硬质合金粉末压制模具材料
- 详细资料
- 分类:钨业知识
- 发布于 2017年6月01日 星期四 17:59
- 点击数:1698
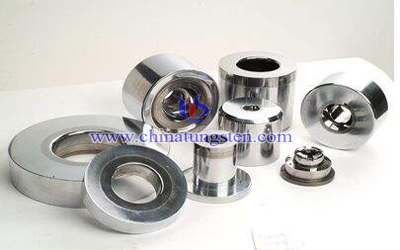
黑钨矿粗选—人工手选
- 详细资料
- 分类:钨业知识
- 发布于 2017年6月01日 星期四 17:55
- 点击数:2186
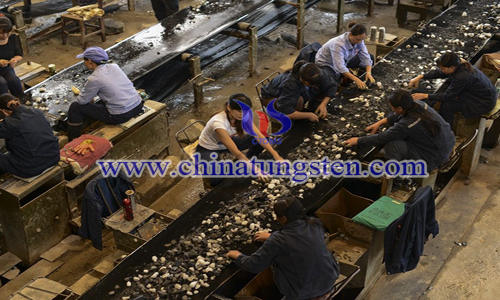
黑钨矿的粗选就是当黑钨矿石从矿山采集下来后,进入重选程序前的第一道预分等级程序,由于黑钨矿在石英脉石中的不均匀嵌布,采集过程中的废石混入量较大,将黑钨矿石和废石进行一次预先分离,有助于提高后续程序的运转效率,节约成本、减少时间,降低损耗。
钨细泥回收-细泥重浮选联合选矿工艺
- 详细资料
- 分类:钨业知识
- 发布于 2017年5月31日 星期三 19:41
- 点击数:1623
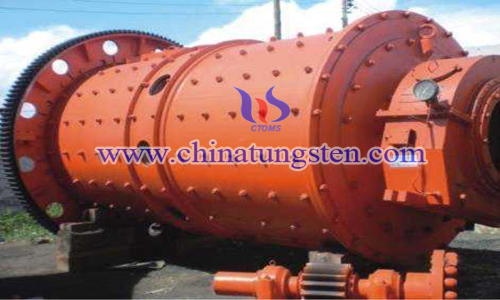
钨矿是性脆易碎的矿物,在选矿过程中极易形成细泥,因此我们的尾矿中仍然含有不少有效的钨金属元素,因此我们需要对钨细泥再次进行一次工艺处理回收,以达到资源利用效果。
钨细泥回收-全摇床选矿工艺
- 详细资料
- 分类:钨业知识
- 发布于 2017年5月31日 星期三 19:36
- 点击数:1500
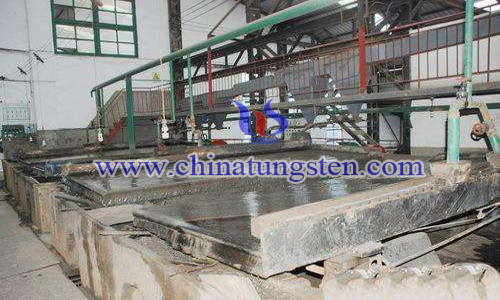
钨矿是性脆易碎的矿物,在选矿过程中极易形成细泥,因此我们的尾矿中仍然含有不少有效的钨金属元素,据统计,细泥中的钨金属量一般占原矿的11%-14%,因此,钨细泥的再一次处理能有效提高资源利用率和降低成本,所以我国的矿山都会把钨细泥做为单独的流程来处理,这也算是一种中国特色吧。
全摇床选矿工艺流程是我国早期普遍使用的一项钨细泥处理工艺,说是工艺也算不上,它就是简单的用单一摇床对浓缩过的细泥进行处理,主要的过程就是“筛”,为提升细泥回收的精矿品位,有的矿山还会不厌其烦地多“筛”几遍,然而这种工艺再怎么“筛”,回收率35%就是它的天花板极限,再也没办法提高了,因为对于37微米以下的钨细泥,摇床它筛不到只能鞭长莫及,看着细泥从指缝中流过。
虽说全摇床选矿工艺现在有种种不好,但也不能因为它落后就去全盘否定它,在工业技术并不发达的年代,这种简单可靠,指标稳定的回收法是各矿山回收细泥的主要手段,虽说最多只有35%的回收率,但是27%—35%基本是稳的,而且任何工艺的进步都是在实践中摸索,由易至难,由简至繁前进的,全摇床选矿工艺流程虽说现在落后了,但它也算是细泥回收的“鼻祖”也有着不可磨灭的历史作用。
钨产品供应商:中钨在线科技有限公司 | 产品详情: http://cn.chinatungsten.com |
电话:0592-5129696 传真:5129797 | 电子邮件:sales@chinatungsten.com |
钨钼文库:http://i.chinatungsten.com | 钨钼图片: http://image.chinatungsten.com |
钨新闻3G版:http://3g.chinatungsten.com | 钼业新闻: http://news.molybdenum.com.cn |


白钨矿的浮选法-剪切絮凝浮选法
- 详细资料
- 分类:钨业知识
- 发布于 2017年5月31日 星期三 19:32
- 点击数:1707
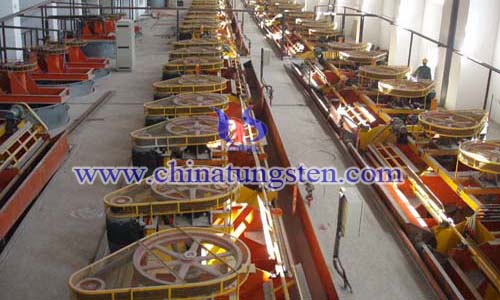
剪切絮凝浮选法是近年来在我国逐渐应用的一种新的白钨矿浮选法,是上世纪瑞典人首先使用的方法,这种方法主要针对含矿品位低、杂质多的白钨矿。
白钨矿的浮选法-常温浮选法
- 详细资料
- 分类:钨业知识
- 发布于 2017年5月31日 星期三 19:26
- 点击数:1733
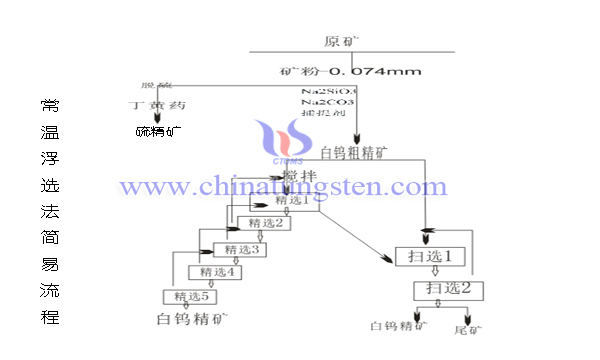
一般来说,加温浮选法是主要缺点是成本高和耗时间,所以,在不断的实践中,我国的钨业发展出了常温浮选法。
白钨矿的浮选法-加温浮选法
- 详细资料
- 分类:钨业知识
- 发布于 2017年5月31日 星期三 19:19
- 点击数:1971
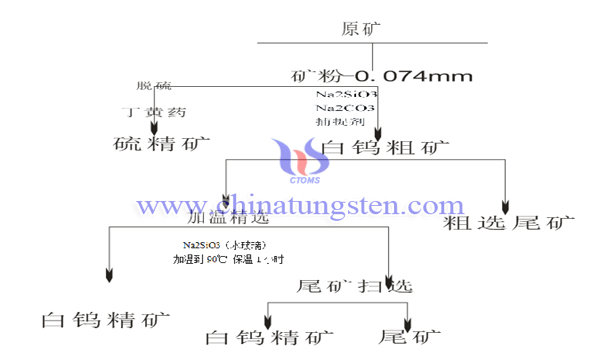
加温浮选法在1970年以前是我国普遍使用的白钨矿的浮选法,是前苏联化学家彼得诺夫于1940年发明的,所以又称彼得诺夫法。
浮选法-白钨矿的粗选
- 详细资料
- 分类:钨业知识
- 发布于 2017年5月31日 星期三 19:09
- 点击数:1799
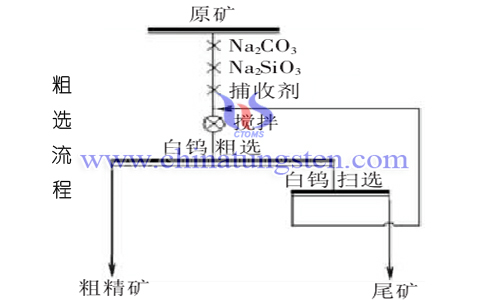
在自然界中,白钨矿大多存在于矽卡岩层中,与可浮性好的含钙脉石矿物共生,所以白钨矿也被称为钨酸钙矿(CaWO4)。在选矿的过程中,这些含钙类矿石成了白钨矿提纯的拖油瓶,难分难舍得必须用到化学方法才能将它们分离,这个过程叫浮选,白钨矿的粗选是浮选法的第一个阶段。
无粘结相硬质合金碳控制
- 详细资料
- 分类:钨业知识
- 发布于 2017年5月31日 星期三 18:22
- 点击数:2155
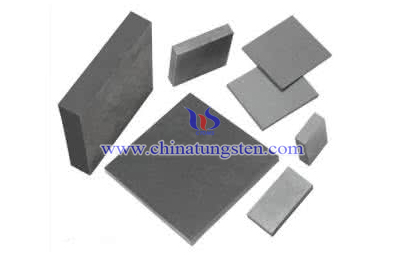