【知钨】钨铜常用配比
- 详细资料
- 分类:钨业知识
- 发布于 2017年5月18日 星期四 18:52
- 作者:tang
- 点击数:686
钨铜合金供应商:中钨在线科技有限公司 | 产品详情: http://www.tungsten-copper.com |
电话:0592-5129696 传真:5129797 | 电子邮件:sales@chinatungsten.com |
钨钼文库:http://i.chinatungsten.com | 钨钼图片: http://image.chinatungsten.com |
钨新闻3G版:http://3g.chinatungsten.com | 钼业新闻: http://news.molybdenum.com.cn |
微博

微信

硬质合金挤压成形与注射成形的工艺异同
- 详细资料
- 分类:钨业知识
- 发布于 2017年5月18日 星期四 16:53
- 作者:ruibin
- 点击数:1935
硬质合金粉末挤压成形( Powder Ex-trusion Molding, PEM) 和硬质合金注射成形( Powder Injection Molding, PIM) 是传统塑料成形工艺与粉末冶金技术相结合的产物。用挤压成形技术可生产等断面而长度不受限制的异形件, 用粉末注射成形技术可生产几何形状复杂的制品。这两种方法之间有许多相同点和不同处。
1.工艺流程的异同
硬质合金的PEM与PIM的基本工艺过程如下:粉末体+ 成形剂→混炼→挤压或注射成形→脱除成形剂→烧结。这两种过程均为混炼一成形脱脂一烧结工艺过程。
2.脱脂工艺的异同
硬质合金注射成型与挤压成形中, 由于加入了大量的添加剂,需要将增塑剂及粘接剂等进行脱除。脱除的方法根据所采用的添加剂不同, 主要采用热脱除法、溶剂萃取法、溶解法、热分解法、催化脱除法等, 有的脱除工艺还采用了混合脱除技术。这两者的脱脂工艺没有本质不同,只是在具体工艺上有所区别。由于金属注射成型所采用的粉末粒度较小, 因此粘接剂与金属粉体的接触面积更大, 粘接剂的脱除也较金属注射成型的脱除工艺困难。(下图为常见的脱脂工艺)
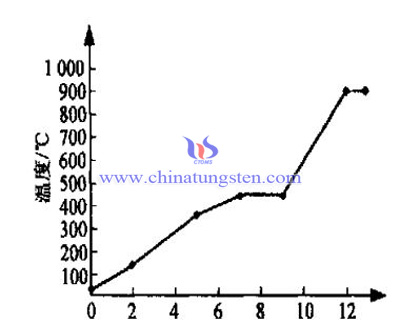
3.烧结工艺的异同
由于硬质合金挤压成形与注射成形所用的成型剂基本相同,这也导致这两者在烧结工艺控制上比较一致,即碳含量控制工艺较为一致。另外硬质合金具体的烧结工艺受牌号和其它因素影响更大,所以这两者的烧结工艺基本一致。
硬质合金供应商:中钨在线科技有限公司 | 产品详情: http://www.tungsten-carbide.com.cn |
电话:0592-5129696 传真:5129797 | 电子邮件:sales@chinatungsten.com |
钨钼文库:http://i.chinatungsten.com | 钨钼图片: http://image.chinatungsten.com |
钨新闻3G版:http://3g.chinatungsten.com | 钼业新闻: http://news.molybdenum.com.cn |
微博

微信

硬质合金压坯形位公差超差
- 详细资料
- 分类:钨业知识
- 发布于 2017年5月18日 星期四 16:50
- 作者:ruibin
- 点击数:1729
硬质合金制品由于自身特点,在烧结后的加工余量不能太大,所以就必须要求在烧结前的压坯尺寸得到较好的控制。对硬质合金压坯尺寸的控制除了基本尺寸的控制之外,更须对形位公差进行较好的控制。形位公差包括形状公差和位置公差。不同的产品要求的形位公差项目不同,如对表面要求较高的制品,对平面度的要求较高;如硬质合金棒材对直线度、同轴度的要求较高。形位公差超差也是硬质合金生产中一个很严重的缺陷类型,直接影响制品的实际使用状态,所以必须对形位公差超差进行改善。
1. 直线度
产生直线度超差的原因及改善措施有:
1.1 模具的直线度超差。可以通过模具的休整和适当的机加予以改善。
1.2 压坯密度分布不均匀。如顶后压工艺造成的柱体锥度,虽然可以通过工艺控制能得到一定的缓解,但超差依然会存在,这是模压工艺自身的特点造成的。如果工艺控制不能解决,可以通过后续的机加工予以改善。
1.3 压坯的壁厚不均匀等造成的直线度超差。与前两者类似,可通过工艺和后续机加予以改善。
2. 平行度
产生平行度超差的原因有: 模具的平行度超差,装粉不均匀等。
3.同轴度
产生同轴度超差的原因有: 模具的精度超差压制工装及设备精度低模具安装不符合要求装粉不均匀等。
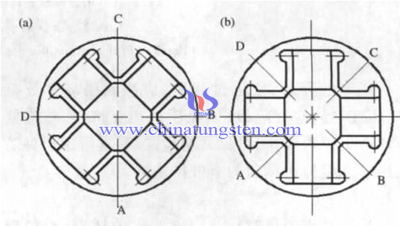
在粉末流速适当模具精度符合设计要求压制工装及设备精度满足安装要求的情况下,形位公差主要与压坯的密度分布有关,在压制方式确定的情况下,压坯密度的分布直接与充粉效果有关。图(a)、图(b)所示为同一零件的2种装粉方向。图(a)以对角方式装粉,压坯壁厚差为0.05-0.10mm;图(b)以对边方式装粉,压坯壁厚差<0.04mm。
硬质合金供应商:中钨在线科技有限公司 | 产品详情: http://www.tungsten-carbide.com.cn |
电话:0592-5129696 传真:5129797 | 电子邮件:sales@chinatungsten.com |
钨钼文库:http://i.chinatungsten.com | 钨钼图片: http://image.chinatungsten.com |
钨新闻3G版:http://3g.chinatungsten.com | 钼业新闻: http://news.molybdenum.com.cn |
微博

微信

硬质合金挤压成形剂体系
- 详细资料
- 分类:钨业知识
- 发布于 2017年5月18日 星期四 16:51
- 作者:ruibin
- 点击数:1834
硬质合金挤压成形与模压成形或等静压成形相比,其最大的特点是喂料中成形剂体积分数含量高,可以达到40%一60%,成形剂作为挤压成形中粉末的临时载体,主要起增强喂料流动、维持挤出棒坯形状的作用,是挤压成形技术的核心。在硬质合金挤压成形应用之初,单纯采用蜡作为成形剂随着研究的深入,成形剂不断向多元化发展。目前,根据成形剂组元的性质,常用的成形剂体系通常可分为热塑性体系、热固性体系、水溶性体系、凝胶体系等。(下图为常见的挤压设备)
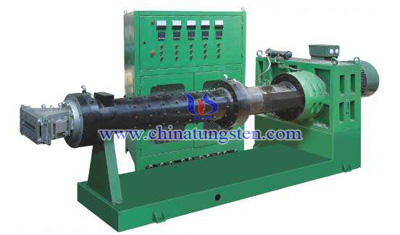
1.热塑性体系
热塑性体系成形剂以热塑性有机物作为成形剂主体,根据成形剂中主体组元的不同,其又可细分为蜡基系、油基系、塑基系等。目前蜡基系成形剂的研究较为成熟,已成为最有竞争力的成形剂体系。
2.热固性体系
热固性体系成形剂以热固性高分子作为成形剂主体组元,利用挤出后高分子的固化来维持挤出棒坯形状热固性体系成形剂的优点是挤出棒坯强度高,在脱脂过程中能够提高棒坯的保形性,可以以较快的加热速率进行热脱脂
3.水溶性体系成形剂
水溶性体系成形剂的主体是以水溶性的高分子,其主要优点是成形剂可用水进行脱除,从而避免了有机溶剂的使用。如聚乙二醇、聚丙烯酸
、聚丙烯酸钠、聚甲基丙烯酸甲酷等。
4.凝胶体系成形剂
凝胶体系成形剂一般以改性纤维素、改性淀粉、海藻酸盐和琼脂等作为成形
剂主体组元
硬质合金供应商:中钨在线科技有限公司 | 产品详情: http://www.tungsten-carbide.com.cn |
电话:0592-5129696 传真:5129797 | 电子邮件:sales@chinatungsten.com |
钨钼文库:http://i.chinatungsten.com | 钨钼图片: http://image.chinatungsten.com |
钨新闻3G版:http://3g.chinatungsten.com | 钼业新闻: http://news.molybdenum.com.cn |
微博

微信

硬质合金压坯尺寸超差
- 详细资料
- 分类:钨业知识
- 发布于 2017年5月18日 星期四 16:47
- 作者:ruibin
- 点击数:1884
硬质合金压坯在压制过程中经常会出现尺寸超差的情况,这一方面是跟工艺控制水平有关,另一方面也是压制过程质量控制的难点所在。如果按照压坯的空间尺度来划分,硬质合金压坯尺寸超差无外乎两种情况:一是径向尺寸超差;二是高度(轴向)尺寸超差。实际生产时根据超差类型和原因予以调整。
1.径向尺寸超差
可能是模具设计或制造有问题 如果误差可以通过调整工艺( 即通过调整粉料成分压坯密度烧结工艺等) 消除,还可补救,否则只有报废模具。另外如果增塑坯,可以通过适当的机加工进行消除。
2.高度尺寸超差
2.1 无台阶柱面压坯
2.1.1 可以通过调整装粉改变压制压力,延长保压时间,可调整和稳定轴向尺寸;
2.1.2 可以通过调整成形高度,装粉量调整轴向尺寸;
2.1.3 可以通过调整顶后压的大小,进而调节压坯的密度分布,进而改变轴向尺寸
2.2 台阶压坯
2.2.1 调整冲头位置。由于粉末的横向流动,各模冲的弹性变形量不同,将影响压坯的厚度 因而在模具设计时应尽量将模冲设计成可调的形式。
2.2.2 调整各台阶装粉比。理论上各台阶的装粉要按照压缩比相等原则来计算。但实际上装粉不均匀是不可避免的,加之粉料的不稳定性,使得实际装粉比与计算值之间存在一定的误差,因而在模具设计时应尽量有调节装粉机构。
2.2.3 浮动模冲速度
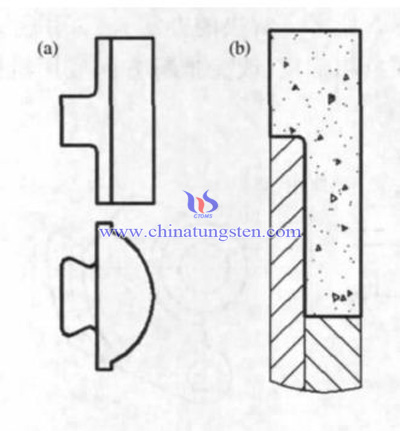
图(a) 所示的镶块制品,其装粉方式如图(b) 所示 浮动模冲运行速度的变化会引起粉末的流动,从而导致台阶尺寸及密度发生变化 若下浮动模冲移动过早过快,会使得此处密度过大尺寸厚;反之相反。这其实是上冲与下冲(浮动冲头)的速度差导致的压坯密度变化。浮动模冲的运行速度,主要取决于模具结构。如下拉式压机模架有粉末移送系统,可根据压坯的密度及尺寸情况方便地调节; 对于无粉末移送系统的模具,只能依靠浮动模冲的浮动力大小来调节,也能起到同样的效果,不过稳定性要略差。
硬质合金供应商:中钨在线科技有限公司 | 产品详情: http://www.tungsten-carbide.com.cn |
电话:0592-5129696 传真:5129797 | 电子邮件:sales@chinatungsten.com |
钨钼文库:http://i.chinatungsten.com | 钨钼图片: http://image.chinatungsten.com |
钨新闻3G版:http://3g.chinatungsten.com | 钼业新闻: http://news.molybdenum.com.cn |
微博

微信
