选择性沉淀法从钨酸钠溶液中除钼
- 详细资料
- 分类:钨业知识
- 发布于 2015年12月24日 星期四 18:30
- 作者:linlu
- 点击数:1024
钨,钼均为我国的传统优势资源,随着优质钨、钼资源的日益消耗,不断开发和利用,高质量的钨资源不断消耗,不得不处理品位较低、杂质含量较多的复杂矿,这就从原料的加工处理上增大了选矿和冶金的难度,特别是钨、钼等一些相似元素的分离难度更大。另一方面,随着科学技术的高速发展,用户对产品纯度提出了更高的要求。传统的除钼方法不仅存在流程长、污染重、钨损失大、成本高等不足,而且料液中允许钼含量范围窄,除钼深度也达不到新的要求。近年来,正在崛起的分子设计和分子工程学已深入到化学、化工、医药、选矿等各个领域。人们已经开始从物质的宏观领域深入到物质的微观世界。借助于计算机分子结构设计智能系统,以及计算机模拟等现代科学技术手段,人们已能合成具有特定性能的特效试剂,用于解决特定的实际问题。由于钨钼同处于元素周期表的第IVB族,尽管它们之间存在一些性质差异,但这些差异并不十分明显,单纯利用这些微小的差异难以进行钨、钼的高效深度分离。因此,因此研究高效而经济的从钨酸钠溶液中深度除钼工艺为钨冶金中的重大课题。
下面就给大家介绍几种人们经过大量的实验和科学研究所掌握的几种有效的除钼方法。首先,我们来看一看第一种方法-选择性沉淀法是如何从钨酸钠溶液中除钼的。
1. 在前人成功经验的基础上,从钨冶炼过程的特定体系出发,以量子化学、结构化学及分子设计理论为基础,以钨、钼化合物的性质差异为依据,经过大量的分析和研究,设计、合成并试制成功了用于从Na2W04及(NH4) 2W04溶液中选择性高效除钼的沉淀剂M1152a 等。
2. 这些试剂与钨酸盐溶液中的钼有很强的亲和力,可在简单而又温和的条件下使钼形成难溶的稳定化合物沉淀下来,而与溶液中的钨几乎不发生作用,从而实现钨、钼的高效深度分离。
3. 实验使用过程中需要注意沉淀剂种类,沉淀剂用量对除钼效果的影响。为保证较好的除钼效果,同时尽可能降低试剂成本,对M1152a 而言,除钼剂的用量以3-4倍理论量为宜。
4. 最后再考虑除钼过程中钨回收率的高低来选择最有效的沉淀法。
钨酸钠供应商:中钨在线科技有限公司 | 产品详情: http://www.sodium-tungstate.com |
电话:0592-5129696 传真:5129797 | 电子邮件:sales@chinatungsten.com |
钨钼文库:http://i.chinatungsten.com | 钨钼图片: http://image.chinatungsten.com |
钨新闻3G版:http://3g.chinatungsten.com | 钼业新闻: http://news.molybdenum.com.cn |
微信:

微博:

仲钨酸铵循环氧化还原法制备亚微米球形钨粉
- 详细资料
- 分类:钨业知识
- 发布于 2015年12月24日 星期四 17:52
- 作者:chunyan
- 点击数:1110
钨粉是硬质合金的主要原料,更是钨基合金的主要原料。但是,钨粉属于脆性材料,其硬度和强度之间存在着矛盾:硬度高则强度低,强度高则硬度低。为了提高材料的性能,将钨粉细化成为了一种趋势,用以制备更加优异的产品。亚微米钨粉经压制烧结后可提高材料的强度、韧性,降低金属塑性和脆性转变温度,大大改善金属及合金的性能,克服硬度和强度存在的固有的矛盾。
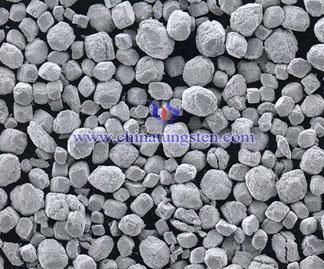
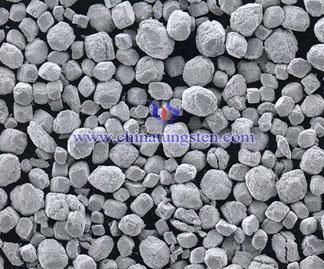
目前,国内外制备亚微米钨粉的主要方法有:循环氧化还原法、高能球磨、干燥气氛还原法、紫钨氢气还原、卤化钨氢还原法、喷雾干燥、流化床法、钨酸盐还原法、熔盐电解法和等离子体技术等。
特纯仲钨酸铵循环氧化还原法制备亚微米球形钨粉的原理是,将仲钨酸铵煅烧得到紫钨,再对紫钨进行还原,得到钨粉,对制得的钨粉进行循环2次氧化和3次还原。工艺生产过程如下:
特纯仲钨酸铵循环氧化还原法制备亚微米球形钨粉的原理是,将仲钨酸铵煅烧得到紫钨,再对紫钨进行还原,得到钨粉,对制得的钨粉进行循环2次氧化和3次还原。工艺生产过程如下:
1、将特纯仲钨酸铵在氩气中缓慢升温到800℃,当温度达到800℃时保温10min,仲钨酸铵经高温煅烧转化为紫钨;
2、用步骤1得到的紫钨在氢气中进行第1次还原,得到钨粉;
3、用步骤2制得的钨粉在空气中缓慢升温到500℃,进行第1次氧化,当温度达到500℃时保温10min,获得三氧化钨;
4、用步骤3得到的三氧化钨在氢气中进行第2次还原,制得钨粉;
5、用步骤4制得的钨粉重复步骤3的工艺条件,进行第2次氧化,获得三氧化钨;
6、用步骤5制得的三氧化钨重复步骤2的工艺条件,进行第3次还原,制备出亚微米球形钨粉。
循环氧化还原法因其独有的受污染少、粒度分布范围窄、工艺路线简捷易行、工艺参数易于控制、设备简单和适合工业化大批量生产等优点在众多方法中脱颖而出,并且,制得的亚微米钨粉颗粒呈球形,有利于钨粉在压坯烧结过程均匀化收缩,实现良好的尺寸控制。
循环氧化还原法因其独有的受污染少、粒度分布范围窄、工艺路线简捷易行、工艺参数易于控制、设备简单和适合工业化大批量生产等优点在众多方法中脱颖而出,并且,制得的亚微米钨粉颗粒呈球形,有利于钨粉在压坯烧结过程均匀化收缩,实现良好的尺寸控制。
偏钨酸铵供应商:中钨在线科技有限公司 | 产品详情: ammonium-metatungstate.com |
电话:0592-5129696 传真:5129797 | 电子邮件:sales@chinatungsten.com |
钨钼文库:http://i.chinatungsten.com | 钨钼图片: http://image.chinatungsten.com |
钨新闻3G版:http://3g.chinatungsten.com | 钼业新闻: http://news.molybdenum.com.cn |
微信:

微博:

铁系金属氧化物掺杂对三氧化钨陶瓷热电性能影响4/5
- 详细资料
- 分类:钨业知识
- 发布于 2015年12月24日 星期四 17:33
- 作者:huahuo
- 点击数:881
掺杂铁系金属氧化物三氧化钨(WO3)陶瓷的热电功率因子。掺杂氧化铁(Fe2O3)与掺杂氧化钴(Co2O3)的陶瓷功率因子要高于未掺杂的陶瓷,但是后者要明显的多,前者提高幅度不大;而掺杂氧化镍(NiO)的陶瓷只有当掺杂浓度为1.0mol%左右时,其功率因子比未掺杂陶瓷大,其余状态都比未掺杂的小。三种掺杂陶瓷的功率因子在达到最大值之前都会随着温度升高而上升,当三者都达到最大功率因子时,掺杂浓度为1.0mol%的NiO数值最大,而且数值都为另外两者的2-3倍,可见掺杂NiO对WO3陶瓷热电功率因子改善效果最佳。
掺杂NiO的 WO3陶瓷的ZT值。确定热电材料的热电转换效率高低,最准确的方式还是ZT值的高低情况,ZT是由电导率、seebeck系数、以及热导率计算得出的,热导率的测试费用相对比较高,所以一般会先去测试热电材料的功率因子,功率因子的数值达到一定水平了,才会去测试其热导率,由于三种掺杂物中NiO所掺杂的陶瓷功率因子最高,所以只对其进行热导率测试。由于掺杂NiO的WO3陶瓷在掺杂浓度为1.0mol%时功率因子最大,所以选择这个掺杂浓度下的掺杂陶瓷来热导率测试,测试结果显示掺杂NiO陶瓷的热导率随着温度上升而下降,通过之前测试的数据,计算出ZT值,当温度从373K上升至973时,ZT值上升了0.00066,说明掺杂NiO的WO3陶瓷在高温情况下具有良好热电性能,具有一定发展潜力。
氧化钨供应商:中钨在线科技有限公司 | 产品详情: http://www.tungsten-oxide.com |
电话:0592-5129696 传真:5129797 | 电子邮件:sales@chinatungsten.com |
钨钼文库:http://i.chinatungsten.com | 钨钼图片: http://image.chinatungsten.com |
钨新闻3G版:http://3g.chinatungsten.com | 钼业新闻: http://news.molybdenum.com.cn |
微信:

微博:

铁系金属氧化物掺杂对三氧化钨陶瓷热电性能影响5/5
- 详细资料
- 分类:钨业知识
- 发布于 2015年12月24日 星期四 17:35
- 作者:huahuo
- 点击数:919
热电材料能作为热电发电与制冷设备,而且无污染、噪音小,如果能将热电发电发展起来,就能替代部分传统的化石能源,既能解决能源危机又能减轻环境负担,所以热电材料是十分具有前景的一种材料。
三氧化钨(WO3)陶瓷虽然本身就具有热电性能,但是我们希望通过掺杂的手段来改善WO3陶瓷的热电性能,提高它的热电转换效率。选用具有较高电导率的铁系氧化物氧化铁(Fe2O3)、氧化钴(Co2O3)、氧化镍(NiO)作为掺杂物质,制备出了Fe2O、Co2O3和NiO掺杂的WO3陶瓷,并对三者的微观结构与热电性能进行对比,得出了一下结论:(1)三种铁系金属氧化物分别在不同程度上提高了WO3陶瓷的电导率,因此三种掺杂WO3陶瓷功率因子都得到了不同程度的提升;(2)WO3陶瓷被三种铁系金属氧化物掺杂后,从微观结构上都生成了第二相,分别为FeWO4、CoWO4、NiWO4,生成这些第二相的主要原因为掺杂物的掺杂浓度大于本身在WO3中的溶解度后稀释出来的掺杂物与WO3发生了化学反应;(3)相比掺杂Fe2O和掺杂Co2O3的WO3陶瓷,掺杂NiO的WO3陶瓷的热电性能最佳,尤其当NiO掺杂浓度为1.0mol%时,电导率提高最为明显。(4)最后将掺杂NiO,掺杂浓度为1.0mol%的WO3陶瓷进行热导率测试,并且根据之前实验数据计算出ZT值,得出在高温下具有良好的热电性能这一结果,在一定条件下能适用于制备热电发电器件。
氧化钨供应商:中钨在线科技有限公司 | 产品详情: http://www.tungsten-oxide.com |
电话:0592-5129696 传真:5129797 | 电子邮件:sales@chinatungsten.com |
钨钼文库:http://i.chinatungsten.com | 钨钼图片: http://image.chinatungsten.com |
钨新闻3G版:http://3g.chinatungsten.com | 钼业新闻: http://news.molybdenum.com.cn |
微信:

微博:

铁系金属氧化物掺杂对三氧化钨陶瓷热电性能影响3/5
- 详细资料
- 分类:钨业知识
- 发布于 2015年12月24日 星期四 17:31
- 作者:huahuo
- 点击数:916
三氧化钨(WO3)陶瓷掺杂铁系金属氧化物前后电导性能变化。温度不高时,掺杂氧化镍(NiO)的WO3陶瓷会因为掺杂浓度的不同,电导率始终在未掺杂陶瓷电导率上下波动,掺杂氧化铁(Fe2O3)与掺杂氧化钴(Co2O3)的陶瓷电导率大于未掺杂的陶瓷。掺杂NiO与掺杂Co2O3的陶瓷只要掺杂浓度不是特别大,电导率都会随着温度和浓度增加而变大,但是当掺杂量很大时,这两者掺杂的陶瓷反而电导率会下降,由于掺杂量浓度大于溶解度时会生成第二相,第二相主要存在于晶界上,使得晶界之间的流动性降低,同时使晶粒之间的空隙附着于晶界附近,导致材料的电导率下降。而掺杂Fe2O3的陶瓷会随着掺杂物浓度的不断上升,电导率也不断变大,这主要是由于作为金属氧化钨Fe2O3本身也有很良好的电导率,当掺杂浓度为10.0mol%时,WO3的电导率最大。
三氧化钨(WO3)陶瓷seebeck系数受掺杂铁系金属氧化物的影响。塞贝克(Seebeck)系数,Seebeck系数的绝对值越大,说明热电材料的热电转换效率更好。从三种掺杂陶瓷的Seebeck系数都大于未掺杂陶瓷且都为负值,可以看出三种掺杂陶瓷都是一种n型热电材料,但是不同的是掺杂Fe2O3与掺杂NiO的陶瓷的Seebeck系数绝对值都是随着温度上升而增加,而掺杂Co2O3的陶瓷在随着温度增加,Seebeck系数的绝对值并没有随着温度升高而出现单调的变化趋势,而是在某一些温度点上出现了下降。可能是在这些温度点上出现出现了相交,材料的微观结构影响了Seebeck系数。
氧化钨供应商:中钨在线科技有限公司 | 产品详情: http://www.tungsten-oxide.com |
电话:0592-5129696 传真:5129797 | 电子邮件:sales@chinatungsten.com |
钨钼文库:http://i.chinatungsten.com | 钨钼图片: http://image.chinatungsten.com |
钨新闻3G版:http://3g.chinatungsten.com | 钼业新闻: http://news.molybdenum.com.cn |
微信:

微博:
