Recovery of Tungsten from SCR Catalysts as Ammonium Paratungstate
- Details
- Category: Tungsten Information
- Published on Tuesday, 06 July 2021 01:40
In order to recycle expensive rare metals such as V2O5 and WO3, a method of separating and recovering solid oxide particles by leaching it in a liquefied form is available. Tungsten has been recovered from SCR catalysts as the form of ammonium paratungstate (APT), the recovery rate as high as 96.0% could be obtained. The SCR catalysts contains 1.23% V2O5 and 7.73% WO3.
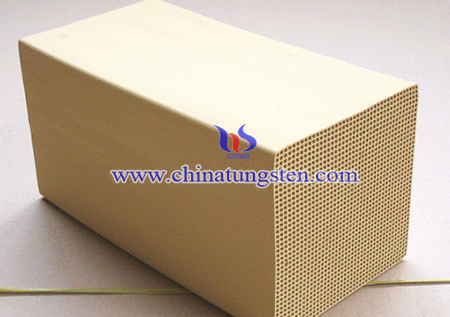
The recovery process of tungsten to produce ammonium paratungstate is as following steps: Pressure leaching process: Under a 1000 rpm condition, the spent SCR catalyst and sodium hydroxide (NaOH, Yakuri Pure Chemicals Co. LTD, 96.0%) were subjected to the pressure leaching process in an autoclave. The reaction was conducted under the following conditions: leaching reaction time maintained for 1, 2, 6, 12, and 24 h at under 200, 250, 300, and 350 °C with a heating rate of 200 °C/h. In addition, sodium carbonate (Na2CO3, 99.0%) was used as an additive. In order to separate the leaching solution and residue, the solution was dried after filtering. The V and W contents in the leaching solution were analyzed by using an inductively coupled plasma optical emission spectrometer.
The calcium precipitation process was used to separate V and W in the leaching solution. Sonicated calcium hydroxide (Ca(OH)2, 96.0%) was stirred with the leaching solution after mixing it with distilled water. After separating the residue and leaching solution again through filtration followed by stirring, 2 M NH4OH was added to the leaching solution and stirred for 2 h. After drying followed by evaporation, APT was manufactured and its properties were analyzed using an X-ray diffraction (XRD, D/Max-2500 model of Rigaku Co.) at a scan rate of 3°/min and a scan range of 10 degrees within the range of 70 degrees.
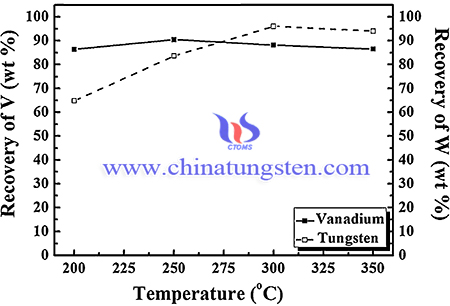
In conclusion, Tungsten has been recovered from SCR catalysts containing 1.23% V2O5 and 7.73% WO3 as the form of ammonium paratungstate (APT), the recovery rate as high as 96.0% could be obtained. optimize the recovery of the rare metals V and W from spent SCR catalyst. Depending on the reaction temperature, the recovery of W increased from 64.8 to 96.0%. At the NaOH concentration of 2 M, the maximum recovery of W was obtained. Na2CO3 had disadvantages compared with NaOH; By reacting NaWO4 with ammonia solution, ammonium tungstate solution was prepared and converted to APT through evaporation. To increase the purity of W, the ammonium solution (MgCl2 + NH4OH) can be used to remove residues. The soda digestion process was used to convert the insoluble V2O5 and WO3 to water-soluble NaVO3 and Na2WO4, respectively. The factors affecting the reaction during pressure leaching were the reaction temperature, time, additive agent, the L/S ratio, and NaOH concentration.
- APT Manufacturer & Supplier, Chinatungsten Online: ammonium-paratungstate.com
- Tungsten News & Prices of China Tungsten Industry Association: www.ctia.com.cn
- Molybdenum News & Price: news.molybdenum.com.cn
- Tel.: 86 592 5129696; Fax: 86 592 5129797; Email: sales@chinatungsten.com