三氧化钨用于含分子筛的加氢脱硫催化剂
- 详细资料
- 分类:钨业知识
- 发布于 2016年4月28日 星期四 18:16
- 作者:chunyan
- 点击数:838
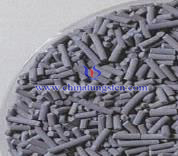
氧化钨供应商:中钨在线科技有限公司 | 产品详情: http://www.tungsten-oxide.com |
电话:0592-5129696 传真:5129797 | 电子邮件:sales@chinatungsten.com |
钨钼文库:http://i.chinatungsten.com | 钨钼图片: http://image.chinatungsten.com |
钨新闻3G版:http://3g.chinatungsten.com | 钼业新闻: http://news.molybdenum.com.cn |


石英连熔炉用钨坩埚
- 详细资料
- 分类:钨业知识
- 发布于 2016年4月28日 星期四 18:14
- 作者:xuejiao
- 点击数:870
石英玻璃是一种只含二氧化硅单一成份的特种玻璃,其微观结构是一种由二氧化硅四面结构体结构单元组成的单纯网络,具有紧密的结构,其中透明石英玻璃的光学性能非常优异,在紫外到红外辐射的连续波长范围都有优良的透射比。通过连熔炉制备的石英玻璃可广泛应用与半导体生产的各项工序中。
钨坩埚具有熔点高,沸点高,高温强度好的优良特性,因此广泛应用于石英玻璃连熔炉中。目前主要的工艺装备是将钼电极和64根钼棒装置在连熔炉内的加热装置,这些钼电极和钼棒均匀的散布在钨坩埚的周围。当电极导电加热时,作为导电发热体的64根钼棒会使钨坩埚不断升温。但是,该工艺设备有一个比较严重的缺陷。当这64根钼棒作为导电发热体时,钼棒之间存在的8-12mm的距离问题会造成钨坩埚的升温不均,从而延长了钨坩埚的升温时间,这样会大大降低连熔炉的生产效率。可以将连熔炉中的钨坩埚的顶部设置加料管和钨芯杆保护气的入口,在钨坩埚底部放置成型器料台,料台中间应该设有成型口,并且将加热装置放在钨坩埚的外部。用钼网代替钼棒均匀的覆盖钨坩埚的表面。钼网的均匀覆盖可以使钨坩埚受热均匀,以此有效解决成型石英管的气泡和气线内在的质量问题。
钨坩埚除了广泛应用于石英连熔炉,还对粉末冶金技术,电子喷涂,晶体生长具有重要作用。
纯钨产品供应商:中钨在线科技有限公司 | 产品详情: http://www.tungsten.com.cn |
电话:0592-5129696 传真:5129797 | 电子邮件:sales@chinatungsten.com |
钨钼文库:http://i.chinatungsten.com | 钨钼图片: http://image.chinatungsten.com |
钨新闻3G版:http://3g.chinatungsten.com | 钼业新闻: http://news.molybdenum.com.cn |


什么是钨合金铆钉顶棒?
- 详细资料
- 分类:钨业知识
- 发布于 2016年4月28日 星期四 17:38
- 作者:yaqing
- 点击数:835
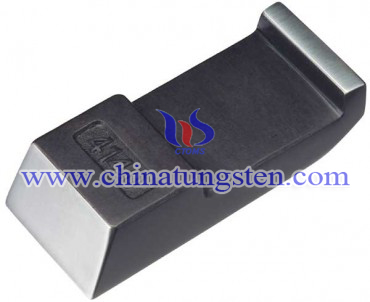
钨铆钉顶棒供应商:中钨在线科技有限公司 | 产品详情: http://www.buckingbar.com.cn |
电话:0592-5129696 传真:5129797 | 电子邮件:sales@chinatungsten.com |
钨钼文库:http://i.chinatungsten.com | 钨钼图片: http://image.chinatungsten.com |
钨新闻3G版:http://3g.chinatungsten.com | 钼业新闻: http://news.molybdenum.com.cn |


三氧化钨用于高氮劣质汽柴油加氢脱硫催化剂
- 详细资料
- 分类:钨业知识
- 发布于 2016年4月28日 星期四 18:12
- 作者:chunyan
- 点击数:751
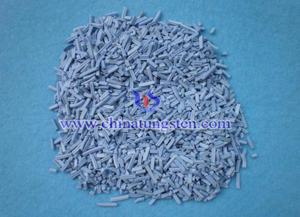
氧化钨供应商:中钨在线科技有限公司 | 产品详情: http://www.tungsten-oxide.com |
电话:0592-5129696 传真:5129797 | 电子邮件:sales@chinatungsten.com |
钨钼文库:http://i.chinatungsten.com | 钨钼图片: http://image.chinatungsten.com |
钨新闻3G版:http://3g.chinatungsten.com | 钼业新闻: http://news.molybdenum.com.cn |


硬质合金镀铜工艺
- 详细资料
- 分类:钨业知识
- 发布于 2016年4月28日 星期四 16:14
- 作者:xiaobin
- 点击数:790
从理论上说,在硬质合金刀具表面通过CVD和PVD的方法沉积一层金刚石薄膜,可以显著改善刀具的各项性能。而其中最常见的问题就是涂层与硬质合金基体间的结合能力以及热学性能的匹配。因此,研究人员发现在涂层薄膜与硬质合金基体间施加一层过渡层能够显著改善膜基性能。即在硬质合金刀具基体上电镀一层金属,这种将电沉积层作为过渡层的工艺是一种新的尝试,硬质合金镀铜工艺就是其中之一。铜对金刚石刀具具有良好的浸润性,在沉积CVD金刚石的过程中,镀铜层所受温度的影响相对较小,是一种较为理想的过渡层材料。
在硬质合金上电镀铜的基本流程是:工件制备→预处理→清洗→预镀→电镀→清洗。由于大部分的硬质合金产品是由WC、TiC等金属碳化物和粘结剂Co组成并采用粉末冶金的方法制备的,因此颗粒间存在一定的孔隙缺陷,而相应的预处理工艺对硬质合金的镀层就有着极为重要的影响。为了去除硬质合金表面的氧化层,通常会选择酸洗的方法,而这样一来就会使得表面少量的Co脱落,增加了表面的孔隙。而相应的失去Co粘结作用而外露的碳化物也就更容易脱落,从而使得镀层的结合性能显著降低。此外,在硬质合金内部通常会含有一定的油脂且不易清洗,在电沉积预处理和电沉积过程中容易渗入电镀液,从而造成镀层泛点,由内向外腐蚀,最终使得镀层脱落。相比于在其他材料上镀铜,硬质合金预处理工艺中对于除油的要求更高。常用的方法有电解除油、高温除油以及有机溶剂除油等,对于硬质合金来说通常采用高温除油的方法。除油后还需进行抛光处理,去除表面的氧化层再用离子水超声波清洗。
预镀时采用氰化镀铜,而电镀铜时通常采用硫酸盐作为电镀液,温度控制在20℃左右,空气搅拌,阳极为紫铜(纯铜),电镀时间约为5-10min。电镀后从外观、显微硬度、结合强度等几个方面对镀层的性能进行综合评定。从外观上镀铜层表面较为平整,呈紫红色,表面粗糙度小于0.3μm。对比未进行预处理和预处理中未进行高温除油的镀层,其镀层更为平滑、致密度更好且无起皮、开裂与脱落的现象。而硬质合金镀铜层的显微硬度可达到216-219HV。结合强度的测验方法可分为两种,其一是加热法,即将镀件置入加热炉加热至300℃,保温1h,迅速取出并放入室温下的水中,观察镀层是否有起皮与脱落的现象;其二为划线法,用刃口为呈30°的硬质合金划刀再度层上划一边长为1mm并深达基体的方格,观察镀层的起皮与脱落现象。
此外,在硬质合金上电镀铜的沉积过程是一种机械堆积过程,因为铜和硬质合金中的WC和Co间基本不存在互相渗透和溶解,是一种机械结合方式。镀层经过氢等离子处理后,Cu与硬质合金基体内的元素在结合面处相互溶解、扩散,从而形成界面扩散层。这一扩散层的存在会使得镀铜层与硬质合金基体的结合由机械结合向冶金结合转变,因而镀铜层和硬质合金基体的结合强度得到了显著的提升。
硬质合金供应商:中钨在线科技有限公司 | 产品详情: http://www.tungsten-carbide.com.cn |
电话:0592-5129696 传真:5129797 | 电子邮件:sales@chinatungsten.com |
钨钼文库:http://i.chinatungsten.com | 钨钼图片: http://image.chinatungsten.com |
钨新闻3G版:http://3g.chinatungsten.com | 钼业新闻: http://news.molybdenum.com.cn |

