碳化钨粉末球磨转速
- 详细资料
- 分类:钨业知识
- 发布于 2017年5月10日 星期三 19:44
- 作者:ruibin
- 点击数:2108
钨粉与碳粉混合:碳化钨粉末质量决定于钨粉与炭黑混合的均匀程度,如果物料混合不均匀,碳化 钨粉末将出现黑心和分层现象。在硬质合金生产工艺中,一般将钨粉与炭黑在球磨机内进行混合(球料比为1:1,钢球直径为35~50mm),球磨时间为2~4h,用肉眼观察物料无分层现象即算混合均匀。
碳化钨粉末球磨:球磨在球磨机中进行。球料比为1:1,钢球直径为10~45mm,球磨时间根据工艺要 求而定,一般为2h。为了防止粉末飞扬,过筛应在封闭情况下进行,细颗粒碳化钨过200目筛,中颗粒碳化钨过250目筛,粗颗粒碳化钨过60目筛。下表为碳化钨球磨、过筛工艺表:
球磨机的合理转速应该处于最低转速和临界转速之间。所谓临界转速,就是合金球在此转速下不再脱离磨筒内壁,此时合金球所受的离心力大于重力在径向的分力。球磨机在运行时由于转速的不同会导致物料会在磨筒内呈现不同的状态
1、转速过低:研磨强度低,且物料没有上升研磨过程,部分料会堆积在底部,无法充分研磨
2、转速过高:研磨作用不充分,类似于搅拌效果
3、转速合理:物料沿球面方向与研磨球充分接触,研磨效果好
如下图所示
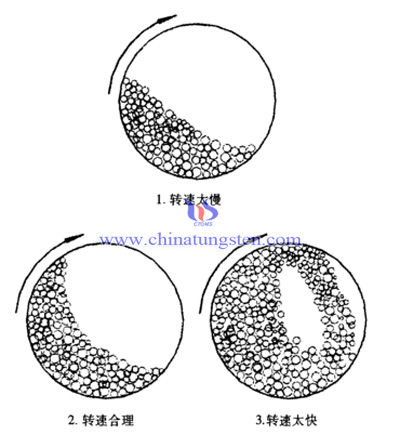
临界转速由下面公式给出:
n临界=42.4/D0.5
n临界-球磨机的转速(r/min);
D-球磨机内径(m)。
生产过程中证明,球磨机转速在60%-75%之间时,球磨效率最高。
球磨工艺参数
填充系数:球磨筒的内容积与所装物料、合金球的体积之比,一般选择0.45-0.5。
球料比:研磨球(硬质合金生产中常用硬质合金球)与粉末原料的质量比。
固液比:原料粉末的质量与液体介质的质量比,WC粉末破损过程中没有添加液。
硬质合金供应商:中钨在线科技有限公司 | 产品详情: http://www.tungsten-carbide.com.cn |
电话:0592-5129696 传真:5129797 | 电子邮件:sales@chinatungsten.com |
钨钼文库:http://i.chinatungsten.com | 钨钼图片: http://image.chinatungsten.com |
钨新闻3G版:http://3g.chinatungsten.com | 钼业新闻: http://news.molybdenum.com.cn |
微博

微信

注射过程的压力损失
- 详细资料
- 分类:钨业知识
- 发布于 2017年5月10日 星期三 19:34
- 作者:ruibin
- 点击数:2025
物料通过料筒的压力损失主要体现在物料内摩擦和与筒壁、模腔的外摩擦上和压紧料粒两种方面上。影响压力损失的因素主要有:注射速率、料筒(喷嘴)内径,料筒(或喷嘴)长度,料温等。
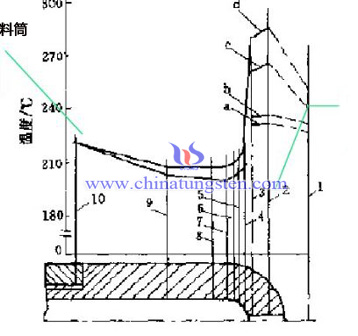
一、压力损失
1.料筒内压力损失-摩擦力损失(如上图所示)
对于柱塞式注射系统,压紧粒料的压力降损失值Δp可以用下式近似得出:
ΔPg=p0(1-e-4fL/R)(1)
式中,p0...注射压力;
R....筒壁内直径;
L....物料区长度;
f....料粒与筒壁的摩擦系数;
2.料筒内压力损失-压紧压力损失
当螺杆或柱塞将物料推向喷嘴,熔料经过料筒时的压力降可由牛顿流体的体积流率的公式进行估算:
qv=πΔpR4/8ηL (2)
ΔPl=8ηLqv/πR4(3)
式中,qv...熔料通过料筒的体积流率;
R...料筒内壁半径;
η...牛顿流体剪切粘度;
L...熔料在料筒的长度。
物料在料筒中的压力损失:ΔP=ΔPg+ΔPl,熔料在喷嘴中的压力损失机理与在料筒中类似,计算过程也一样。
3、喷嘴中的压力损失
熔料在喷嘴中的压力损失机理与在料筒中类似,计算过程也一样。
二、影响压力损失的因素
1、注射速率,由公式(2)可知,注射速率升高,qv升高,ΔPl增大;
2、料筒(或喷嘴)内径,由公式(1)(3)可知,R增大,ΔPg和ΔPl也随之增大;
3、其它条件一定时,喷嘴长度增加,ΔPg和ΔPl也随之增大;
4、温度对压力损失的影响主要是通过改变熔料的剪切粘度;当然从另外一个角度看,注射压力的变化也会导致熔料温度的变化。
硬质合金供应商:中钨在线科技有限公司 | 产品详情: http://www.tungsten-carbide.com.cn |
电话:0592-5129696 传真:5129797 | 电子邮件:sales@chinatungsten.com |
钨钼文库:http://i.chinatungsten.com | 钨钼图片: http://image.chinatungsten.com |
钨新闻3G版:http://3g.chinatungsten.com | 钼业新闻: http://news.molybdenum.com.cn |
微博

微信

注射成型塑化过程
- 详细资料
- 分类:钨业知识
- 发布于 2017年5月10日 星期三 19:29
- 作者:ruibin
- 点击数:2206
粉末冶金注射成形过程包括:加料、塑化、注射、保压、制件冷却、制件脱模、制件修整等几个步骤,所谓塑化是指聚合物-粉末混合物在料筒内经加热(外加热、剪切发热)转化为聚合物粘流态,称为具有一定流动性和可塑性熔料的过程。塑化过程是成形前期的准备过程,也称为预塑过程,塑化质量和效率对后续的注射成形过程和制品质量起着及其重要的影响。
要求
MIM(粉末注射成形)对塑化过程的控制其实是对熔料的性能的要求。熔料必须具备以下特点:
1、物料完全熔融,即有机聚合物要达到粘流态温度以上,成为具有流动性的粘流态熔料;
2、熔料不发生热分解现象,即温度不能高于组分的热分解温度;
3、物料得到充分的混合,温度分布均匀,不存在偏聚情况。
衡量指标
1.料温均匀性,熔料温度的均匀性程度直接影响制品质量优劣,是衡量塑化过程的重要指标。料筒的外加热会在物料的径向方向产生较大的温度梯度,通过螺杆的搅拌剪切使温度得以均匀化。
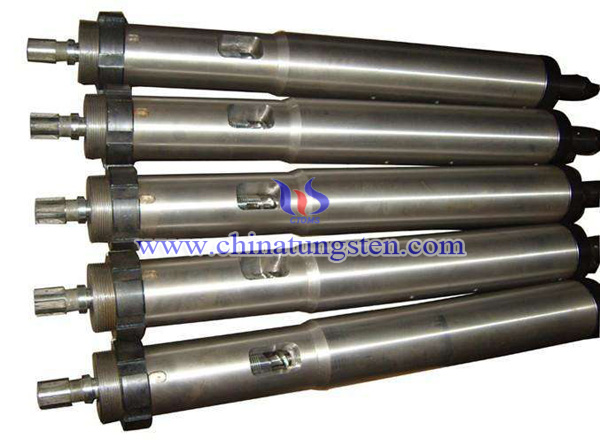
2.加热系数,是指料筒加热的有效利用率,用以衡量外加热效率。塑化过程的热量来源有两种(针对螺杆注射系统),料筒通过电热元件从外部加热,料筒内的物料能通过横截面方向及长度方向上产生很大的温度梯度,上图为常见注射料筒;2.物料靠螺杆旋转作用,通过剪切机理和摩擦机理生热。可以用下式进行量化:
E=Tt-To/(Tl-To)
式中,E...加热系数,不应小于0.8;
Tt..物料经塑化后的温度;
To..物料的初始温度;
Tl..料筒的温度
硬质合金供应商:中钨在线科技有限公司 | 产品详情: http://www.tungsten-carbide.com.cn |
电话:0592-5129696 传真:5129797 | 电子邮件:sales@chinatungsten.com |
钨钼文库:http://i.chinatungsten.com | 钨钼图片: http://image.chinatungsten.com |
钨新闻3G版:http://3g.chinatungsten.com | 钼业新闻: http://news.molybdenum.com.cn |
微博

微信

塑化剪切作用
- 详细资料
- 分类:钨业知识
- 发布于 2017年5月10日 星期三 19:32
- 作者:ruibin
- 点击数:2543
注射成形的塑化过程其实对物料的混合分散(针对多组分物料)和加热的过程,混合分散过程主要是由螺杆的旋转搅拌实现的。而加热过程的热量来源有两种,料筒通过电热元件从外部加热,料筒内的物料能通过横截面方向及长度方向上产生很大的温度梯度;2.物料靠螺杆旋转作用,通过剪切机理和摩擦机理生热(柱塞注射系统无此过程)。
对于多组分物料,螺杆对物料的剪切作用主要体现在三个方面:
1、进一步混合分散
2、挤压充实,排出气体
3、对物料进行加热

剪切热效应来源
螺杆的剪切热效应是螺杆最为重要的作用之一(上图为剪切数学模型),它直接影响了物料的塑化质量。从产生机理上讲,螺杆旋转,带动熔体运动,熔体与螺杆表层摩擦生热,同时不同流层分子链内摩擦发热。对于常见的粉末注射聚合物体系,其高聚物体系通常为非牛顿流体,其剪切应力与切变速率不成正比,计算较为复杂,通常简化为牛顿流体计算。剪切热推理公式如下:
1.热量计算,单位时间,单位体积熔料的热量由应力作用产生,
Q=τγ(1)
2.剪切应变计算,为简化计算,按牛顿流体处理
γ=τ/η(2)
3.综合(1)(2)两式,可得出剪切热的计算公式
Q=ηγ2(3)
4.对于螺杆注射机,
γ=πDn/60h(4)
式中 τ...剪切应力;
γ...剪切应变;
η...流体的剪切粘度;
D...螺杆直径;
n...螺杆转速;
h...螺槽深度。
实际生产中由于是非牛顿流体,其计算要更为复杂,但规律基本一致。
从(3)(4)熔料吸收的热量与螺杆直径和螺杆转速的平方成正比,与螺杆深度成反比,而且熔体的粘度越大,其吸收的热量越多。螺杆转速越高,塑化能力越强。塑料的熔融,大体是因螺杆旋转所产生的热量,因此螺杆转速太快,则有下列影响:1.塑料的热裂解;2.使螺杆或螺缸磨损加速
硬质合金供应商:中钨在线科技有限公司 | 产品详情: http://www.tungsten-carbide.com.cn |
电话:0592-5129696 传真:5129797 | 电子邮件:sales@chinatungsten.com |
钨钼文库:http://i.chinatungsten.com | 钨钼图片: http://image.chinatungsten.com |
钨新闻3G版:http://3g.chinatungsten.com | 钼业新闻: http://news.molybdenum.com.cn |
微博

微信

注射成型的加热控制
- 详细资料
- 分类:钨业知识
- 发布于 2017年5月10日 星期三 19:29
- 作者:ruibin
- 点击数:1669
注射成形的塑化过程其实对物料的混合分散(针对多组分物料)和加热的过程,混合分散过程主要是由螺杆的旋转搅拌实现的。而加热过程的热量来源有两种,料筒通过电热元件从外部加热,料筒内的物料能通过横截面方向及长度方向上产生很大的温度梯度;2.物料靠螺杆旋转作用,通过剪切机理和摩擦机理生热(柱塞注射系统无此过程)。
料筒加热机理
料筒对物料的加热主要是通过物料与料筒的接触热传导实现的。由于热传导的前提是有温度差,故通常加热时,料筒温度要高于熔料的粘流态转化温度。此过程的量化计算可以根据传导传热的基本方程式----傅立叶定律,进行计算,如下式:
dQ=-λdA•dt/dn……(1)
式中 Q-----导热速率,w;
A------导热面积,m2;
dt/dn-----温度梯度,K/m;
λ------比例系数,称为导热系数,w/m•K。
加热控制因素
由上式可知,影响单位时间内物料吸收的热量主要有三个因素:
1、导热面积,即接触面积。其实对于圆柱形料筒中的物料而言,更准确的说法是物料的比表面积。物料的比表面积越大(与料筒接触部分),加热速度越快。故在设计料筒时,应充分考虑到料筒的直径对加热过程的影响。
2、温度梯度,主要取决于初末温差和料筒直径。初末温差大,加热速度快,所以在合理的温度区间适当提高料筒温度,有利于加热效率的提升,但会增加耗能。直径越大,内外层温差越大,加热不均匀性越大,这种不均匀可通过螺杆的机械旋转搅拌予以消除。
3、导热系数。导热系数λ的值越大,表示其导热性能越好。对于多组分熔料,液相(或者流动态)比例越高,其导热系数越大。所以在设计聚合物体系时,要充分考虑高低熔点组分的比例。
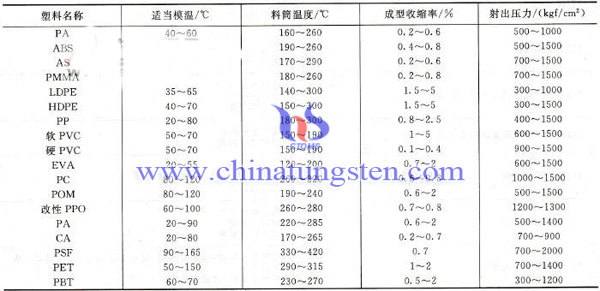
硬质合金供应商:中钨在线科技有限公司 | 产品详情: http://www.tungsten-carbide.com.cn |
电话:0592-5129696 传真:5129797 | 电子邮件:sales@chinatungsten.com |
钨钼文库:http://i.chinatungsten.com | 钨钼图片: http://image.chinatungsten.com |
钨新闻3G版:http://3g.chinatungsten.com | 钼业新闻: http://news.molybdenum.com.cn |
微博

微信
