粉末成形过程
- 详细资料
- 分类:钨业知识
- 发布于 2017年4月21日 星期五 08:58
- 作者:ruibin
- 点击数:1716
粉末成形,使金属粉末体密实成具有一定形状、尺寸、密度和强度的坯块的工艺过程。它是粉末冶金工艺的基本工序之一。硬质合金品种多,用途广,成型方式很多,如模压成型、等静压成型、挤压成型、注射成型等。虽然成型方式各有不同,但粉末在成形中历经的过程是一致的,分别是颗粒位移与重排、弹塑性变形、断裂这三个过程。
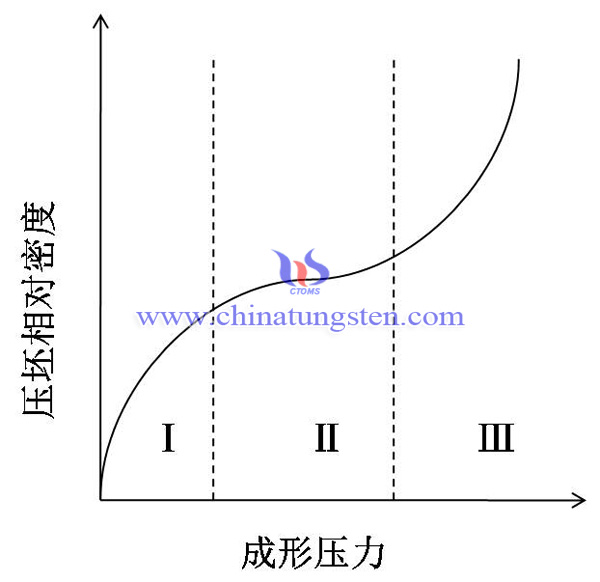
1、颗粒位移与重排
在这一阶段中,压坯密度迅速增大,这是因为粉末的拱桥现象在成形力的作用下迅速(颗粒间由于摩擦力的作用而相互搭架形成拱桥孔洞的现象)消除,粉末颗粒移动距离比较大,使孔隙急剧减少。压制压力部分耗费与颗粒间的摩擦。
影响第一阶段的主要因素有:
1、粉末颗粒间内摩擦;
2、模具、模腔表面粗糙度;
3、润滑条件;
4、颗粒的显微硬度;
5、颗粒形状;
6、颗粒间可用于相互填充的空间(孔隙度);
7、加压速度
粉末变形:
1、在这一阶段中,压坯密度增加缓慢,压制压力主要耗费与颗粒与模壁之间的摩擦和颗粒的弹塑性变形。粉末挤紧,颗粒开始有变形,根据变形的先后可以分为发生弹性变形和塑性变形阶段。
(1)弹性变形(颗粒接触应力≤材料的弹性极限)
对于塑性(有较大变形量)粉末,这一阶段并不明显,而对于硬质合金粉末,由于弹性模量大,这个阶段相当明显。
(2)塑性变形(颗粒接触应力≥材料的屈服强度)
压力的增大可能到达粉末材料的屈服强度,此时产生塑性变形。颗粒塑性变形的方向指向坯块中的孔隙,使得孔隙被填充,使压坯的密度增大。
断裂:
压力继续增大,可能达到粉末的强度极限,就会发生脆性断裂,脆性断裂使得断裂碎块填充孔隙,使得压坯密度继续增大。压制压力主要消耗于颗粒的破坏(也包括模具的变形)对于脆性粉末(没有明显变形过程)当粉末接触压力>断裂强度时发生脆性断裂;而对于塑性粉末,断裂过程较为复杂:颗粒接触应力≥材料的屈服强度-塑性变形-加工硬化-脆化-断裂。
影响粉末变形和断裂的主要因素
1、颗粒形状
2、粒度及组成;
3、颗粒表面粗糙度
4、颗粒比重(致密程度)
颗粒表面粘附作用(颗粒的磁性、静电、液膜的存在等。)
硬质合金供应商:中钨在线科技有限公司 | 产品详情: http://www.tungsten-carbide.com.cn |
电话:0592-5129696 传真:5129797 | 电子邮件:sales@chinatungsten.com |
钨钼文库:http://i.chinatungsten.com | 钨钼图片: http://image.chinatungsten.com |
钨新闻3G版:http://3g.chinatungsten.com | 钼业新闻: http://news.molybdenum.com.cn |
微博

微信
