钨青铜型结构铁电铌酸盐
- 详细资料
- 分类:钨业知识
- 发布于 2016年5月03日 星期二 18:14
- 作者:xinyi
- 点击数:2330
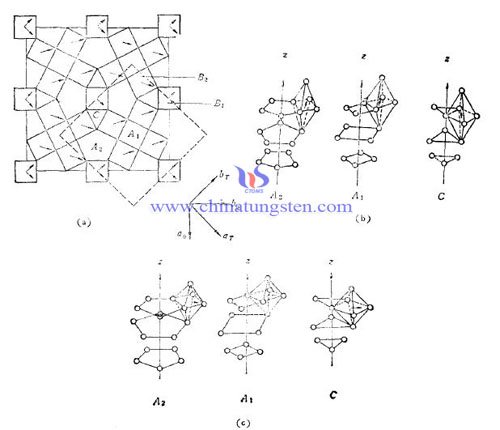
氧化钨供应商:中钨在线科技有限公司 | 产品详情: http://www.tungsten-oxide.com |
电话:0592-5129696 传真:5129797 | 电子邮件:sales@chinatungsten.com |
钨钼文库:http://i.chinatungsten.com | 钨钼图片: http://image.chinatungsten.com |
钨新闻3G版:http://3g.chinatungsten.com | 钼业新闻: http://news.molybdenum.com.cn |


WO3用于汽油选择性加氢脱硫催化剂
- 详细资料
- 分类:钨业知识
- 发布于 2016年5月03日 星期二 18:04
- 作者:chunyan
- 点击数:884
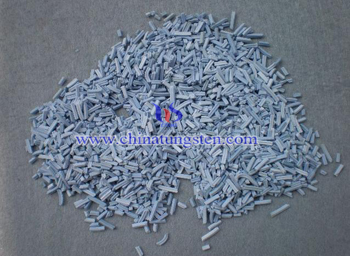
氧化钨供应商:中钨在线科技有限公司 | 产品详情: http://www.tungsten-oxide.com |
电话:0592-5129696 传真:5129797 | 电子邮件:sales@chinatungsten.com |
钨钼文库:http://i.chinatungsten.com | 钨钼图片: http://image.chinatungsten.com |
钨新闻3G版:http://3g.chinatungsten.com | 钼业新闻: http://news.molybdenum.com.cn |


硬质合金钢连接工艺
- 详细资料
- 分类:钨业知识
- 发布于 2016年5月03日 星期二 15:43
- 作者:xiaobin
- 点击数:738
随着科学技术的飞速发展,轧制技术领域的相应需求也在不断增大。轧辊是轧钢厂轧钢机上的重要零件,利用一对或一组轧辊滚动时产生的压力来轧碾钢材。它主要承受轧制时的动静载荷,磨损和温度变化的影响。轧辊硬度检测常用的肖氏和里氏硬度检测,二者均为反弹式硬度检测,表面淬火硬度为HS45-105。采用单一材料制成的压辊已经难以满足如今日益变化的轧制需求,若采用镀层工艺,虽然能够保证达到规定的性能要求,但是镀层与基体的结合强度以及热膨胀系数等参数存在一定的匹配问题且造价较高,一直得不到很好的推广。而采用复合结构的复合型压辊,组织均匀,结构致密且轧制性能稳定,已经成为了国内外许多相关研究人员的研究热点之一。采用硬质合金钢连接工艺制成的硬质合金复合型轧辊,一方面既发挥了硬质合金的高硬度、高致密性、良好的耐磨耐蚀性以及低的热膨胀系数,另一方面又充分利用了钢材的强韧性,使得硬质合金复合轧辊能够适应大多数轧制行业的使用需求。
理论上说,不同材料的连接通常难于同种材料的连接。这是由于不同材料的连接质量不仅会受到材料本身理化性能的性能的影响,其更大程度上还取决于两种材料性能的匹配与否。硬质合金是由高硬度的难熔金属碳化物为基体,加入粘结相金属并通过粉末冶金的方法制成的合金材料,在力学性能、机械性能等方面与常用钢铁材料(铸铁、铸钢、碳素钢等)存在一定的差别。尤其是两者在线膨胀系数上的差异是直接影响连接性能的关键因素,其容易在接头处产生内应力。若该应力超过了硬质合金的抗拉强度,则会导致硬质合金开裂。另外,硬质合金材料的特殊性,通常采用的方法有热装法、铸造法、热等静压法、焊接法以及胶结法,其中的WC复合铸造和钎焊过程对铁水和钎料的润湿性较差。
热装法是利用内层的过盈量,以热装的方式将内外层固定在一起。该工艺要求硬质合金外环必须具有一定的厚度,以避免内环在张力的作用下开裂。因此该工艺最大的缺陷就在于对硬质合金的损耗较大,无法节约成本。而胶结法,顾名思义就是采用环氧树脂等高分子粘合剂将内外环粘结在一起。但是由于胶黏剂的理化性质限制,使得通过该工艺所制备的复合轧辊无法在高温高压的环境下使用,在交变应力与机械应力的共同作用下,极其容易发生表面开裂的现象。
因此,目前主要使用的三种方法是铸造法、热等静压法以及焊接法。铸造法是在硬质合金外环上预镀一层金属作为过渡层,采用浇铸的方法将铸铁与硬质合金外环结合成复合轧辊。其中的铸焊工艺和CIC铸入式工艺是两种应用较多的方法:铸焊工艺是将硬质合金的表面清理干净并涂覆一层低熔点钎料,在铸型型腔中利用液态金属的热量使硬质合金表面的低熔点合金熔化,形成的过渡层将硬质合金和铸铁紧密结合;CIC铸入式硬质合金则是将硬质合金环与球墨铸铁浇铸在一起形成坚固的冶金连接,这样一来可以分散硬质合金上的应力分布,具有高硬度和优良耐磨性的硬质合金外环承受纯轧制力,韧性好的球墨铸铁通过与硬质合金外环的良好连接进行轧制力矩的传递。但是铸造法也存在一定的技术上的问题,如浇铸过程难以得到精确控制,这样一来会造成复合轧辊的质量稳定性得不到保证。
硬质合金供应商:中钨在线科技有限公司 | 产品详情: http://www.tungsten-carbide.com.cn |
电话:0592-5129696 传真:5129797 | 电子邮件:sales@chinatungsten.com |
钨钼文库:http://i.chinatungsten.com | 钨钼图片: http://image.chinatungsten.com |
钨新闻3G版:http://3g.chinatungsten.com | 钼业新闻: http://news.molybdenum.com.cn |


含三氧化钨的超强酸脱硫催化剂
- 详细资料
- 分类:钨业知识
- 发布于 2016年5月03日 星期二 17:56
- 作者:chunyan
- 点击数:772
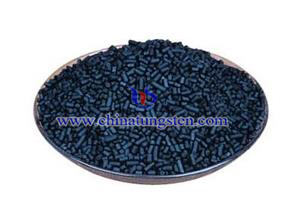
氧化钨供应商:中钨在线科技有限公司 | 产品详情: http://www.tungsten-oxide.com |
电话:0592-5129696 传真:5129797 | 电子邮件:sales@chinatungsten.com |
钨钼文库:http://i.chinatungsten.com | 钨钼图片: http://image.chinatungsten.com |
钨新闻3G版:http://3g.chinatungsten.com | 钼业新闻: http://news.molybdenum.com.cn |


生肖龙钨金块
- 详细资料
- 分类:钨业知识
- 发布于 2016年5月03日 星期二 11:25
- 作者:yaqing
- 点击数:685
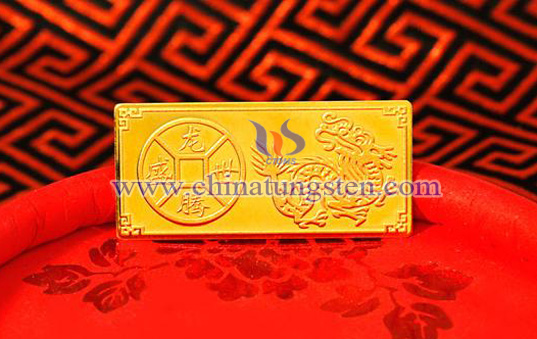
生肖钨金供应商:中钨在线科技有限公司 | 产品详情: http://t.tungsten-alloy.com |
电话:0592-5129696 传真:5129797 | 电子邮件:sales@chinatungsten.com |
钨钼文库:http://i.chinatungsten.com | 钨钼图片: http://image.chinatungsten.com |
钨新闻3G版:http://3g.chinatungsten.com | 钼业新闻: http://news.molybdenum.com.cn |

