钨合金核辐射屏蔽件
- 详细资料
- 分类:钨业知识
- 发布于 2016年5月25日 星期三 18:05
- 作者:minghui
- 点击数:650
核辐射又称为电离辐射,是原子核在状态转变过程中(从一种结构或一种能量状态转变为另一种结构或另一种能量状态)所释放出来的微观粒子流。其可以引起物质的电离或激发。核辐射主要由核反应产生,或从裂变产物中释放。核爆炸和核事故都会产生核辐射,主要包括α、β、γ三种射线。核辐射对人体具有危害,但人体的躯体和生殖细胞对核辐射的敏感性以及受损后效应不同。当躯体细胞受损时,会导致人体器官组织发生疾病,最终使得人体死亡,躯体细胞死亡后,损伤细胞不会转移到下一代;而当生殖细胞受损时,下一代将继承母体改变了的基因,从而导致后代出现缺陷。
核辐射的放射性物质包括碘131和铯137,这些放射性物质可通过呼吸吸入、皮肤伤口及消化道吸收进入体内,从而引起内辐射。其中,碘131一旦进入人体,可能会引起甲状腺疾病;而铯137一旦进入人体,则会损伤人体的造血系统和神经系统,因此必须避免人体受到核辐射的照射。γ辐射还可穿透一定距离被人体吸收,造成外辐射损伤。内外辐射所引发的放射病症状包括脱发、白血病、出血、呕吐、疲劳、皮肤发红、头昏、失眠、溃疡、腹泻等。有时还会增加畸变、癌症、遗传性病变的发生率,对下一代的健康造成影响。一般来说,人体接受的核辐射能量越多,其放射病症状越严重,致癌、致畸的风险越大。
钨合金核辐射屏蔽件具有很好的核辐射屏蔽性能,是一种耐高温、适用性很强的钨合金屏蔽件。铅长期作为屏蔽件的原材料,但其屏蔽效果依然不如钨合金屏蔽件。钨合金屏蔽件是辐射屏蔽的首选材料。由于钨合金屏蔽件的密度很高,其屏蔽效果是铅的两倍,且重量只有铅的25%到50%。此外,铅及其化合物具有毒性,会危害人体健康,而钨合金屏蔽件无毒无害,是极其环保友好的屏蔽件材料。
高比重合金供应商:中钨在线科技有限公司 | 产品详情: http://www.tungsten-alloy.com |
电话:0592-5129696 传真:5129797 | 电子邮件:sales@chinatungsten.com |
钨钼文库:http://i.chinatungsten.com | 钨钼图片: http://image.chinatungsten.com |
钨新闻3G版:http://3g.chinatungsten.com | 钼业新闻: http://news.molybdenum.com.cn |


纳米贵金属改性的三氧化钨光触媒涂料
- 详细资料
- 分类:钨业知识
- 发布于 2016年5月25日 星期三 18:01
- 作者:chunyan
- 点击数:869
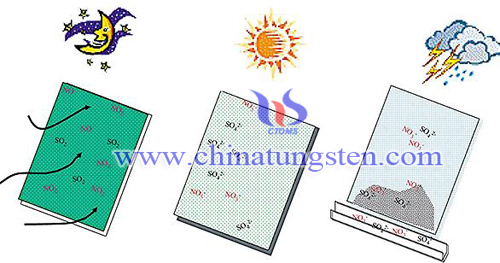
氧化钨供应商:中钨在线科技有限公司 | 产品详情: http://www.tungsten-oxide.com |
电话:0592-5129696 传真:5129797 | 电子邮件:sales@chinatungsten.com |
钨钼文库:http://i.chinatungsten.com | 钨钼图片: http://image.chinatungsten.com |
钨新闻3G版:http://3g.chinatungsten.com | 钼业新闻: http://news.molybdenum.com.cn |


纳米硬质合金的发展
- 详细资料
- 分类:钨业知识
- 发布于 2016年5月25日 星期三 16:59
- 作者:xiaobin
- 点击数:777
通常所使用的硬质合金主要是由难熔金属碳化物(如WC、TiC等)与过渡族金属或合金所组成的粘结相(如Fe、Co、Ni等)形成的超硬复合材料。其具有高硬度、高强度、高熔点、良好的热硬性以及优良的耐磨耐蚀性等优点。早在20世纪20年代德国人就首先采用了粉末冶金的方法(Powder Metallurgy,简称PM)制备了WC硬质合金,从此推动了硬质合金在航天航空、机械加工、冶金、石油钻井、矿山工具、电子通讯、建筑、军工等领域的广泛运用。一开始硬质合金主要运用于拉丝模和一些耐磨零部件的制造,后来由于技术工艺的不断改进,性能不断得到提高,在金属切削领域也逐渐演变为不可或缺的角色。随着研究的不断深入,研究人员发现硬质合金中WC晶粒的尺寸越小,其粘结相Co的平均自由程越短,会使得合金的硬度和强度有一个较大的提升,尤其是当WC晶粒尺寸降低至100nm左右时,其力学性能有着一个较为明显的突破。
现如今在一些新兴的工业领域以及一些难加工的金属材料领域,如航空材料中的高温合金加工、电子工业中使用广泛的印刷电路板(PCB)钻孔、复合板材加工、玻璃纤维增强结构的热塑材料、点阵打印机针头、玻璃的精密切割等,都需要硬度更高、强度更好的超细晶粒或纳米晶粒硬质合金刀具来完成。然而在硬质合金的致密化过程中不可避免地会存在晶粒长大的现象,因而要获得纳米级的硬质合金,首先必须合成晶粒更为细小的纳米粉末。以下实际中较为常见的制备纳米级硬质合金粉末的工艺方法:
1.机械合金化法(Mechanical Alloying,简称MA):其是一个通过高能球磨使粉末经受反复的变形、冷焊、破碎,从而达到元素间原子水平合金化的复杂物理化学过程。该工艺操作简单方便、制备效率高、制作的粉末晶粒尺寸也能达到要求,但是往往会因为与罐体、球体摩擦造成粉末的污染;
2.喷射转换法:喷射转换法又称喷雾转化法(SCP),是美国学者研制出的一种新型工艺方法。其利用偏钨酸铵(CH4)6(H2W12O40)和氯化钴水溶液CoCl2·nH2O 或Co(en)3WO4和钨酸H2WO4水溶液经喷雾干燥以及流化床还原以及碳化反应生成组织均匀的晶粒粉末(20-50nm之间);
3.原位渗碳法(in-situ carburization):其结合了原位合成和渗碳的工艺,原位合成是利用不同元素或化合物间在一定条件下发生化学反应,而在金属基体内生成一种或几种陶瓷相颗粒,已达到改善单一金属合金性能的目的。美国学者所采用的是将聚丙烯腈作为原位碳源,不需要气相碳化,将钨酸和钴盐溶解在聚丙烯腈溶液中,经低温干燥后移至90%氩气Ar-10%氢气H2的还原炉中直接还原呈硬质合金粉末,其晶粒度约为50-80nm;
4.共沉淀法:通常是在溶液状态下将不同化学成分的物质混合,在混合液中加入适当的沉淀剂制备前驱体沉淀物,再将沉淀物进行干燥或锻烧,从而制得相应的粉体颗粒,是制备含两种或两种以上金属元素的复合氧化物超细粉体的重要方法。有研究人员采用由钨酸钠或钨酸铵和醋酸钴共沉淀形成WC-Co前驱体粉末,再通过氢气还原反应和碳化反应制成硬质合金粉末(约50nm)。但是该方法只适用于W/Co原子比接近于5.5的粉末,而采用钨酸铵和钴的氢氧化物共沉淀就能高边W/Co的原子比,获得范围更广的复合粉末。
此外,还有一些其他的合成方法,如气相蒸发法、高频等离子体合成法、高频感应加热合成法、离子电弧法等,这些方法都尚在研究阶段,并未投入实际的生产当中。纳米硬质合金显微组织的细小且均匀,其力学性能也得到了显著提高。钴粘结相的平均自由程缩短,裂纹扩展阻力随之提高,硬质合金的韧性也越好。在现如今使用越来越多的微钻领域,纳米晶粒硬质合金钻头钻孔效率更高,磨损量越小,使用寿命也越长,是普通硬质合金钻头的十几倍。
硬质合金供应商:中钨在线科技有限公司 | 产品详情: http://www.tungsten-carbide.com.cn |
电话:0592-5129696 传真:5129797 | 电子邮件:sales@chinatungsten.com |
钨钼文库:http://i.chinatungsten.com | 钨钼图片: http://image.chinatungsten.com |
钨新闻3G版:http://3g.chinatungsten.com | 钼业新闻: http://news.molybdenum.com.cn |


纳米三氧化钨光触媒纸基竹帘
- 详细资料
- 分类:钨业知识
- 发布于 2016年5月25日 星期三 17:58
- 作者:chunyan
- 点击数:789
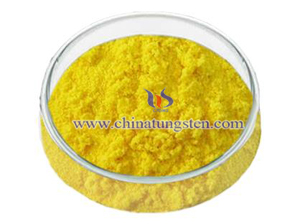
氧化钨供应商:中钨在线科技有限公司 | 产品详情: http://www.tungsten-oxide.com |
电话:0592-5129696 传真:5129797 | 电子邮件:sales@chinatungsten.com |
钨钼文库:http://i.chinatungsten.com | 钨钼图片: http://image.chinatungsten.com |
钨新闻3G版:http://3g.chinatungsten.com | 钼业新闻: http://news.molybdenum.com.cn |


废钨条与钨粉
- 详细资料
- 分类:钨业知识
- 发布于 2016年5月25日 星期三 11:22
- 作者:xuejiao
- 点击数:852
钨粉是呈粉末状的金属钨,是制备钨加工材、钨合金和钨制品的原料。纯钨粉可制成丝、棒、管、板等加工材和一定形状制品。钨细粉与其他金属粉末混合,可以制成各种钨合金,如钨钼合金、钨铼合金、钨铜合金和高密度钨合金等。钨粉的另一个重要应用是制成碳化钨粉,进而制备硬质合金工具,如车刀、铣刀、钻头和模具等。
比起从矿石中提炼金属,回收再生产废弃金属不仅可以节约能源,降低成本,还有助于改善生态环境。所以,得到国际的广泛关注。特别是日本,他们国家把这项工程认为是“第二矿业”的开发。其中包含钨钢废料,金属钨及其合金废料,硬质合金废料,研磨硬质合金工具的磨屑,粉尘等二次原材料。许多国家已经开始设立专门的部门负责废钨条的回收利用。其中苏联设有研究所专门负责有色金属废料的回收再生利用。该研究所研制出的处理含钨废料流程,在通过一系列的工业试验后,被认为是最具发展前景的工序。最近几年,许多国家都在研制如何处理钨废条的方法,其中废料再生产钨的方法主要有电解法,锌熔法,高温氧化法,化学溶解法和氯化法。
钨条的废端块经过试验证明可以代替工业钨细粉作为原料,并且可以制取同样质量的超级细微颗粒的钨细粉。这样不仅大幅度的降低工业成本,最重要的是资源的合理再利用,可以改善现在工业迅速发展所带来的弊端。
纯钨产品供应商:中钨在线科技有限公司 | 产品详情: http://www.tungsten.com.cn |
电话:0592-5129696 传真:5129797 | 电子邮件:sales@chinatungsten.com |
钨钼文库:http://i.chinatungsten.com | 钨钼图片: http://image.chinatungsten.com |
钨新闻3G版:http://3g.chinatungsten.com | 钼业新闻: http://news.molybdenum.com.cn |

