注射成型硬质合金脱脂催化剂的选择
- 詳細
- カテゴリ: 钨业知识
- 2017年5月12日(金曜)16:35に公開
- 作者: ruibin
- 参照数: 1577
注射成型硬质合金催化脱脂速率由于反应机理的优势,远高于传统的注射成型硬质合金脱脂技术。
催化速率
催化反应仅在气体—粘结剂界面上进行,由生坯外部逐渐向内部发展, 催化脱脂从外向内的脱脂机制不产生裂纹和孔洞, 并且可以得到很高的脱脂速率。气体粘结剂界面向内部的移动速率为2-4mm/h, 远高于传统的脱
脂技术。而一般粘结剂为基的注射成形坯的脱脂速率为0.2mm/h, 催化脱脂速率是传统脱脂工艺速率的10~20倍。粘结剂组分、催化气体流量、脱脂时间和脱脂温度具会对催化脱脂率的影响,呈正相关关系。
注射成型硬质合金脱脂催化剂的选择
注射成型硬质合金脱脂催化脱脂过程中可在脱脂炉中引入高速惰性气流(氮气、氩气、氦气及其混合物)以加速小分子的扩散, 调节脱脂速率。通过控制催化剂的浓度可以控制脱脂速率。而且随着惰性气体流动速率的降低,脱脂区的催化剂浓度增加, 整个脱脂速率增加。因此, 惰性气流的流动速率要控制在适中的范围内。对于大多数陶瓷注射成型(CIM)粉末原料而言, 硝酸是合适的催化剂。硝酸具有强氧化性和很强的气化倾向,在正常的脱脂条件下, 硝酸蒸气不会沉积在脱除有机载体后的陶瓷零件的毛细管孔内,不会腐蚀炉子结构。对于因氧化而形成硝酸盐的粉末如Y2O3(烧结Si3N4 和SiC的添加剂)等, 草酸是可克服硝酸的缺点成为另一种应用广泛的催化剂。草酸是一种挥发性的有机酸, 室温是固态, 100℃以上升华为气态, 187℃以上分解为CO、CO2 和H2O。因此, 用草酸做催化剂, 催化后的废气处理也比较简单。草酸的应用, 拓宽了原料范围的选择。此外矿物酸、三氟化硼和有机酸等也有一定的应用范围。硝酸作催化剂时, 脱除速率为0.7—1.5mmh-1,且脱脂速率快慢顺序为Si3N4 >ZrO2 >SiC。草酸作催化剂时, 脱脂速率为0.9—1.5mmh-1, 脱脂快慢顺序为ZrO2 >SiC>Si3N4 。可见不同催化剂的催化作用存在很大的差异。两种催化剂作用下的脱脂效果进行了比较, 如图1, 图2所示。
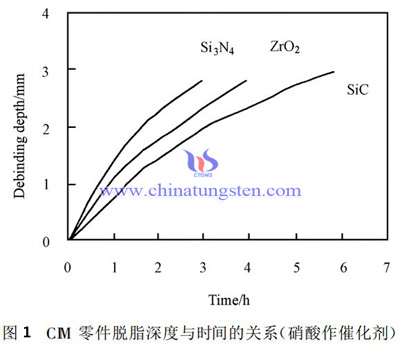
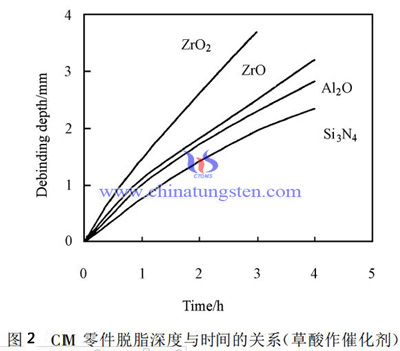
硬质合金供应商:中钨在线科技有限公司 | 产品详情: http://www.tungsten-carbide.com.cn |
电话:0592-5129696 传真:5129797 | 电子邮件:sales@chinatungsten.com |
钨钼文库:http://i.chinatungsten.com | 钨钼图片: http://image.chinatungsten.com |
钨新闻3G版:http://3g.chinatungsten.com | 钼业新闻: http://news.molybdenum.com.cn |
微博

微信

注射成型硬质合金催化脱脂原理
- 詳細
- カテゴリ: 钨业知识
- 2017年5月12日(金曜)15:29に公開
- 作者: ruibin
- 参照数: 2346
注射成型硬质合金催化脱脂的脱脂原理是利用一种催化剂把有机载体分子解聚为较小的可挥发的分子, 这些分子比其它脱脂过程中的有机载体分子有较高的蒸气压, 能迅速地扩散出坯体。注射成型硬质合金催化脱脂工艺所采用的粘结剂体系一般是由聚醛树脂、起辅助框架作用的聚合物和起稳定作用的添加剂组成.
聚醛树脂
其中聚醛树脂的结构特点是重复的C-O键组成, 如图1所示。具有较强的粘接力、高光泽、高硬度和优良的耐候性、耐化学品性。常用于用作增黏树脂,提高粘接力和硬度。
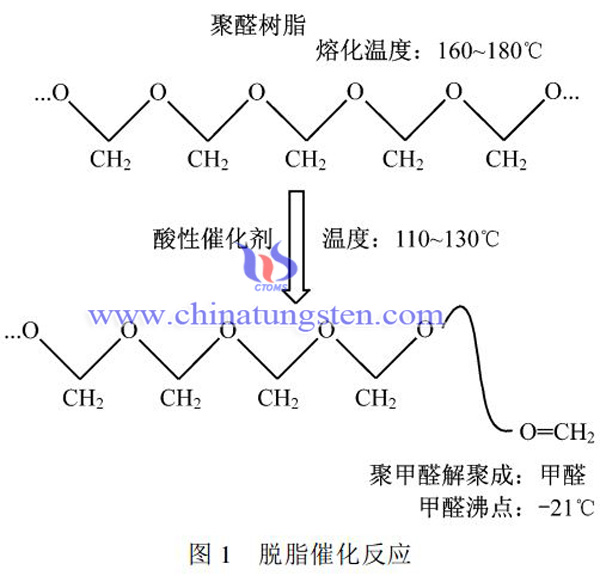
反应过程(如上图所示)
聚合物链的氧原子对酸的作用很敏感,当曝露在合适的酸催化剂中时, 在较低的温度下就能进行催化反应引起大分子聚醛树脂分裂成CH2O(甲醛)气体。一般用于注射成型硬质合金催化脱脂过程中的催化剂气体是硝酸和草酸气体。在110℃~130℃温度范围注射成型硬质合金催化脱脂的速率可以达到很高, 而该温度范围远低于聚醛树脂的熔化区间(160~180℃)。这种催化反应发生的条件特别适合于粉末注射成形中的粘结剂的脱除。这样, 生坯中的主粘结剂――聚醛树脂在催化剂的作用下直接由固态裂解为气态小分子, 达到快速注射成型硬质合金催化脱脂的目的。此时, 剩余的少量(低于10%)聚合物将起保形作用, 脱除了主粘结剂的生坯仍然是充分坚固的, 使零件在脱粘时具有延续的坚硬性, 避免任何塑性变形, 得到较好的公差。气态酸不透过粘结剂, 反应只是在气体与粘结剂的界面上进行。气体的扩散限制在已形成的多孔外壳上, 在生坯内部不会形成压力。而这些在生坯中残留的有机物质、分解剂、某些聚合物均可以在预烧结阶段迅速热解脱除。反应方程如下:
〖(CH_2-O)〗_2 □(→┴(acid(T>100℃)) nCH_2=O)
硬质合金供应商:中钨在线科技有限公司 | 产品详情: http://www.tungsten-carbide.com.cn |
电话:0592-5129696 传真:5129797 | 电子邮件:sales@chinatungsten.com |
钨钼文库:http://i.chinatungsten.com | 钨钼图片: http://image.chinatungsten.com |
钨新闻3G版:http://3g.chinatungsten.com | 钼业新闻: http://news.molybdenum.com.cn |
微博

微信

注射成型硬质合金催化脱脂
- 詳細
- カテゴリ: 钨业知识
- 2017年5月12日(金曜)15:22に公開
- 作者: ruibin
- 参照数: 1527
催化脱脂是近几年才发展起来的一种新脱脂工艺,也称为Metamold脱脂工艺。催化脱脂的工作原理是利用一种催化剂把有机载体分子解聚为较小的可挥发的分子,这些分子比其它脱脂过程中的有机载体分子有较高的蒸汽压,能迅速的扩散出坯体。催化脱脂工艺所采用的粘结剂体系一般是由起骨架作用的聚醛树脂,起辅助框架的高分子和起稳定作用的添加剂组成,目前催化脱脂已应用在注射成型硬质合金生产领域。
过程
该脱脂方法是利用某些在特定气氛下可以发生快速降解的聚合物作为主粘结剂, 使注射生坯在相应的气氛中发生催化脱脂, 其中的主粘结剂被快速分解脱除, 而对催化气氛不敏感的辅助粘结剂仍存留在生坯体中, 起到支撑的作用。催化脱脂工艺所采用的粘结剂体系一般是由聚醛树脂和起稳定作用的添加剂组成。聚醛基体系由于极性高和硬质合金粉体的相容性较好, 成型坯体强度高。在酸蒸汽催化作用下, 聚醛类的解聚反应一般在110℃—150℃之间快速进行, 反应产物是气态甲醛单体。反应过程如下图所示。
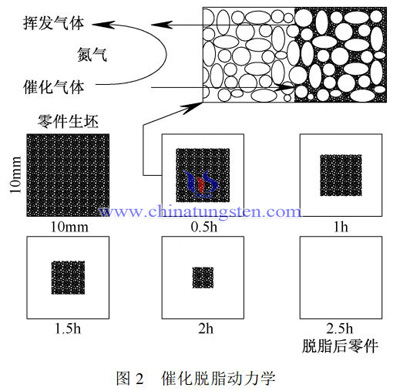
特点
催化反应温度低于主粘结剂软化温度, 在整个脱脂过程中不会产生液相, 从而避免了变形、坍塌等脱脂缺陷的产生。因此,催化脱脂综合了热脱脂和溶剂脱脂的优点, 克服了传统脱脂方式时间长、缺陷多、能耗高、污染环境等缺点。气体的扩散限制在已形成的多孔外壳上,在坯体内部不会形成压力。
硬质合金供应商:中钨在线科技有限公司 | 产品详情: http://www.tungsten-carbide.com.cn |
电话:0592-5129696 传真:5129797 | 电子邮件:sales@chinatungsten.com |
钨钼文库:http://i.chinatungsten.com | 钨钼图片: http://image.chinatungsten.com |
钨新闻3G版:http://3g.chinatungsten.com | 钼业新闻: http://news.molybdenum.com.cn |
微博

微信

注射成型硬质合金催化脱脂的特点
- 詳細
- カテゴリ: 钨业知识
- 2017年5月12日(金曜)15:25に公開
- 作者: ruibin
- 参照数: 1634
从注射成型硬质合金催化脱脂的脱脂原理中可以看出,注射成型硬质合金催化脱脂具有区别于传统脱脂方法(热脱脂和溶剂脱脂)的优异脱脂特性。
特点
1.脱脂速率快。在酸性催化剂的作用下聚醛树脂能够快速地分解成甲醛气体, 粘结剂――气态界面以1~2mm/h的线速度向内推进。注射成型硬质合金催化脱脂的速率可以达到2~4mm/h, 而一般粘结剂为基的注射成形坯的脱脂速率为0.2mm/h,注射成型硬质合金催化脱脂速率是传统脱脂工艺速率的10~20倍。由于注射成型硬质合金催化脱脂速率快, 脱脂时间短, 使得对注射成形坯尺寸厚度的限制小, 最大的脱脂厚度超过1英寸。
2.脱脂温度低。注射成型硬质合金催化脱脂的反应温度范围为100℃~ 140℃, 低于聚甲醛树脂的熔点(160℃~180℃), 避免了液相生成。这样就避免了热脱脂过程中由于生成液相而导致“生坯”软化, 或由于重力、内应力或粘性流动影响而产生变形和缺陷。
3.脱脂缺陷少。催化反应仅在气体—粘结剂界面上进行,由生坯外部逐渐向内部发展, 称之为“缩芯”机制。甲醛气体仅局限于在生坯的多孔“壳”区域产生, 可以容易地通过生坯的已是多孔的外部区域迅速逸出, 而不会在生坯内部产生应力, 不会产生生坯鼓泡、开裂等脱脂缺陷。
4.能实现连续脱脂和烧结。由于注射成型硬质合金催化脱脂速率快,脱除粘结剂所需的时间短, 使得注射成形中采用连续脱脂和烧结成为可能,下图为连续催化脱脂设备。
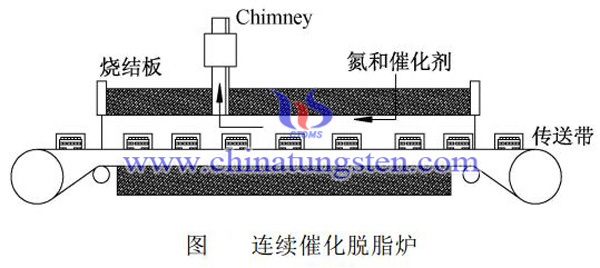
硬质合金供应商:中钨在线科技有限公司 | 产品详情: http://www.tungsten-carbide.com.cn |
电话:0592-5129696 传真:5129797 | 电子邮件:sales@chinatungsten.com |
钨钼文库:http://i.chinatungsten.com | 钨钼图片: http://image.chinatungsten.com |
钨新闻3G版:http://3g.chinatungsten.com | 钼业新闻: http://news.molybdenum.com.cn |
微博

微信

水萃取脱脂
- 詳細
- カテゴリ: 钨业知识
- 2017年5月12日(金曜)15:12に公開
- 作者: ruibin
- 参照数: 1609
水萃取脱脂
水萃取脱脂是Injectamax法的直接发展,此工艺是基于溶剂萃取脱脂工艺的基础上,经过改进而发展起来的一种新型脱脂工艺,该工艺所用的粘结剂可分为两个部分,一部分是可溶于水的,目前应用最广泛的水溶性高分子聚合物是聚乙二醇(PEG),聚环氧乙烷(PEO)以及纤维素和纤维素衍生出的琼脂糖,另一部分是不溶于水的,主要包括聚甲基丙酸甲酯(PMMA),聚乙烯醇缩丁醛(PVB)等树脂或乙酸丁酸纤维素(CAB)等。
水萃取脱脂过程
水溶性粘结剂在坯体中的脱除机制如下图表示。首先,脱脂前坯体为陶瓷粉末与粘结剂两相体系粉末颗粒间被连续的粘结剂填充;坯体在浸入40 ℃-60 ℃热水中,由于受热而迅速膨胀,水分子就扩散到坯体表面与粘结剂分子形成溶胀体坯体表面的粘结剂发生溶解形成了细小的空隙;随着脱脂进行,水分子随着空隙不断扩散到坯体内部与内部粘结剂分子形成溶胀,并且随着内部粘结剂溶解排除坯体而留下了更多的空隙;随着新的通道的产生,水与粘结剂的接触面越来越大,提高了脱脂速率。最后,当脱脂2-3 h之后,形成了相互连通的孔隙通道。可以看出最后坯体内部气孔明显增加了,在这个时期这些不溶于水的粘结剂支撑着坯体也是比较脆弱的阶段,坯体内部形成了大量的通道,这些通道也能成为之后不溶于水的粘结剂受热排出坯体的通道。
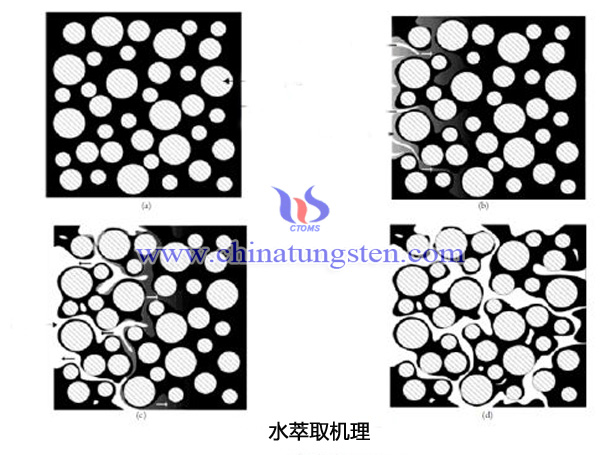
水萃取脱脂特点
与有机溶剂脱脂相比较水脱脂既具有脱脂速率快的特点,又不会损害人体的健康或污染环境。但是水溶性粘结剂存在吸水问题,因此MIM喂料的贮存和运输需特殊装置,而且与水溶性粘结剂中的水溶性部分(如聚乙二醇) 相容的聚合物很少且混炼时易发生溶胀,喂料混炼时间很长。
硬质合金供应商:中钨在线科技有限公司 | 产品详情: http://www.tungsten-carbide.com.cn |
电话:0592-5129696 传真:5129797 | 电子邮件:sales@chinatungsten.com |
钨钼文库:http://i.chinatungsten.com | 钨钼图片: http://image.chinatungsten.com |
钨新闻3G版:http://3g.chinatungsten.com | 钼业新闻: http://news.molybdenum.com.cn |
微博

微信
