氧化镨(Pr6O11)掺杂三氧化钨陶瓷1/3
- 详细资料
- 分类:钨业知识
- 发布于 2015年12月22日 星期二 17:30
- 作者:huahuo
- 点击数:738
三氧化钨(WO3)陶瓷与氧化锡(SnO2)系陶瓷都是金属陶瓷,不仅具有金属陶瓷硬度高、耐磨、耐高温、耐腐蚀等特性,且都具有电学性能中的压敏特性,但两者形成压敏特性的机理不同,也因此采用掺杂多种稀土元素来提高压敏特性及电学稳定性时,SnO2系陶瓷性能得到改善,WO3陶瓷无明显作用。陶瓷掺杂Sb、Co和 Pr等过渡金属元素能使其压敏特性和烧结得到显著改善,Pr系压敏陶瓷相比传统的Bi系压敏陶瓷在微结构以及化学组成上具有较大的优势,而且具有更好的电学稳定性。采用Pr6O11掺杂三氧化钨陶瓷,并分析掺杂Pr6O11对三氧化钨微观结构、烧结性能以及电化学性能的影响。
掺杂Pr6O11影响WO3 陶瓷微观结构。WO3陶瓷的晶粒大小随着烧结温度与掺杂浓度增加而增大并气孔减少,呈现致密化结构。同时WO3陶瓷的形貌随着烧结温度变化发生明显的变化,当烧结温度在950℃左右时,表面颗粒会出现大小不均匀的现象;当结烧温度增加时,表面颗大小逐渐向均匀发展;当烧结温度达到1100℃以后,烧结时间与温度增加均能促进WO3陶瓷晶粒生长,由此可判断出1100℃为最佳烧结温度。Pr6O11的熔点为935℃左右,在低温情况下Pr6O11无法形成液相保留在晶界,对陶瓷的致密性起不到影响,所以当WO3陶瓷烧结温度为950℃时,才会出现表面颗粒会出现大小不均匀的现象。掺杂Pr6O11能改善WO3陶瓷的致密性与表面形貌。
氧化钨供应商:中钨在线科技有限公司 | 产品详情: http://www.tungsten-oxide.com |
电话:0592-5129696 传真:5129797 | 电子邮件:sales@chinatungsten.com |
钨钼文库:http://i.chinatungsten.com | 钨钼图片: http://image.chinatungsten.com |
钨新闻3G版:http://3g.chinatungsten.com | 钼业新闻: http://news.molybdenum.com.cn |
微信:

微博:

钨铜电极金相及性能分析
- 详细资料
- 分类:钨业知识
- 发布于 2015年12月22日 星期二 16:49
- 作者:xiaobin
- 点击数:742
钨铜粉末烧结材料其形态分布为以钨为骨架均匀分布在铜基体上。由于钨W的高熔点和高硬度的特性,钨在1000℃下,其极限抗拉强度仍有50kgf/mm2,比常温下的低碳钢强度还要高,这就使得钨铜材料在铜熔点温度以下(约1000℃左右),仍具有极高的抗磨损性和热硬性。而钨骨架以铜为基体粘为一体,并且构成了烧结材料的良好导体和散热的通路,从而使得钨骨架在使用的过程中不会产生局部过热的现象。
常用金属的室温强度主要决定于两个基本因素,即金属原子结合力以及对位错运动阻力。在钨铜材料作为电阻焊电极时常采用增加对位错运动阻力的方法来提高强度,包括冷作硬化和拆出强化等方法。但是,这些方法所得到的强化效果会随着钨铜合金的温度升高而显著降低,最终消失。举个例子,冷作硬化后的紫铜电极,室温下硬度可达到HB100-110,然而当温度升高至200-250℃时,这种冷作硬化效应会全部消失。此外,大多数靠沉淀相析出强化的铜合金,在温度达到500-650℃时,由于沉淀相重新融入基体,而使得强度迅速降低。相比之下,铜钨粉末烧结材料在高温下不会发生相变,再结晶或重结晶等现象。一些对钨铜材料研究数据表明,钨铜W-30Cu的硬度和电导率高于铍铜,软化温度则为铍铜的两倍以上。因此,以钨铜材料来作为闪光对焊或弧焊用的电极,尤其是连续在高温下作业的情况下,对导电性以及耐磨性要求较高的场合,更能凸显钨铜电极材料的优越性。
钨铜合金供应商:中钨在线科技有限公司 | 产品详情: http://www.tungsten-copper.com |
电话:0592-5129696 传真:5129797 | 电子邮件:sales@chinatungsten.com |
钨钼文库:http://i.chinatungsten.com | 钨钼图片: http://image.chinatungsten.com |
钨新闻3G版:http://3g.chinatungsten.com | 钼业新闻: http://news.molybdenum.com.cn |
微信:

微博:

钨合金飞轮配重
- 详细资料
- 分类:钨业知识
- 发布于 2015年12月22日 星期二 13:41
- 作者:yaqing
- 点击数:803
飞轮是转动惯量很大的盘形零件主要用于大型机械的零部件或装置,其作用如同一个能量存储器。对于AP1000三代核电主泵电机来说,由于它是一种世界先进的立式单级、整体密封式、高惯量、离心的屏蔽电机,所以主泵的电气、水力和惰转性能至关重要。但是如果在没有电源的情况下,惰转将不能正常进行,也就无法保证反应堆的安全。而在主泵电机上设置飞轮则可以提供大转动惯量从而提高惰转时间,保证反应堆的安全。
这种高惯量飞轮为重金属钨合金镶嵌结构,由内轮毂、12块重金属钨合金插件、保持环、上下盖板以及外套组成。由于转速慢的偏心造成的偏载会小一些,但是像飞轮这样转速高的则一定要加配重块以保持其平衡性。将钨合金块安装到飞轮的轮毂上将其固定即可达到为飞轮配重从而保持其在高转速下亦能平衡的目的。这是由于钨合金具有较高的密度和较好的耐磨损性,高密度使其能很好地用于保持飞轮转动时的平衡;当飞轮在高速运转的情况产生较大的摩擦力,钨合金则可以很好地克服这一点不至于被磨损消耗。
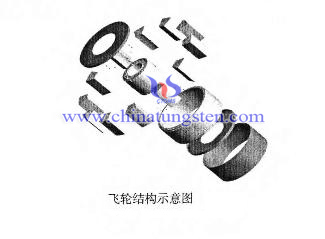
高比重合金供应商:中钨在线科技有限公司 | 产品详情: http://www.tungsten-alloy.com |
电话:0592-5129696 传真:5129797 | 电子邮件:sales@chinatungsten.com |
钨钼文库:http://i.chinatungsten.com | 钨钼图片: http://image.chinatungsten.com |
钨新闻3G版:http://3g.chinatungsten.com | 钼业新闻: http://news.molybdenum.com.cn |
微信:

微博:

APT杂质行为分析
- 详细资料
- 分类:钨业知识
- 发布于 2015年12月22日 星期二 13:51
- 作者:xinyi
- 点击数:778
APT工艺的现代方法是使用高纯APT取代钨酸,借助于钨酸铵溶液的热不稳定性,溶剂中氨易于气化的特点,用快速加热、剧烈搅拌的方法,使溶剂与溶质间的平衡发生破坏,呈过饱和状态,APT从钨酸铵溶液中经成核,晶体生长而结晶出来。
据文献研究指出,钨酸铵溶液存在的杂质P、As、SiO2、Na、Mg、Ca、Fe、Mo等在ATP结晶过程中的行为取决于它们与仲钨酸盐的相互作用特性及其所形成的化合物的溶解度,杂多酸型可溶性杂质(NH4)3PW12O40;(NH4)3AsW12O40;(NH4)3SiW12O40在仲盐结晶过程中实际上完全留在母液中,最高可达1kg/L以上,而在仲盐中的含量不超过0.005%。
P、As、Si杂质会降低仲盐结晶率。其它杂质的净化效率Mo>Na>Mg>Ca>Fe,并取决于原始溶液中的浓度。
仲盐对杂质的净化效率除取决于它们在原始溶液中的浓度外,还取决于APT蒸发工艺。循环蒸发由于结晶器结垢等原因,最终产品不稳定。在槽罐中间接蒸发,股入空气搅拌,与同样槽罐密封真空状态下蒸发,杂质P、As、SiO2、Fe、Mo等在APT晶体中和母液中的分配相差很大(见表1),符合文献所指仲盐结晶过程中各种杂质的净化规律。
加晶种蒸发过程中定量补加AT溶液可避免生产复晶,除能得到均匀的APT具体外,可进一步净化杂质,提高APT纯度。将国外介绍的数据与株洲硬质合金厂黑钨精矿萃取新工艺加晶种蒸发结晶的数据相比,可以看出,株洲厂的工艺对产品进一步的提纯有一定的优点(见表2)。
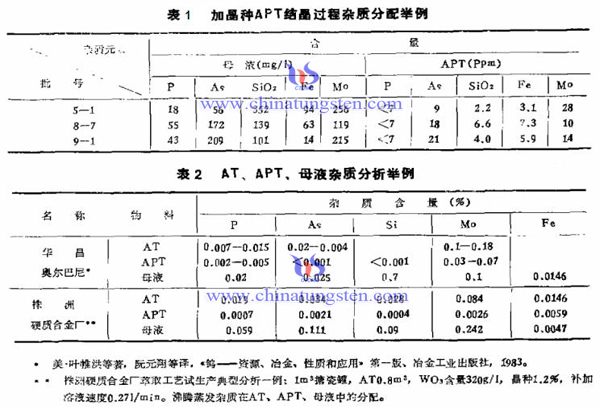
钨产品供应商:中钨在线科技有限公司 | 产品详情: http://cn.chinatungsten.com |
电话:0592-5129696 传真:5129797 | 电子邮件:sales@chinatungsten.com |
钨钼文库:http://i.chinatungsten.com | 钨钼图片: http://image.chinatungsten.com |
钨新闻3G版:http://3g.chinatungsten.com | 钼业新闻: http://news.molybdenum.com.cn |
微信:

微博:

液相烧结法制备钨合金配重件Ⅱ
- 详细资料
- 分类:钨业知识
- 发布于 2015年12月22日 星期二 13:34
- 作者:yaqing
- 点击数:865
烧结的目的是把粉状材料转变为块体材料,并赋予材料特有的性能。液相烧结钨合金配重件时主要分为三个阶段:1、液相生成与颗粒重排阶段。2、溶解-析出阶段;3、固相骨架形成与晶粒长大阶段。而经过液相烧结后的两相合金,其密度与理论密度相近。这意味着用液相烧结法制备钨合金配重件可以很好地保留其原有的高密度特性,从而使得钨合金配重件能更好地应用于各个领域,发挥其效能。
1、液相生成与颗粒重排阶段
这是制备钨合金配重件时所需时间最短的一个阶段,在该阶段,镍、铁粉末会随着温度升高而产生液相,继而产生毛细管力,使得粉末发生快速的致密化。镍是制备钨合金配重件必不可少的元素,适量的镍(0.5%~12%)可以增加粉末间的粘性,使其更好地致密化。颗粒重排时的致密化程度则取决于液体数量、颗粒尺寸、固体在液体中的溶解度等等,如果液相数量足够(35%),压坯可完全致密。
2、溶解-析出阶段
经过重排阶段后致密化速度变慢,溶解和扩散效应则成为了该阶段的主导。小颗粒的粉末将优先溶解于液相之中,而随颗粒尺寸溶解的小颗粒通过扩散产生物质迁移而沉析在大颗粒的表面上,使得颗粒粗化长大,同时使得材料进一步致密化。
3、固相骨架形成与晶粒长大阶段
颗粒在经过液相生成与颗粒重排,溶解-析出阶段之后会互相靠拢,在颗粒接触表面同时产生固相烧结,形成牢固的固相骨架。但此阶段的烧结时间不宜过长。
钨合金通过液相烧结工艺可以使金属间达到全致密性,再根据具体需求制作出各类不同形状的配重件,这些配重件都具有高密度、高导电导热以及耐腐蚀抗氧化等等优异的特性,使得其成为许多需要配重产品领域的首选。
高比重合金供应商:中钨在线科技有限公司 | 产品详情: http://www.tungsten-alloy.com |
电话:0592-5129696 传真:5129797 | 电子邮件:sales@chinatungsten.com |
钨钼文库:http://i.chinatungsten.com | 钨钼图片: http://image.chinatungsten.com |
钨新闻3G版:http://3g.chinatungsten.com | 钼业新闻: http://news.molybdenum.com.cn |
微信:

微博:
