钨螺旋线镀金
- 詳細
- カテゴリ: 钨业知识
- 2017年5月16日(火曜)20:10に公開
- 参照数: 1882
螺旋线行波管是一种具有宽频带的微波管,广泛应用于航空航天、卫星通讯系统、雷达系统和电子对抗系统等领域,在现代军事电子装备中显示出不可替代的作用。螺旋线慢波系统是螺旋线行波管中能量交换的关键部件,直接影响行波管工作稳定性与可靠性,慢波系统中热量主要产生于螺旋线的高频损耗和电子轰击。螺旋线多采用高强度、高硬度、熔点高、机械强度好的钨材料制备。在钨制成的钨螺旋线内外表面镀覆低损耗薄膜材料用来降低钨螺旋线的高频损耗,称为钨螺旋线镀金。
随着行波管功率量级和工作频率的不断提高,特别是进入毫米波频段,关键部件螺旋线(钨材料,电阻率大)高频损耗的显著增大给行波管高频散热带来了极大的压力,钨螺旋线的高频损耗增大,严重影响行波管的输出功率和工作稳定性。为了降低钨螺旋线的高频损耗,一般采用对钨螺旋线内外表面镀覆低损耗薄膜材料的方法,如镀金薄膜。
钨螺旋线在镀金处理时须特别注意,如在钨螺旋线表面直接镀金,二者之间结合性能不好。采用增加过渡层铜的前处理方法,能够改善镀金层与钨基体的结合性能,且镀金层表面平整、光滑、致密,晶粒细小、均匀。但也要注意把控,预镀层过薄,影响后续镀金层覆盖效果,导致螺旋线表面部分裸露;预镀层过厚,氢炉高温处理过程中可形成铜含量较高的Cu-Au合金易熔化,镀金层出现起皮脱落等现象。过渡层应控制在适宜厚度,所获得的镀金层质量较好,且高温结合效果理想。
高比重合金供应商:中钨在线科技有限公司 | 产品详情: http://www.tungsten-alloy.com |
电话:0592-5129696 传真:5129797 | 电子邮件:sales@chinatungsten.com |
钨钼文库:http://i.chinatungsten.com | 钨钼图片: http://image.chinatungsten.com |
钨新闻3G版:http://3g.chinatungsten.com | 钼业新闻: http://news.molybdenum.com.cn |


钨合金金箔
- 詳細
- カテゴリ: 钨业知识
- 2017年5月15日(月曜)19:08に公開
- 参照数: 1708
金箔是用黄金锤成的薄片。黄金由于具有良好的延展性和可塑性,一两(31.25克)纯金可锤成万分之一毫米厚、面积为16.2平方米的金箔。在中国金箔是中华民族传统的工艺品,源于东晋,成熟于南朝,流行于宋、齐、梁、陈,南京是中国金箔的发源地。如今南京是世界最大的金箔生产中心。
人们对黄金的赞美中常常也在无形中体现了黄金的特殊工艺,如:“金枝玉叶”、“金碧辉煌”,所描述的就是黄金工艺的一个重要品种——金箔。钨合金金箔的外观与黄金耳环相似,金光灿烂,五彩缤纷,令人爱不释手。钨合金加工成钨合金金箔制品,在钨合金制品表面经过镀金处理,其形式和黄金金箔的外观和相似的手感而被称为“黄金替代品”。钨合金金箔密度与黄金相近,且独有的高密度、耐腐蚀、耐磨损特性,和黄金一样具有良好的延展性和可塑性,它性质稳定,永久不变色、抗氧化、防潮湿、防变霉、防虫咬、防辐射,用钨合金制成的镀金金箔具有广泛的用途。作为一种性价比极高的产品越来越受到人们的欢迎,金箔是用途最广泛的装饰用金箔,适用于任何装饰贴金,但因钨合金并不是黄金,所以,钨合金金箔仅用于装饰以及纪念。
钨合金金箔可广泛地运用于佛教,道教、古典园林建筑装饰、医药以及食品等行业,佛像贴金、雕梁画栋贴金、牌匾楹联、装饰用贴金等等,为促进传统工艺的发展,作出了巨大的贡献。
高比重合金供应商:中钨在线科技有限公司 | 产品详情: http://www.tungsten-alloy.com |
电话:0592-5129696 传真:5129797 | 电子邮件:sales@chinatungsten.com |
钨钼文库:http://i.chinatungsten.com | 钨钼图片: http://image.chinatungsten.com |
钨新闻3G版:http://3g.chinatungsten.com | 钼业新闻: http://news.molybdenum.com.cn |


钨合金药型罩
- 詳細
- カテゴリ: 钨业知识
- 2017年5月15日(月曜)18:28に公開
- 参照数: 1936
破甲技术作为攻击装甲目标的一种重要手段,近几十年来在我国进行了系统的研究。作为空心装药战斗部的关键部件之一的药型罩,其研究也相应得到加强。钨合金药型罩称为弹的心脏。
药型罩有两大基本类型,即角度小于700的锥形药罩和角度大于1200的盘形或球缺形药型罩。作为聚能装药的核心部件在爆炸产物的推动下形成射流最终对目标进行侵彻。所以药型罩的质量直接决定了爆炸战斗部的侵彻和破甲能力。破甲射流的侵彻能力与射流的长度、射流与目标材料的密度比的平方根、以及射流速度的平方成正比;还与射流的稳定性、连续性、后柞大小等因素有关。有利于提高射流稳定性的材料因互包括:高熔点、高密度、高声速、细晶粒、适当的晶粒取向、良好的延伸率、最小的制造缺陷、低杂质含量、高动态强度、高韧性等。所以,用于制造药型罩的金属材料必须具备密度大、塑性好、强度适当、熔点不能太低等特性。
经研究,把不同性能的金属或合金,按照药型罩的设计要求复合起来发挥综合优势,于是出现了复合药型罩——钨合金药型罩,它的能量转换与吸收机制与单金属药型罩相比更合理,化学能的利用率更充分,破甲性能更优越,造价也更低。钨合金药型罩既有钨的高强度、高硬度、低膨胀系数等特性,同时又有其他合金的高塑性、良好的导电导热性互补,这种特有的综合性能使钨合金药型罩得到广泛的应用,钨合金药型罩利用不同合金材料性能的互补以及最佳的结构使药型罩既具有先进材料效应又具有先进结构效应,从而大大提高了破甲弹的侵彻威力。
高比重合金供应商:中钨在线科技有限公司 | 产品详情: http://www.tungsten-alloy.com |
电话:0592-5129696 传真:5129797 | 电子邮件:sales@chinatungsten.com |
钨钼文库:http://i.chinatungsten.com | 钨钼图片: http://image.chinatungsten.com |
钨新闻3G版:http://3g.chinatungsten.com | 钼业新闻: http://news.molybdenum.com.cn |


钨合金破片
- 詳細
- カテゴリ: 钨业知识
- 2017年5月15日(月曜)18:25に公開
- 参照数: 1928
现代战争中空袭作战的地位和作用越来越突出,已成为决定整块战争胜负的重要因素。防空战斗部中破片式战斗部具有结构简单、制造成本低、杀伤半径大、摧毁目标能力好、对各种作战条件适应性强等优点,该战斗越来越受到各国的重视。钨合金破片一般是用在地雷、手榴弹等弹药上的用于杀伤有生力量的部件。由于预制破片有一个会影响弹体结构的负面作用,通常只在低膛压火炮弹药里采用,如迫弹和大口径榴弹。应用最为普遍的还要属航弹、手榴弹、地雷等。钨柱作为破片的一种类型,由于密度高、穿甲能力强,成为防空、反辐射、面杀伤的主要杀伤元素之一,并得到广泛应用。
钨合金破片由于其密度大,保持速度和穿甲的能力强,被日益广泛地用作杀伤弹药的杀伤元素。它是一种具有穿甲及随后引爆的多功能毁伤材料,利用该材料制造的弹体可有效解决多种毁伤功能匹配不良的缺陷。根据弹药战术使用的要求,往往希望破片在满足穿甲威力的同时还具有引燃或纵火功能,于是具有这一功能的新的钨合金材料——钨锆合金应运而生。对于防空反导一来说,拦截并起爆来袭导弹的战斗部装药是最理想的毁伤方式之一。对于采用普通惰性破版的反导战斗部来说,若实现这种毁伤方式需要很大的破片质量,这对有限尺寸的战斗来说,势必大大减少破片数量和密度,从而降低目标被击中和毁伤的概率。钨锆合金破片对反导战斗部具有潜在的应用前景。
经过实验证明,钨合金破片比其他破片具有更强的起爆引燃战斗部装药的能力,对于毁伤导弹战斗部更有效。钨锆合金破片的起爆主要是机械作用,其他一些破片的起爆主要是冲击波作用。
高比重合金供应商:中钨在线科技有限公司 | 产品详情: http://www.tungsten-alloy.com |
电话:0592-5129696 传真:5129797 | 电子邮件:sales@chinatungsten.com |
钨钼文库:http://i.chinatungsten.com | 钨钼图片: http://image.chinatungsten.com |
钨新闻3G版:http://3g.chinatungsten.com | 钼业新闻: http://news.molybdenum.com.cn |


纳米碳化钨
- 詳細
- カテゴリ: 钨业知识
- 2017年5月15日(月曜)18:22に公開
- 参照数: 1845
纳米碳化钨是制造超细晶硬质合金的重要原料,是一种高技术含量的高性能粉末材料,主要应用于生产硬质合金和各种硬面材料。其性能对超细晶硬质合金的性能有重要影响,纳米钨粉是制备纳米碳化钨和其他纳米/超细钨合金的重要原材料。
纳米硬金合金比普通硬质合金具有更高的强度、硬度、耐磨性等优良的性能。随着研究的不断深入,纳米硬质合金的质量稳定性也越来越受关注。原料碳化钨质量的好坏是获得组织结构均匀,综合性能优异的纳米硬质合金的关键。
纯碳化钨易碎,若掺入少量钛、钴等金属,就能减少脆性。用作钢材切割工具碳化钨,常加入碳化钛、碳化钽或它们混合物,以提高抗爆能力。碳化钨化学性质稳定。碳化钨的抗高温氧化能力存在不足,温度达到500℃-800℃时,在空气中易氧化分解为W2C和碳。这个问题可通过用耐热抗氧化的金属做包裹层或粘结相,对碳化钨颗粒进行预保护。也可以与TaC、TIC等固溶形成复合碳化物,改善碳化钨的耐热抗氧化性能。碳化钨在Ar气氛中加热至2850摄度仍然稳定,在高温氮气中亦不受影响。纳米碳化钨粉不溶于冷水,耐酸性强,硬度高,弹性模量大。纳米碳化钨号称硬王,除了硬度高以外,尚有耐磨损、耐腐蚀、耐高温等特性。
碳化钨应用与用途
1.大量用作高速切削车刀、窑炉结构材料、喷气发动机部件、金属陶瓷材料、电阻发热元件等制得。
2.用于制造切削工具、耐磨部件,铜、钴、铋等金属的熔炼坩埚,耐磨半导体薄膜。
3.用作超硬刀具材料、耐磨材料。它能与许多碳化物形成固溶体。碳化钨-TiC-Co硬质合金刀具已获得广泛应用。
4.作为NbC-C及TaC-C三元体系碳化物的改性添加物,既可降低烧结温度,又能保持优良性能,可用作宇航材料。
高比重合金供应商:中钨在线科技有限公司 | 产品详情: http://www.tungsten-alloy.com |
电话:0592-5129696 传真:5129797 | 电子邮件:sales@chinatungsten.com |
钨钼文库:http://i.chinatungsten.com | 钨钼图片: http://image.chinatungsten.com |
钨新闻3G版:http://3g.chinatungsten.com | 钼业新闻: http://news.molybdenum.com.cn |


纳米钨合金
- 詳細
- カテゴリ: 钨业知识
- 2017年5月15日(月曜)18:19に公開
- 参照数: 1838
难熔金属钨合金具有一系列优异的物理力学性能。在国防军工、航空航天、电子信息、能源、冶金和机械加工工业等领域中具有十分广泛的用途,在国民经济中占有重要地地位。如W-Ni-Fe高密度合金用作集束弹、侵彻弹、易碎弹和穿甲弹等材料,有着越来越广阔的应用前景。W-Cu-(Mo-Cu)材料具有好的导热性和导电性、小的热膨胀系数,可广泛用作电接触材料,微电子封装材料和热沉材料。WC-Co硬质合金具有高度的硬度强度和好的耐磨性。是一种仅次于金刚石的硬质超硬材料,广泛用作切削加工工具,被称为现代工业的牙齿。
随着科学技术日新月异的发展与更新换代,对材料的要求愈来愈高。与之相适应,采用新的技术和新型材料是研究发展新型高性能多功能钨合金材料的发展方向。
纳米材料的应运而生赋予该类合金更加广泛的用途。如纳米W-Cu材料具有非常高的致密度(可达到近乎全致密)和高的导电导热率,该合金可广泛用作各种集成电路、可控硅等大功率微波器件的电子封装,热沉材料在雷达和各种微电子应用中是一种很重要的热沉和封装电子材料。纳米WC硬质合金的最高抗弯强度可达5000MPa,用于电子工业集成电路板的微型钻和计算机打印针,具有十分广阔的应用前景和市场需求。纳米钨基高密度合金的最高拉伸强度可达1700MPa,相当于传统钨基合金的2倍,是未来极为重要的关键军工材料。采用纳米粉末制备的钨合金块材料具有非常优越的潜在物理力学性能,用作高性能结构件和高性能电子、微电子等功能材料等方面都将具有很大的潜在优势,可以更好的满足高性能新型材料的要求。
高比重合金供应商:中钨在线科技有限公司 | 产品详情: http://www.tungsten-alloy.com |
电话:0592-5129696 传真:5129797 | 电子邮件:sales@chinatungsten.com |
钨钼文库:http://i.chinatungsten.com | 钨钼图片: http://image.chinatungsten.com |
钨新闻3G版:http://3g.chinatungsten.com | 钼业新闻: http://news.molybdenum.com.cn |


高密度钨合金
- 詳細
- カテゴリ: 钨业知识
- 2017年5月15日(月曜)18:16に公開
- 参照数: 2018
钨合金是一种密度较高(一般大于等于16.5g/cm3)的两相合金,又称高密度钨合金。高密度钨合金最早出现于1935年,当时被用作屏蔽材料。经过多年发展,高密度钨合金目前不仅在诸如航空、航天和兵器等军事工业部门中得到广泛应用,在民用工业部门也越来越多地被人们所使用。高密度钨合金已发展出民多个系列,其中应用最为广泛的是W-Ni-Fe和W-Ni-Cu两个系列。高密度钨合金作为一种两相合金,兼具强度高、塑性好、韧性强等特点,并可以用过形变等来提高力学性能。在较高温下,其依然能保持良好的性能,这在军事等领域是非常重要的。此外,高密度钨合金还易于进行多种机械加工。正是由于其具有的一系列优良特性,钨合金不仅得到了广泛运用,也受到国内外研究者们的关注。而随科技和生产的发展,人们对高密度钨合金的强度、硬度和伸长率等性能提出了更高的要求。
经过大量研究实践证明,通过控制钨合金的成分,并选择合适的成形、烧结工艺,可得到微观组织较理想的钨合金材料,这样大大地提高了钨合金的性能以满足在不同运用的不同要求;后期的加工处理可改变高密度钨合金的显微组织(如获得具有强化作用的钨颗粒纤维状组织),较大的提高材料强度,经相应后处理可保证适当的伸长率,钨合金的形变强化工艺简单、强化效果显著。钨合金的这些性能及特点使得其广泛用于电子、电光源工业,也在航天、铸造、武器等部门中用于制作火箭喷管、压铸模具、穿甲弹芯、触点、发热体和隔热屏等。
高比重合金供应商:中钨在线科技有限公司 | 产品详情: http://www.tungsten-alloy.com |
电话:0592-5129696 传真:5129797 | 电子邮件:sales@chinatungsten.com |
钨钼文库:http://i.chinatungsten.com | 钨钼图片: http://image.chinatungsten.com |
钨新闻3G版:http://3g.chinatungsten.com | 钼业新闻: http://news.molybdenum.com.cn |


钨合金辐射屏蔽件
- 詳細
- カテゴリ: 钨业知识
- 2017年5月15日(月曜)18:09に公開
- 参照数: 1706
钨合金辐射屏蔽件是由柔韧的耐热屏蔽沉浸在有机硅聚合物的钨铁金属粉末制成的辐射屏蔽装置。随着人们对环境的破坏,辐射对人的危害也逐渐加强。因此防辐射装置也渐渐被人们所重视。钨合金作为一种辐射屏蔽材料已被人们广泛利用。
钨合金辐射屏蔽件对辐射的屏蔽是通过材料中所含吸收物质对辐射的吸收完成的。物质对射线的吸收大体以下述两种方式进行:即能量吸收和粒子吸收。科学家们发现使用使用高比重材料可大幅减小辐射水平,证实防辐射能力和材料密度有着紧密的关系,密度越大屏蔽性能越好。钨合金有很大的密度,所以它的屏蔽性能很高。钨合金辐射屏蔽件具有高密度(密度比铅高60%),良好的机械加工性,耐腐蚀性,良好的辐射吸收能力(吸收能力优于铅),高强度等特性。和同等重量的铅屏蔽件相比,钨合金辐射屏蔽件的辐射吸收能力与铅强,而体积和厚度却远小于铅。且钨合金在长期使用中并没有发现对人或者环境有危害,在这个方面比铅就有更大的优势。钨合金对γ射线的线性衰减能力使其在屏蔽件领域具有很大的优势,且等量的钨合金屏蔽提供比同等铅屏蔽更低的风险。
钨合金辐射屏蔽件因为期具有高密度,高辐射屏蔽及环保等特性,现在已成为制造辐射屏蔽件的首选。钨辐射屏蔽件在医疗、核电、军事、石油等行业都有其重要的运用地位。
高比重合金供应商:中钨在线科技有限公司 | 产品详情: http://www.tungsten-alloy.com |
电话:0592-5129696 传真:5129797 | 电子邮件:sales@chinatungsten.com |
钨钼文库:http://i.chinatungsten.com | 钨钼图片: http://image.chinatungsten.com |
钨新闻3G版:http://3g.chinatungsten.com | 钼业新闻: http://news.molybdenum.com.cn |


硬质合金脱脂缺陷
- 詳細
- カテゴリ: 钨业知识
- 2017年5月15日(月曜)17:21に公開
- 参照数: 2055
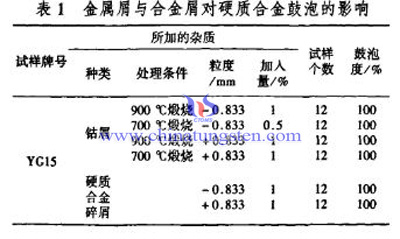
硬质合金供应商:中钨在线科技有限公司 | 产品详情: http://www.tungsten-carbide.com.cn |
电话:0592-5129696 传真:5129797 | 电子邮件:sales@chinatungsten.com |
钨钼文库:http://i.chinatungsten.com | 钨钼图片: http://image.chinatungsten.com |
钨新闻3G版:http://3g.chinatungsten.com | 钼业新闻: http://news.molybdenum.com.cn |


硬质合金脱脂裂纹产生原因
- 詳細
- カテゴリ: 钨业知识
- 2017年5月15日(月曜)17:20に公開
- 参照数: 1937
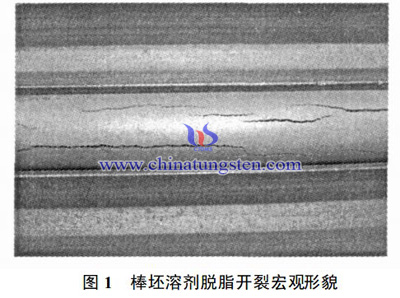
硬质合金供应商:中钨在线科技有限公司 | 产品详情: http://www.tungsten-carbide.com.cn |
电话:0592-5129696 传真:5129797 | 电子邮件:sales@chinatungsten.com |
钨钼文库:http://i.chinatungsten.com | 钨钼图片: http://image.chinatungsten.com |
钨新闻3G版:http://3g.chinatungsten.com | 钼业新闻: http://news.molybdenum.com.cn |

