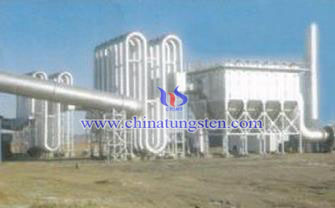
With SCR denitration power being constantly put into the plant large-scale construction projects, at the same time, the waste catalysts are increasing dramatically; on the other hand, the continuous development of science, high-tech demand for tungsten will be rising. Tungsten is a rare metal, the more we use, the less rest. For fully using the limited tungsten ore, recycling tungsten from waste SCR denitration catalyst has became urgent. There are many reachers both at home and abroad committed to study on this subject, and someone has proposed the secondary alkaline leaching method to recover tungsten trioxide, ammonium metavanadate, molybdenum and other precious metal oxides from waste SCR denitration catalysts. Steps are as following:
1. Crushing the waste catalyst into 80 mesh or more;
2. Removing impurities: soaking the powder with excessive water to make arsenic, Hg, alkali metal salts and organic matters dissolved in water, and then carrying out filtration, the wastewater can be recycle after removed impurities through activated carbon;
3. Leaching: adding excessive Na0H solution (concentration of 20~30%) into the powder, and heating to 80 °C, soaking for 1~2 hours to leach out most tungsten, molybdenum, and vanadium;
4. Recovering vanadium: Adjusting pH value to 1.7-1.8 with NH4Cl, and boiling for 1~2 hours to make vanadium precipitated, thus to recycle pure ammonium metavanadate;
5. Recovering molybdenum and tungsten : Tungsten and molybdenum respectively exist in the form of ammonium tungstate, ammonium molybdate; before adding calcium chloride solution, we supposed to adjust pH value to 4.5~5.0 by hydrochloric acid, then get the calcium tungstate, calcium molybdate, then dissolved by hydrochloric acid to obtain tungstic and molybdic acid;
6. Generating ammonium paratungstate by traditional methods, then calcined to recover tungsten trioxide.