Tungsten carbide milling cutters are more expensive than high speed steel, but last longer, and can be run much faster, so prove more economical in the long run. Tungsten carbide milling cutter selecting is not a simple task. There are many variables, opinions and lore to consider, but essentially the machinist is trying to choose a tool which will cut the material to the required specification for the least cost. There are four main factors to consider when selecting a tungsten carbide milling cutter.
I. Diameter:
Larger tools can remove material faster than small ones, therefore the largest possible cutter that will fit in the job is usually chosen. When milling an internal contour, or concave external contours, the diameter is limited by the size of internal curves. The radius of the cutter must be less than or equal to the radius of the smallest arc.
II. Flutes:
More flutes allows a higher feed rate, because there is less material removed per flute. But because the core diameter increases, there is less room for swarf, so a balance must be chosen.
III. Coating:
Coatings, such as titanium nitride, also increase initial cost but reduce wear and increase tool life. TiAlN coating reduces sticking of aluminium to the tool, reducing and sometimes eliminating need for lubrication.
IV. Helix angle:
High helix angles are typically best for soft metals, and low helix angles for hard or tough metals.
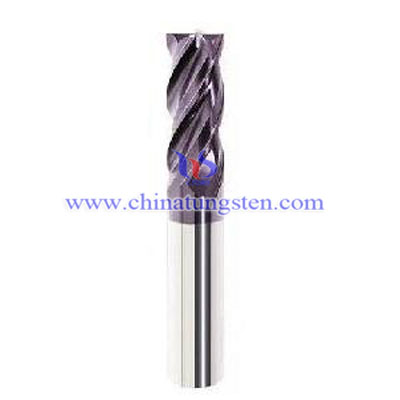
Tungsten Manufacturer & Supplier: Chinatungsten Online - http://www.chinatungsten.com
Tel.: 86 592 5129696; Fax: 86 592 5129797
Email: sales@chinatungsten.com
Tungsten & Molybdenum Information Bank: http://i.chinatungsten.com
Tungsten News & Tungsten Prices, 3G Version: http://3g.chinatungsten.com
Molybdenum News & Molybdenum Price: http://news.molybdenum.com.cn