硬质合金催化脱脂炉
- 详细资料
- 分类:钨业知识
- 发布于 2017年5月12日 星期五 16:41
- 作者:ruibin
- 点击数:1569
硬质合金催化脱脂炉是注射成型硬质合金进行催化脱脂反应的设备。催化脱脂炉一般由催化反应炉、催化剂加入机构、惰性气体供应机构和废弃处理机构等几部分组成。
催化脱脂炉根据其是否能实现连续化生产可分为两种:一种是非连续催化脱脂炉, 一种是连续催化脱脂炉。非连续催化脱脂炉主要用于实验室和小规模的工业生产;大规模的注射成形催化脱脂工业生产中应用的主要是连续催化脱脂炉, 能实现注射成形的自动化连续生产, 大大降低了
注射成形的成本。
非连续催化脱脂炉
非连续催化脱脂炉(如下图所示)由催化反应炉、催化剂加人装置、惰性气体供应装置和废气处理装置等几部分组成如下图所示。非连续炉可根据不同材料和在炉中的装载量, 调节温度和催化剂浓度, 很容易控制脱脂速度;载体氮气中的解聚产物甲醛在废气处理装置中氧化燃烧。
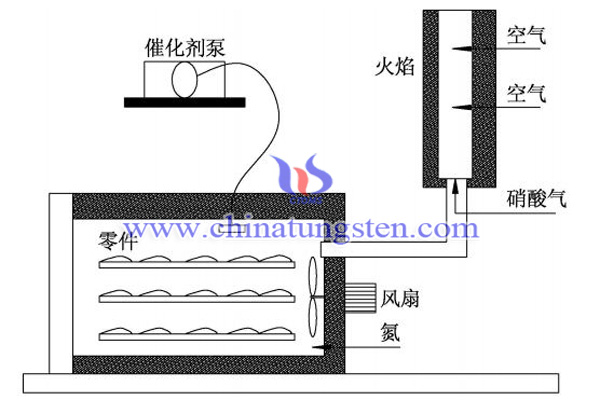
连续催化脱脂炉
由于催化脱脂速率快、时间短, 使得注射成形工业中采用连续脱脂和烧结成为可能。连续催化脱脂炉结合连续烧结炉运用于注射成形连续生产线上,实现了注射成形的自动化连续生产, 降低了注射成形的生产成本, 大大提高了注射成形这一近净成形方法的竞争力。
硬质合金供应商:中钨在线科技有限公司 | 产品详情: http://www.tungsten-carbide.com.cn |
电话:0592-5129696 传真:5129797 | 电子邮件:sales@chinatungsten.com |
钨钼文库:http://i.chinatungsten.com | 钨钼图片: http://image.chinatungsten.com |
钨新闻3G版:http://3g.chinatungsten.com | 钼业新闻: http://news.molybdenum.com.cn |
微博

微信

催化脱脂率影响因素
- 详细资料
- 分类:钨业知识
- 发布于 2017年5月12日 星期五 16:38
- 作者:ruibin
- 点击数:2040
催化脱脂的脱脂程度收到多方面的影响,最常见的影响有粘结剂组分、催化气体流量、脱脂时间、脱脂温度这几种。
评价脱脂过程的程度主要是用脱脂率来衡量,其计算公式如下:
Wd%=(Wi-W)/Wi×100
式中:
Wi 是注射坯中原始粘结剂的重量(g);
W是脱脂坯中残留粘结剂的重量(g)。
1.粘结剂组分对催化脱脂率的影响(如下图所示)
注射成形催化脱脂过程的关键因素是粘结剂在特定酸性气氛下的快速分解, 为此在注射成形粘结剂中必须含有能在特定的酸性气氛下发生快速降解的组分。同时为保证聚醛树脂脱除后坯体能保证一定强度,需要添加其他辅助组分。在催化脱脂型粘结剂中, 聚醛树脂的含量越多, 注射坯中粘结剂的脱除率越高, 但脱脂坯的保形性越差。所以需要组分达到一个平衡值。
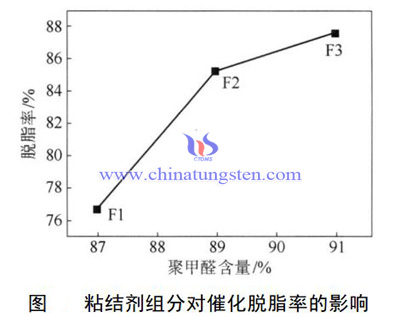
2.催化气体流量对催化脱脂率的影响
催化脱脂过程中通常会在脱脂炉中引入高速惰性气流(氮气、氩气、氦气及其混合物)以加速小分子的扩散,调节脱脂速率。通过控制催化剂的浓度可以控制脱脂速率。而且随着惰性气体流动速率的降低, 脱脂区的催化剂浓度增加, 整个脱脂速率增加。因此, 惰性气流的流动速率要控制在适中的范围内。但是H酸性气体的流量也不能太大,比如HNO3,如果HNO3浓度太大催化气体会具有一定的腐蚀性, 会对粉末和设备造成危害。
3.脱脂时间对催化脱脂率的影响
催化脱脂率和脱脂时间的关系, 随着催化脱脂时间增加, 注射成形坯脱脂量增加, 而且随着时间增加, 脱脂量增加趋势变平稳, 这一变化趋势与热脱脂时脱脂量随脱脂时间的变化规律不同。
4.脱脂温度对催化脱脂率的影响
催化脱脂率随脱脂温度的升高而增加。主要是由于聚甲醛在酸性作用下是由末端开始进行逐步分解的, 随着反应温度的增加,这种解聚反应的速度增加, 因此脱脂速率增大。
硬质合金供应商:中钨在线科技有限公司 | 产品详情: http://www.tungsten-carbide.com.cn |
电话:0592-5129696 传真:5129797 | 电子邮件:sales@chinatungsten.com |
钨钼文库:http://i.chinatungsten.com | 钨钼图片: http://image.chinatungsten.com |
钨新闻3G版:http://3g.chinatungsten.com | 钼业新闻: http://news.molybdenum.com.cn |
微博

微信

注射成型硬质合金催化脱脂原理
- 详细资料
- 分类:钨业知识
- 发布于 2017年5月12日 星期五 15:29
- 作者:ruibin
- 点击数:2395
注射成型硬质合金催化脱脂的脱脂原理是利用一种催化剂把有机载体分子解聚为较小的可挥发的分子, 这些分子比其它脱脂过程中的有机载体分子有较高的蒸气压, 能迅速地扩散出坯体。注射成型硬质合金催化脱脂工艺所采用的粘结剂体系一般是由聚醛树脂、起辅助框架作用的聚合物和起稳定作用的添加剂组成.
聚醛树脂
其中聚醛树脂的结构特点是重复的C-O键组成, 如图1所示。具有较强的粘接力、高光泽、高硬度和优良的耐候性、耐化学品性。常用于用作增黏树脂,提高粘接力和硬度。
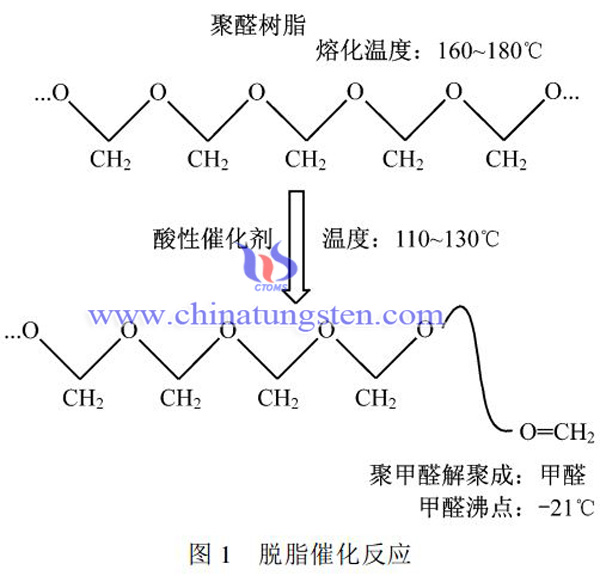
反应过程(如上图所示)
聚合物链的氧原子对酸的作用很敏感,当曝露在合适的酸催化剂中时, 在较低的温度下就能进行催化反应引起大分子聚醛树脂分裂成CH2O(甲醛)气体。一般用于注射成型硬质合金催化脱脂过程中的催化剂气体是硝酸和草酸气体。在110℃~130℃温度范围注射成型硬质合金催化脱脂的速率可以达到很高, 而该温度范围远低于聚醛树脂的熔化区间(160~180℃)。这种催化反应发生的条件特别适合于粉末注射成形中的粘结剂的脱除。这样, 生坯中的主粘结剂――聚醛树脂在催化剂的作用下直接由固态裂解为气态小分子, 达到快速注射成型硬质合金催化脱脂的目的。此时, 剩余的少量(低于10%)聚合物将起保形作用, 脱除了主粘结剂的生坯仍然是充分坚固的, 使零件在脱粘时具有延续的坚硬性, 避免任何塑性变形, 得到较好的公差。气态酸不透过粘结剂, 反应只是在气体与粘结剂的界面上进行。气体的扩散限制在已形成的多孔外壳上, 在生坯内部不会形成压力。而这些在生坯中残留的有机物质、分解剂、某些聚合物均可以在预烧结阶段迅速热解脱除。反应方程如下:
〖(CH_2-O)〗_2 □(→┴(acid(T>100℃)) nCH_2=O)
硬质合金供应商:中钨在线科技有限公司 | 产品详情: http://www.tungsten-carbide.com.cn |
电话:0592-5129696 传真:5129797 | 电子邮件:sales@chinatungsten.com |
钨钼文库:http://i.chinatungsten.com | 钨钼图片: http://image.chinatungsten.com |
钨新闻3G版:http://3g.chinatungsten.com | 钼业新闻: http://news.molybdenum.com.cn |
微博

微信

注射成型硬质合金脱脂催化剂的选择
- 详细资料
- 分类:钨业知识
- 发布于 2017年5月12日 星期五 16:35
- 作者:ruibin
- 点击数:1623
注射成型硬质合金催化脱脂速率由于反应机理的优势,远高于传统的注射成型硬质合金脱脂技术。
催化速率
催化反应仅在气体—粘结剂界面上进行,由生坯外部逐渐向内部发展, 催化脱脂从外向内的脱脂机制不产生裂纹和孔洞, 并且可以得到很高的脱脂速率。气体粘结剂界面向内部的移动速率为2-4mm/h, 远高于传统的脱
脂技术。而一般粘结剂为基的注射成形坯的脱脂速率为0.2mm/h, 催化脱脂速率是传统脱脂工艺速率的10~20倍。粘结剂组分、催化气体流量、脱脂时间和脱脂温度具会对催化脱脂率的影响,呈正相关关系。
注射成型硬质合金脱脂催化剂的选择
注射成型硬质合金脱脂催化脱脂过程中可在脱脂炉中引入高速惰性气流(氮气、氩气、氦气及其混合物)以加速小分子的扩散, 调节脱脂速率。通过控制催化剂的浓度可以控制脱脂速率。而且随着惰性气体流动速率的降低,脱脂区的催化剂浓度增加, 整个脱脂速率增加。因此, 惰性气流的流动速率要控制在适中的范围内。对于大多数陶瓷注射成型(CIM)粉末原料而言, 硝酸是合适的催化剂。硝酸具有强氧化性和很强的气化倾向,在正常的脱脂条件下, 硝酸蒸气不会沉积在脱除有机载体后的陶瓷零件的毛细管孔内,不会腐蚀炉子结构。对于因氧化而形成硝酸盐的粉末如Y2O3(烧结Si3N4 和SiC的添加剂)等, 草酸是可克服硝酸的缺点成为另一种应用广泛的催化剂。草酸是一种挥发性的有机酸, 室温是固态, 100℃以上升华为气态, 187℃以上分解为CO、CO2 和H2O。因此, 用草酸做催化剂, 催化后的废气处理也比较简单。草酸的应用, 拓宽了原料范围的选择。此外矿物酸、三氟化硼和有机酸等也有一定的应用范围。硝酸作催化剂时, 脱除速率为0.7—1.5mmh-1,且脱脂速率快慢顺序为Si3N4 >ZrO2 >SiC。草酸作催化剂时, 脱脂速率为0.9—1.5mmh-1, 脱脂快慢顺序为ZrO2 >SiC>Si3N4 。可见不同催化剂的催化作用存在很大的差异。两种催化剂作用下的脱脂效果进行了比较, 如图1, 图2所示。
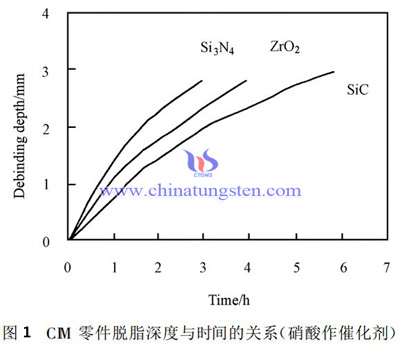
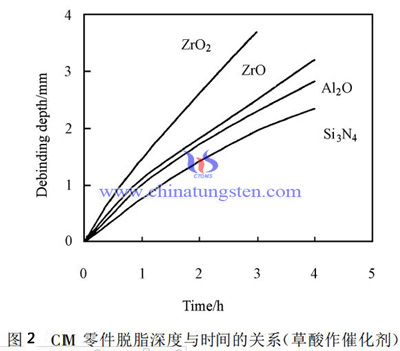
硬质合金供应商:中钨在线科技有限公司 | 产品详情: http://www.tungsten-carbide.com.cn |
电话:0592-5129696 传真:5129797 | 电子邮件:sales@chinatungsten.com |
钨钼文库:http://i.chinatungsten.com | 钨钼图片: http://image.chinatungsten.com |
钨新闻3G版:http://3g.chinatungsten.com | 钼业新闻: http://news.molybdenum.com.cn |
微博

微信

注射成型硬质合金催化脱脂的特点
- 详细资料
- 分类:钨业知识
- 发布于 2017年5月12日 星期五 15:25
- 作者:ruibin
- 点击数:1676
从注射成型硬质合金催化脱脂的脱脂原理中可以看出,注射成型硬质合金催化脱脂具有区别于传统脱脂方法(热脱脂和溶剂脱脂)的优异脱脂特性。
特点
1.脱脂速率快。在酸性催化剂的作用下聚醛树脂能够快速地分解成甲醛气体, 粘结剂――气态界面以1~2mm/h的线速度向内推进。注射成型硬质合金催化脱脂的速率可以达到2~4mm/h, 而一般粘结剂为基的注射成形坯的脱脂速率为0.2mm/h,注射成型硬质合金催化脱脂速率是传统脱脂工艺速率的10~20倍。由于注射成型硬质合金催化脱脂速率快, 脱脂时间短, 使得对注射成形坯尺寸厚度的限制小, 最大的脱脂厚度超过1英寸。
2.脱脂温度低。注射成型硬质合金催化脱脂的反应温度范围为100℃~ 140℃, 低于聚甲醛树脂的熔点(160℃~180℃), 避免了液相生成。这样就避免了热脱脂过程中由于生成液相而导致“生坯”软化, 或由于重力、内应力或粘性流动影响而产生变形和缺陷。
3.脱脂缺陷少。催化反应仅在气体—粘结剂界面上进行,由生坯外部逐渐向内部发展, 称之为“缩芯”机制。甲醛气体仅局限于在生坯的多孔“壳”区域产生, 可以容易地通过生坯的已是多孔的外部区域迅速逸出, 而不会在生坯内部产生应力, 不会产生生坯鼓泡、开裂等脱脂缺陷。
4.能实现连续脱脂和烧结。由于注射成型硬质合金催化脱脂速率快,脱除粘结剂所需的时间短, 使得注射成形中采用连续脱脂和烧结成为可能,下图为连续催化脱脂设备。
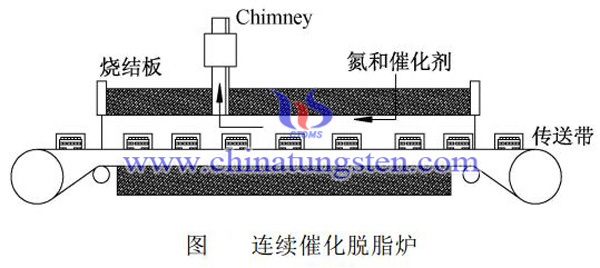
硬质合金供应商:中钨在线科技有限公司 | 产品详情: http://www.tungsten-carbide.com.cn |
电话:0592-5129696 传真:5129797 | 电子邮件:sales@chinatungsten.com |
钨钼文库:http://i.chinatungsten.com | 钨钼图片: http://image.chinatungsten.com |
钨新闻3G版:http://3g.chinatungsten.com | 钼业新闻: http://news.molybdenum.com.cn |
微博

微信
