知名矿山—黑龙江省宾县弓棚子铜锌钨矿
- 详细资料
- 分类:钨业知识
- 发布于 2017年5月30日 星期二 13:16
- 作者:Ganzhe
- 点击数:4731
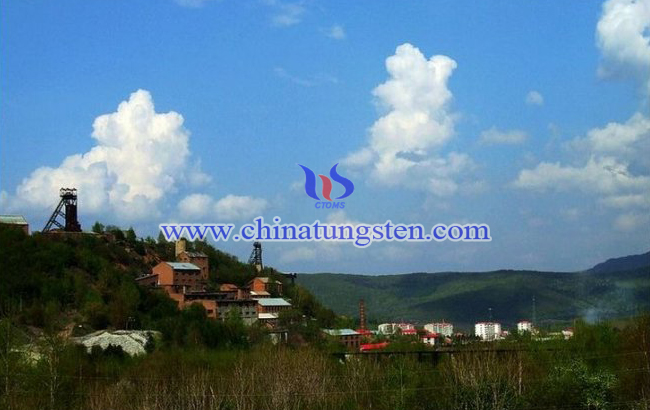
黑龙江省宾县弓棚子铜锌钨矿地处黑龙江省哈尔滨松江镇,地处松嫩边缘成矿区,以前主产铜,现在主产锌、钨,钼,其中钨储量为3.1万吨,可开采储量为3.01万吨,矿石品位0.41%,达到中型钨矿山标准。
知名矿山-黑龙江省逊克县翠宏山多金属矿
- 详细资料
- 分类:钨业知识
- 发布于 2017年5月30日 星期二 12:59
- 作者:Ganzhe
- 点击数:3606
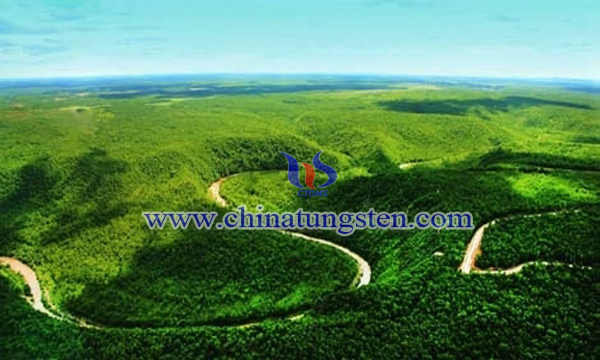
黑龙江省逊克县翠宏山多金属矿位于黑龙江省伊春市,地处小兴安岭林区腹地,主产铁、钨、钼、铅、锌、铜等矿,其储藏的矿产资源价值超过千亿元,该矿山的钨资源储量为12.16万吨,钨矿品位0.32%,多为伴生矿。
知名矿山-内蒙古克什克腾旗黄岗山锡多金属矿
- 详细资料
- 分类:钨业知识
- 发布于 2017年5月30日 星期二 12:46
- 作者:Ganzhe
- 点击数:2673
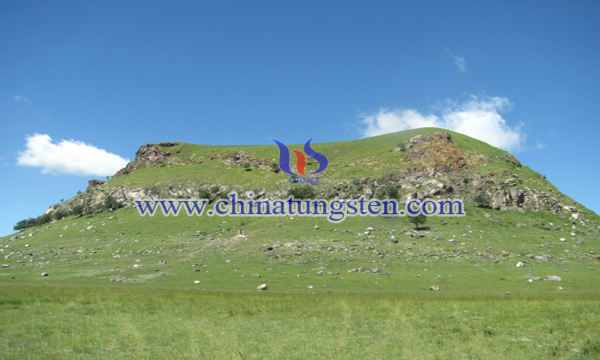
内蒙古克什克腾旗黄岗山锡多金属矿位于内蒙古自治区赤峰市克什克腾旗北部的黄岗梁一带,南距克什克腾旗驻地经棚镇 30km,北距黄岗梁林场场部 5km,是一座以铁和锡为主矿的大型多金属矿山,但近期,矿山外围发现了多条含钨矿脉,已探明钨储量5.29万吨,主要为白钨矿,钨矿石综合品位0.39%。
知名矿山-内蒙古额济纳旗七一山钨钼多金属矿
- 详细资料
- 分类:钨业知识
- 发布于 2017年5月30日 星期二 12:54
- 作者:weiping
- 点击数:2584
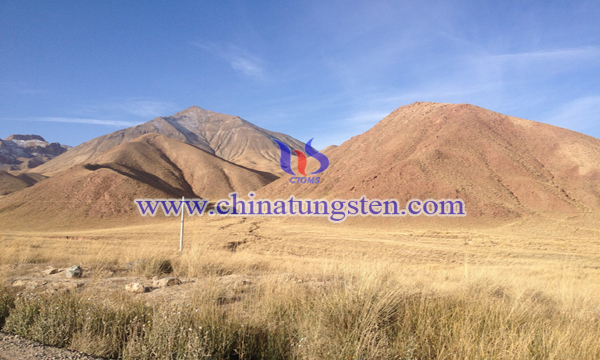
内蒙古额济纳旗额济纳旗七一山钨钼多金属矿位于内蒙古自治区阿拉善盟,地处中国北疆,位于内蒙古自治区最西端,目前已探明钨储量1.27万吨,主产黑钨矿,可开采1.27万吨,钨矿石综合品位0.174%,该矿山虽然目前没有开发价值,但拥有很好的开发前景。
知名矿山-内蒙古太仆寺旗白石头洼钨矿
- 详细资料
- 分类:钨业知识
- 发布于 2017年5月30日 星期二 12:38
- 作者:Ganzhe
- 点击数:3090
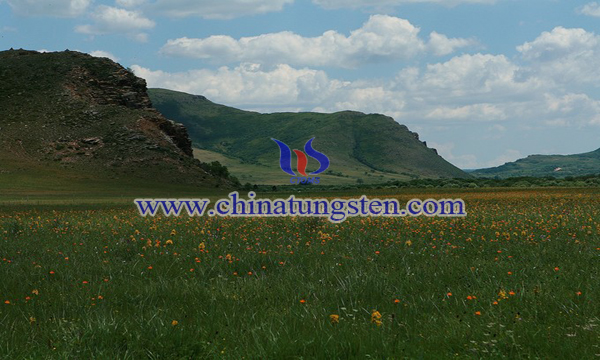
内蒙古太仆寺旗白石头洼钨矿地处内蒙古自治区锡林郭勒盟南部,大兴安岭西南边缘,阴山北麓,平均海拔1400米,主产黑钨矿,目前已探明钨储量2.22万吨,主产黑钨矿,可开采2.12万吨,钨矿石综合品位0.63%。