超细硬质合金压制性能
- 详细资料
- 分类:钨业知识
- 发布于 2017年5月31日 星期三 18:13
- 作者:ruibin
- 点击数:1917
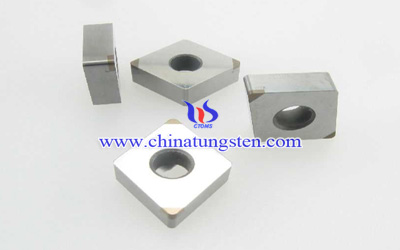
超细晶硬质合金混合料由于粉末拱桥效应大,比表面积,压坯相对密度小且密度不均匀,容易出现较大孔隙和颗粒团聚等问题,需要通过采取合适的混合料制备工艺和压制-烧结工艺来改善。
超细晶硬质合金混合料压制问题
- 详细资料
- 分类:钨业知识
- 发布于 2017年5月31日 星期三 18:09
- 作者:ruibin
- 点击数:1991
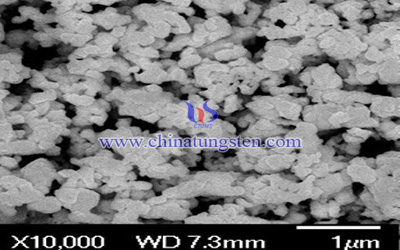
超细晶硬质合金(WC晶粒度小于0.5μm),晶粒度小于0.2μm的硬质合金为纳米硬质合金,但两者概念较为重叠,经常当作同一种类型的硬质合金看待。具有高强度、高硬度、高耐磨性等优良性能,满足了现代工业和特种难加工材料的发展。超细硬质合金材料可将和的优良性能复合有效地解决了传统硬质合金硬度与强度之间的矛盾实现了三高(高硬度高强度和高韧性)。
知名矿山-广东石人嶂钨矿山
- 详细资料
- 分类:钨业知识
- 发布于 2017年5月31日 星期三 13:13
- 作者:Ganzhe
- 点击数:3694
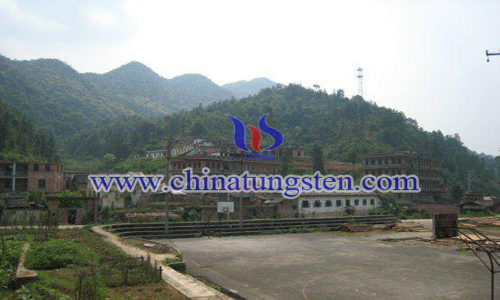
广东石人嶂钨矿山位于广东省韶关市始兴县境内的莲花山上,距离梅子窝钨矿山37公里,矿山面积3平方公里,石子嶂钨矿山和梅子窝钨矿山五十年前本一家,只是后来石人嶂矿山钨矿资源枯竭,兄弟才分了家。
知名矿山-广西武鸣大明山钨矿山
- 详细资料
- 分类:钨业知识
- 发布于 2017年5月31日 星期三 09:23
- 作者:Ganzhe
- 点击数:4251
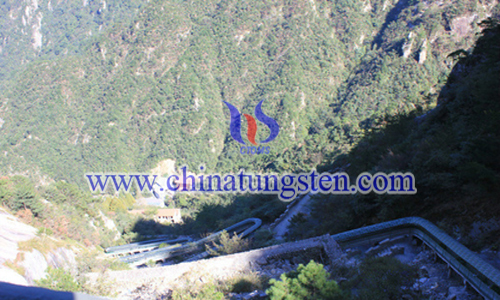
广西武鸣大明山钨矿山位于广西南宁武鸣县大明山脉那汉沟北东侧,区内蕴藏着丰富的矿产资源,包含有钨、铜、金、银、铅、锌、锰、钼等多种资源,尤其是钨铜钼富集明显并以钨矿尤为重要,目前已探明钨储量为16.02吨,钨矿品位0.236%,伴生贵金属矿多,具有良好的经济价值。