1/3,高密度性使其拥有和铅相当的射线吸收能力。由于钨合金的密度更高,墙的厚度也可以更薄。同时,由于钨合金屏蔽件材料独有的环保特性,被广泛地应用于核医疗中,作为放射治疗癌症肿瘤,医疗造影,及放射性示踪的辐射屏蔽材料。
高比重合金供应商:中钨在线科技有限公司 | 产品详情: http://www.tungsten-alloy.com |
电话:0592-5129696 传真:5129797 | 电子邮件:sales@chinatungsten.com |
钨钼文库:http://i.chinatungsten.com | 钨钼图片: http://image.chinatungsten.com |
钨新闻3G版:http://3g.chinatungsten.com | 钼业新闻: http://news.molybdenum.com.cn |


正电子药物钨合金防护装置
- 詳細
- カテゴリ: 钨业知识
- 2017年5月11日(木曜)19:23に公開
PET/CT是一种完全正电子放射性药物依赖型设备,正电子放射性药物用于PET/CT显像是在分子水平上反映细胞代谢、细胞受体活性和细胞核内的核酸合成与细胞基因的改变,从而达到早期分析和判定组织病变。没有必须的正电子放射性药物,PET/CT是无法发挥临床作用的。
因此,正电子放射性药物是放射治疗的必要治疗手段,相关医护人员和患者不可避免地会接触到此类药品。正电子类放射性药品是含短半衰期正电子核素的放射性药品,释放出的射线是一种特殊的、既看不见也摸不着的物质。这些射线各具特定能量,对物质具有不同的穿透能力和间离能力,从而使物质或机体发生一些物理、化学、生化变化。如果人体受到长时间大剂量的射线照射,就会使细胞器官组织受到损伤。所以,分装正电子药物应配置必要的正电子药物钨合金防护装置,其中包括通风橱、分装装置、活度计及污染检测仪等。钨合金防护装置因含有钨而具有高密度,高辐射屏蔽,防护性能好的特性,能够对各种放射性射线的进行屏蔽吸收,从而改善防护条件,减少放射源对医护人员及患者的辐射伤害,此外钨合金机械性强,可塑性强,可根据特定场所的特殊需求加工塑形,制作成各种不同形状、不同性能、不同配比的屏蔽防护件,且钨合金材质环保无公害,目前已被广泛地应用在医疗领域屏蔽件中。
高比重合金供应商:中钨在线科技有限公司 | 产品详情: http://www.tungsten-alloy.com |
电话:0592-5129696 传真:5129797 | 电子邮件:sales@chinatungsten.com |
钨钼文库:http://i.chinatungsten.com | 钨钼图片: http://image.chinatungsten.com |
钨新闻3G版:http://3g.chinatungsten.com | 钼业新闻: http://news.molybdenum.com.cn |


医用PET/CT钨合金屏蔽件
- 詳細
- カテゴリ: 钨业知识
- 2017年5月11日(木曜)19:19に公開
PET/CT是将正电子发身断层显像和CTE有机整合一体化的影像检查设备,它同时具有PET和CT功能,是目前临床核医学领域最先进的显像设备,由于PET/CT系统(含正电子计算机断层显像装置及配套的回旋加速器)在使用中均能产生电离辐射并对从业人员构成放射性职业病危害。需要对其外照射屏蔽防护。
钨以合金系状态广泛应用于屏蔽材料中,高比重钨合金屏蔽件主要由90%以上的钨粉与其他金属粉末如镍,铁,铜粉混合而成,它具有高密度,高辐射屏蔽,及环保的特性,一直以来是制造医用辐射屏蔽件的首选。
PET/CT系统主要由生产放射性核素的回旋加速器,放射性药物合成,受检者放射性药物注射与待诊及PET/CT扫描4个部分组成。其中放射性药物合成室主要外照射线种类为γ射线,PET/CT扫描室主要外照射线种类为γ射线;CT在扫描时产生X射线,X、γ射线均会导致医护工作人员及患者等受到不必要的照射伤害,医用PET/CT钨合金屏蔽件能够对穿透人体的射线吸收,能够屏蔽对该控制区和非控制区的辐射影响,提高放射工作人员健康,降低对职业性外照射剂量水平。扫描显像期间,在机房和控制室之间都有设置钨合金屏蔽墙来阻挡辐射。由于钨的硬度和密度都很高,使的钨合金非常适合应用于X射线以及以及辐射防护等医学领域,通常,X射线和γ射线的吸收能力与屏蔽材料的密度是成正比的,由于医用PET/CT钨合金屏蔽件的钨合金材料具有对各种射线的屏蔽本领高的优点,对阻止150keV的γ射线,衰减90%的厚度仅需3mm厚,非常适合于对空间分辨率要求高的场合。钨合金材料有着很高的密度(比铅大60%),减小了射线屏蔽件的尺寸,却不影响射线屏蔽效果。同时,由于医用钨合金屏蔽件材料独有的环保特性,遍布全球的客户正在广泛使用钨合金的可靠的辐射屏蔽件。
高比重合金供应商:中钨在线科技有限公司 | 产品详情: http://www.tungsten-alloy.com |
电话:0592-5129696 传真:5129797 | 电子邮件:sales@chinatungsten.com |
钨钼文库:http://i.chinatungsten.com | 钨钼图片: http://image.chinatungsten.com |
钨新闻3G版:http://3g.chinatungsten.com | 钼业新闻: http://news.molybdenum.com.cn |


注射成型缺陷-熔接缝
- 詳細
- カテゴリ: 钨业知识
- 2017年5月11日(木曜)18:55に公開
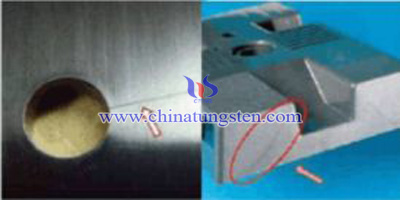
溶剂脱脂技术种类
- 詳細
- カテゴリ: 钨业知识
- 2017年5月11日(木曜)18:48に公開
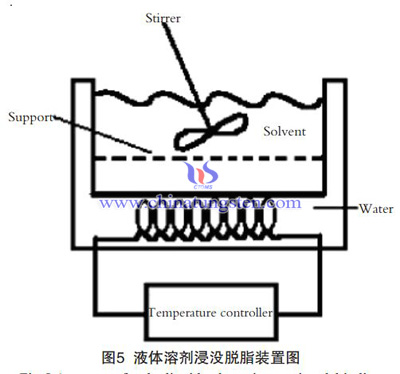
硬质合金供应商:中钨在线科技有限公司 | 产品详情: http://www.tungsten-carbide.com.cn |
电话:0592-5129696 传真:5129797 | 电子邮件:sales@chinatungsten.com |
钨钼文库:http://i.chinatungsten.com | 钨钼图片: http://image.chinatungsten.com |
钨新闻3G版:http://3g.chinatungsten.com | 钼业新闻: http://news.molybdenum.com.cn |


热脱脂过程和机理
- 詳細
- カテゴリ: 钨业知识
- 2017年5月11日(木曜)18:45に公開
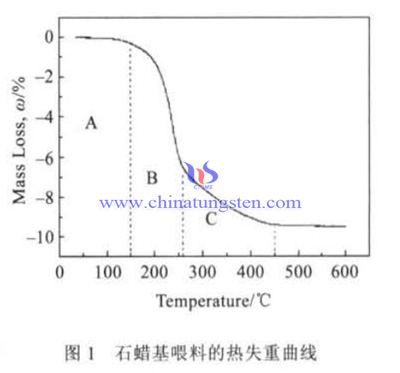
硬质合金供应商:中钨在线科技有限公司 | 产品详情: http://www.tungsten-carbide.com.cn |
电话:0592-5129696 传真:5129797 | 电子邮件:sales@chinatungsten.com |
钨钼文库:http://i.chinatungsten.com | 钨钼图片: http://image.chinatungsten.com |
钨新闻3G版:http://3g.chinatungsten.com | 钼业新闻: http://news.molybdenum.com.cn |


粉末注射成型-脱脂
- 詳細
- カテゴリ: 钨业知识
- 2017年5月11日(木曜)18:42に公開
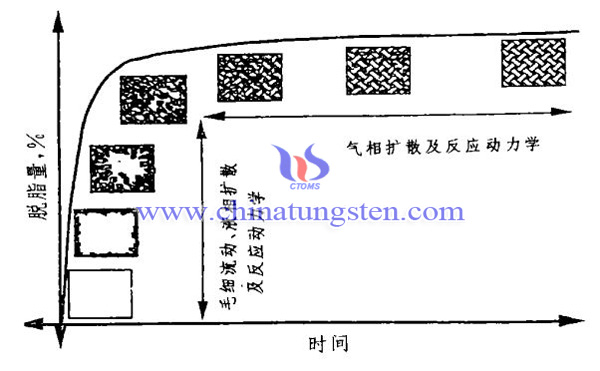
硬质合金供应商:中钨在线科技有限公司 | 产品详情: http://www.tungsten-carbide.com.cn |
电话:0592-5129696 传真:5129797 | 电子邮件:sales@chinatungsten.com |
钨钼文库:http://i.chinatungsten.com | 钨钼图片: http://image.chinatungsten.com |
钨新闻3G版:http://3g.chinatungsten.com | 钼业新闻: http://news.molybdenum.com.cn |


注射成型缺陷,翘曲变形
- 詳細
- カテゴリ: 钨业知识
- 2017年5月11日(木曜)18:32に公開
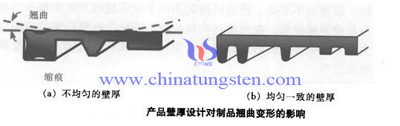
硬质合金供应商:中钨在线科技有限公司 | 产品详情: http://www.tungsten-carbide.com.cn |
电话:0592-5129696 传真:5129797 | 电子邮件:sales@chinatungsten.com |
钨钼文库:http://i.chinatungsten.com | 钨钼图片: http://image.chinatungsten.com |
钨新闻3G版:http://3g.chinatungsten.com | 钼业新闻: http://news.molybdenum.com.cn |


注射成型缺陷-飞边
- 詳細
- カテゴリ: 钨业知识
- 2017年5月11日(木曜)18:28に公開
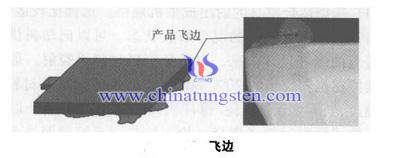
硬质合金供应商:中钨在线科技有限公司 | 产品详情: http://www.tungsten-carbide.com.cn |
电话:0592-5129696 传真:5129797 | 电子邮件:sales@chinatungsten.com |
钨钼文库:http://i.chinatungsten.com | 钨钼图片: http://image.chinatungsten.com |
钨新闻3G版:http://3g.chinatungsten.com | 钼业新闻: http://news.molybdenum.com.cn |


注射成型缺陷-裂纹
- 詳細
- カテゴリ: 钨业知识
- 2017年5月11日(木曜)18:22に公開
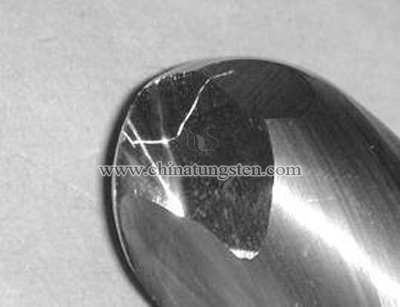
硬质合金供应商:中钨在线科技有限公司 | 产品详情: http://www.tungsten-carbide.com.cn |
电话:0592-5129696 传真:5129797 | 电子邮件:sales@chinatungsten.com |
钨钼文库:http://i.chinatungsten.com | 钨钼图片: http://image.chinatungsten.com |
钨新闻3G版:http://3g.chinatungsten.com | 钼业新闻: http://news.molybdenum.com.cn |

