粉末注射成形粘结剂要求
- 詳細
- カテゴリ: 钨业知识
- 2017年4月26日(水曜)18:11に公開
有机粘结剂的作用是粘结金属粉末颗粒,使混合料在注射机料筒中加热后具有流变性和润滑性,还要具有一定的塑形能力,即粘结剂是带动粉末流动和维持粉末形状的载体。因此,粘结剂的选择是整个粉末注射成型的关键。对有机粘结剂的要求为:
1、用量少,用较少的粘结剂能使混合料产生较好的流变性;
2、不反应,在去除粘结剂的过程中与金属粉末不起任何化学反应;
3、易去除,在制品内不残留碳。
4、粘度较低,但不能过低,过低容易导致两相分离。常加入表面活性剂,阻止在混料和注射过程中发生两相分离。
5、脱脂过程易于排除,且不易形成脱脂缺陷。
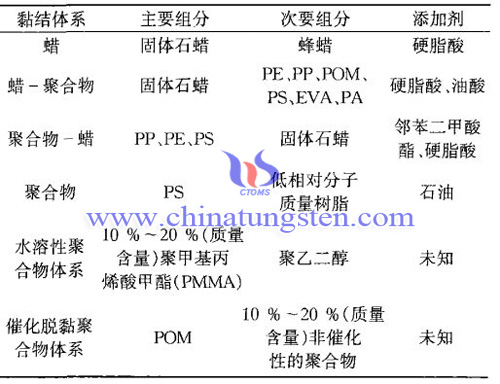
在PIM中,粘结剂增强流动是其本质的功能,它使PIM具有了本身独有的优点与特点:
(1)粘结剂的加入增强了粉末的流动性,使得粉末在注射压力下能充填复杂形状的模腔;
(2)粉末的流动性增强后,在充填模控过 程中,其压力梯度减小,密度分布就会更均匀,这对最终产品的组织均匀性有利;
(3)坯块的结构及密度均匀,使以后的脱脂和烧结过程中收缩也均匀,这样不但有利于保持坯块的复杂几何形状,也有利于尺寸公差的控制,这是制备形状复杂、少切削零件的关键;
(4)组织均匀为PIM产品具有较高性能提供了良好基础。此外增强粉末流动性,还能降低注射压力,减少磨损,延长模具及其他设备的使用寿命等。
维持形状是粘结剂另一项重要功能,它使PIM工艺得以顺利进行:
(1)坯块从模腔中脱出后,粘结剂使之具有一定强度,保持一定形状,便于转移搬运操作等;
(2)良好的保形性可以避免成形时的一些缺陷,如裂纹、掉角等,这对于提高产品成品率尤为重要;
(3)在脱脂时使坯块不致变形,既不使粘结剂中低熔点组元因过早软化而导致坯块塌陷,也不因气体排出过多、过快而使坯块裂开。粘结剂肩负着这两项重要的功能,也就决定了它在PIM中举足轻重的地位。
硬质合金供应商:中钨在线科技有限公司 | 产品详情: http://www.tungsten-carbide.com.cn |
电话:0592-5129696 传真:5129797 | 电子邮件:sales@chinatungsten.com |
钨钼文库:http://i.chinatungsten.com | 钨钼图片: http://image.chinatungsten.com |
钨新闻3G版:http://3g.chinatungsten.com | 钼业新闻: http://news.molybdenum.com.cn |
微博

微信

注射成形粘结剂种类
- 詳細
- カテゴリ: 钨业知识
- 2017年4月26日(水曜)18:10に公開
注射成形粘结剂都为有机粘结剂,是PIM技术的灵魂,其加入与脱除是PIM的关键技术。一部PIM发展史也就是粘结剂的设计、加入和脱除技术的革新史。
在PIM中,粘结剂具有两个最基本的功能:增强流动与维持形状.同时它还应具有易于脱除、无污染、无毒性、成本合理等特点。
通常采用的粘结剂主要有三种:石蜡基、油基和热塑性聚合物)、凝胶体系、热固性体系和水溶性体系。
热塑性体系:热塑性体系是以具有热塑性的有机化合物为主的粘结剂。在注射过程中,喂料被加热塑化,注射到冷模中后又凝固成具有一定强度的生坯。常见的有如聚乙烯,聚丙烯、聚苯乙烯等。热塑性体系是MIM粘结剂的主流与先导。热塑性粘结剂由于使用较多聚合物,成形坯强度高,但较多的聚合物会导致脱脂慢、装载量低。
热固性体系
热固性体系采用热固性有机化合物作为粘结剂的主要组分。喂料注入热模中发生缩合反应而固化。一般认为热固性树脂不适合于MIM,主要因为其缩合副产物通常是气体,常导致零件中出现气孔,而且热固性树脂粘度低且对温度敏感,使粉末的混合困难。
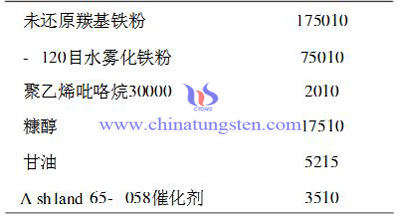
水溶性体系:是从“固态聚合物溶液”(SPS)体系中发展起来的,用水溶性聚乙二醇(PEG)作主要成分,加部分PMMA或苯氧树脂作粘结剂。
粉末注射成形粘结剂要求
- 詳細
- カテゴリ: 钨业知识
- 2017年4月26日(水曜)18:06に公開
有机粘结剂的作用是粘结金属粉末颗粒,使混合料在注射机料筒中加热后具有流变性和润滑性,还要具有一定的塑形能力,即粘结剂是带动粉末流动和维持粉末形状的载体。因此,粘结剂的选择是整个粉末注射成型的关键。对有机粘结剂的要求为:
1、用量少,用较少的粘结剂能使混合料产生较好的流变性;
2、不反应,在去除粘结剂的过程中与金属粉末不起任何化学反应;
3、易去除,在制品内不残留碳。
4、粘度较低,但不能过低,过低容易导致两相分离。常加入表面活性剂,阻止在混料和注射过程中发生两相分离。
5、脱脂过程易于排除,且不易形成脱脂缺陷。
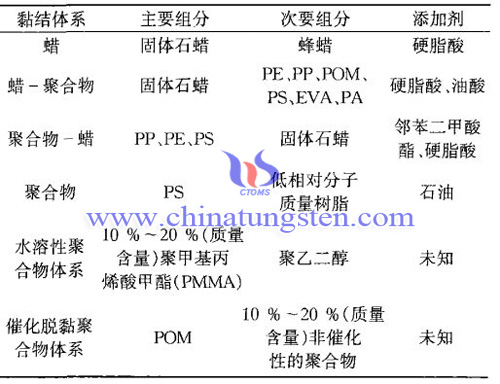
在PIM中,粘结剂增强流动是其本质的功能,它使PIM具有了本身独有的优点与特点:
(1)粘结剂的加入增强了粉末的流动性,使得粉末在注射压力下能充填复杂形状的模腔;
(2)粉末的流动性增强后,在充填模控过 程中,其压力梯度减小,密度分布就会更均匀,这对最终产品的组织均匀性有利;
(3)坯块的结构及密度均匀,使以后的脱脂和烧结过程中收缩也均匀,这样不但有利于保持坯块的复杂几何形状,也有利于尺寸公差的控制,这是制备形状复杂、少切削零件的关键;
(4)组织均匀为PIM产品具有较高性能提供了良好基础。此外增强粉末流动性,还能降低注射压力,减少磨损,延长模具及其他设备的使用寿命等。
维持形状是粘结剂另一项重要功能,它使PIM工艺得以顺利进行:
(1)坯块从模腔中脱出后,粘结剂使之具有一定强度,保持一定形状,便于转移搬运操作等;
(2)良好的保形性可以避免成形时的一些缺陷,如裂纹、掉角等,这对于提高产品成品率尤为重要;
(3)在脱脂时使坯块不致变形,既不使粘结剂中低熔点组元因过早软化而导致坯块塌陷,也不因气体排出过多、过快而使坯块裂开。粘结剂肩负着这两项重要的功能,也就决定了它在PIM中举足轻重的地位。
硬质合金供应商:中钨在线科技有限公司 | 产品详情: http://www.tungsten-carbide.com.cn |
电话:0592-5129696 传真:5129797 | 电子邮件:sales@chinatungsten.com |
钨钼文库:http://i.chinatungsten.com | 钨钼图片: http://image.chinatungsten.com |
钨新闻3G版:http://3g.chinatungsten.com | 钼业新闻: http://news.molybdenum.com.cn |
微博

微信

粉末注射成型工艺流程
- 詳細
- カテゴリ: 钨业知识
- 2017年4月26日(水曜)18:01に公開
粉末注射成型技术是塑料成型工艺学、高分子化学、粉末冶金工艺学和金属材料学等多学科渗透与交叉的产物,利用模具可注射成型坯件并通过烧结快速制造高密度、高精度、三维复杂形状的结构零件,能够快速、准确地将设计思想物化为具有一定结构、功能特性的制品,并可直接批量生产出零件,是制造技术行业一次新的变革。
首先将固体金属或陶瓷粉末与有机粘结剂均匀混练后得到喂料,经制粒后在加热塑化状态下(约150℃)用注塑成形机把喂料注入模腔内固化成形得到注射成形坯,然后用化学或热分解的方法将注射坯中的粘结剂脱除,最后经真空炉或气氛炉将产品烧结致密化,对部分需要后处理的产品再进行后工序处理,得到最终形状和性能的产品。
PIM的工艺流程为:金属或陶瓷粉末+粘结剂→混炼→注射成型→脱脂→烧结→后处理。
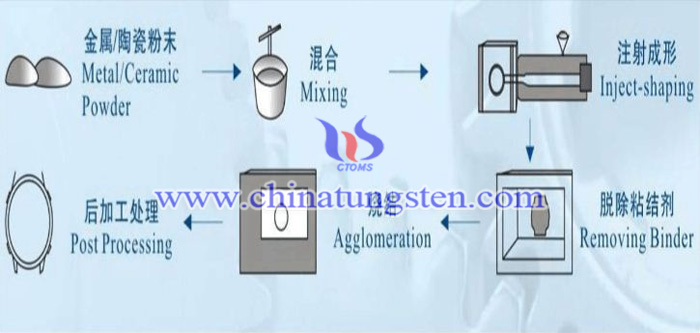
混料:混料(混炼)把粉末与有机粘结剂均匀掺混在一起,使各种原料成为注射成型用混合料。硬质合金合金生产中,此步骤还包括制粒过程。
注射成型:在注射成型过程中,混合料在注射机料筒内被加热成具有流变性的塑性物料,并在适当的注射压力下注入模具中,成型出毛坯。
脱脂:也称萃取过程,主要是指将有机粘结剂从坯体中去除。
烧结: 烧结能使多孔的脱脂毛坯收缩密化成为具有一定组织和性能的制品。尽管制品的性能与烧结前的许多工艺因素有关,但在许多情况下,烧结工艺对最终制品的金相组织和性能有着很大甚至决定性的影响。
硬质合金供应商:中钨在线科技有限公司 | 产品详情: http://www.tungsten-carbide.com.cn |
电话:0592-5129696 传真:5129797 | 电子邮件:sales@chinatungsten.com |
钨钼文库:http://i.chinatungsten.com | 钨钼图片: http://image.chinatungsten.com |
钨新闻3G版:http://3g.chinatungsten.com | 钼业新闻: http://news.molybdenum.com.cn |
微博

微信

粉末注射成形的应用领域
- 詳細
- カテゴリ: 钨业知识
- 2017年4月26日(水曜)17:58に公開
粉末注射成形技术具有一次成形生产形状复杂的金属、陶瓷等零件部件的能力,同时产品成本低、 光洁度好、精度高(±0.3%~±0.1%),一般无需后续加工产品强度,硬度,延伸率等力学性能高,耐磨性好,耐疲劳,组织均匀原材料利用率高,生产自动化程度高,工序简单,可连续大批量生产无污染等优点,其应用领域也十分广阔。可用于注射成型的材料非常广泛,原则上任何可高温浇结的粉末材料均可由PIM工艺造成零件,包括了传统制造工艺中的难加工材料和高熔点材料。主要有以下几种应用:
1.计算机及其辅助设备:如打印机零件、磁芯、撞针轴销、驱动零件
2.工具:如钻头、刀头、喷嘴、枪钻、螺旋铣刀、冲头、套筒、扳手、电工工具,手工具等
3.家用器具:如表壳、表链、电动牙刷、剪刀、风扇、高尔夫球头、珠宝链环、圆珠笔卡箍、刃具刀头等零部件
4.医疗机械用零件:如牙矫形架、剪刀、镊子
5.军用零件:导弹尾翼、枪支零件、弹头、药型罩、引信用零件
6.电器用零件:微型马达、电子零件、传感器件
7.机械用零件:如松棉机、纺织机、卷边机、办公机械等;
8.汽车船舶用零件:如离合器内环、拔叉套、分配器套、汽门导管、同步毂、安全气囊件等
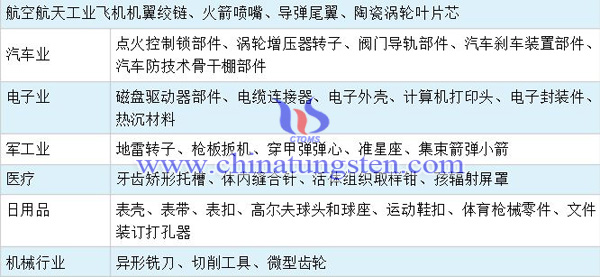
粉末注射成型在硬质合金领域的应用
粉末注射成型在硬质合金领域的应用包括:硬质合金刀具、硬质合金PCB钻头、离心器、喷嘴、活塞、泵零件、高尔夫球头、手表表壳。
粉末注射成形的优点
- 詳細
- カテゴリ: 钨业知识
- 2017年4月26日(水曜)17:57に公開
粉末注射成形能像生产塑料制品一样,一次成形生产形状复杂的金属、陶瓷零部件。该工艺技术利用注射方法,保证物料充满模具型腔,也就保证了零件高复杂结构的实现。以往在传统加工技术中,对于复杂的零件,通常是先分别制作出单个零件,然后再组装;而在使用PIM技术时,可以考虑整合成完整的单一零件,这样大大减少了生产步骤,简化了加工程序。
与传统零件加工成形工艺相比,它具有下述特点:
1、与传统的机械加工、精密铸造相比,制品内部组织结构更均匀;与传统粉末冶金相比,制品性能更优异,产品尺寸精度高,表面光洁度好,不必进行再加工或只需少量精加工。像生产塑料制品一样,一次成形生产形状复杂的金属、陶瓷等零部件,产品成本低,光洁度好,表面粗糙度可达到Ra 0.80~1.6μm,精度高,一般无需后续加工。金属注射成形工艺可直接成形薄壁结构件,制品形状已能接近或达到最终产品要求,零件尺寸公差一般保持在±0.10%~±0.30%水平,特别对于降低难以进行机械加工的硬质合金的加工成本、减少贵重金属的加工损失尤其具有重要意义。
2、零部件几何形状的自由度高,制件各部分密度均匀、尺寸精度高,适于制造几何形状复杂、精度密高及具有特殊要求的小型零件(0.2~200g)。 下图是粉末注射成形产品:
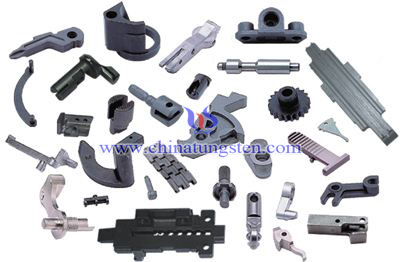
3、合金化灵活性好,对于过硬、过脆、难以切削的材料或原料铸造时有偏析或污染的零件,可有效降低制造成本。
4、产品质量稳定、性能可靠,制品的相对密度可达95%~100%,可进行渗碳、淬火、回火等热处理。
5、适用材料范围宽,应用领域广,原材料利用率高,生产自动化程度高,工序简单,可连续大批量规模化生产。生产过程无污染,为清洁工艺生产。MIM技术使用的模具,其寿命与塑料注射成形模具相似。由于使用金属模具,MIM适于零件的大批量生产;由于利用注射机成形产品毛坯,极大地提高了生产效率,降低了成本,而且注射成形产品一致性好、重复性好,从而为大批量和规模化工业生产提供了保证,再者一模多腔可进一步提高效率和降低毛坯的成形成本。
6、制品微观组织均匀,密度高,产品强度、硬度、伸长率等力学性能高,耐磨性好,耐疲劳,组织均匀,性能好。在粉末冶金压制过程中,由于模壁与粉末以及粉末与粉末之间的摩擦力,使得压制压力分布不均匀,也就导致了压制毛坯在微观组织的不均匀、材料致密性差、密度低,严重影响了产品的力学性能;而MIM是一种流体成形工艺,粘结剂的存在保证了粉末均匀排布,从而可消除毛坯微观组织的不均匀,进而使烧结制品密度接近材料的理论密度,从而使强度增加、韧性加强,延展性、导电性、导热性得到改善,综合性能提高。
硬质合金供应商:中钨在线科技有限公司 | 产品详情: http://www.tungsten-carbide.com.cn |
电话:0592-5129696 传真:5129797 | 电子邮件:sales@chinatungsten.com |
钨钼文库:http://i.chinatungsten.com | 钨钼图片: http://image.chinatungsten.com |
钨新闻3G版:http://3g.chinatungsten.com | 钼业新闻: http://news.molybdenum.com.cn |
微博

微信

粉末注射成型(PIM)
- 詳細
- カテゴリ: 钨业知识
- 2017年4月26日(水曜)17:53に公開
粉末注射成形(Powder Injection Molding,PIM)由金属粉末注射成形(Metal Injection Molding,MIM)与陶瓷粉末注射成形(Ceramics Injection Molding,CIM)两部分技术结合而成,它是一种新的金属、陶瓷零部件制备技术,它是将塑料注射成形技术引入到粉末冶金领域而形成的一种全新的零部件加工技术。 MIM的基本工艺步骤是:首先选取符合MIM要求的金属粉末和黏结剂,然后在一定温度下采用适当的方法将粉末和黏结剂混合成均匀的喂料,经制粒后再注射成形,获得成形坯(Green Part),再经过脱脂处理后烧结致密化成为最终成品(White Part)。
硬质合金混合料粉末注射成形是将热塑性聚合物加热到熔融状态后,加入一定比例的粉末,利用高剪切混料机将粉末与熔融态的聚合物均匀混合,制成喂料,在加热状态下,用注射成形机以一定的注射压力和注射速度将喂料注入模腔内,制得形状复杂的零部件坯体,再用化学、热分解或催化方法脱除其中的的成型剂。经烧结后得到最终制品。硬质合金产品注射成型包括喂料制备、注射成型、脱脂和烧结4个阶段,其工艺流程图如下:
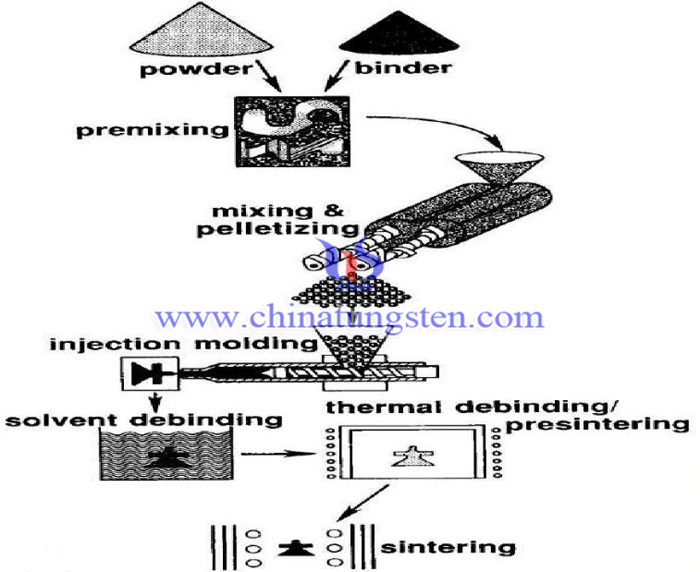
硬质合金供应商:中钨在线科技有限公司 | 产品详情: http://www.tungsten-carbide.com.cn |
电话:0592-5129696 传真:5129797 | 电子邮件:sales@chinatungsten.com |
钨钼文库:http://i.chinatungsten.com | 钨钼图片: http://image.chinatungsten.com |
钨新闻3G版:http://3g.chinatungsten.com | 钼业新闻: http://news.molybdenum.com.cn |
微博

微信

挤压外观缺陷之表面折叠
- 詳細
- カテゴリ: 钨业知识
- 2017年4月25日(火曜)15:29に公開
冷挤压时往往由于变形工序设计不妥, 会使坯料在挤压成形过程中产生各种缺陷。因此, 只有预先了解这些缺陷的成因, 才能在设计变形工序时, 采取有效的解决办法来确保生产出合格的挤压件。表面折叠是较为常见的挤压缺陷,
一、表面折叠
多余的表皮金属被压入坯料表层所形成的缺陷, 称为表面折叠。例如在正挤压中, 挤压头部较粗大的杆形件, 需要采用两道成形工序。如果在第一道正挤压中工件的头部与杆部连接处圆弧太大或相应锥角太小, 则在第二道成形工序中因凹模的圆角半径较小, 便有可能使坯料过渡区部分的材料被压入端部的底平面上, 而形成折叠。又如, 反挤压时凹摸底部设有较大的圆角半径, 而坯料底部为直角过渡, 在挤压过程中就会产生折叠。如果挤压变形继续进行, 这种折叠还会被移到工件的侧面。
折叠是线材表面沿挤压方向平直或弯曲的细线,通常与盘条表面呈某一角度分布,很长且形状相似。有时以两条平行线的形态出现。
挤压时,如果摩擦系数大和模具温度较低时,常在凹模底部形成一个难变形区,通常称为“死区”。由于该区金属不变形,而与其相邻的上部金属有变形和流动,于是便在交界处发生强烈的剪切变形,严重时将引起金属剪裂,即“死区”裂纹,有时可能由于上部金属的大量流动带着“死区”金属流动而形成折叠,如下图所示。
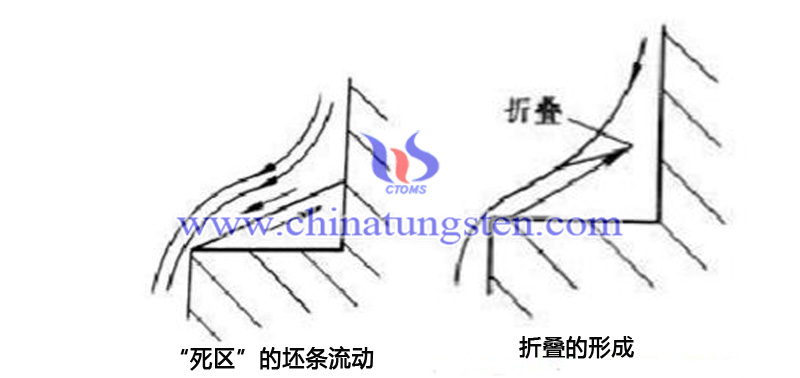
二、防止表面折叠的对策
防止“死区”剪裂和折叠的对策是改善润滑条件和正确控制模具和坯料的温度,还可以采用带锥角的凹模,锥角的作用在于使作用力在平行于锥面的方向有一个分力,该分力与摩擦力的方向相反,从而有利于金属的变形和流动。根据不同的条件可以通过计算确定一个合适的锥角,以抵消摩擦的影响。
硬质合金供应商:中钨在线科技有限公司 | 产品详情: http://www.tungsten-carbide.com.cn |
电话:0592-5129696 传真:5129797 | 电子邮件:sales@chinatungsten.com |
钨钼文库:http://i.chinatungsten.com | 钨钼图片: http://image.chinatungsten.com |
钨新闻3G版:http://3g.chinatungsten.com | 钼业新闻: http://news.molybdenum.com.cn |
微博

微信

挤压坯条长度和截面形状对挤压力的影响
- 詳細
- カテゴリ: 钨业知识
- 2017年4月25日(火曜)15:27に公開
一、挤压坯条长度对挤压力的影响
正向挤压时,通过挤压筒内坯条与筒壁之间的摩擦阻力产生作用,所以坯条长度对挤压力的大小有影响。挤压力与坯条长度的影响关系如下图所示。
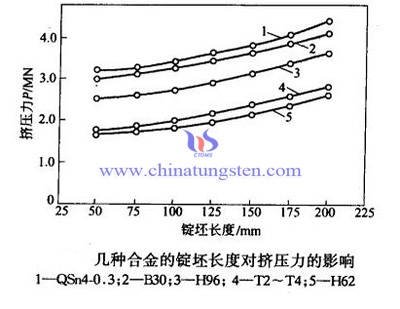
正向挤压时,坯条与挤压筒壁之间存在着较大的摩擦作用。一般来讲,随着外摩擦增加,金属流动不均匀程度增加,金属与挤压筒、挤压模表面之间的摩擦阻力增加,从而使挤压力增加。由上图可以看出,挤压力随着坯条长度增长而增大。实际生产中,由于不同的挤压条件下坯条与挤压筒壁之间的摩擦状态不同,因而坯条长度对挤压力的影响规律也不同。
一般反向挤压时,金属坯条与挤压筒内衬之间无相对滑动,挤压力与坯条长度无关。
二、制品断面形状对挤压力的影响
制品断面形状只有在比较复杂的情况下才对挤压力有明显的影响。挤压制品断面形状只是在比较复杂的情况下,才对挤压力有明显的影响。制品断面的复杂程度系数C1、C2可按下式计算:
C1=型材断面周长/等断面圆周;
C2=型材的外切圆面积/型材断面积。
在挤压变形条件下,制品断面形状越复杂,所需的挤压力越大,当断面复杂程度系数大于1.5时,挤压制品断面形状对挤压力影响更明显。
硬质合金供应商:中钨在线科技有限公司 | 产品详情: http://www.tungsten-carbide.com.cn |
电话:0592-5129696 传真:5129797 | 电子邮件:sales@chinatungsten.com |
钨钼文库:http://i.chinatungsten.com | 钨钼图片: http://image.chinatungsten.com |
钨新闻3G版:http://3g.chinatungsten.com | 钼业新闻: http://news.molybdenum.com.cn |
微博

微信

挤压速度对挤压力的影响
- 詳細
- カテゴリ: 钨业知识
- 2017年4月25日(火曜)15:25に公開
挤压速度系指单位时间内挤出坯料的长度,一般用mm/min表示。严格意义上讲,挤压速度其实包括挤压杆的前进速度和坯料从模孔流出的速度,即挤压速度与流出速度,两种之间在一定条件下有着确定的比例关系。挤压速度是通过对坯条的变形抗力的变化来影响挤压力的。冷挤压时,挤压速度对挤压力的影响较小。热挤压时,通常随挤压速度增加,挤压力增加(热挤压时,坯条在变形过程中产生的硬化可以通过再结晶软化,但这需要充分的时间,当挤压速度增加时,软化来不及进行,导致变形抗力增加,使挤压力增加)。下图为挤压黄铜棒时,挤压速度对挤压力的影响。
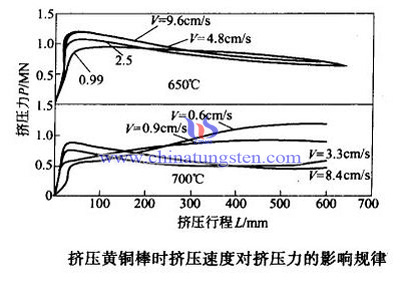
挤压速度过快,压坯易发生断裂,其原因有两种解释:一种认为中心部位的混合料与外层混合料由于流速差过大而引起料层间剧烈的摩擦,由摩擦产生的热造成局部石蜡熔化,减弱颗
粒间的粘结而造成断裂;另一种则认为,由于挤压速度过快,中心部位混合料流动的超前现象变得更严重,造成较大的剪切应力而使压坯断裂。
不同挤压阶段的挤压速度
(1)挤压前阶段,挤压速度越高,挤压力越大。
(2)随挤压继续进行,坯条冷却较慢,变形区温度可能提髙,挤压力逐渐下降。实际生产中,如果采用较低的挤压速度,由于挤压筒内锭坯的冷却,变形抗力增高,此时挤压力可能一直上升。
(3)挤压后阶段,挤压速度慢时,坯条温度降低,变形抗力升高,挤压力反而升高。
在适当的范围内,挤压速度对坯条质量影响不大。挤压速度主要从生产效率和操作方便性两个方面考虑。挤压速度过快,容易出现密度不均匀现象,甚至导致环状裂纹。过慢的挤压速度则使坯条产生“竹节”状痕迹。
硬质合金供应商:中钨在线科技有限公司 | 产品详情: http://www.tungsten-carbide.com.cn |
电话:0592-5129696 传真:5129797 | 电子邮件:sales@chinatungsten.com |
钨钼文库:http://i.chinatungsten.com | 钨钼图片: http://image.chinatungsten.com |
钨新闻3G版:http://3g.chinatungsten.com | 钼业新闻: http://news.molybdenum.com.cn |
微博

微信
