黑白钨矿捕收剂—GY螯合捕收剂
- 详细资料
- 分类:钨业知识
- 发布于 2017年6月02日 星期五 19:28
- 点击数:2975
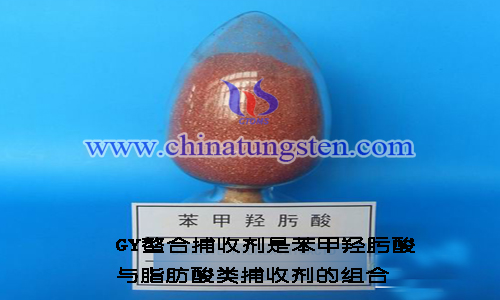
我国黑白钨混合矿大部分为组分复杂、有用矿物嵌布粒度细、选矿难度大的贫矿,在早期,黑白钨混合矿的选矿是个技术难题,两个同名不同姓的家伙往往只能选其一不能选其二,导致资源浪费和成本增加,黑白钨混合矿山经济效益不高,然而随着新型黑白钨矿捕收剂--GY螯合捕收剂的出现,难题便迎刃而解。
黑钨矿捕收剂—COBA螯合捕收剂
- 详细资料
- 分类:钨业知识
- 发布于 2017年6月02日 星期五 19:22
- 点击数:1926
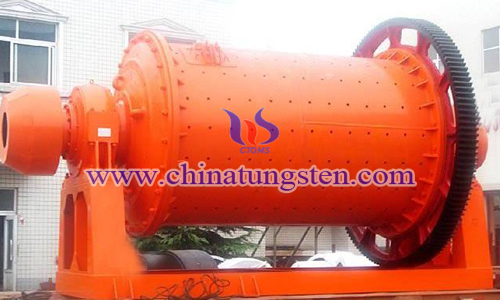
浮选过程中,捕收剂的作用是改变钨元素的表面疏水性,使浮游的钨矿颗粒黏附于气泡上。由于螯合捕收剂对金属具有更好的选择性,所以近年来,螯合剂在黑钨矿浮选中得到了越来越广泛的应用,COBA 是一种新型螯合捕收剂,相对于其它的黑钨矿捕收剂,COBA兼具选择性好和捕捉能力强的优点且廉价。
黑钨矿捕收剂—水杨羟肟酸
- 详细资料
- 分类:钨业知识
- 发布于 2017年6月02日 星期五 19:18
- 点击数:3924
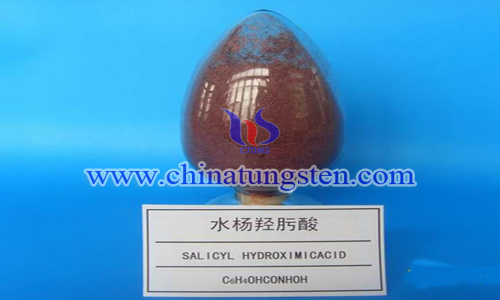
浮选过程中,捕收剂的作用是改变钨元素的表面疏水性,使浮游的钨矿颗粒黏附于气泡上,水杨羟肟酸是一种较常用的羟肟酸螯合捕收剂,相对于油酸,它具有更强的黑钨矿捕收能力。
黑钨矿精选—枱浮作业
- 详细资料
- 分类:钨业知识
- 发布于 2017年6月02日 星期五 19:14
- 点击数:2189
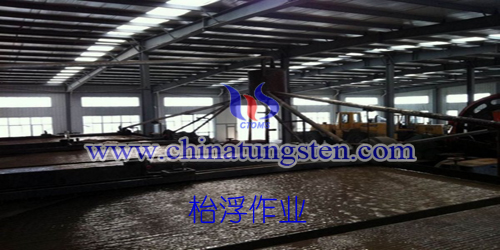
枱浮作业是黑钨矿精选阶段最重要的工序之一,它的主要作用就是分离黑钨精矿中的硫化物,达到提升黑钨精矿纯度和回收其它具有经济价值的硫化矿。
黑钨细泥回收—选择性絮凝浮选法
- 详细资料
- 分类:钨业知识
- 发布于 2017年6月02日 星期五 19:05
- 点击数:1857
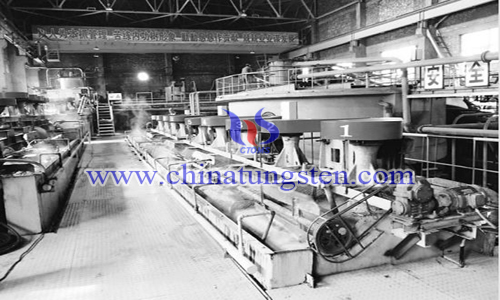
黑钨细泥因为颗粒小而成为一个选矿难题,而对细泥中更微细矿粒的回收更是难上加难,近年来,为了能有效处理微细粒黑钨细泥,工业上出现了多种先聚集再选别的工艺,选择性絮凝浮选工艺就是其中的一种新生的黑钨细泥回收工艺。