Annealing, in metallurgy and materials science, is a heat treatment that alters the physical and sometimes chemical properties of a material to increase its ductility and reduce its hardness, making it more workable. It involves heating a material to above its recrystallization temperature, maintaining a suitable temperature, and then cooling.
In annealing, atoms migrate in the crystal lattice and the number of dislocations decreases, leading to the change in ductility and hardness.In the cases of copper, steel, silver, and brass, this process is performed by heating the material (generally until glowing) for a while and then slowly letting it cool to room temperature in still air. Copper, silver and brass can be cooled slowly in air, or quickly by quenching in water, unlike ferrous metals, such as steel, which must be cooled slowly to anneal. In this fashion, the metal is softened and prepared for further work—such as shaping, stamping, or forming.
Figure 1 exhibits the typical XRD patterns of the synthesized Cs0.33WO3 particles with the different annealing temperatures. All peaks could be indexed to the hexagonal cesium tungsten bronze (JCPDS No. 831334) and the only Cs0.33WO3 particle synthesized in annealing at 800 ℃ almost was identified to disappear the impurity peak. It can be seen that the nanoparticles obtained by annealing at 800 ℃ prefers the hexagonal tungsten bronze structure. It was well known that the relatively larger ions such as Ti (0.150 nm), Rb (0.152 nm), and Cs (0.170 nm) compared with Li, Na etc. could fit better in the hexagonal vacant tunnels (0.163 nm) in the hexagonal tungsten bronze structure rather than in the rectangular vacant tunnels in the cubic tungsten bronze structure. In the other hand, this result suggested that the typical hexagonal structure of Cs0.33WO3 with remarkable absorption of NIR was formed by annealing at 800 ℃.
A synthesis of Cs0.33WO3 particle with annealing temperature of 800℃ was morphology as measured by SEM. The Cs0.33WO3 particle under the 100 nm can be observed in Fig. 2. Each Cs0.33WO3 particle was aggregated with the mass of the few micron size. Those clusters shatter to pieces by pulverization dispersed methods. These results agree well with the XRD profiles of the samples shown in Fig. 1.
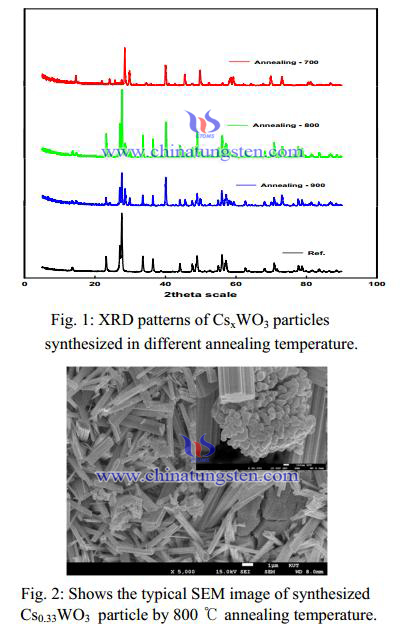