注射硬质合金孔洞
- 詳細
- カテゴリ: 钨业知识
- 2017年5月11日(木曜)18:17に公開
- 作者: ruibin
- 参照数: 1840
表面缺陷硬质合金
定义:孔洞是指在生坯或制品的横截面上发现的孔隙。严重时可贯通生坯。孔洞发展到一定程度可贯穿坯体。注射成形坯孔洞可分为两种:中心缩孔和蜂窝状气孔。缩孔具体可参见下图。
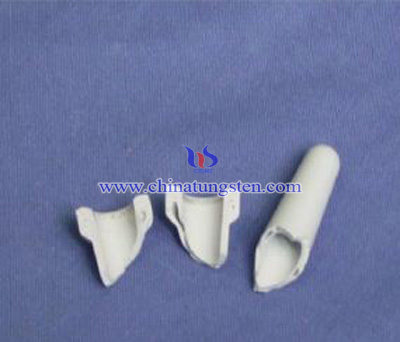
孔洞产生原因和改善措施
注射成型硬质合金的缩孔产生原因主要是当注射温度过高时,粘结剂发生较大膨胀(石蜡由固相转变为液相的体积膨胀率为 11%~20%) ,使其所占体积分数增大,喂料的装载量减小,充模后注射坯冷却时粘结剂发生较大收缩导致中心缩孔的产生。解决方法主要是使注射温度保持在较低温度。窝状气孔主要是由于在充模过程中模腔中的气体无法及时排出,夹杂在注射坯中而形成的,当注射时料温过低时,导致喂料粘度过大,喂料充模排气性变差,另外由于注射速度过快导致喂料中气体无法及时排出。通过调整注射速度与注射温度的匹配度消除了蜂窝状气孔。
总结来说,形成孔洞的因素有:
a) 注射时夹入气体、混炼时喂料不均、喂料夹有气体、不良充模均会引发;
b) 粉末同粘结剂分离;
c) 模温和料温不匹配;
d) 保压压力过小, 保压时间不足;
e) 喷射(解决办法: 改进模具设计, 使充模过程中喂料能以柱塞式运动; 降低模温或注射温度; 降低注射速度)。
硬质合金供应商:中钨在线科技有限公司 | 产品详情: http://www.tungsten-carbide.com.cn |
电话:0592-5129696 传真:5129797 | 电子邮件:sales@chinatungsten.com |
钨钼文库:http://i.chinatungsten.com | 钨钼图片: http://image.chinatungsten.com |
钨新闻3G版:http://3g.chinatungsten.com | 钼业新闻: http://news.molybdenum.com.cn |
微博

微信

注射成型缺陷-夹心
- 詳細
- カテゴリ: 钨业知识
- 2017年5月11日(木曜)18:12に公開
- 作者: ruibin
- 参照数: 2039
定义
夹心:夹心是指注射坯内外层冷却速率不同而造成先冷却的外部与后冷却的内部收缩率不一致。夹心现象就是在生坯破损断面上颜色不一, 像洋葱状, 内部颜色浅、外部颜色深的现象。颜色差异越大, 则夹心现象越严重。具体可参照下图。
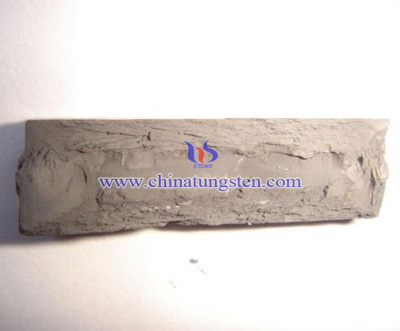
原因
1、充模过程中模温与料温差过大,料的外部接触到冷模迅速冷却而内部却保持柔软, 内外收缩不一造成的。
2、在充模时保压压力会将另一部分料压入坯中, 这同先入模的料在温度和收缩上不一致。
产生夹心表明注射坯内存在很大的内应力,这部分内应力是导致后续溶剂脱脂过程中坯体开裂的主要原因之一。通过缩小模/ 料温温度差异可使夹心程度降至最
低。
改善措施
1) 提高热导率,具体来说,根据热导率的傅里叶定律dQ=-λdA•dt/dn
可知,提高热导率可通过提高导热面积A和导热系数λ来实现。要提高充模和脱脂过程中硬质合金粉末相互之间的导热面积就必须提高熔料的粉末装载率;而要提高导热系数就必须增加熔料中流动态组分的比例。前者需要提高装载量(降低流动态组分比例),后者需提高流动态比例,这就需要在混合料体系中加入适量的分散剂(即表面活性剂)来实现,通过加入分散剂,既可改善导热情况,也能改善整体的流动性。
2)减小注射温度, 升高模温。降低温度不均匀,改善收缩不均的情况。
硬质合金供应商:中钨在线科技有限公司 | 产品详情: http://www.tungsten-carbide.com.cn |
电话:0592-5129696 传真:5129797 | 电子邮件:sales@chinatungsten.com |
钨钼文库:http://i.chinatungsten.com | 钨钼图片: http://image.chinatungsten.com |
钨新闻3G版:http://3g.chinatungsten.com | 钼业新闻: http://news.molybdenum.com.cn |
微博

微信

注射成型缺陷-欠注
- 詳細
- カテゴリ: 钨业知识
- 2017年5月10日(水曜)19:56に公開
- 作者: ruibin
- 参照数: 2137
定义
欠注又叫短射、充填不足、制件不满,俗称欠注(如下图所示),指物料末端出现部分不完整现象或一模多腔中一部分填充不满,特别是薄壁区或流动路径的末端区域。主要是因为熔料在没有充满型腔就冷凝了,熔料进入型受腔后没有充填完全,导致产品缺料。
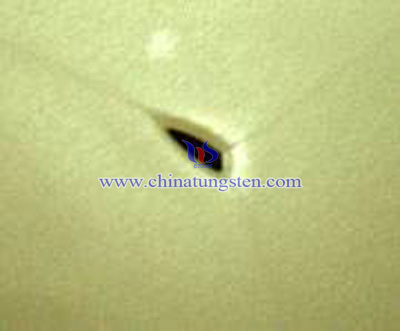
原因:
1) 料温或模温过低,通常,在适合成型的范围内,料温与充模长度接近于正比例关系,低温熔料的流动性能下降,使得充模长度减短。
2) 加料量不足,目前常用的控制加料的办法是定体积加料法,
3) 喂料粘度过大, 一般升高喂料温度则可解决此问题;
4) 料流动性差,因此应改善模具浇注系统的滞流缺陷,如合理设置浇道位置,扩大浇口,流道和注料口尺寸,以及采用较大的喷嘴等。
5)注射压力或保压不足,注射压力与充模长度接近于正比例关系,注射压力太小,充模长度短,型腔填充不满。
6)注射速度太慢,注射速度与充模速度直接相关。如果注射速度太慢,熔料充模缓慢,而低速流动的熔体很容易冷却,使其流动性能进一步下降产生欠注。
7)浇注系统设计不合理。实际生产中往往因浇口和浇道平衡设计不合理导致塑件外观缺陷。设计浇注系统时,要注意浇口平衡,各型腔内塑件的重量要与浇口大小成正比,使各型腔能同时充满,浇口位置要选择在厚壁处,也可采用分流道平衡布置的设计方案。若浇口或流道小,薄,长,熔料的压力在流动过程中沿程损失太大,流动受阻,容易产生填充不良。对此应扩大流道截面和浇口面积,必要时可采用多点进料的方法。
硬质合金供应商:中钨在线科技有限公司 | 产品详情: http://www.tungsten-carbide.com.cn |
电话:0592-5129696 传真:5129797 | 电子邮件:sales@chinatungsten.com |
钨钼文库:http://i.chinatungsten.com | 钨钼图片: http://image.chinatungsten.com |
钨新闻3G版:http://3g.chinatungsten.com | 钼业新闻: http://news.molybdenum.com.cn |
微博

微信

注射成型硬质合金表面缺陷
- 詳細
- カテゴリ: 钨业知识
- 2017年5月11日(木曜)18:06に公開
- 作者: ruibin
- 参照数: 2082
硬质合金粉末具有较高硬度、耐磨性、抗变形能力等性能,这些特点使其在注射成型过程中需要更细化的工艺选择。通过控制注射参数可在一定范围内控制注射坯的质量。如果注射参数匹配不当,则会产生各种缺陷。同时因硬质合金的力学性能对于极小的杂质、孔洞或其它小缺陷引起的断裂源都特别敏感,故研究工艺中各工序可能产生的缺陷及其原因,提出预防措施和解决办法,就显得至关重要。在这其中表面缺陷占据了很大的缺陷比重,常见的表面缺陷有两种:表面凹陷和表面流动纹。这两种表面缺陷,通常是由原料和注射工艺控制不当造成的。
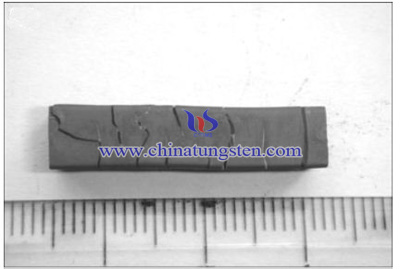
表面凹陷产生原因及改善措施
具体的硬质合金注射生坯表面凹陷如上图1所示。引起注射硬质合金生坯表面凹陷的原因
a) 冷流动, 即喂料在未充模腔之前, 最先入模的一部分料就已开始凝固的充模行为。可升高模温或用流动性更好的粘结剂来消除;
b)粉末和粘结剂分离,这是混炼时温度过高或注射温度过高, 粘度太低引起的;可适当降低注射加热温度;
c) 模温料温不匹配,引起局部的热收缩进而导致表面凹陷;可通过适当加热模具予以消除;
d)保压压力小且保压时间短,导致局部为充实压紧。可增大保压压力和保压时间予以消除。
表面流动纹产生原因及改善措施
注射坯表面出现的波浪状层纹即为表面流动纹,具体可参照下图2.原因在于此时的喂料粘度大,流动性差,与模壁之间的摩擦增大。喂料和模壁间的摩擦还取决于模具的加工精度,模腔表面光洁度越高出现流动纹的几率越小。实际注射过程中,在合适的注射温度下,通过适当提高注射速度和增大注射压力能很好地消除此类缺陷。
硬质合金供应商:中钨在线科技有限公司 | 产品详情: http://www.tungsten-carbide.com.cn |
电话:0592-5129696 传真:5129797 | 电子邮件:sales@chinatungsten.com |
钨钼文库:http://i.chinatungsten.com | 钨钼图片: http://image.chinatungsten.com |
钨新闻3G版:http://3g.chinatungsten.com | 钼业新闻: http://news.molybdenum.com.cn |
微博

微信

混炼与制粒质量控制
- 詳細
- カテゴリ: 钨业知识
- 2017年5月10日(水曜)19:53に公開
- 作者: ruibin
- 参照数: 1971
混炼过程需严格控制, 因为这一步骤产生的缺陷, 在以后的步骤中无法弥补并且会引发许多新的缺陷.对于硬质合金在混炼时, 因硬质合金粉末不规则、颗粒细, 须延长混料时间。若是亚微米粉末, 颗粒间的作用力较大, 可能产生团聚。为获得均匀喂料, 须加入极性分子粘结剂如乙烯—醋酸乙烯共聚物等, 以减少颗粒团聚和粉末间摩擦, 从而在尽可能短时间内获得均匀喂料。若因粉末粒度分布不佳导致的粉末颗粒因粒度不同而产生的偏聚, 可采用粘度较高的粘结剂,如高密聚乙烯等。混炼时温度过低,喂料的粘度就会增大, 导致喂料和混料器之间的磨损而带入异物, 且会在喂料中间夹入空气而引发后续缺陷(下图混炼设备)。
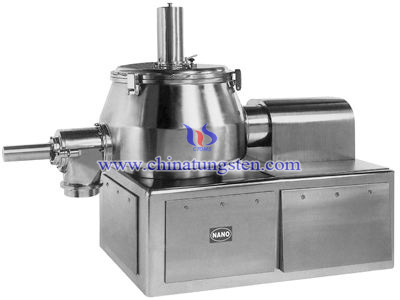
混炼温度
混炼温度太低, 喂料粘度过大, 容易引入异物, 同时会导致搅拌挤压不充分、不均匀,喂料中夹入过多气体, 带入注射生坯中产生孔隙;混炼温度过高则会恶化粘结剂性能和导致粉末同粘结剂分离;
混炼机转速
混炼机转速太快而产生的高剪切力将导致磨损引入杂质, 转速太低则不能产生足够的剪切力粉碎合金粉末团粒、不能使粘结剂的粘度适当降低。上述条件若控制不当, 都不能达到混炼均匀的效果, 从而在以后的工序中引发新的缺陷。
制粒控制
用于注射成型的物料经混炼后一般需进行制粒。制粒有两个目的:1、得到便于储存和运输的颗粒,方便注射时的加料;2、便于回收料的循环利用。通常采用切割法制粒。制粒过程中,气孔是最主要的缺陷,挤压切割制粒时可以负压甚至是真空操作,这样就可以有效减少气孔的产生。
硬质合金供应商:中钨在线科技有限公司 | 产品详情: http://www.tungsten-carbide.com.cn |
电话:0592-5129696 传真:5129797 | 电子邮件:sales@chinatungsten.com |
钨钼文库:http://i.chinatungsten.com | 钨钼图片: http://image.chinatungsten.com |
钨新闻3G版:http://3g.chinatungsten.com | 钼业新闻: http://news.molybdenum.com.cn |
微博

微信
