稀土对钨电极焊接性能的影响
- 详细资料
- 分类:钨业知识
- 发布于 2016年6月28日 星期二 17:41
- 作者:yiping
- 点击数:788
了解稀土含量对钨电极焊接性能的影响,对于提高钨电极焊接性能具有重要的意义。在相同制备工艺下将不同含量的稀土含量的稀土钨电极的焊接性能进行比较,从而了解稀土含量对焊接性能的影响。众所周知,钍钨电极具有优良的焊接性能,因此稀土钨电极也要和钍钨电极进行比较。
引弧性能
在实验中阴极为水冷黄铜。从30V电压下开始进行引弧实验,每次按1V电压间隔升高空载电压,每个电压下进行引弧实验30次,每次打高频1秒内起弧为引弧成功,1~10内起弧为引弧滞后,超过10秒则为引弧失败。从实验数据可知,稀土钨电极的引弧性能优于钍钨电极。因为稀土钨电极具有较低的逸出功,因此引弧性能较好。添加多种稀土制得的复合稀土钨电极的引弧性能优于单元稀土钨电极,其中含有高氧化钇的钨钇电极的引弧性能较好。
抗烧损性能
在实验中将钨电极接在负极,在250A焊接电流下燃弧30分钟。然后用DP-100光学分析天平测量实验前后电极质量的变化。从实验数据可知,稀土钨电极的质量高于钍钨电极,即稀土钨电极的烧损率优于钍钨电极,其中钇钨电极表现出较为优异的抗烧损性能。在其他条件都相同的情况下,电极表面的逸出功越低,其工作温度也就越低,烧损量也就越少。添加稀土的钨电极,其表面形成了较低逸出功的活性层,因此稀土钨电极的抗烧损性能较为良好。
纯钨产品供应商:中钨在线科技有限公司 | 产品详情: http://www.tungsten.com.cn |
电话:0592-5129696 传真:5129797 | 电子邮件:sales@chinatungsten.com |
钨钼文库:http://i.chinatungsten.com | 钨钼图片: http://image.chinatungsten.com |
钨新闻3G版:http://3g.chinatungsten.com | 钼业新闻: http://news.molybdenum.com.cn |


微波在钨粉生产中的应用
- 详细资料
- 分类:钨业知识
- 发布于 2016年6月28日 星期二 17:34
- 作者:xinyi
- 点击数:688
钨粉供应商:中钨在线科技有限公司 | 产品详情: http://www.tungsten-powder.com |
电话:0592-5129696 传真:5129797 | 电子邮件:sales@chinatungsten.com |
钨钼文库:http://i.chinatungsten.com | 钨钼图片: http://image.chinatungsten.com |
钨新闻3G版:http://3g.chinatungsten.com | 钼业新闻: http://news.molybdenum.com.cn |


钨粉用于碳化钨粉合成
- 详细资料
- 分类:钨业知识
- 发布于 2016年6月28日 星期二 17:08
- 作者:xinyi
- 点击数:867
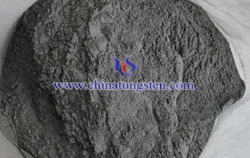
钨粉供应商:中钨在线科技有限公司 | 产品详情: http://www.tungsten-powder.com |
电话:0592-5129696 传真:5129797 | 电子邮件:sales@chinatungsten.com |
钨钼文库:http://i.chinatungsten.com | 钨钼图片: http://image.chinatungsten.com |
钨新闻3G版:http://3g.chinatungsten.com | 钼业新闻: http://news.molybdenum.com.cn |


钨粉用于碳化钨粉合成的影响因素
- 详细资料
- 分类:钨业知识
- 发布于 2016年6月28日 星期二 17:14
- 作者:xinyi
- 点击数:820
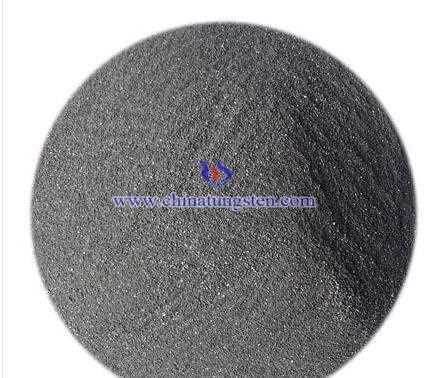
钨粉供应商:中钨在线科技有限公司 | 产品详情: http://www.tungsten-powder.com |
电话:0592-5129696 传真:5129797 | 电子邮件:sales@chinatungsten.com |
钨钼文库:http://i.chinatungsten.com | 钨钼图片: http://image.chinatungsten.com |
钨新闻3G版:http://3g.chinatungsten.com | 钼业新闻: http://news.molybdenum.com.cn |


梯度结构涂层硬质合金刀片
- 详细资料
- 分类:钨业知识
- 发布于 2016年6月28日 星期二 15:18
- 作者:xiaobin
- 点击数:709
传统硬质合金虽然组织成分均匀一致,且各项综合性能相比于其他材料都具有一定的优势,但是其存在一个不可避免的矛盾,即硬度与韧性之间的平衡问题。这也是一直限制传统硬质合金材料应用的一个重要因素。而采用新型的制备技术,使传统硬质合金材料在结构上呈现梯度变化,可以有效调和这一组内部矛盾。梯度结构硬质合金通过组织成分呈梯度分布而实现良好的性能,尤其是在高性能硬质合金切削工具方面具有极大的优势。经梯度处理后,合金在表面区域形成缺立方相氮化物和碳氮化物的韧性区域,相应的粘结剂含量高于基体名义粘结剂的含量。在此基础上,采用CVD或PVD的方法在硬质合金基体上沉积涂层,得到涂层梯度硬质合金。当涂层中形成的裂纹扩展到梯度韧性区域时,由于其良好的塑性和韧性,可以有效吸收裂纹扩展时的能量,从而有效地阻止裂纹向合金内部扩展并提高硬质合金切削工具的使用性能。
通过实验发现,随着合金中Co含量的增多,梯度结构合金强度与磁饱和度得到提高,硬度、磁力、密度减小,合金成分梯度结构愈明显,梯度层也越厚;而随着合金中的Ti(CN)含量的增多,梯度结构合金硬度提高,磁力增大,强度和密度发生减小,合金梯度层厚度变薄;在基体和涂层成分相同的情况下,有梯度结构的涂层硬质合金刀片的切削性能与无梯度结构涂层硬质合金刀片的切削性能更为优良(在同一磨损高度的条件下,切削刀具的使用寿命提高了近一倍)。此外,Co含量较高的梯度涂层硬质合金刀片的切削性能普遍优于Co含量较低的梯度涂层刀片的切削性能。
硬质合金供应商:中钨在线科技有限公司 | 产品详情: http://www.tungsten-carbide.com.cn |
电话:0592-5129696 传真:5129797 | 电子邮件:sales@chinatungsten.com |
钨钼文库:http://i.chinatungsten.com | 钨钼图片: http://image.chinatungsten.com |
钨新闻3G版:http://3g.chinatungsten.com | 钼业新闻: http://news.molybdenum.com.cn |

