挤压成形影响因素-挤压嘴直径
- 詳細
- カテゴリ: 钨业知识
- 2017年4月25日(火曜)15:23に公開
- 参照数: 2014
挤压嘴直径也称为出口自径或出门喇叭锥直径。模具出口直径d过小,则易划伤制品表面,甚至会引起堵模。但d过大,会大大削弱定径带的强度,引起定径带过早地变形、压蹋,明显地降低模具使用寿命。因此,在一般情况下,出口带尺寸应比定径带尺寸大,对于薄壁管或变外径管材的模具,其值可适当增大。为增大模具的强度和延长模具的使用寿命,出口带可做成喇叭锥。出口喇叭锥角(从挤压型材离开定径带开始)可取 (此值受锥刀角度的限制)。特别是对于壁厚小于 而外形十分复杂的型材模具,为了保证模具的强度,必须做成喇叭出口。有时为了便于加工,也可设计成阶梯形的多级喇叭锥。为了增大定径带的抗剪强度,定径带与出口带之间可以20°-45°的斜面以圆角半径为1.5-3.0mm的圆弧连接。
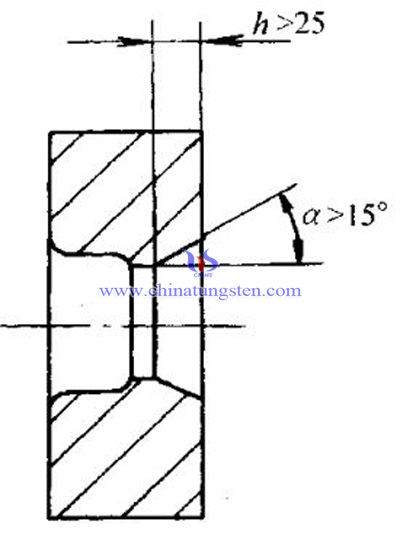
挤压嘴直径通常根据挤压时的收缩系数确定。对于确定的挤压机,所能挤出坯条的最大直径受挤压机的能力限制,确切地说,受挤压缸径和压力的限制。挤出坯条的最大直径可按下式计算
d=√((1-k) D^2 )
式中:d---挤压机所能挤出的最大坯条直径,mm;
k---挤压压缩率,一般取值≥0.95;
D---挤压缸直径,mm。
硬质合金供应商:中钨在线科技有限公司 | 产品详情: http://www.tungsten-carbide.com.cn |
电话:0592-5129696 传真:5129797 | 电子邮件:sales@chinatungsten.com |
钨钼文库:http://i.chinatungsten.com | 钨钼图片: http://image.chinatungsten.com |
钨新闻3G版:http://3g.chinatungsten.com | 钼业新闻: http://news.molybdenum.com.cn |
微博

微信

挤压成形影响因素-定径带
- 詳細
- カテゴリ: 钨业知识
- 2017年4月25日(火曜)15:15に公開
- 参照数: 2668
定径带有称定型带、工作带,是模具中垂直模具工作端面并用以保证挤压制品的形状、尺寸和表面质量的区段,下图中h即为定径带长度,α为模角.

定径带长度h过短,挤出阻力虽小,但会造成挤压速度快,弹性后效急剧释放,坯条容易产生摆动,制品尺寸难于稳定,易产生弯曲、变形、波纹、椭圆等废品,同时,模具易磨损,会大大降低模具的使用寿命;但h过长,会增大与金属的摩擦,增加挤压力,易粘结金属,使制品表面出现划伤、毛刺、麻面、搓衣板型波浪,同时由于附加内应力的增大而导致坯条纵向裂纹等缺陷。h应根据挤压机的结构(立式或卧式)、被挤压金属材料、产品的形状和尺寸等因素来确定。在立式挤压机上挤压管材时,一般2-6mm;挤压镁合金时,一般的最小值为1.5-33mm,最大值依产品的尺寸和形状确定。对于硬质合金混合料挤压工艺而言,定径带的长度一般按坯条直径的3-5倍选取,
即h=3-5d
式中:h-为定径带长度;
d-为挤压嘴直径;
挤压硬质合金混合料与挤压致密金属不同,h取值较大,以保证适当的坯条密度、减少物料的弹性膨胀、维持坯条的形状。
硬质合金供应商:中钨在线科技有限公司 | 产品详情: http://www.tungsten-carbide.com.cn |
电话:0592-5129696 传真:5129797 | 电子邮件:sales@chinatungsten.com |
钨钼文库:http://i.chinatungsten.com | 钨钼图片: http://image.chinatungsten.com |
钨新闻3G版:http://3g.chinatungsten.com | 钼业新闻: http://news.molybdenum.com.cn |
微博

微信

挤压成形影响因素-模角
- 詳細
- カテゴリ: 钨业知识
- 2017年4月25日(火曜)15:13に公開
- 参照数: 2334
挤压模具的模孔形状主要是指模角大小、定型带长度、挤压嘴直径这三部分,它们对挤压过程,特别是挤压压力都会不同程度的影响。其中模角大小是非常重要的挤压模具参数,它对挤压力的大小、挤压成形质量影响重大。
模角是指模面与挤压轴线的夹角。模角对挤压力也有明显影响。模角α由0°改变到90°之间,在45°-60°范围内挤压力最小。 挤压模角对挤压力的影响:模角对挤压力的影响,主要表现在变形区及变形区锥表面,模角对挤压力有着明显的影响。挤压应力与模角的关系如下图所示。随着模角α逐渐增大,挤压力逐渐降低,模角继续增大时,挤压力呈升高趋势。另外,由下图也可以看出挤压力分量与模角之间的关系。在一定的变形条件下,随着模角的增大,变形区内所需的挤压力分量RM增加,这是由于粉末坯条流入和流出模孔时的附加弯曲变形增加之故。但用于克服挤出锥面上摩擦阻力的分量TM,由于摩擦面积的减小而下降。以上两个方面因素综合作用的结果,使Tm在某一模角下为最小,从而总的挤压力也为最小。模角视坯条的直径而定,坯条较大,模角α相应增大,坯条较小时,α可相应减小。模角角过小,物料容易流入定型带,坯条中心密度难以保证。模角过大,挤压力增大,毛坯产生分层等缺陷。
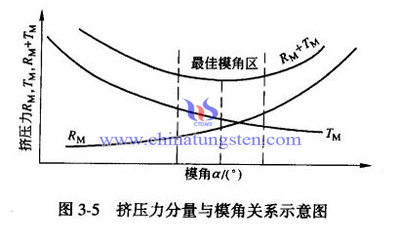
挤出锥角是挤压嘴中心剖面中两个对称模面的角度大小,其数值为模角的两倍,工业中也常以挤出锥角参数来代替模角参数。
硬质合金供应商:中钨在线科技有限公司 | 产品详情: http://www.tungsten-carbide.com.cn |
电话:0592-5129696 传真:5129797 | 电子邮件:sales@chinatungsten.com |
钨钼文库:http://i.chinatungsten.com | 钨钼图片: http://image.chinatungsten.com |
钨新闻3G版:http://3g.chinatungsten.com | 钼业新闻: http://news.molybdenum.com.cn |
微博

微信

挤压温度对挤压力的影响
- 詳細
- カテゴリ: 钨业知识
- 2017年4月25日(火曜)15:09に公開
- 参照数: 2072
挤压温度对挤压力的影响:挤压温度对挤压力的影响,是通过变形抗力的大小反映出来的。下图为不同温度下几种铜合金挤压时挤压力的影响规律。一般来讲,随着变形温度的升高,锭坯的变形抗力下降,所需的挤压力也下降。实际上,大多数金属与合金的变形抗力随温度升高而下降的关系,不能保持上述的严格线性关系,所以挤压力与温度的关系也一般为非线性关系。
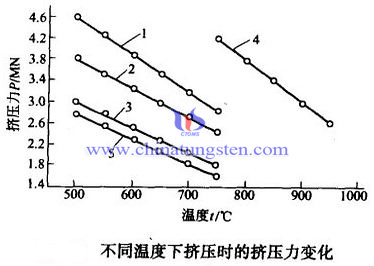
挤压物料的塑性受温度的影响。大多数的增塑剂的粘性会随温度的升高而下降。如在20℃时,石蜡的粘度为26.1x1010Pa.S,而在熔点附近时(45℃左右),石蜡的粘度只有0.8x1010Pa.S。随着挤压温度的升高,增塑剂的塑形变好。温度太低时,所需的挤压压力太大,容易造成横向断裂或分层,挤压温度太高,挤压压力急剧下降,造成坯条软化变形,难于挤压坯的形状也容易产生断裂。一般来说,增塑剂加量较多时,坯条尺寸较大时,应该采用较低的挤压温度。随着温度的升高,金属或合金的变形阻力降低,塑性提高。利用此特性,将金属粉末或压坯加热通过模具进行挤压成形的过程称为粉末热挤。挤出的坯件尺寸及形状完全由模具嘴的尺寸或型腔来控制。按挤压金属特性和挤压零件形状,热挤法可分成非包套热挤和包套热挤两种形式。
硬质合金供应商:中钨在线科技有限公司 | 产品详情: http://www.tungsten-carbide.com.cn |
电话:0592-5129696 传真:5129797 | 电子邮件:sales@chinatungsten.com |
钨钼文库:http://i.chinatungsten.com | 钨钼图片: http://image.chinatungsten.com |
钨新闻3G版:http://3g.chinatungsten.com | 钼业新闻: http://news.molybdenum.com.cn |
微博

微信

变形抗力和变形程度对挤压力的影响
- 詳細
- カテゴリ: 钨业知识
- 2017年4月25日(火曜)15:07に公開
- 参照数: 1987
掌握影响挤压力的主要因素
影响挤压力的主要因素有:挤压时的金属变形抗力、变形程度、模孔形状、制品断面形状、流出速度、锭坯的长度、接触摩擦条件等。
(1) 挤压时的粉末变形抗力。挤压力与抵抗力成正比关系。(但由于粉末的不均匀性,往往不能保持严格的线性关系。)变形温度通过影响金属变形抗力而影响挤压力,随着温度的升高,挤压力降低。
(2) 变形程度。挤压力与之也是成正比关系,随着变形程度增大挤压力增加。下图为不同种类粉末在不同挤压比的条件下的挤压力对比。挤压比extrusion ratio)是指挤压筒腔的横断面面积同挤压制品总横断面面积之比,也叫挤压系数。挤压比是挤压生产中用于表示金属变形程度大小的参数,用λ表示:λ=Ft/ΣF1。挤压比同变形程度、挤压力有如下关系:(1)挤压比增大时,金属流出模孔的困难程度会增大,挤压力也增大;(2)当其他条件相同时,挤压比增大,挤压时锭坯外层金属向模孔流动的阻力也增大,因此使内外部金属流动速度差增大,变形不均匀;(3)但当挤压比增加到一定程度后,剪切变形深入到内部,变形开始向均匀方向转化。研究证明,当挤压变形程度ε达到85%~90%时,挤压金属流动均匀,制品内外层的力学性能也趋于均匀。从图中可以看出,抵抗力(粉末种类)与变形程度(挤压比)均会对挤压压力产生影响。
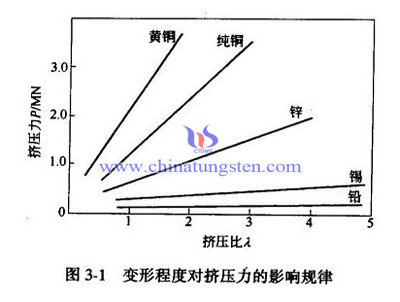
硬质合金供应商:中钨在线科技有限公司 | 产品详情: http://www.tungsten-carbide.com.cn |
电话:0592-5129696 传真:5129797 | 电子邮件:sales@chinatungsten.com |
钨钼文库:http://i.chinatungsten.com | 钨钼图片: http://image.chinatungsten.com |
钨新闻3G版:http://3g.chinatungsten.com | 钼业新闻: http://news.molybdenum.com.cn |
微博

微信

挤压工艺流程
- 詳細
- カテゴリ: 钨业知识
- 2017年4月25日(火曜)15:03に公開
- 参照数: 2336
挤压工艺流程为如下所示:
掺和
掺和的目的是在于使增塑剂和粉末混合均匀,以获得良好塑性的混合料。该过程也称为捏合,是挤压过程的关键环节,捏合是一种强力剪切的混合过程。掺和(捏合)后的混合料称为喂料
预压(压团)
混合料预压的作用是使增塑剂与颗粒表面充分接触,消除其中夹杂的气体,使混合料密度均匀。预压的操作程序是将掺合料装入圆筒压模内在压力机上以一定压力压实混合料;或把掺合料直接装入挤压筒内,密封挤压嘴,施以一定压力把混合料挤压密实。为了排气充分,最好在具有真空装置的挤压机中进行预压作业,并适当保压。硬质合金的压团过程需要在5x10-2pa的真空度,压团压力在1.2-1.5t/cm2的压力下进行,该压力与普通模压压力接近。
挤压
增塑粉末料的挤压可在油压机或专用挤压机上进行。物料进入料仓后,通过蜗杆将物料推压入挤压套筒内,通过挤压嘴获得所需的制品。混合料的挤压温度一般控制在40-50℃,可在模筒外壁装上加热器。挤压速度可在较大的范围内选择,以实际挤压坯不出现缺陷为限。挤压压力通常在300MPa以下。挤压过程受挤压压力、挤压速度、挤压温度等参数的影响。
硬质合金供应商:中钨在线科技有限公司 | 产品详情: http://www.tungsten-carbide.com.cn |
电话:0592-5129696 传真:5129797 | 电子邮件:sales@chinatungsten.com |
钨钼文库:http://i.chinatungsten.com | 钨钼图片: http://image.chinatungsten.com |
钨新闻3G版:http://3g.chinatungsten.com | 钼业新闻: http://news.molybdenum.com.cn |
微博

微信

挤压过程的三个阶段
- 詳細
- カテゴリ: 钨业知识
- 2017年4月25日(火曜)14:58に公開
- 参照数: 3658
(一)掌握挤压过程的三个基本阶段
根据金属在挤压过程中的流动特点,通常把挤压变形过程划分为三个阶段(对应下图挤压力行程曲线上的Ⅰ、Ⅱ、Ⅲ区),分别是:
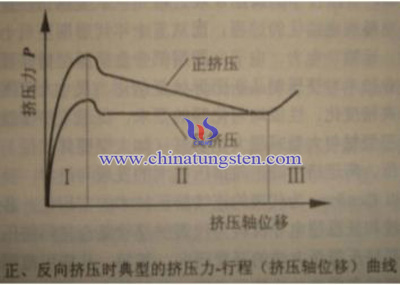
(1) 开始挤压阶段(也称填充挤压阶段)。金属受挤压轴的压力后,首先充满挤压筒与模孔,挤压力直线上升,粉末间空隙被逐渐填充,孔隙率大幅下降。
(2) 基本挤压阶段(也称平流挤压阶段)。从混合料粉末开始流出模孔到正常挤压过程即将结束时为止。在此阶段,筒内的锭坯一般来说,其内部与外部之间基本上不发生交错流动,锭坯的外层金属流出模孔后仍在制品的外层而不会流到制品的中心。在挤压时,锭坯任一横断面上的金属质点皆以同一速度或一定的速度差进入变形区压缩锥。靠近垫片和模子角落处的金属不流动,形成难变形区。正挤压的挤压力随着锭坯长度的减小而直线下降。
(3) 终了挤压阶段(也称缩尾挤压阶段或紊流挤压阶段)。在此阶段,锭坯的外层金属向其中心剧烈流动,同时两个难变形区中的金属也向模孔流动,形成挤压所特有的缺陷“挤压缩尾”。挤压力重新开始上升,此时应结束挤压操作。
硬质合金供应商:中钨在线科技有限公司 | 产品详情: http://www.tungsten-carbide.com.cn |
电话:0592-5129696 传真:5129797 | 电子邮件:sales@chinatungsten.com |
钨钼文库:http://i.chinatungsten.com | 钨钼图片: http://image.chinatungsten.com |
钨新闻3G版:http://3g.chinatungsten.com | 钼业新闻: http://news.molybdenum.com.cn |
微博

微信

【知钨】什么是高比重钨合金?
- 詳細
- カテゴリ: 钨业知识
- 2017年4月24日(月曜)20:51に公開
- 参照数: 2157
高比重合金供应商:中钨在线科技有限公司 | 产品详情: http://www.tungsten-alloy.com |
电话:0592-5129696 传真:5129797 | 电子邮件:sales@chinatungsten.com |
钨钼文库:http://i.chinatungsten.com | 钨钼图片: http://image.chinatungsten.com |
钨新闻3G版:http://3g.chinatungsten.com | 钼业新闻: http://news.molybdenum.com.cn |
微博

微信

挤压增塑剂的选择
- 詳細
- カテゴリ: 钨业知识
- 2017年4月24日(月曜)20:09に公開
- 参照数: 1931
挤压增塑剂
由于挤压压力的限制,为保持坯条密度,就要求挤压增塑剂(类似模压成型剂)比普通模压所用的增塑剂具有更大的粘性,加入量也要相应增多。
增塑剂的要求:
1、增塑剂应具有较佳的可塑性质,具有较强的粘结能力,
2、不与金属粉末料起化学作用,在制品的烧结温度下能全部挥发除去。
表中数据为各种增塑剂在空气中灼烧后的残渣,从表可看出,石蜡汽油及石蜡在空气中灼烧后全部挥发除去。所以,生产上常优先选用石蜡作增塑剂。为了改善挤压粉末与增塑剂之间的接触,提高颗粒之间的粘结能力,常常加入少量表面活性剂(如硬脂酸)和粘结剂(如聚乙烯醇)组成混合增塑成形剂。
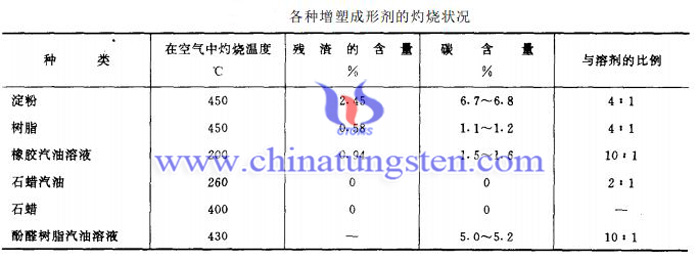
硬质合金粉末混合料(RTP)必须经过增塑处理,才能挤压成型。增塑过程也称捏合。捏合是一种强力剪切的混合过程。捏合的目的是使挤压增塑剂均匀分布在混合料中,捏合后得到的混合料称为喂料。
一般碳化钨钴类合金,常采用石蜡作增塑剂,其用量同合金料的牌号及挤压嘴的孔径大小有关,一般为6.0%-8.5%。
硬质合金供应商:中钨在线科技有限公司 | 产品详情: http://www.tungsten-carbide.com.cn |
电话:0592-5129696 传真:5129797 | 电子邮件:sales@chinatungsten.com |
钨钼文库:http://i.chinatungsten.com | 钨钼图片: http://image.chinatungsten.com |
钨新闻3G版:http://3g.chinatungsten.com | 钼业新闻: http://news.molybdenum.com.cn |
微博

微信

硬质合金棒材的成形方法
- 詳細
- カテゴリ: 钨业知识
- 2017年4月24日(月曜)20:05に公開
- 参照数: 2168
硬质合金棒材因其特殊的耐磨蚀、高硬度、优良的断裂韧性和抗压强度使其在金属加工、电子工业、木材加工、航空航天业及医学等领域得到了广泛应用, 是制造印刷电路板微钻、铣刀、铰刀、阶梯刀具、长杆刀具、丝锥和点阵打印机打印针等的理想前期材料。
制粉→按用途要求配方→经湿磨→混合→粉碎→干燥→过筛→后加入成型剂→再干燥→过筛后制得混合料→制粒→ 压制→成型→低压烧结→成型(毛坯)→外圆磨精磨(毛坯没有这道工序)→检测尺寸→包装→入库。
硬质合金棒材成型工艺主要有挤压成形、等静压成形、模压成形这三种。
一、 挤压成形
硬质合金棒材挤压工艺的优点在于棒材的长度原则上不受成形的限制,且纵向密度均匀;生产连续性强,成形效率高,设备简便,操作方便。流程图如下:
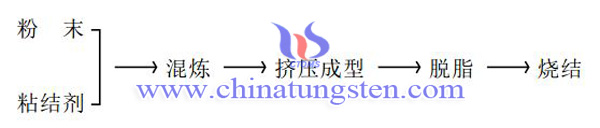
二、等静压成形
1、压割法
把研磨后过筛的碳化物粉末压制成块状, 然后进行冷等静压处理, 再进行后续加工。在此工艺中, 只要少量的塑化剂, 如石蜡、聚乙醇等。如果冷等静压的压力足够高(400MPa), 甚至可不加粘结剂。这种方法成型的棒材, 表面非常粗糙, 成品
前, 必须进行磨削和车削加工。
2、湿袋法
模具处于高压液体内均匀受压(约200MPa),试件尺寸受模腔限制, 不适于批量生产, 主要用于大直径棒材
3、干袋法
它以不同的流体作传压介质, 模具是半固定式的, 坯料的添加和取出都在干燥状态下操作。自动化程度较高, 操作周期短, 适用于批量成型。这种方法成型的棒材长度比机械模压法长些(最长达400mm), 成型时使用少量(1%~1.5 %)石蜡或聚乙烯醇。
硬质合金供应商:中钨在线科技有限公司 | 产品详情: http://www.tungsten-carbide.com.cn |
电话:0592-5129696 传真:5129797 | 电子邮件:sales@chinatungsten.com |
钨钼文库:http://i.chinatungsten.com | 钨钼图片: http://image.chinatungsten.com |
钨新闻3G版:http://3g.chinatungsten.com | 钼业新闻: http://news.molybdenum.com.cn |
微博

微信
