硬质合金生坯预烧工艺制定
- 详细资料
- 分类:钨业知识
- 发布于 2017年5月24日 星期三 16:09
- 作者:ruibin
- 点击数:1868
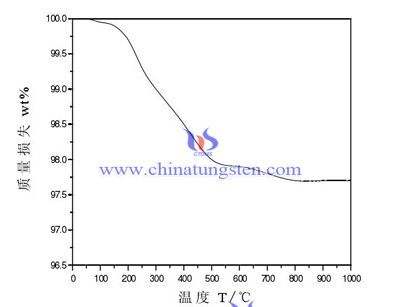
硬质合金的成形需要成型剂的参与,对于需要预烧工艺的硬质合金生坯,其工艺制定主要就是围绕成型剂的有效脱除展开的。为了能有效评价成型剂的脱除效果,常采用热重分析的方法。
硬质合金生坯加工的刀具磨损
- 详细资料
- 分类:钨业知识
- 发布于 2017年5月24日 星期三 16:07
- 作者:ruibin
- 点击数:1508
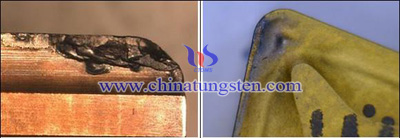
硬质合金生坯加工中刀具磨损在生坯加工中客观存在,若不加以控制将严重影响硬质合金生坯的加工性能,同时刀具磨损也是硬质合金生坯零件的加工性能之一,刀具磨损、平均破损宽度和表面光洁度是硬质合金生坯零件的三个主要加工性能。
典型的硬质合金生坯切削加工工艺
- 详细资料
- 分类:钨业知识
- 发布于 2017年5月24日 星期三 15:53
- 作者:ruibin
- 点击数:1747
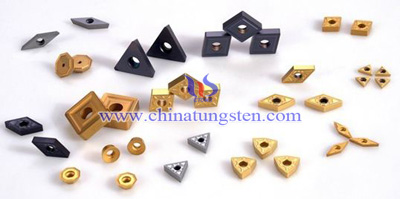
对于硬质合金生坯状态下的切削加工,其切削条件的控制非常重要。由于生坯零件和烧结件的加工行为不同,所选用的刀具也不同,因此,选择的最优切削参数也不同。对于生坯零件的加工,由于切削速度对表面光洁度和边缘破损宽度影响较小,因而可以采用较高的切削速度。
提高硬质合金生坯强度的手段
- 详细资料
- 分类:钨业知识
- 发布于 2017年5月24日 星期三 15:48
- 作者:ruibin
- 点击数:2009
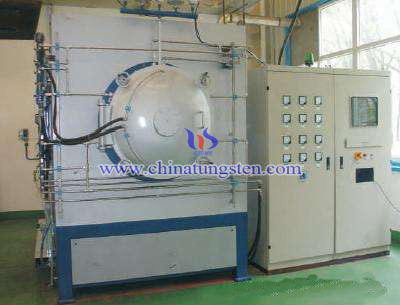
传统的预烧、渗蜡等手段可以提高生坯强度,通过多年的技术革新,开发了多种不同的生产工艺,如温压工艺、高速压制等新技术的出现,对提高粉末冶金压坯的力学性能起了突破性的促进作用,推动了粉末冶金工业的快速发展。