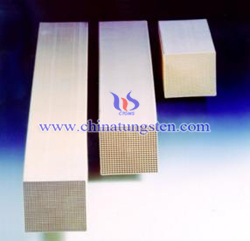
Currently, working life of SCR denitration catalyst is generally 3~5 years, the commonly treatment ways of the deactivated catalyst are regenerating or landfill. Landfill will not only result in the occupation of land resources, but also a tremendous waste of resources. According to statistics, by 2018, it will produce annually 38,000 tons of waste SCR denitration catalyst, which contains 1520 tons of tungsten trioxide. Because tungsten is a rare metal and the very high price of tungsten trioxide, if the waste SCR catalyst can’t get reasonable treatment and the valuable resources can’t be recovered, the great waste of resources will cause.
Simple method for recovering tungsten trioxide from SCR denitration catalyst is as following:
1. Crushing the tungsten trioxide contained waste SCR denitration catalyst into dry powder, and calcining under a high temperature;
2. Add the waste SCR denitration catalyst and ammonia in a sealed reactor and heated to 60~180°C;
3. Stand until the liquid-solid layers stratified after fully dissolved (for 5~15 hours), then collect the upper layer of serum;
4. The lower layer of solid residue and ammonia are added into the reactor, heating and collect the supernatant upper layer of serum;
5. Repeat steps 3 and 4 at least once;
6. Collect the upper layer of serum of tungsten trioxide component and evaporate to dryness and water is sufficiently dried, to obtain a solid;
7. Calcining the solid obtained in the step 6 under the high-temperature (conditions: 500~800°C, roasting time for 1~5 hours) to generate tungsten trioxide, thus completing the process of waste SCR denitration catalyst recycling tungsten trioxide.
Using this method, the recovery rate of tungsten trioxide can ensure up to 95%, and with high purity (98.5%), which can be directly re-used for the production of SCR denitration catalyst; in addition, the waste of resource is reduced which brings the positive implications of both economic and environmental protection.