黑钨矿精选—螺旋溜槽选矿
- 详细资料
- 分类:钨业知识
- 发布于 2017年6月06日 星期二 18:44
- 点击数:2945
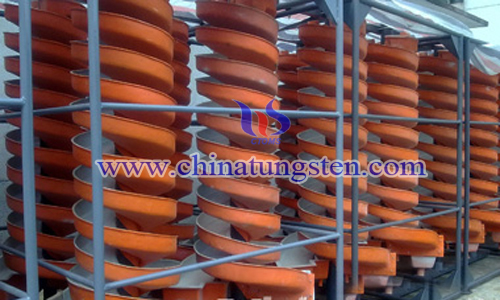
螺旋溜槽选矿是利用沿斜面流动的水流进入溜槽,在垂直运动下实现矿和砂分离的选矿的方法,它是利用矿石与脉石不同比重、不同密度来实现分层的。在近年来的黑钨矿精选中,它有部分或全部取代摇床选矿的趋势。
硬质合金烧结润湿角影响因素
- 详细资料
- 分类:钨业知识
- 发布于 2017年6月06日 星期二 17:22
- 点击数:2797
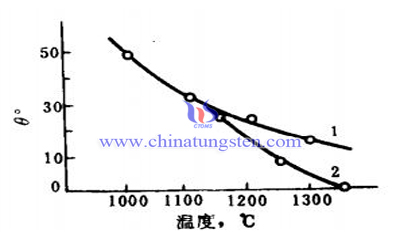
硬质合金烧结时润湿性对致密化、合金组织与性能影响极大,而体现液相和固体颗粒润湿性的是润湿角。液相只有具备完全或部分润湿的条件,即润湿角为0°<θ<90°,才能渗入颗粒的微孔和裂隙甚至晶粒间。而影响润湿角的因素有很多,如烧结温度,接触时间,添加剂,烧结气氛等。
硬质合金烧结液相润湿性
- 详细资料
- 分类:钨业知识
- 发布于 2017年6月06日 星期二 17:19
- 点击数:2344
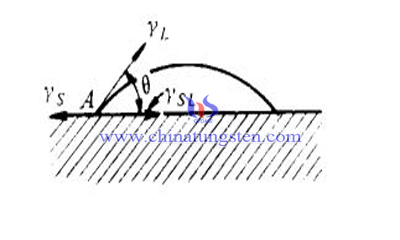
硬质合金属于典型的多元系液相烧结,硬质合金坯体在低于合金主要组分(WC)熔点的温度下烧结,低熔点组分(Co)熔化并与WC形成低熔共晶相。液相烧结能否顺利完成(致密化进行彻底),取决于同液相性质有关的三个基本条件:润湿性、溶解度和液相数量。这其中润湿性对致密化、合金组织与性能影响极大。
硬质合金综合作用烧结理论
- 详细资料
- 分类:钨业知识
- 发布于 2017年6月06日 星期二 17:18
- 点击数:1897
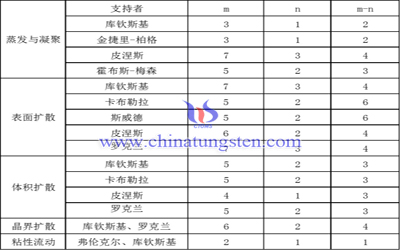
硬质合金烧结是一种复杂过程,通常是两种或两种以上的机制同时存在。在特定的条件下,一种机制占优势,限制着整个烧结过程的速度,那么它的动力学方程就可作为实际烧结过程的近似描述。但这种近似仍然十分粗糙。这就需要对烧结过程进行系统而综合的理论描述。
硬质合金烧结机制的判定
- 详细资料
- 分类:钨业知识
- 发布于 2017年6月06日 星期二 17:14
- 点击数:2015
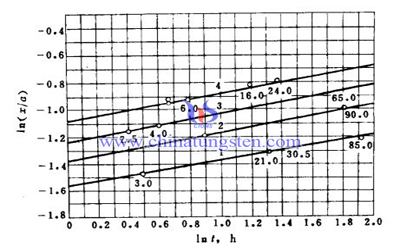
硬质合金烧结时,由于原料的不同、工艺的不用都可能对实际的烧结机制产生影响。判定实际的烧结机制可以通过指数法和烧结图两种方式进行。烧结理论目前只指出了烧结过程中各种可能出现的物质迁移机构及其相应的动力学规律,而后者只有当某一种机构占优势时,才能够应用。不同的粉末、不同的粒度、不同的烧结温度或等温烧结的不同阶段以及不同的烧结气氛、方式(如外应力)等都可能改变烧结的实际机构和动力学规律。具体的主导烧结机制取决于粉末材质,粉末粒度,粉末颗粒的致密度,表面状态,烧结温度和烧结气氛等。
硬质合金各烧结机制比较
- 详细资料
- 分类:钨业知识
- 发布于 2017年6月06日 星期二 17:10
- 点击数:1923
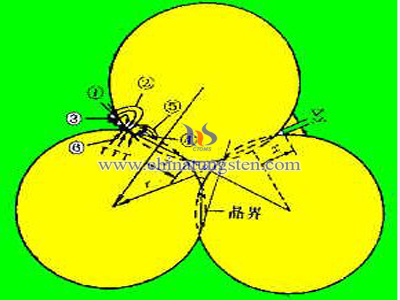
硬质合金烧结机制主要有粘性流动、蒸发于凝聚、体积扩散、表面扩散、晶界扩散、塑性流动等。各个烧结机制在本质上既有一些共同点,又有一些异同。实际的烧结过程,比模型研究的条件复杂得多,各种机制可能同时或交替地出现在某一烧结过程中。
硬质合金烧结机制-塑性流动
- 详细资料
- 分类:钨业知识
- 发布于 2017年6月06日 星期二 17:08
- 点击数:2187
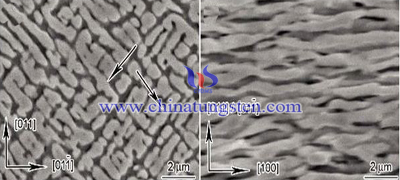
硬质合金烧结过程中物质迁移机制有很多种,如粘性变形、扩散、塑性变形等。不同的学者对此持不同的观点。其中,有学者认为,烧结颈形成和长大可看成是金属粉末在表面张力作用下发生塑性变形的结果。
硬质合金烧结机制-晶界扩散
- 详细资料
- 分类:钨业知识
- 发布于 2017年6月06日 星期二 17:05
- 点击数:3129
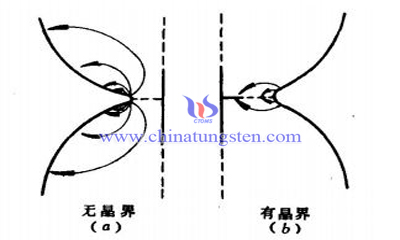
硬质合金生产中烧结极其重要的一道工序,它对硬质合金制品的性能影响巨大。烧结过程中伴随物质迁移,这其中扩散机制起着特别而十分重要的作用,晶界扩散是扩散机制的一种,它对烧结有着重要的意义,晶界对烧结颈长大和烧结体收缩会起到作用。
硬质合金烧结机制-表面扩散
- 详细资料
- 分类:钨业知识
- 发布于 2017年6月06日 星期二 17:04
- 点击数:2109
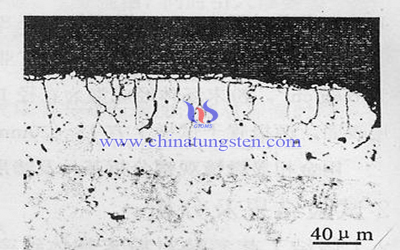
硬质合金生产中烧结是最重要的一道工序,它对产品的性能有着重要的影响。研究烧结过程中物质迁移有助于烧结工艺的有效制定。而在这些物质迁移机制中,表面扩散对物质的迁移具有重要的作用。
硬质合金烧结机制-体积扩散
- 详细资料
- 分类:钨业知识
- 发布于 2017年6月06日 星期二 17:01
- 点击数:3433
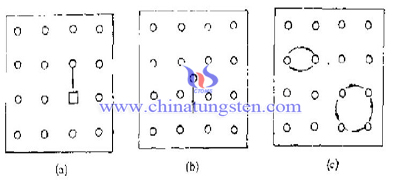
硬质合金烧结过程伴随物质迁移,这其中靠原子扩散的物质迁移也起着十分重要的作用。物质扩散是由空位浓度梯度造成化学位的差别所引起的。人们早就注意和重视扩散所起的作用,许多研究工作详细阐述了烧结的扩散过程,并应用扩散方程导出烧结的动力学方程。体积扩散是扩散机制中非常重要的一种。