脱硝催化剂回收三氧化钨
- 详细资料
- 分类:钨业知识
- 发布于 2016年1月28日 星期四 14:47
- 作者:qiongyao
- 点击数:773
SCR脱硝催化剂泛指应用在电厂SCR(selective catalytic reduction)脱硝系统上的催化剂(Catalyst),在SCR反应中,促使还原剂选择性地与烟气中的氮氧化物在一定温度下发生化学反应的物质。近年来,美、日、德等发达国家不断投入大量人力、物力和资金,研究开发高效率、低成本的烟气脱硝催化剂,重视在催化剂专利技术、技术转让、生产许可过程中的知识产权保护工作。最初的催化剂是Pt-Rh和Pt等金属类催化剂,以氧化铝等整体式陶瓷做载体,具有活性较高和反应温度较低的特点,但是昂贵的价格限制了其在发电厂中的应用。
SCR脱硝催化剂中回收三氧化钨和偏酸铵的方法如下所示:
1.将SCR脱硝催化剂粉碎、过筛后制成催化剂粉末,掺入碳酸钠后充分搅拌均匀。
2.将混合粉末放入烧结炉中煅烧成为烧结料。
3.保温一个小时后粉碎、过筛制成烧结料粉末,再倒入温水使烧结粉末中的钨酸钠Na2WO4和偏钒酸钠NaVO3充分溶解、经过滤、弃去沉淀后得到Na2WO4和NaVO3混合溶液。
4.调节PH值至6.5~7.5后,加入碳酸氢铵或者氯化铵溶液,析出偏钒酸铵沉淀,过滤后先用稀碳酸氢铵溶液洗涤2-3次,接着用30%的乙醇洗涤1-2次,烘干后得偏钒酸铵成品。
5.剩余溶液里Na2WO4已转换成仲钨酸铵,将剩下的的溶液蒸发制得仲钨酸铵晶体,再进行煅烧制得三氧化钨。
氧化钨供应商:中钨在线科技有限公司 | 产品详情: http://www.tungsten-oxide.com |
电话:0592-5129696 传真:5129797 | 电子邮件:sales@chinatungsten.com |
钨钼文库:http://i.chinatungsten.com | 钨钼图片: http://image.chinatungsten.com |
钨新闻3G版:http://3g.chinatungsten.com | 钼业新闻: http://news.molybdenum.com.cn |


超声空化法制备纳米三氧化钨
- 详细资料
- 分类:钨业知识
- 发布于 2016年1月28日 星期四 14:40
- 作者:qiongyao
- 点击数:726
当超声波能量足够高时,就会产生“超声空化”现象,即指存在于液体中的微小气泡(空化核)在超声场的作用下振动、生长并不断聚集声场能量,当能量达到某个阈值时,空化气泡急剧崩溃闭合的过程。空化气泡的寿命约0.1μs,它在急剧崩溃时可释放出巨大的能量,并产生速度约为110m/s、有强大冲击力的微射流,使碰撞密度高达1.5kg/cm2。空化气泡在急剧崩溃的瞬间产生局部高温高压(5000K,1800atm),冷却速度可达109K/s。超声波这种空化作用大大提高非均相反应速率,实现非均相反应物间的均匀混合,加速反应物和产物的扩散,促进固体新相的形成,控制颗粒的尺寸和分布。
超声空化法因其独特的物理效应和化学效应在制备纳米三氧化钨能收获很好的效果。因为在超声空化作用下产生的高温和在固体颗粒表面产生的大量气泡都大大降低了晶核的比表面,从而抑制了晶核的聚结和长大。另外超声空化作用产生的冲击波和微射流的粉碎作用使得凝胶沉淀以均匀的微小颗粒存在。利用超声空化技术,通过空化时产生的局部高温、高压或强冲击波和微射流等作用,可以较大幅度地减少纳米粒子间的结合力,从而有效地阻止团聚现象的产生,有利于制备了具有微孔结构高比表面积、高结晶度的纳米三氧化钨。
制备方法是:匀速把配置好的钨酸钠溶液加入阳离 子树脂交换柱中,交换后的钨酸溶液放入烧杯,冷却后会形成凝胶。放置1~2天后,加入蒸馏水超声分散凝胶20min,在8000r/min下离心分离1h 得到沉淀物。然后在重复上述过程1、4、7、10次后在室温下分别进行真空干燥或100℃干燥,可得含少量结晶水的不同纳米级微孔三氧化钨样品。
氧化钨供应商:中钨在线科技有限公司 | 产品详情: http://www.tungsten-oxide.com |
电话:0592-5129696 传真:5129797 | 电子邮件:sales@chinatungsten.com |
钨钼文库:http://i.chinatungsten.com | 钨钼图片: http://image.chinatungsten.com |
钨新闻3G版:http://3g.chinatungsten.com | 钼业新闻: http://news.molybdenum.com.cn |


纳米金刚石涂层硬质合金球简介
- 详细资料
- 分类:钨业知识
- 发布于 2016年1月27日 星期三 17:00
- 作者:xiaobin
- 点击数:906
纳米金刚石涂层多见于硬质合金刀具等平面体的应用中,像硬质合金球这样的球体或曲面上需要采用有别于传统的化学气相沉积法(Chemical Vapor Deposition,CVD)和物理气相沉积法(Physical Vapor Deposition,PVD)新型工艺。这些新的工艺方法在基于传统工艺的基础上根据基体的物理性质、化学性质以及形状或表面特性等的不同,加以改进,形成适用性更广的沉积工艺,如微波等离子体CVD法(在750℃硅衬底沉积纳米金刚石膜)、热丝化学气相沉积法(可制备厚度达3μm的球面金刚石膜)、直流电弧等离子体喷射法(在钼Mo衬底上成功制备出厚度大于500μm的球面金刚石厚膜)。
在硬质合金球上沉积纳米金刚石涂层的意义在于其可以有效地减少机械设备中零部件的磨损,这也是导致一些机械零件失效的直接原因。随着科学技术的不断发展,一些机械设备的工作环境要求也不断变得严苛,如超高温或超低温、高载荷以及真空度高等都给机械设备带来了极大的难题。若仅仅依靠传统的润滑油脂已经难以满足如今的润滑需求,这就使得固体润滑剂得到了较大的发展空间。固体润滑材料一般可分为固体粉末润滑剂、固体润滑膜以及自润滑复合材料三类。如今已经成功投入生产的固体润滑膜已有二硒化钨(WSe2)、氮化硼(BN)、二硫化钼(MoS2)、金(Au)、银(Ag)、铅(Pb)等,而纳米金刚石薄膜就属于固体润滑膜中的一种,其所具有的高硬度、低摩擦系数、良好的化学稳定性、高热导率以及高弹性模量使其具有广阔的应用前景。
此外,纳米金刚石固体润滑膜还可应用于一些制药机械的轴承滚珠,目前这些轴承滚珠大多采用氮化硅(SiN)等陶瓷材料,这会使得成本偏高且耐磨性及弹性模量等性能有所欠缺。而如果直接采用价格相对较低的硬质合金球,虽然在一定程度上降低了生产成本,但是硬质合金球的组成成分中含有钨W、钴Co等重金属元素,若发生磨损这些重金属元素会渗入污染药品,危害了服用者的健康。因此,纳米金刚石固体薄膜的沉积一方面提升了轴承球的硬度、耐磨性能以及使用寿命,另一方面纳米金刚石膜层磨损后渗入的小部分碳粉对人体危害极小,几乎可忽略不计。
硬质合金供应商:中钨在线科技有限公司 | 产品详情: http://www.tungsten-carbide.com.cn |
电话:0592-5129696 传真:5129797 | 电子邮件:sales@chinatungsten.com |
钨钼文库:http://i.chinatungsten.com | 钨钼图片: http://image.chinatungsten.com |
钨新闻3G版:http://3g.chinatungsten.com | 钼业新闻: http://news.molybdenum.com.cn |


液膜法和仲钨酸铵生产
- 详细资料
- 分类:钨业知识
- 发布于 2016年1月27日 星期三 18:49
- 作者:xinyi
- 点击数:690
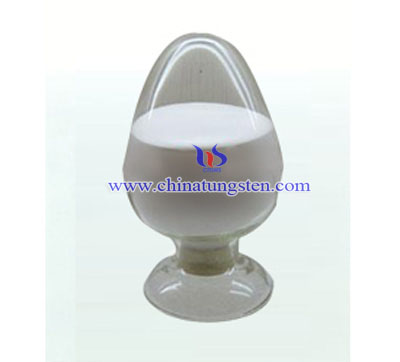
钨产品供应商:中钨在线科技有限公司 | 产品详情: http://cn.chinatungsten.com |
电话:0592-5129696 传真:5129797 | 电子邮件:sales@chinatungsten.com |
钨钼文库:http://i.chinatungsten.com | 钨钼图片: http://image.chinatungsten.com |
钨新闻3G版:http://3g.chinatungsten.com | 钼业新闻: http://news.molybdenum.com.cn |


含钨物料制备仲钨酸铵
- 详细资料
- 分类:钨业知识
- 发布于 2016年1月27日 星期三 16:52
- 作者:chunyan
- 点击数:679
本文提供一种既能处理白钨精矿、高钙黑钨精矿及尾矿,又能处理钨细泥及难选低品位钨矿,同时能提高钨的回收率、降低碱耗量,制取仲钨酸铵的方法。
具体步骤为:
1. 湿磨:使98%以上含钨物料颗粒达到50μm;
2. 溶解:按原料的性质,含杂质量的高低,在进料的同时,加入料重1~20%的铝氧化物或铝盐,目的是使浸出钨的同时将大部分的P、As、Si留在渣中;按原料中含钙量的高低,在进料时还应加入料重1~20%的磷的氧化物或磷酸盐,使钙生成CaPO4进入渣中,钨转化成可溶性钨酸盐进入溶液,浸出温度控制在100℃以上,浸出剂含NaOH为350~550g/L,液固比为1∶0.8~1,浸出时间为1.5~4小时,气压大于0.1MPa。
3. 分解后的物料经稀释过滤,洗涤3~4次,滤液澄清,蒸发结晶、过滤,得到工业用钨酸钠产品;过滤后剩下的母液补充碱后,可以继续作为浸出剂使用。
4. 离子交换:将所得的钨酸钠结晶溶解后,再过滤、稀释、澄清;也可直接将步骤3没有结晶的澄清液进行离子交换,只是耗碱量更大;
5. 除钼:加入含硫为80~150g/L的(NH4)2S溶液理论量的4~5倍,用以络合钼保留在结晶母液中;
6. 浓缩结晶,制得仲钨酸铵晶体。为深度净化除去Mo、As、P、Si等杂质,再用含NH4NO3或NH4Cl为2~4%的溶液在30~50℃下进行3~4次淋洗,洗涤、烘干。
仲钨酸铵供应商:中钨在线科技有限公司 | 产品详情: ammonium-paratungstate.com |
电话:0592-5129696 传真:5129797 | 电子邮件:sales@chinatungsten.com |
钨钼文库:http://i.chinatungsten.com | 钨钼图片: http://image.chinatungsten.com |
钨新闻3G版:http://3g.chinatungsten.com | 钼业新闻: http://news.molybdenum.com.cn |

