冷等静压的包套和模具
- 详细资料
- 分类:钨业知识
- 发布于 2017年4月18日 星期二 19:43
- 作者:ruibin
- 点击数:2266
冷等静压可大致分为两个大的工艺过程:模具的制造和成形。在冷等静压技术中,包套和模具的合理设计,是保证压坯质量和提高包套使用寿命的关键,也是节约原材料、降低成本的重要因素。
无论是湿袋法还是干袋法,模具都是由塑性模、刚性模、端口密封装置和支撑装置四个基本构件组成。
一、塑性模
塑性模也称为塑料软模,塑性模在冷等静压成型中,不仅起型模作用,而且起传递压力使粉料达到成型致密的作用。
二、刚性模
刚性模的模芯、型模等是由金属材料制成的.刚性模的尺寸形状在成型过程中保持不变。
三、端口密封装置
依据压坯的形状和尺寸
不同.可设计成不同的形式。如成型圆柱形的压坯的端口装置,
常见的密封方式有:橡胶塞密封;橡胶塞加包套密封;包套盖加弹性环密封;弹性包套盖自密封;包套盖刚性环捆扎密
封;弹性包套盖刚性自紧加捆扎密封等。对于冷等静压工艺,成形模具的端口密封装置具有十分重要的作用。封口密封装置需要具备塑性和刚性这两个矛盾的特性,既要起到密封作用,又要方便装取料,当然也要考虑使用寿命、成本等。
四、支撑装置(支撑桶)
由于包套薄,对包套内的粉末进行除氧时,很难保持装料后包套固定的形状,需要在包套外附设一种专门的支撑装置。这种装置,可分为固定型和随机型。
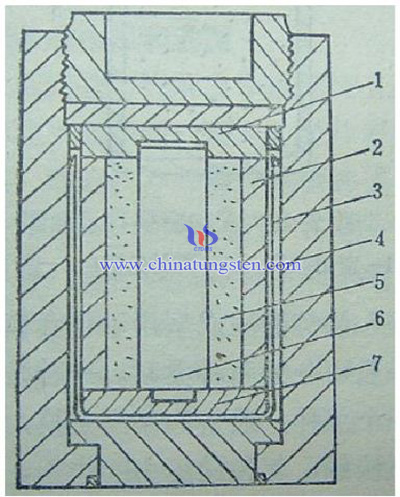
干袋包套组合模示意图
1-上橡胶端塞
2-塑性模
3-液体传压介质
4-支撑装置
5-粉末
6-刚性模芯
7-下橡胶端塞
硬质合金供应商:中钨在线科技有限公司 | 产品详情: http://www.tungsten-carbide.com.cn |
电话:0592-5129696 传真:5129797 | 电子邮件:sales@chinatungsten.com |
钨钼文库:http://i.chinatungsten.com | 钨钼图片: http://image.chinatungsten.com |
钨新闻3G版:http://3g.chinatungsten.com | 钼业新闻: http://news.molybdenum.com.cn |
微博

微信

等静压传压介质
- 详细资料
- 分类:钨业知识
- 发布于 2017年4月18日 星期二 19:35
- 作者:ruibin
- 点击数:2111
1利用帕斯卡原理对粉末进行等静压压制时,其成形有两个要点:
a、被压缩液体或气体的任意点静压应力相等(即等静压)
b、液体或气体对内部粉末的压力是通过液/固或气/固界面进行的,如果固体坯中的气孔与液体或气体相连,将无法压缩气孔,因此需要使用致密包套包裹固体,才能对固体进行压制。
等静压传压介质
等静压传压介质有三类:液体、固体和气体。
按传压特性来看,液体和气体可以无损耗地传递压力,这种特性成为准静力特性,具备这种特性的传压介质称之为准静力介质。反之,不具备这种特性的传压介质称之为非准静力介质。固体介质就是非准静力介质。
1)气体传压介质
一般采用Ar、He、N2等气体。
气体容易被压缩,在高压下甚至出现液化。所以常温下,气体传压介质应用于不大于100MPa场合,或用于热等静压中。下图为常温下Ar密度与压力的关系。
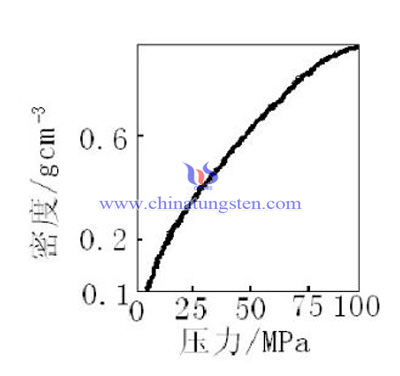
2)液体传压介质
常用的液体传压介质有甘油、水、矿物油、黄油等。液体也具有可压缩特性,当液体所受到的压力低于50MPa时,不会凝固。在高压下,液体甚至出现凝固现象。当水的压力超过400MPa时或者矿物油的压力大约超600MPa时,会出现凝固。因此在液体等静压时压力通常低于300MPa。如果要采用更高的压力,熔融盐、玻璃熔体、各种金属熔液也可作为传压介质,特别是在热等静压中,最大压力可达1000MPa。
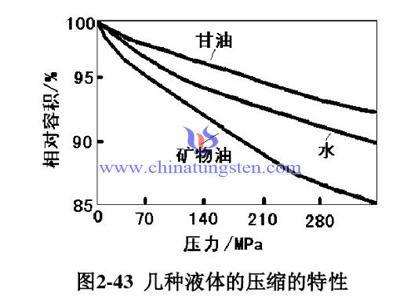
3)固体传压介质
当等静压的压力超过400MPa时,一般使用弹性或塑性较好的固体,如橡胶、塑料软膜、滑石粉、氮化硼粉、Cr2O3粉、硬脂酸锌粉等作为传压介质;如果所需压力继续增大,到1500MPa时,可用铁粉、镍粉、滑石粉等作传压介质。
硬质合金供应商:中钨在线科技有限公司 | 产品详情: http://www.tungsten-carbide.com.cn |
电话:0592-5129696 传真:5129797 | 电子邮件:sales@chinatungsten.com |
钨钼文库:http://i.chinatungsten.com | 钨钼图片: http://image.chinatungsten.com |
钨新闻3G版:http://3g.chinatungsten.com | 钼业新闻: http://news.molybdenum.com.cn |
微博

微信

等静压成形种类
- 详细资料
- 分类:钨业知识
- 发布于 2017年4月17日 星期一 19:33
- 作者:ruibin
- 点击数:2009
等静压成型是将待压试样置于高压容器中,利用介质不可压缩的性质和均匀传递压力的性质从各个方向对试样进行均匀加压,当介质通过压力泵注入压力容器时,根据流体力学原理,其压强大小不变且均匀地传递到各个方向。此时高压容器中的粉料在各个方向上受到的压力是均匀的和大小一致的。特点:等静压成型时介质传递的压力在各个方向上等是相等的。弹性模具在受到介质压力时产生的变形传递到模具中的粉料,粉料与模具壁的摩擦力小,坯体受力均匀,密度分布均一,产品性能有很大提高。按成形温度的高低,等静压技术通常分为冷等静压(cold isostatic pressing,CIP)、温等静压(warm isostatic pressing,WIP)和热等静压(hot isostatic pressing,HIP).

1、冷等静压
在常温下的等静压称之为冷等静压,流程如下
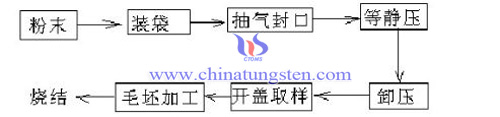
冷等静压又分为干袋等静压和湿袋等静压这两种。
干袋等静压是将成形模具(包套)永久地固定在高压缸内,将粉料直接填入高压缸内的包套内进行压制。特点是适用于简单形状制件的大批量生产,便于自动化。
湿袋等静压所用的包套不是高压缸的一个固定部分,包套完全浸入液体介质中。特点是适应性强,可以同时一缸多袋,适合于小批量生产,能生产大型的复杂的制件。
2、温等静压
当粉末在室温下不能成形时,可采用温等静压。通常在粉末中添加有很高塑化能力的粘结剂,通过温等静压成形获得更高强度的压坯,特点是工作温度介于冷等静压和热等静压。
3、热等静压
热等静压是一种在高温(1000℃以上)高压(100MPa以上)同时作用下使物料经受等静压的技术。特点是将粉末成形与烧结结合在一起,还可以用于扩散粘结、缺陷消除等领域。工作介质一般采用惰性气体(氩气或氮气),也可采用液态金属、固体颗粒作为压力传递介质。包套材料通常为金属或玻璃。
硬质合金供应商:中钨在线科技有限公司 | 产品详情: http://www.tungsten-carbide.com.cn |
电话:0592-5129696 传真:5129797 | 电子邮件:sales@chinatungsten.com |
钨钼文库:http://i.chinatungsten.com | 钨钼图片: http://image.chinatungsten.com |
钨新闻3G版:http://3g.chinatungsten.com | 钼业新闻: http://news.molybdenum.com.cn |
微博

微信

压制润滑剂
- 详细资料
- 分类:钨业知识
- 发布于 2017年4月17日 星期一 19:38
- 作者:ruibin
- 点击数:1850
采用润滑剂的目的是使压制成形时压力分布均匀,并且在压制后容易脱模。润滑剂可混合在粉末内或涂在模壁上。压制成形中存在有几种不同类型的摩擦,它们都受到润滑剂的影响。应认真选择润滑剂的种类及其添加数量。粉末里混入润滑剂,会影响粉末的流动及其松装密度,同时也影响粉末混合。粉末体中的摩擦受粉末材质种类、粉末粒度、粉末形状以及周围介质(如气体气氛)和温度的影响。润滑剂在烧结的最初阶段被烧除.主要有固体润滑剂和液体润滑剂两种。
选择原则:
1、具有较好的润滑性并有一定粘性的物质;
2、与粉体不发生化学反应及其他有害作用;
3、不影响烧结体的性能和外观;
4、在预烧或烧结过程中容易排除,且不造成环境污染。
一、混合在粉末内的润滑剂:
硬脂酸和金属的硬质酸盐,如硬脂酸锌、硬脂酸锂、硬脂酸钙、硬脂酸钡、硬脂酸铝、液体石蜡、二硫化钼、石墨等。通常通过双锥混料器以细粉末的形式加入混合料中。加入量为粉体重量的0.5%-1.0%,视压坯的形状和粉体的粒度而定:若粉末细、压坯形状复杂,润滑剂加入量就较大。
多数的润滑剂会使压坯密度降低,因为其本身密度低于混合料密度。同时润滑剂包裹颗粒,妨碍固体颗粒的接触,也会造成压坯密度的降低。
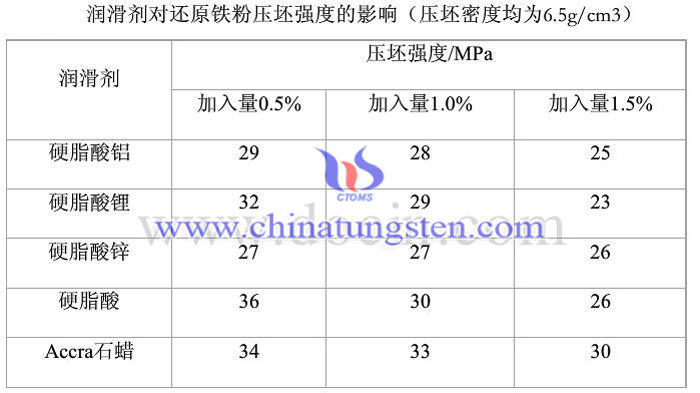
二、涂抹在模具上的润滑剂
涂抹在模具上的润滑剂可以减少压制时的外摩擦力,这样的润滑剂有:丙酮、笨、甘油、油酸、三氯乙烷等。
硬质合金供应商:中钨在线科技有限公司 | 产品详情: http://www.tungsten-carbide.com.cn |
电话:0592-5129696 传真:5129797 | 电子邮件:sales@chinatungsten.com |
钨钼文库:http://i.chinatungsten.com | 钨钼图片: http://image.chinatungsten.com |
钨新闻3G版:http://3g.chinatungsten.com | 钼业新闻: http://news.molybdenum.com.cn |
微博

微信

压坯外观缺陷
- 详细资料
- 分类:钨业知识
- 发布于 2017年4月17日 星期一 19:30
- 作者:ruibin
- 点击数:1945
在压制过程中,由于种种原因,常会产生粉末冶金压制件( 压坯) 缺陷 ,常见的压坯缺陷有压坯密度不均匀分层裂纹掉边掉角毛刺过大表面划伤同轴度超差等 。这些缺陷又可以分为:1、密度不达标;2、尺寸不达标;3、形位尺寸公差;4、外观缺陷。这其中外观缺陷最为常见。下面就几个常见的外观缺陷展开讨论。
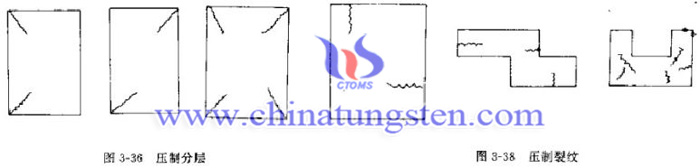
1、分层
定义:压块的棱出现,与受压面呈一定角度(大约45°),向内部延伸,形成整齐的分界面叫分层。
原因:压块中弹性内应力和剪切应力。如混合料钴含量低,碳化物硬度高,粉末或料粒愈细,成型剂太少或分布不均匀,混合料过湿或过干,压制压力过大,单重过大,压块形状复杂,模具光洁度太差,台面不平,均有可能造成分层。
改善措施:装料均匀;不超压;提高压块强度,减少压块内应力和弹性后效。
检验方法:压坯可通过观察断面;合金可同过超声波探伤。
2、裂纹
定义:压块中出现不规则局部断裂的现象叫裂纹。
原因:与分层类似,也是弹性后效的结果。区别在于应力集中部位在受压面,则分层,不在受压面,则裂纹。
措施:与分层类似,另外延长保压时间或多次加压,减少压力,单重,改善模具设计和适当增加模具厚度,加快脱模速度,增加成型剂,提高物料松装密度;可以减少裂纹。
3、未压好
定义:压坯中颗粒间孔洞尺寸太大,烧结时不能完全消失,合金内仍残留较多孔洞的现象。
原因:料粒太硬,料粒过粗,物料松装太大;松装料粒在模腔中分布不均匀,单重偏低,压制压力太小等均可能造成未压好(显颗粒)。
硬质合金供应商:中钨在线科技有限公司 | 产品详情: http://www.tungsten-carbide.com.cn |
电话:0592-5129696 传真:5129797 | 电子邮件:sales@chinatungsten.com |
钨钼文库:http://i.chinatungsten.com | 钨钼图片: http://image.chinatungsten.com |
钨新闻3G版:http://3g.chinatungsten.com | 钼业新闻: http://news.molybdenum.com.cn |
微博

微信
