注射成型缺陷-飞边
- 详细资料
- 分类:钨业知识
- 发布于 2017年5月11日 星期四 18:28
- 作者:ruibin
- 点击数:1966
定义
当熔料从分型面被挤压出至模具型腔而产生薄片时便形成了飞边,又称溢边、 披锋、毛刺等,如下图所示。大多数飞边发生在模具的分合位置上,如动模和静模的分型面,滑块的滑配部位、镶件的绝隙、顶杆孔隙等处,飞边在很大程度上是由于模具或机台锁模力失效造成。一般来讲,由于各种因素的影响,塑件绝对不产生飞边是不可能的,只能通过条件控制予以弱化。
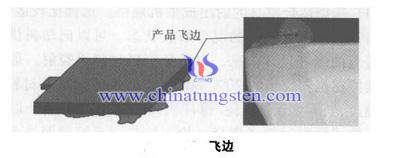
产生原因和改善措施
1、工艺:塑化温度过高、注塑时间过长、加料量太多、注塑压力过高、模温太高都会导致飞边的产生,这主要是由于温度和压力过大,导致熔料的溢出。
2、模具与设备:模具的问题是导致飞边最重要的原因。模具变形、型芯与型腔配合尺寸有误差、排气槽过深、锁模力不足、模板精度不足导致模板不平行、锁模力不足、模板闭合不紧、模板之间有异物都会导致两模板配合精度不足。特别是在大型成型品的情况下,模具一般都会发生变形,此时,有无支柱对飞边也有影响。如果没有支柱,变形缝隙就会增大,飞边也会增多。
3、原材料:流动性过高。同时,应选用流动性稍低的原料,否则树脂流动性越好,树脂就越容易进入缝隙,因此飞边也就越大。
硬质合金供应商:中钨在线科技有限公司 | 产品详情: http://www.tungsten-carbide.com.cn |
电话:0592-5129696 传真:5129797 | 电子邮件:sales@chinatungsten.com |
钨钼文库:http://i.chinatungsten.com | 钨钼图片: http://image.chinatungsten.com |
钨新闻3G版:http://3g.chinatungsten.com | 钼业新闻: http://news.molybdenum.com.cn |
微博

微信

注射成型缺陷-裂纹
- 详细资料
- 分类:钨业知识
- 发布于 2017年5月11日 星期四 18:22
- 作者:ruibin
- 点击数:1603
裂纹是注射制品较常见的一种缺陷,其主要成因是应力变形所致。这里的应力主要包括生坯或制品的残留应力、受到的外部应力。当裂纹拓展较严重时会导致制品的断裂,特别是对于硬质合金或陶瓷制品。
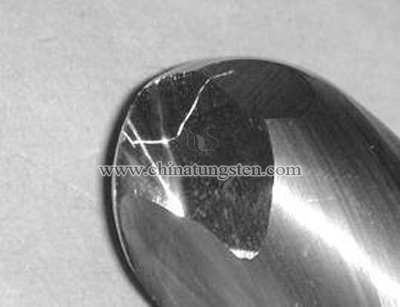
裂纹产生原因和改善措施
(1)产品结构设计不合理。注射制品中的尖角及缺口处通常会导致部件有较大残留应力集中,进而导致制品表面产生裂纹甚至断裂。在这些尖锐交接部位尽量设计圆弧倒角的形式不但可以有效降低应力集中素,而且可以使熔料流动得更顺畅和成品脱模时更容易。
(2)充填过剩,注射计量值太大,导致熔料在模具内的残留应力太高从而造成裂纹,如果裂纹产生在浇口周围,那么依据直浇口压力损失最小的特点,可考虑改用多个针形点浇口、侧浇口及柄形浇口等方式。 另外由于注射压力与残余应力存在正相关关系,可以通过降低注射压力,以减小残余应力。同理,在保压过程中,保压压力也不宜过大。适当提高模具温度,也可降低收缩时产生的应力。适当延长冷却时间也有利于残留应力的释放。
(3)外力导致应力集中。如果脱模,制品表面也会出现擦伤,甚至裂纹。模具设计时要考虑便于脱模,同时顶出力不能太大,顶出速度不能太快。
硬质合金供应商:中钨在线科技有限公司 | 产品详情: http://www.tungsten-carbide.com.cn |
电话:0592-5129696 传真:5129797 | 电子邮件:sales@chinatungsten.com |
钨钼文库:http://i.chinatungsten.com | 钨钼图片: http://image.chinatungsten.com |
钨新闻3G版:http://3g.chinatungsten.com | 钼业新闻: http://news.molybdenum.com.cn |
微博

微信

注射成型缺陷-夹心
- 详细资料
- 分类:钨业知识
- 发布于 2017年5月11日 星期四 18:12
- 作者:ruibin
- 点击数:1725
定义
夹心:夹心是指注射坯内外层冷却速率不同而造成先冷却的外部与后冷却的内部收缩率不一致。夹心现象就是在生坯破损断面上颜色不一, 像洋葱状, 内部颜色浅、外部颜色深的现象。颜色差异越大, 则夹心现象越严重。具体可参照下图。
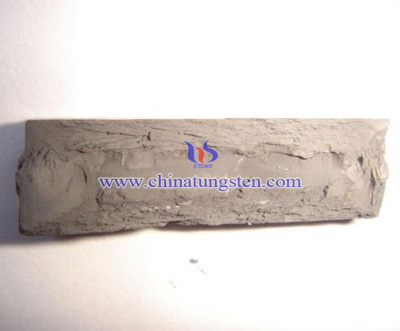
原因
1、充模过程中模温与料温差过大,料的外部接触到冷模迅速冷却而内部却保持柔软, 内外收缩不一造成的。
2、在充模时保压压力会将另一部分料压入坯中, 这同先入模的料在温度和收缩上不一致。
产生夹心表明注射坯内存在很大的内应力,这部分内应力是导致后续溶剂脱脂过程中坯体开裂的主要原因之一。通过缩小模/ 料温温度差异可使夹心程度降至最
低。
改善措施
1) 提高热导率,具体来说,根据热导率的傅里叶定律dQ=-λdA•dt/dn
可知,提高热导率可通过提高导热面积A和导热系数λ来实现。要提高充模和脱脂过程中硬质合金粉末相互之间的导热面积就必须提高熔料的粉末装载率;而要提高导热系数就必须增加熔料中流动态组分的比例。前者需要提高装载量(降低流动态组分比例),后者需提高流动态比例,这就需要在混合料体系中加入适量的分散剂(即表面活性剂)来实现,通过加入分散剂,既可改善导热情况,也能改善整体的流动性。
2)减小注射温度, 升高模温。降低温度不均匀,改善收缩不均的情况。
硬质合金供应商:中钨在线科技有限公司 | 产品详情: http://www.tungsten-carbide.com.cn |
电话:0592-5129696 传真:5129797 | 电子邮件:sales@chinatungsten.com |
钨钼文库:http://i.chinatungsten.com | 钨钼图片: http://image.chinatungsten.com |
钨新闻3G版:http://3g.chinatungsten.com | 钼业新闻: http://news.molybdenum.com.cn |
微博

微信

注射硬质合金孔洞
- 详细资料
- 分类:钨业知识
- 发布于 2017年5月11日 星期四 18:17
- 作者:ruibin
- 点击数:1553
表面缺陷硬质合金
定义:孔洞是指在生坯或制品的横截面上发现的孔隙。严重时可贯通生坯。孔洞发展到一定程度可贯穿坯体。注射成形坯孔洞可分为两种:中心缩孔和蜂窝状气孔。缩孔具体可参见下图。
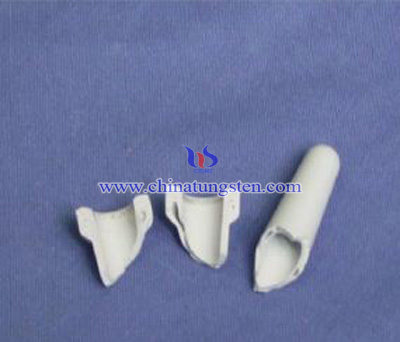
孔洞产生原因和改善措施
注射成型硬质合金的缩孔产生原因主要是当注射温度过高时,粘结剂发生较大膨胀(石蜡由固相转变为液相的体积膨胀率为 11%~20%) ,使其所占体积分数增大,喂料的装载量减小,充模后注射坯冷却时粘结剂发生较大收缩导致中心缩孔的产生。解决方法主要是使注射温度保持在较低温度。窝状气孔主要是由于在充模过程中模腔中的气体无法及时排出,夹杂在注射坯中而形成的,当注射时料温过低时,导致喂料粘度过大,喂料充模排气性变差,另外由于注射速度过快导致喂料中气体无法及时排出。通过调整注射速度与注射温度的匹配度消除了蜂窝状气孔。
总结来说,形成孔洞的因素有:
a) 注射时夹入气体、混炼时喂料不均、喂料夹有气体、不良充模均会引发;
b) 粉末同粘结剂分离;
c) 模温和料温不匹配;
d) 保压压力过小, 保压时间不足;
e) 喷射(解决办法: 改进模具设计, 使充模过程中喂料能以柱塞式运动; 降低模温或注射温度; 降低注射速度)。
硬质合金供应商:中钨在线科技有限公司 | 产品详情: http://www.tungsten-carbide.com.cn |
电话:0592-5129696 传真:5129797 | 电子邮件:sales@chinatungsten.com |
钨钼文库:http://i.chinatungsten.com | 钨钼图片: http://image.chinatungsten.com |
钨新闻3G版:http://3g.chinatungsten.com | 钼业新闻: http://news.molybdenum.com.cn |
微博

微信

注射成型硬质合金表面缺陷
- 详细资料
- 分类:钨业知识
- 发布于 2017年5月11日 星期四 18:06
- 作者:ruibin
- 点击数:1793
硬质合金粉末具有较高硬度、耐磨性、抗变形能力等性能,这些特点使其在注射成型过程中需要更细化的工艺选择。通过控制注射参数可在一定范围内控制注射坯的质量。如果注射参数匹配不当,则会产生各种缺陷。同时因硬质合金的力学性能对于极小的杂质、孔洞或其它小缺陷引起的断裂源都特别敏感,故研究工艺中各工序可能产生的缺陷及其原因,提出预防措施和解决办法,就显得至关重要。在这其中表面缺陷占据了很大的缺陷比重,常见的表面缺陷有两种:表面凹陷和表面流动纹。这两种表面缺陷,通常是由原料和注射工艺控制不当造成的。
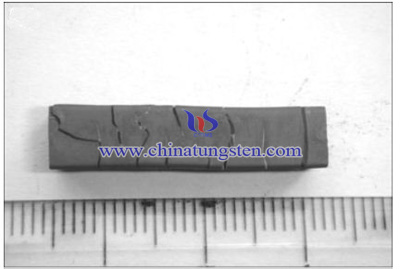
表面凹陷产生原因及改善措施
具体的硬质合金注射生坯表面凹陷如上图1所示。引起注射硬质合金生坯表面凹陷的原因
a) 冷流动, 即喂料在未充模腔之前, 最先入模的一部分料就已开始凝固的充模行为。可升高模温或用流动性更好的粘结剂来消除;
b)粉末和粘结剂分离,这是混炼时温度过高或注射温度过高, 粘度太低引起的;可适当降低注射加热温度;
c) 模温料温不匹配,引起局部的热收缩进而导致表面凹陷;可通过适当加热模具予以消除;
d)保压压力小且保压时间短,导致局部为充实压紧。可增大保压压力和保压时间予以消除。
表面流动纹产生原因及改善措施
注射坯表面出现的波浪状层纹即为表面流动纹,具体可参照下图2.原因在于此时的喂料粘度大,流动性差,与模壁之间的摩擦增大。喂料和模壁间的摩擦还取决于模具的加工精度,模腔表面光洁度越高出现流动纹的几率越小。实际注射过程中,在合适的注射温度下,通过适当提高注射速度和增大注射压力能很好地消除此类缺陷。
硬质合金供应商:中钨在线科技有限公司 | 产品详情: http://www.tungsten-carbide.com.cn |
电话:0592-5129696 传真:5129797 | 电子邮件:sales@chinatungsten.com |
钨钼文库:http://i.chinatungsten.com | 钨钼图片: http://image.chinatungsten.com |
钨新闻3G版:http://3g.chinatungsten.com | 钼业新闻: http://news.molybdenum.com.cn |
微博

微信
