钨粉钼砂直接炼钢工艺
- 详细资料
- 分类:钨业知识
- 发布于 2016年7月01日 星期五 18:15
- 作者:xinyi
- 点击数:754
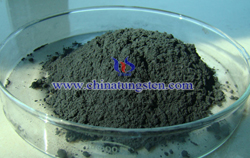
钨粉供应商:中钨在线科技有限公司 | 产品详情: http://www.tungsten-powder.com |
电话:0592-5129696 传真:5129797 | 电子邮件:sales@chinatungsten.com |
钨钼文库:http://i.chinatungsten.com | 钨钼图片: http://image.chinatungsten.com |
钨新闻3G版:http://3g.chinatungsten.com | 钼业新闻: http://news.molybdenum.com.cn |


钨粉粒度分布对聚能射孔弹破甲性能的影响
- 详细资料
- 分类:钨业知识
- 发布于 2016年7月01日 星期五 18:10
- 作者:xinyi
- 点击数:821
钨粉供应商:中钨在线科技有限公司 | 产品详情: http://www.tungsten-powder.com |
电话:0592-5129696 传真:5129797 | 电子邮件:sales@chinatungsten.com |
钨钼文库:http://i.chinatungsten.com | 钨钼图片: http://image.chinatungsten.com |
钨新闻3G版:http://3g.chinatungsten.com | 钼业新闻: http://news.molybdenum.com.cn |


钨铜电极烧结性能的内部影响因素
- 详细资料
- 分类:钨业知识
- 发布于 2016年7月01日 星期五 14:55
- 作者:xiaobin
- 点击数:767
钨铜材料不但具有钨高硬度、高强度、高熔点、高密度、低热膨胀系数以及优良的耐磨耐蚀性,还具有铜良好的可塑性和优良的导电导热性,因而在电接触材料以及电极材料领域有着较为广泛的运用。但是由于二者的熔点和理化性质相差很大且完全不互溶,在制备工艺方面一般只能采用粉末冶金的方法,这也使得钨铜材料的应用范围受到了很大的限制。目前主要的制备钨铜复合材料主要方式是对W-Cu复合粉末进行高能球磨、压制、烧结,通过分析粉末本身粒度及组成和杂质所带来的对烧结性能的影响,从而更好地控制各项参数以达到高性能的钨铜电极产品。
一般来说,在制备钨铜电极材料的过程中,为了提高压坯的成型效果,会加入一些化学助剂,如无水乙醇、硬脂酸等。这些助剂会在后续的烧结工序中直接挥发或分解,在颗粒间形成气孔。当烧结温度不断升高,液相Cu流动性变差,气体没有完全逸出形成封闭的孔隙,从而影响钨铜电极的致密度。此外这些助剂还很可能分解形成一些C、H、O等杂质元素,其直径较小,在合金中有很强的扩展能力,因而比较容易在晶界、相界等能量较高的位置发生偏聚,甚至生成脆生相,使合金在断裂过程中的沿晶断裂数目增加,降低了整体的性能。
对于粉末粒度来说,当粉末的晶粒尺寸小到一定程度时,粉末烧结温度下降,比表面积增加,烧结活性增强,利于粉末的合金化。当粉末粒度达到纳米级别时,粉末扩散大大提高,致密化过程加快,同时也可加大最终钨铜电极的致密度。有实验表明,在一定烧结温度和保温时间下,烧结体中的W颗粒尺寸会随着球磨时间的增大而增大。这是由于W颗粒尺寸变小是W在Cu中的溶解度增大所致。此外,由于球磨过程中反复地冷焊、破碎,晶格发生了严重的畸变,从而贮能升高,导致W在Cu中溶解度升高。
钨铜合金供应商:中钨在线科技有限公司 | 产品详情: http://www.tungsten-copper.com |
电话:0592-5129696 传真:5129797 | 电子邮件:sales@chinatungsten.com |
钨钼文库:http://i.chinatungsten.com | 钨钼图片: http://image.chinatungsten.com |
钨新闻3G版:http://3g.chinatungsten.com | 钼业新闻: http://news.molybdenum.com.cn |


烧结工艺对钨铜电极烧结性能的影响
- 详细资料
- 分类:钨业知识
- 发布于 2016年7月01日 星期五 14:56
- 作者:xiaobin
- 点击数:650
除了钨铜粉末自身的粒度及组成和外来杂质对钨铜电极的烧结性能所产生的影响外,烧结工艺本身的参数控制也会对其性能产生一定的影响。烧结工艺对钨铜电极烧结性能的影响主要源于两个方面,其一是成型压力的影响,另一个则是烧结气氛的影响。在试样进行压制成型时,通常会经历三个变化阶段。第一阶段是滑动阶段,此时压坯的密度上升很快;第二阶段是在第一阶段的基础上继续加压,空隙度为减少,压坯的密度几乎不发生改变;第三阶段是当压力继续增大超过某一定值时,随着压力继续升高,压坯密度相对继续增加。一方面是由于压力的增大提高了材料在压制第三阶段的致密化程度,即当压力继续增大超过某一定值时,如果继续增大压力,使粉末所受到的挤压力与摩擦力大于其弹性应力,颗粒产生塑性变形以填塞粉末间隙,其密度进一步增加;另一方面,由于纳米晶粒本身就具有极大的表面自由能,若进一步增大压制压力,通颗粒会发生塑性变形且表面自由能进一步增大,熔点则进一步被降低。这就使得其在较低温度下就能够有效浸润W颗粒。
在钨铜复合材料球磨过程中,随着球磨时间的延长,就不避免地会带来杂质金属元素,真空烧结可有效排除杂质元素或其氧化物,起到提纯的作用;另外,真空烧结还有利于排除吸附气体(孔隙中残留气体以及反应气体产物),对促进烧结后期的收缩作用明显。此外,在烧结到一定温度时候应该对炉体充如惰性气体进行保护。但是,充入惰性气体的时机是一个至关重要的问题。若充入时间过早,材料表面铜颗粒没有完全熔化和封闭表面,氩气便会通过颗粒之间的缝隙进入材料体内填充原本被抽成真空的孔洞,增大液态铜在对钨颗粒间隙进行浸润与填塞时的阻力,并在铜熔化并封闭材料表面后形成气孔;若充入时间过晚,材料表面已经产生了裂纹,再充入惰性气体也就错过了最好时机。最佳的时机应该是当表面铜已经大部分熔化并封闭表面,而温度却又没有高到发的程度。这时候充入惰性气体能够降低引起液相Cu的扩散的驱动力, 保持材料内部铜含量的稳定。
钨铜合金供应商:中钨在线科技有限公司 | 产品详情: http://www.tungsten-copper.com |
电话:0592-5129696 传真:5129797 | 电子邮件:sales@chinatungsten.com |
钨钼文库:http://i.chinatungsten.com | 钨钼图片: http://image.chinatungsten.com |
钨新闻3G版:http://3g.chinatungsten.com | 钼业新闻: http://news.molybdenum.com.cn |


钨粉应用于聚能射孔弹
- 详细资料
- 分类:钨业知识
- 发布于 2016年6月30日 星期四 18:07
- 作者:xinyi
- 点击数:785
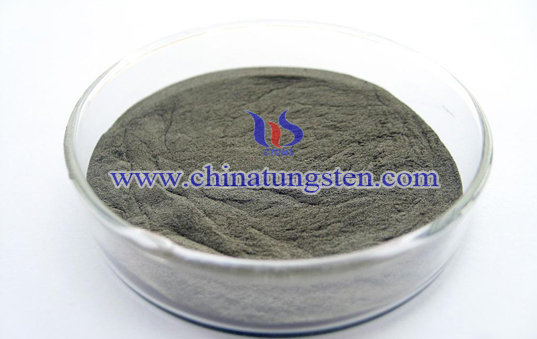
钨粉供应商:中钨在线科技有限公司 | 产品详情: http://www.tungsten-powder.com |
电话:0592-5129696 传真:5129797 | 电子邮件:sales@chinatungsten.com |
钨钼文库:http://i.chinatungsten.com | 钨钼图片: http://image.chinatungsten.com |
钨新闻3G版:http://3g.chinatungsten.com | 钼业新闻: http://news.molybdenum.com.cn |

