废三氧化钨板式脱硝催化剂湿法回收金属氧化物
- 详细资料
- 分类:钨业知识
- 发布于 2016年5月18日 星期三 16:49
- 作者:chunyan
- 点击数:989
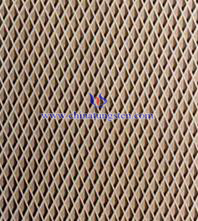
氧化钨供应商:中钨在线科技有限公司 | 产品详情: http://www.tungsten-oxide.com |
电话:0592-5129696 传真:5129797 | 电子邮件:sales@chinatungsten.com |
钨钼文库:http://i.chinatungsten.com | 钨钼图片: http://image.chinatungsten.com |
钨新闻3G版:http://3g.chinatungsten.com | 钼业新闻: http://news.molybdenum.com.cn |


硬质合金球粒尺寸精度的控制
- 详细资料
- 分类:钨业知识
- 发布于 2016年5月18日 星期三 16:23
- 作者:xiaobin
- 点击数:822
硬质合金球粒又被称为硬质合金球珠或钨钢滚珠,一般以YQ表示。其以高硬度难熔金属的碳化物(WC,TiC)微米级粉末为主要成分,以Co、Ni等为粘结剂,在真空炉或还原炉中烧结而成的粉末冶金产品。硬质合金球粒是硬质合金球种类中的一种,其体积相对较小(一般直径在φ0.3-φ1之间),多用于传动、笔用球珠等方面。除此之外,硬质合金球还有许多种类与用途,如毛坯球、精磨球、冲孔球、轴承滚珠、阀球、无磁球、蒙乃尔球、通孔球、计量球、刮色球等等。常见的硬质合金球粒的牌号也有许多,YG6、YG6x、YG8、YG13、YG20、YN6、YN9、YG12、YT5、YT15,因其具有极高的硬度、优良的耐磨耐蚀性、抗弯强度高等优点,其几乎可以完全取代同类钢球产品。
随着相关技术的飞速发展,对硬质合金球粒的组分、使用性能以及尺寸精度等也提出了更高的要求。通常情况下,硬质合金球粒是采用喷焊、乙炔焊或热注入等方式将其作为金属材料表面的耐磨层,以提高材料的耐磨耐蚀性能。这也就要求硬质合金球粒的圆度高、致密好,才能有效提高焊附过程中的流动性,使其均匀分散。但是由于不同金属材料表面要求不同,相应的硬质合金球粒的粒度组成和尺寸分布也不尽相同,这就给尺寸精度的控制带来一定的困难。从工艺上看,硬质合金球粒需经过制粒、振动过筛、干燥、等静压压制成型等工序。其与其他硬质合金产品不同,是不经过模具压制成型的,其是通过擦筛过程利用粒子自重在转动的制粒机上粘附粉末而不断滚动并长大成型的,最后再经等静压制成型,使其具有一定的密度和强度。然而在等静压前,各个硬质合金球粒的密度是相对不均匀的,这就使得经过等静压和烧结工序后,球粒的尺寸大小偏差较大、收缩系数也大不一致。
硬质合金球粒的尺寸控制与球粒自身密度有着直接的影响,半成品球粒滚动长大速度与球粒密度呈递减关系。在长大速度过快时,相应的球粒制品致密度下降,通过金相观察可以发现等静压制压力能够有效降低硬质合金球粒内部的孔隙度,但是密度虽然得到了提高,尺寸却变小了,经烧结收缩后尺寸进一步减小,出现超负公差的废品。通过金相观察可以发现等静压制压力能够有效降低硬质合金球粒内部的孔隙度。以YQ3硬质合金球粒为例,将YQ3混合料按每千克加入汽油橡胶溶液80-90ml与混合料在混合容器中进行均匀渗胶,渗胶后倒入不锈钢盘中放入干燥柜中进行干燥,将蒸汽压力和时间控制在一定的适宜范围内。将渗胶擦筛后的粒子料倒入制粒机中滚动一定时间后,再将渗胶过筛的粉磨料加入制粒机中粘附在粒子表面使其不断滚动长大,按尺寸要求仔细观察确认球粒致密度、形状与尺寸,直至球粒表面发光为止。经多次实验比较,半成品球粒尺寸上下公差限控制为以平均收缩系数与成品尺寸下限的乘积加上成品尺寸公差背书值来确定球粒制品尺寸的下限;以平均收缩系数与成品尺寸上限乘积值的结果确定半成品尺寸的上限。此外,关于硬质合金球粒HV的检测方法是取大于100颗硬质合金球粒以树脂镶块,金相制样,取五颗完整无缺陷的硬质合金球粒测其HV并计算平均值;对硬质合金球粒缺陷率的检测方法也是取100颗硬质合金球粒以树脂镶块,金相制样,100倍检测计算。
硬质合金供应商:中钨在线科技有限公司 | 产品详情: http://www.tungsten-carbide.com.cn |
电话:0592-5129696 传真:5129797 | 电子邮件:sales@chinatungsten.com |
钨钼文库:http://i.chinatungsten.com | 钨钼图片: http://image.chinatungsten.com |
钨新闻3G版:http://3g.chinatungsten.com | 钼业新闻: http://news.molybdenum.com.cn |


碳硫分析仪与钨粒的检定标准——检定条件,检定方法,鉴定结果处理和检定周期
- 详细资料
- 分类:钨业知识
- 发布于 2016年5月18日 星期三 10:27
- 作者:xuejiao
- 点击数:828
碳硫分析仪与钨粒的检定标准除了对技术的要求,还包括检定条件,检定方法,鉴定结果处理和检定周期。碳的相对标准偏差要低于1.0%,硫要低于4.0%,分析的时间要少于一分钟,称量的稳定性小于0.002克。检定的条件要求环境要达到标准。检测所处的环境温度要控制在15℃到30℃之间,相对湿度需小于80%,如果是针对含量为0.0010%~0.0100%的碳硫的测定,其相对湿度要低于60%。供电的电源为(220±4.4) V,(50±1) Hz,并且检测周围要保证没有强烈的振动,没有强电,磁场的妨碍,没有腐蚀性气体的存在。
检定需要的主要的设备与材料要根据国家标准进行测定。采用国家计量行政部门批准的钢铁成份分析国家一级、二级标准物质,对碳硫标准物质的测定的不确定度需要小于示值误差的三分之一。用三级1g标准砝码称量。检定外观是要根据目视和手感,按照外观标准检定。检定前需要根据说明书进行仪器的预热。选含碳量在(0.100%~1.000%)范围,含硫量在(0.010%~0.100%)范围内的一种钢铁标准物质,每次称取样品0.5 g,重复测定7次,按式标准计算方法计算标准偏差及相对标准偏差。用1 g 标准砝码,连续称重6次,其最大值与最小值之差即为称量稳定性。检定完毕后,发给合格检定证书,不合格则指出不合格的项目。检定周期通常为2年1次。在搬动,修理或者对测量结果有疑义的都可进行检定。
纯钨产品供应商:中钨在线科技有限公司 | 产品详情: http://www.tungsten.com.cn |
电话:0592-5129696 传真:5129797 | 电子邮件:sales@chinatungsten.com |
钨钼文库:http://i.chinatungsten.com | 钨钼图片: http://image.chinatungsten.com |
钨新闻3G版:http://3g.chinatungsten.com | 钼业新闻: http://news.molybdenum.com.cn |


钍钨电极加工变形组织研究
- 详细资料
- 分类:钨业知识
- 发布于 2016年5月18日 星期三 16:10
- 作者:yiping
- 点击数:716
通过粉末冶金法制得钨坯条后,钍钨电极要经过一系列的变形加工才能得到成品。钍钨电极的加工变形主要经历旋锻开坯、再结晶退火、203旋锻、202旋锻、201旋锻、拉丝、矫直、抛光,最后得到成品。在整个加工过程中选取三个典型阶段分析钍钨电极组织的变化,这三个阶段的取样分别在再结晶退火阶段、202旋锻阶段和成品。
再结晶退火的钍钨电极,钨基体的晶界非常明显,沿开坯轴方向的晶界比较平整。其中钨基体的晶粒比较粗大,有一定的延长性,其内部弥散分布着许多黑色细小的球状颗粒,这些颗粒是电极的第二相。
电极经过202旋锻后,钨基体的晶粒变得比较细长,晶界更为清晰。与再结晶阶段不同的是,其组织出现了一定的纤维化,钨基体的晶粒沿旋转轴的轴向方向延长,粗大的晶粒逐渐向细长的晶粒转变。而第二相黑色粒子分布得更加均匀,但仍保持着球状或近似球状的形状。
随着变形量的加大,成品钍钨电极钨基体的晶界逐渐变得模糊,晶粒完全由纤维组织所取代,其中纤维组织沿着电极的轴向方向伸长。第二相粒子分布得更加均匀。
由以上分析可知,钍钨电极在加工过程中钨基体随着变形量的增加,逐渐向纤维化转变。其第二相粒子的分布随着加工量的增加变得更加均匀,第二相主要是由Th、O和W三种元素组成的。
纯钨产品供应商:中钨在线科技有限公司 | 产品详情: http://www.tungsten.com.cn |
电话:0592-5129696 传真:5129797 | 电子邮件:sales@chinatungsten.com |
钨钼文库:http://i.chinatungsten.com | 钨钼图片: http://image.chinatungsten.com |
钨新闻3G版:http://3g.chinatungsten.com | 钼业新闻: http://news.molybdenum.com.cn |


钨合金屏蔽件的优势
- 详细资料
- 分类:钨业知识
- 发布于 2016年5月18日 星期三 09:54
- 作者:minghui
- 点击数:763
随着科技的高速发展和辐射技术的广泛应用,辐射的危害逐渐引起人们的关注。辐射指的是场源放出的电磁能量中一部分脱离场源以电磁波或粒子(如阿尔法粒子、贝塔粒子等)的形式向远处传播,之后再返回场源的现象。辐射可分为电离辐射和非电离辐射,且能够对人体产生危害。长期受到辐射照射,会使人体感到不适,严重则可损伤人体系统和器官,导致白血病、肿瘤、再生障碍性贫血、眼底病变、生殖系统疾病、早衰等各种疾病。而辐射防护的主要方法包括时间防护、距离防护和屏蔽防护。其中屏蔽防护指的是在射线源与人体之间放置一种能有效吸收射线的屏蔽材料。常用的屏蔽材料有铅、钨合金以及碳化硼。
碳化硼别名黑钻石,分子式为B4C。由于其可以吸收大量中子而不会形成任何放射性同位素,因此其在核能发电场里是一种很理想的中子吸收剂,主要作用是对核分裂的速率进行控制。铅是有毒的弱金属,也是重金属,具有柔软和延展性强等特点,可用作耐硫酸腐蚀材料以及防电离辐射屏蔽件、蓄电池等的材料,其用于制造防护设备时主要是针对放射性辐射、X射线的防护。然而,由于铅在环境中的长期持久性,又对许多生命组织具有较强的潜在毒性,所以其一直被列入强污染物范围。铅及其化合物对人体有较大毒性,并可在人体内积累。
与碳化硼和铅相比,相同重量的屏蔽件,体积更小的钨合金屏蔽件,密度却更高,射线吸收能力更好。和同等重量的铅屏蔽件相比,钨合金屏蔽件的体积只有铅的1/3,但高密度性使其拥有和铅相当的射线吸收能力。重量确定下来之后,密度更高,钨合金屏蔽件的厚度却更薄。由于钨合金的高密度,使得钨合金屏蔽件的厚度更薄,但射线吸收能力更高。这就是钨合金成为辐射屏蔽件的最佳原材料的原因。
高比重合金供应商:中钨在线科技有限公司 | 产品详情: http://www.tungsten-alloy.com |
电话:0592-5129696 传真:5129797 | 电子邮件:sales@chinatungsten.com |
钨钼文库:http://i.chinatungsten.com | 钨钼图片: http://image.chinatungsten.com |
钨新闻3G版:http://3g.chinatungsten.com | 钼业新闻: http://news.molybdenum.com.cn |

