挤压成形影响因素-挤压嘴直径
- 詳細
- カテゴリ: 钨业知识
- 2017年4月25日(火曜)15:23に公開
- 作者: ruibin
- 参照数: 2065
挤压嘴直径也称为出口自径或出门喇叭锥直径。模具出口直径d过小,则易划伤制品表面,甚至会引起堵模。但d过大,会大大削弱定径带的强度,引起定径带过早地变形、压蹋,明显地降低模具使用寿命。因此,在一般情况下,出口带尺寸应比定径带尺寸大,对于薄壁管或变外径管材的模具,其值可适当增大。为增大模具的强度和延长模具的使用寿命,出口带可做成喇叭锥。出口喇叭锥角(从挤压型材离开定径带开始)可取 (此值受锥刀角度的限制)。特别是对于壁厚小于 而外形十分复杂的型材模具,为了保证模具的强度,必须做成喇叭出口。有时为了便于加工,也可设计成阶梯形的多级喇叭锥。为了增大定径带的抗剪强度,定径带与出口带之间可以20°-45°的斜面以圆角半径为1.5-3.0mm的圆弧连接。
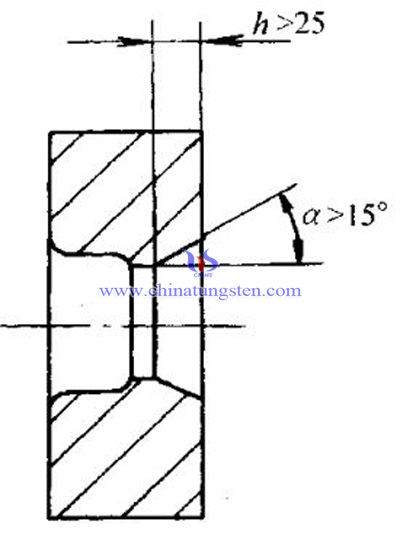
挤压嘴直径通常根据挤压时的收缩系数确定。对于确定的挤压机,所能挤出坯条的最大直径受挤压机的能力限制,确切地说,受挤压缸径和压力的限制。挤出坯条的最大直径可按下式计算
d=√((1-k) D^2 )
式中:d---挤压机所能挤出的最大坯条直径,mm;
k---挤压压缩率,一般取值≥0.95;
D---挤压缸直径,mm。
硬质合金供应商:中钨在线科技有限公司 | 产品详情: http://www.tungsten-carbide.com.cn |
电话:0592-5129696 传真:5129797 | 电子邮件:sales@chinatungsten.com |
钨钼文库:http://i.chinatungsten.com | 钨钼图片: http://image.chinatungsten.com |
钨新闻3G版:http://3g.chinatungsten.com | 钼业新闻: http://news.molybdenum.com.cn |
微博

微信

挤压成形影响因素-定径带
- 詳細
- カテゴリ: 钨业知识
- 2017年4月25日(火曜)15:15に公開
- 作者: ruibin
- 参照数: 2756
定径带有称定型带、工作带,是模具中垂直模具工作端面并用以保证挤压制品的形状、尺寸和表面质量的区段,下图中h即为定径带长度,α为模角.

定径带长度h过短,挤出阻力虽小,但会造成挤压速度快,弹性后效急剧释放,坯条容易产生摆动,制品尺寸难于稳定,易产生弯曲、变形、波纹、椭圆等废品,同时,模具易磨损,会大大降低模具的使用寿命;但h过长,会增大与金属的摩擦,增加挤压力,易粘结金属,使制品表面出现划伤、毛刺、麻面、搓衣板型波浪,同时由于附加内应力的增大而导致坯条纵向裂纹等缺陷。h应根据挤压机的结构(立式或卧式)、被挤压金属材料、产品的形状和尺寸等因素来确定。在立式挤压机上挤压管材时,一般2-6mm;挤压镁合金时,一般的最小值为1.5-33mm,最大值依产品的尺寸和形状确定。对于硬质合金混合料挤压工艺而言,定径带的长度一般按坯条直径的3-5倍选取,
即h=3-5d
式中:h-为定径带长度;
d-为挤压嘴直径;
挤压硬质合金混合料与挤压致密金属不同,h取值较大,以保证适当的坯条密度、减少物料的弹性膨胀、维持坯条的形状。
硬质合金供应商:中钨在线科技有限公司 | 产品详情: http://www.tungsten-carbide.com.cn |
电话:0592-5129696 传真:5129797 | 电子邮件:sales@chinatungsten.com |
钨钼文库:http://i.chinatungsten.com | 钨钼图片: http://image.chinatungsten.com |
钨新闻3G版:http://3g.chinatungsten.com | 钼业新闻: http://news.molybdenum.com.cn |
微博

微信

挤压温度对挤压力的影响
- 詳細
- カテゴリ: 钨业知识
- 2017年4月25日(火曜)15:09に公開
- 作者: ruibin
- 参照数: 2128
挤压温度对挤压力的影响:挤压温度对挤压力的影响,是通过变形抗力的大小反映出来的。下图为不同温度下几种铜合金挤压时挤压力的影响规律。一般来讲,随着变形温度的升高,锭坯的变形抗力下降,所需的挤压力也下降。实际上,大多数金属与合金的变形抗力随温度升高而下降的关系,不能保持上述的严格线性关系,所以挤压力与温度的关系也一般为非线性关系。
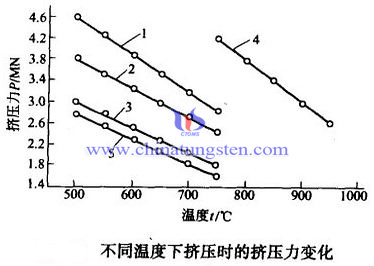
挤压物料的塑性受温度的影响。大多数的增塑剂的粘性会随温度的升高而下降。如在20℃时,石蜡的粘度为26.1x1010Pa.S,而在熔点附近时(45℃左右),石蜡的粘度只有0.8x1010Pa.S。随着挤压温度的升高,增塑剂的塑形变好。温度太低时,所需的挤压压力太大,容易造成横向断裂或分层,挤压温度太高,挤压压力急剧下降,造成坯条软化变形,难于挤压坯的形状也容易产生断裂。一般来说,增塑剂加量较多时,坯条尺寸较大时,应该采用较低的挤压温度。随着温度的升高,金属或合金的变形阻力降低,塑性提高。利用此特性,将金属粉末或压坯加热通过模具进行挤压成形的过程称为粉末热挤。挤出的坯件尺寸及形状完全由模具嘴的尺寸或型腔来控制。按挤压金属特性和挤压零件形状,热挤法可分成非包套热挤和包套热挤两种形式。
硬质合金供应商:中钨在线科技有限公司 | 产品详情: http://www.tungsten-carbide.com.cn |
电话:0592-5129696 传真:5129797 | 电子邮件:sales@chinatungsten.com |
钨钼文库:http://i.chinatungsten.com | 钨钼图片: http://image.chinatungsten.com |
钨新闻3G版:http://3g.chinatungsten.com | 钼业新闻: http://news.molybdenum.com.cn |
微博

微信

挤压成形影响因素-模角
- 詳細
- カテゴリ: 钨业知识
- 2017年4月25日(火曜)15:13に公開
- 作者: ruibin
- 参照数: 2408
挤压模具的模孔形状主要是指模角大小、定型带长度、挤压嘴直径这三部分,它们对挤压过程,特别是挤压压力都会不同程度的影响。其中模角大小是非常重要的挤压模具参数,它对挤压力的大小、挤压成形质量影响重大。
模角是指模面与挤压轴线的夹角。模角对挤压力也有明显影响。模角α由0°改变到90°之间,在45°-60°范围内挤压力最小。 挤压模角对挤压力的影响:模角对挤压力的影响,主要表现在变形区及变形区锥表面,模角对挤压力有着明显的影响。挤压应力与模角的关系如下图所示。随着模角α逐渐增大,挤压力逐渐降低,模角继续增大时,挤压力呈升高趋势。另外,由下图也可以看出挤压力分量与模角之间的关系。在一定的变形条件下,随着模角的增大,变形区内所需的挤压力分量RM增加,这是由于粉末坯条流入和流出模孔时的附加弯曲变形增加之故。但用于克服挤出锥面上摩擦阻力的分量TM,由于摩擦面积的减小而下降。以上两个方面因素综合作用的结果,使Tm在某一模角下为最小,从而总的挤压力也为最小。模角视坯条的直径而定,坯条较大,模角α相应增大,坯条较小时,α可相应减小。模角角过小,物料容易流入定型带,坯条中心密度难以保证。模角过大,挤压力增大,毛坯产生分层等缺陷。
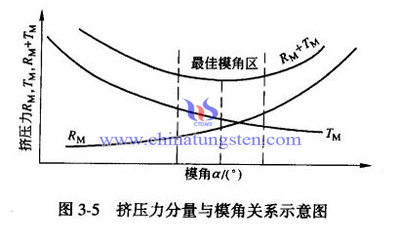
挤出锥角是挤压嘴中心剖面中两个对称模面的角度大小,其数值为模角的两倍,工业中也常以挤出锥角参数来代替模角参数。
硬质合金供应商:中钨在线科技有限公司 | 产品详情: http://www.tungsten-carbide.com.cn |
电话:0592-5129696 传真:5129797 | 电子邮件:sales@chinatungsten.com |
钨钼文库:http://i.chinatungsten.com | 钨钼图片: http://image.chinatungsten.com |
钨新闻3G版:http://3g.chinatungsten.com | 钼业新闻: http://news.molybdenum.com.cn |
微博

微信

变形抗力和变形程度对挤压力的影响
- 詳細
- カテゴリ: 钨业知识
- 2017年4月25日(火曜)15:07に公開
- 作者: ruibin
- 参照数: 2045
掌握影响挤压力的主要因素
影响挤压力的主要因素有:挤压时的金属变形抗力、变形程度、模孔形状、制品断面形状、流出速度、锭坯的长度、接触摩擦条件等。
(1) 挤压时的粉末变形抗力。挤压力与抵抗力成正比关系。(但由于粉末的不均匀性,往往不能保持严格的线性关系。)变形温度通过影响金属变形抗力而影响挤压力,随着温度的升高,挤压力降低。
(2) 变形程度。挤压力与之也是成正比关系,随着变形程度增大挤压力增加。下图为不同种类粉末在不同挤压比的条件下的挤压力对比。挤压比extrusion ratio)是指挤压筒腔的横断面面积同挤压制品总横断面面积之比,也叫挤压系数。挤压比是挤压生产中用于表示金属变形程度大小的参数,用λ表示:λ=Ft/ΣF1。挤压比同变形程度、挤压力有如下关系:(1)挤压比增大时,金属流出模孔的困难程度会增大,挤压力也增大;(2)当其他条件相同时,挤压比增大,挤压时锭坯外层金属向模孔流动的阻力也增大,因此使内外部金属流动速度差增大,变形不均匀;(3)但当挤压比增加到一定程度后,剪切变形深入到内部,变形开始向均匀方向转化。研究证明,当挤压变形程度ε达到85%~90%时,挤压金属流动均匀,制品内外层的力学性能也趋于均匀。从图中可以看出,抵抗力(粉末种类)与变形程度(挤压比)均会对挤压压力产生影响。
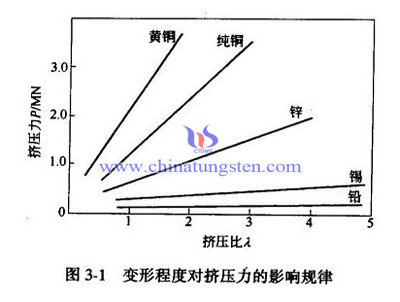
硬质合金供应商:中钨在线科技有限公司 | 产品详情: http://www.tungsten-carbide.com.cn |
电话:0592-5129696 传真:5129797 | 电子邮件:sales@chinatungsten.com |
钨钼文库:http://i.chinatungsten.com | 钨钼图片: http://image.chinatungsten.com |
钨新闻3G版:http://3g.chinatungsten.com | 钼业新闻: http://news.molybdenum.com.cn |
微博

微信
