钨芯脱壳穿甲弹
- 詳細
- カテゴリ: 钨业知识
- 2017年5月12日(金曜)18:43に公開
- 参照数: 2639
脱壳穿甲弹曾是坦克炮发射的动能穿甲弹的主流,是传统穿甲弹提升破坏效果的改良型。在一个比主炮口径小的钨合金制弹芯再套上由轻金属制造的套环,套环和主炮口径相同,当发射时轻金属套环脱落而钨合金弹芯继续飞向目标,这是为了要兼顾以大口径坦克炮发射高速炮弹和以小口径炮弹较易穿透装甲的要求,这种炮弹的弹芯长径比不可大于1:7,以便用线膛炮发射。钨芯脱壳穿甲弹的弹头采用了脱壳原理和高密度钨合金的新结构、新材料,具有初速高、弹道低伸、飞行时间短、命中精度高、侵彻力大等特点,能有效地对付快速运动目标;其弹心断面密度大,与硬质钢心或碳化钨弹心在侵彻过程中整个破碎相反,钨合金弹心可展性较好,以飞溅式穿甲,具有极好的二次侵彻特性,对大着角、夹心和多层结构复合装甲的穿甲效果更为明显。已在军事方面被广泛采用。
钨心脱壳穿甲弹弹头的典型结构,由弹心、前托(上托)、底托和闭气环组成。在膛内,底托包覆着弹心在火药燃气作用下沿枪管运动,使质量较轻的弹头获得高初速和转速。出枪口后,底托脱落,弹心飞向目标。弹心是穿甲元件,由钨合金材料制成。因为钨合金的比重为18g/cm3,是钢比重(7.8g/cm3)的2.3倍,所以弹心的断面密度大,有利于提高飞行时的存速能力和对钢板的侵彻能力。
高比重合金有个最突出的特点就是比重高也就是大家常说的密度大,此外,钨合金耐高温;热稳定性好,在穿甲弹飞行过程中与空气摩擦产生大量的热,要是穿甲弹中的填充物热性不好就会使它粘结在一起,无法达到穿甲的作用。钨合金的这一特性使穿甲弹很好的发挥了应有的功效。
高比重合金供应商:中钨在线科技有限公司 | 产品详情: http://www.tungsten-alloy.com |
电话:0592-5129696 传真:5129797 | 电子邮件:sales@chinatungsten.com |
钨钼文库:http://i.chinatungsten.com | 钨钼图片: http://image.chinatungsten.com |
钨新闻3G版:http://3g.chinatungsten.com | 钼业新闻: http://news.molybdenum.com.cn |


钨芯穿甲弹
- 詳細
- カテゴリ: 钨业知识
- 2017年5月12日(金曜)18:39に公開
- 参照数: 3173
钨芯穿甲弹是在普通的穿甲弹的基础上发展起来的高效穿甲弹。是现代军事武器常用的弹种之一。穿甲弹内部装载钨合金弹芯所以称之为钨芯穿甲弹。
为了击穿更厚的装甲,势必要提高炮弹射击后的动能,制造更大的炮弹,相对的要有更大的大炮来使用,一味的加大尺寸并不是唯一的方法。所以就在弹头的材质上做点功夫,由于穿甲弹速度越大,头部越硬越好,所以在炮弹中又包了一个小一号的由钨芯制成的弹头,命中目标后小弹头被挤出并对对方造成杀伤。钨芯穿甲弹由风帽、弹芯、弹体、曳光管组成。弹芯是穿甲弹的主体也是关键部位,用高密度钨合金制成。钨合金一种致密金属不仅密度大而且硬度超凡,是制造硬芯弹药的主要材料。弹体用低碳钢或铝合金制造,主要起支承弹芯的作用,其上有导带,能保证弹丸旋转稳定。弹芯被固定在弹体中间,当碰击装甲瞬间,弹体破裂,弹芯进行穿甲。钨芯穿甲弹具有“速度高、弹道低伸、穿甲威力大”等优点。其中“穿甲威力大”是该弹较同等口径弹种最为突出的优点。
钨芯穿甲弹用高比重钨合金制造,密度可达到18g/cm3,弹心的断面密度大,有利于提高飞行时的存速能力和对钢板的侵彻能力,提高穿甲弹的动能给装甲致命的打击。钨合金还是一种耐高温、热稳定性好金属材料。钨芯在穿甲弹内要承受高压高温环境,使用钨合金制造的弹芯,即使在高温高压环境下也不会粘结变形等。
高比重合金供应商:中钨在线科技有限公司 | 产品详情: http://www.tungsten-alloy.com |
电话:0592-5129696 传真:5129797 | 电子邮件:sales@chinatungsten.com |
钨钼文库:http://i.chinatungsten.com | 钨钼图片: http://image.chinatungsten.com |
钨新闻3G版:http://3g.chinatungsten.com | 钼业新闻: http://news.molybdenum.com.cn |


钨合金方块
- 詳細
- カテゴリ: 钨业知识
- 2017年5月12日(金曜)18:36に公開
- 参照数: 1630
钨合金方块是钨合金的一种块状产品,具有密度高、抗压强度好、抗氧化性、良好的导电、导热性和耐腐蚀及高密度(密度在16g/cm3到18.5g/cm3),远高于镍、钛、铅。钨合金方块还有良好的抗拉强度,膨胀系数和大弹性系数。在军事中用做穿甲弹弹芯填充材料以及各种配重件等。
纯钨的脆性极高,钨合金方块加工时在复合材料中添加镍与铁,在液相烧结过程使用熔料。镍铁相结合钨颗粒,从而保证钨合金方块具有高延展性,钨合金方块的优势在于具有极佳的机械加工性能,能够承受高负载。此外,钨合金方块具有很好的物理化学性能,如密度高,硬度强,耐高温腐蚀等。密度可以达到18.5g/cm3,是同等钢材料的两倍,这使得钨合金在配重领域有很大的优势。
钨合金方块的应用主要包括两个方面,配重和军事运用。
钨合金具有很高的密度,并且和铅相比较钨合金对环境没有危害,因此钨合金在配重方面的运用广泛。钨合金方块做为配重能够弥补摆动、重量转移、失衡和振动等情况,形成或改变重心,确保最佳平衡性。如飞机配重、潜艇配重、赛车配重、武器配重、运动器材配重等。
在军事方面钨合金方块可作为穿甲弹弹芯填充材料,弹芯是穿甲弹的主体也是关键部位,钨合金一种致密金属不仅密度大而且硬度超凡,是制造硬芯弹药的主要材料。因为钨合金方块有很好的抗拉强度,所以对于穿甲弹的性能有很大的提高。
钨合金还可用于武器的配重,可以减小重型武器的后坐力,保护枪管遭到撞击时不会影响射击的精确度。
高比重合金供应商:中钨在线科技有限公司 | 产品详情: http://www.tungsten-alloy.com |
电话:0592-5129696 传真:5129797 | 电子邮件:sales@chinatungsten.com |
钨钼文库:http://i.chinatungsten.com | 钨钼图片: http://image.chinatungsten.com |
钨新闻3G版:http://3g.chinatungsten.com | 钼业新闻: http://news.molybdenum.com.cn |


钨合金砧块
- 詳細
- カテゴリ: 钨业知识
- 2017年5月12日(金曜)18:31に公開
- 参照数: 1661
镦模锻工艺是由电热镦粗后再进行加工的工艺方法,电热镦粗用砧块材料是随气门用钢材的发展而发展。随着内燃机燃气温度的提高,要求有更高的红硬性,耐磨性的砧块相适应。钨合金砧块是具有较好综合性能的砧块,能满足不同气门钢种发展的要求,是促进镦模锻工艺发展的关键。
钨合金砧块具有以下优异性能:1、良好的导电性能,而砧块本身不要过热。2、良好的高温硬度和强度,在镦粗的高温高压下,砧块材料不易变形。3、良好抗氧化性能和抗电弧烧蚀性能,钨合金砧块红硬性高,使用寿命长。
电热镦粗过程是一个断续的周期性作业,砧块材料还将承受热疲劳应力的反复作用,特别是随着内燃机燃气温度的提高,对气门钢材材质的性能,如耐高温性能、耐磨性能等也有更高的要求。由于气门钢种的不断发展,气门钢材能否镦粗,和其选用具有高性能的钨合金做砧块材料有着极大的关系。钨合金砧块以钨为基,添加适量的镍、铁、铜或钼等作为粘结相,采用粉末治金工艺方法,经混料、压制、烧结等工艺制备出不同组分的钨合金砧块及复合结构砧块,产品经性能测试,具有高的室温硬度及高温硬度。实验表明钨合金砧块钨、镍、铁系钨合金最理想,含钨的质量分数在90%-95%时,其使用寿命最佳,当含钨量低于此值时,则钨合金的红硬性、耐磨性还不理想;当含钨量高于此值后,则合金的韧性降低,脆性提高 ,易产生龟裂现象,均降低砧块的使用寿命。因此,在电热镦粗中使用钨合金砧块可减少工人劳动强度,提高产品合格率,降低有关电能消耗,具有良好的经济效益。
高比重合金供应商:中钨在线科技有限公司 | 产品详情: http://www.tungsten-alloy.com |
电话:0592-5129696 传真:5129797 | 电子邮件:sales@chinatungsten.com |
钨钼文库:http://i.chinatungsten.com | 钨钼图片: http://image.chinatungsten.com |
钨新闻3G版:http://3g.chinatungsten.com | 钼业新闻: http://news.molybdenum.com.cn |


大型集装箱检查系统
- 詳細
- カテゴリ: 钨业知识
- 2017年5月12日(金曜)18:02に公開
- 参照数: 1964
集装货物/车辆检查系统是海关港口急需的检测设备之一。目前国内外港口对集装货物的检查主要采用开箱检查或辐射成像的方法。开箱拆货检查时间长、日检量低、检查成本高。对辐射成像而言,国内外现在已经研制出用加速器或钴-60做辐射源的大型集装货物/车辆检查系统。
进出口货物品种日益丰富,形成了钢材、煤炭、废纸、纸浆、木材、石材等特色货种的转运中心,对放射性检测的要求越来越高。使用钴-6做辐射源大型集装箱检查系统属于大型放射性检测系统,近年来在我国较大的港口码头开始普及。这种仪器由大容量塑料闪烁体和信号探测分析系统组成,该系统对过往的集装箱、大型车辆、行李物品等进行放射性物质实时监测,实现对异常的放射性同位素夹带实时联动预警的功能,基于特征谱分布动态扫描和甄别的人工核素识别技术,能够有效地降低系统的识报率和漏报率,由于其探测器面积大,不间断扫描时检测,极大地提高了检验检疫和通关速度。
由于钴-60是人造放射性同位素,是β衰变核素,会发射β-和γ射线,有极强的放射性。因此,在大型集装箱检查系统中同时大量运用了鎢合金屏蔽件来屏蔽辐射源对人体造成的伤害。防辐射能力和屏蔽材料密度有关,密度越大屏蔽性能越好。鎢合金材料具有高的密度和原子序数,作为理想的防辐射材料具有很多优势,吸收射线能力强、比重大、强度高、具有良好的可焊性和加工性、无毒環保,综合的优异性能使得鎢合金成為大型集裝箱檢測設備射線防護障蔽的最佳选择。
高比重合金供应商:中钨在线科技有限公司 | 产品详情: http://www.tungsten-alloy.com |
电话:0592-5129696 传真:5129797 | 电子邮件:sales@chinatungsten.com |
钨钼文库:http://i.chinatungsten.com | 钨钼图片: http://image.chinatungsten.com |
钨新闻3G版:http://3g.chinatungsten.com | 钼业新闻: http://news.molybdenum.com.cn |


钨合金多叶光栅叶片
- 詳細
- カテゴリ: 钨业知识
- 2017年5月12日(金曜)17:58に公開
- 参照数: 1858
多叶光栅系统主要用于放射医疗中控制X射线的方向和辐照范围,作用是替代手工制作的不规则铅挡块,在治疗过程中,由计算机控制多叶光栅系统各个叶片的运动,形成临床所需的不规则形状射野进行照射。多叶光栅系统由120个钨合金光栅叶片组成,其中叶片的制造材料采用钨合金材料,这比用铅做的挡板叶片产生的危害要小得多。
多叶光栅系统广泛运用在放射医疗技术中,主要基于钨合金对放射性物质的屏蔽效应。钨合金是一种高致密金属材料,研究证实高密度金属材料可对放射性物质产生屏蔽效应。由于金属钨对放射线有较强的防护性,所以目前多叶光栅叶片的材料多数都是由金属钨制成。整个多页光栅包括两组叶片,两组叶片相向排列安装于支架上,叶片可以在支架上移动,移动的方向与射线束轴线方向垂直,每个叶片都由步进电机独立驱动;由于在叶片之间为减少运动时的相互摩擦而留有适当的间隙,为减少放射线通过此间隙的泄露,还在两组叶片的下面各安装一个可移动的挡板,通过挡板的适当移动来遮挡泄露的放射线。为了防止相对应的两片钨叶在闭合实时发生碰撞,闭合的两片钨叶之间也留有微小的间隙,同样为了降低在此间隙泄露的放射线,也可以在与两组钨叶相垂直的方向再安排一族防漏挡板。
由于钨合金材料具有对各种射线的屏蔽本领高的优点,非常适合于对多叶光栅系统这一类空间分辨率要求高的场合,钨合金材料有着很高的密度减小了射线屏蔽件的尺寸,却不影响射线屏蔽效果,同时还具有无害环保的特性,在放射医疗技术中广泛运用。
高比重合金供应商:中钨在线科技有限公司 | 产品详情: http://www.tungsten-alloy.com |
电话:0592-5129696 传真:5129797 | 电子邮件:sales@chinatungsten.com |
钨钼文库:http://i.chinatungsten.com | 钨钼图片: http://image.chinatungsten.com |
钨新闻3G版:http://3g.chinatungsten.com | 钼业新闻: http://news.molybdenum.com.cn |


注射成型硬质合金粘结剂类型
- 詳細
- カテゴリ: 钨业知识
- 2017年5月12日(金曜)16:46に公開
- 参照数: 1836
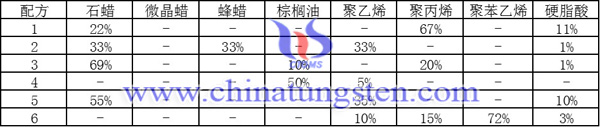
硬质合金供应商:中钨在线科技有限公司 | 产品详情: http://www.tungsten-carbide.com.cn |
电话:0592-5129696 传真:5129797 | 电子邮件:sales@chinatungsten.com |
钨钼文库:http://i.chinatungsten.com | 钨钼图片: http://image.chinatungsten.com |
钨新闻3G版:http://3g.chinatungsten.com | 钼业新闻: http://news.molybdenum.com.cn |


硬质合金注射成形制品原料控制
- 詳細
- カテゴリ: 钨业知识
- 2017年5月12日(金曜)16:43に公開
- 参照数: 1932
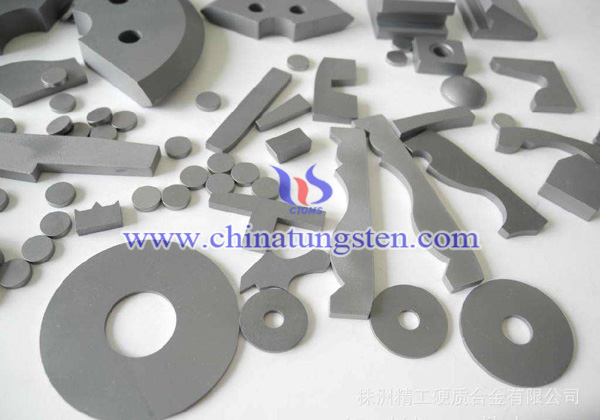
硬质合金供应商:中钨在线科技有限公司 | 产品详情: http://www.tungsten-carbide.com.cn |
电话:0592-5129696 传真:5129797 | 电子邮件:sales@chinatungsten.com |
钨钼文库:http://i.chinatungsten.com | 钨钼图片: http://image.chinatungsten.com |
钨新闻3G版:http://3g.chinatungsten.com | 钼业新闻: http://news.molybdenum.com.cn |


硬质合金催化脱脂炉
- 詳細
- カテゴリ: 钨业知识
- 2017年5月12日(金曜)16:41に公開
- 参照数: 1763
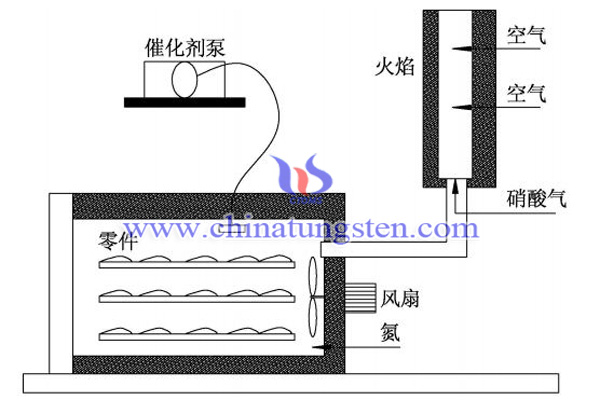
硬质合金供应商:中钨在线科技有限公司 | 产品详情: http://www.tungsten-carbide.com.cn |
电话:0592-5129696 传真:5129797 | 电子邮件:sales@chinatungsten.com |
钨钼文库:http://i.chinatungsten.com | 钨钼图片: http://image.chinatungsten.com |
钨新闻3G版:http://3g.chinatungsten.com | 钼业新闻: http://news.molybdenum.com.cn |


催化脱脂率影响因素
- 詳細
- カテゴリ: 钨业知识
- 2017年5月12日(金曜)16:38に公開
- 参照数: 2261
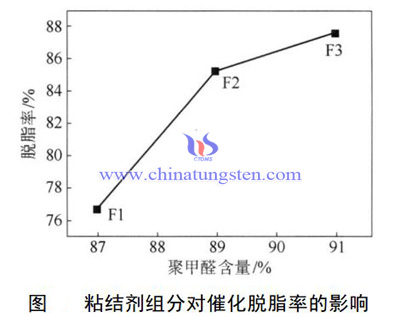
硬质合金供应商:中钨在线科技有限公司 | 产品详情: http://www.tungsten-carbide.com.cn |
电话:0592-5129696 传真:5129797 | 电子邮件:sales@chinatungsten.com |
钨钼文库:http://i.chinatungsten.com | 钨钼图片: http://image.chinatungsten.com |
钨新闻3G版:http://3g.chinatungsten.com | 钼业新闻: http://news.molybdenum.com.cn |

